10 Exciting Examples of 3D Printing in the Automotive Industry in 2021

This article was updated in May 2021
The automotive industry is facing demands on all fronts: the demand for newer, better-performing vehicles, as well as the need to optimise production and streamline supply chains and logistics. One technology that is helping to meet these challenges is 3D printing.
3D printing is increasingly being explored across all areas of automotive production. Aside from its extensive use for rapid prototyping, the technology is also being used to produce tooling and, in some cases, end parts.
With the range of automotive 3D printing applications continuing to expand, below are some of the most promising examples of automotive companies using the technology to enhance their production.
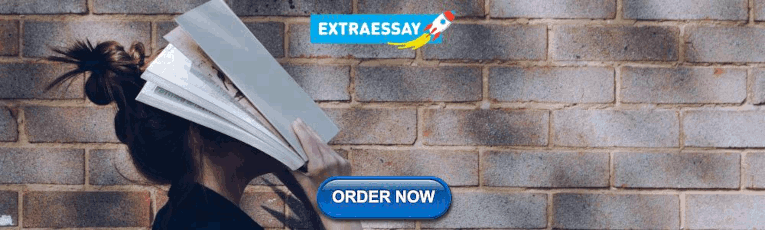
1. Porsche’s 3D-printed custom seats

Porsche has recently introduced a new concept for sports car seating that leverages 3D printing and lattice design.
The new seats feature polyurethane 3D-printed central seat and backrest cushion sections, which can be customised by three firmness levels: hard, medium and soft.
With its personalised seating, the German automaker is taking cues from the motorsport sector, where customised driver-specific seat fitting is a norm.
Porsche plans to 3D print 40 prototype seats for use on European race tracks as early as May 2020, with customer feedback being used to develop the final street-legal models for mid-2021.
Down the line, Porsche wants to expand seat customisation beyond firmness and colour by personalising the seat to customer’s specific body contour. 3D printing currently remains the only technology that can enable this level of customisation.
2. 3D printing for automotive brackets

Brackets are small and rather mundane parts, which were difficult to optimise in the past, when engineers were constrained by traditional manufacturing methods. Today, engineers can design optimised brackets and bring these designs to life with the help of 3D printing.
Rolls Royce has recently showcased the capabilities of 3D printing for brackets. The company showed off the large batch of DfAM-optimised and 3D-printed automotive metal parts, many of which look to be brackets.
Cost savings, faster production and design optimisation are typically the key reasons to use AM for brackets.
In the Rolls Royce’ example, the team was able to incorporate some really cool features into parts, including the 3D-printed brand name and a QR code, along with numbers to identify the specific, unique, part.
Adding these features during the manufacturing process is something that can only be achieved with digital manufacturing, as no subtractive method could ever compete in terms of the production cost and time.
Read also: Application Spotlight: 3D-Printed Brackets
3. Ford 3D prints parts for high-performance Mustang Shelby GT500
Ford Motor Company is one of the earliest adopters of 3D printing, having purchased the third 3D printer ever made some 30 years ago.
Ford, which opened its Advanced Manufacturing Center last year, has made steps to integrate 3D printing into its product development cycle. Now, the company is looking to use the technology for manufacturing applications.
Its latest vehicle, the 2020 Shelby GT500, is one example of this. Due to go on sale later this year, the 2020 Shelby GT500 is reportedly the most aerodynamically advanced Mustang to date.
Virtual design testing was a key part of the design process for the high-performance vehicle. Using virtual testing, more than 500 c ooling and aerodynamic 3D designs were analysed to enable the team to reach its downforce, braking and cooling targets.
Once the most promising designs were identified, Ford’s engineering team used 3D printing to create and test prototypes. For instance, the team printed and tested over 10 designs for front splitter wickers, which they were able to simultaneously send out for test evaluation.

In addition to using 3D-printed prototypes for design validation and functional testing, the upcoming 2020 Shelby GT500 will also feature two structural 3D-printed brake components . These components were created using Carbon’s Digital Light Synthesis (DLS) 3D printing technology and EPX (epoxy) 82 material, and have passed all of Ford’s performance standards and requirements.
With these applications, it’s clear that Ford is laying the foundation to be able to do some pretty impressive things with additive manufacturing.
“Additive manufacturing is going to continue to be ingrained more and more into the daily part of what we do as a business,” Ford’s Technical Leader of AM Technologies, Harold Sears, recently explained in AMFG’s Expert Interview series. ”Instead of being an exception to the norm, it’s going to be much more accepted as the way it’s done.”
Looking ahead, it will be exciting to see how Ford continues to leverage the capabilities of 3D printing to further enhance the production of its vehicles.
4. Volkswagen Autoeuropa: 3D-printed manufacturing tools

While prototyping remains the primary application of 3D printing within the automotive industry, using the technology for tooling is rapidly catching on.
One exciting example of this is Volkswagen, which has been using 3D printing in-house for a number of years.
In 2014, the company began to pilot Ultimaker’s desktop 3D printers to produce tooling equipment at the Volkswagen Autoeuropa factory in Portugal. Since the success of the pilot, Volkswagen has switched its tooling production almost entirely to 3D printing.
Using the technology for this application brings a number of advantages.
Producing its tooling internally reduces tool production costs for the car manufacturer by 90% — and cuts lead times from weeks to just a few days. To take one example, a tool like a liftgate badge would reportedly take 35 days to develop using traditional manufacturing and cost up to €400. With 3D printing, the same tool can be produced in four days at a cost of just €10.
Using 3D printing for tooling is said to have saved Volkswagen nearly €325,000 in 2017, whilst improving ergonomics, productivity and operator satisfaction.
When it comes to manufacturing aids, 3D printing is rapidly growing as an alternative to more established ways of manufacturing tools. In a few years, we’ll likely see more automotive OEMs switching to 3D-printed tooling to improve the efficiency of their production and the performance of their tools.
Read also: 6 Ways to Improve Production Efficiency with 3D Printed Jigs and Fixtures
5. 3D-printed lug nuts that save car wheels from thieves

How to stop thieves from stealing car wheels? Ford is answering that question with a program in Europe to 3D print custom locking wheel lug nuts for cars that are more resistant to theft.
Normally, cars will have a single locking lug nut per wheel to prevent its removal without the special key attached to the lug wrench. But these can be defeated, so Ford is 3D printing patterns for its locks that can’t be cloned as easily.
Using 3D printers from EOS, Ford creates locks using a custom pattern for each customer. Using a sound wave pattern from a simple sentence, it’s possible to create a completely unique pattern that provides an added layer of security in a similar fashion to fingerprint recognition.
Once designed, the lock and the key are 3D-printed as a single stainless steel part. After cutting the two apart, they need only a little polishing to work.
The advantage of these locks is that they are virtually impossible to clone. With unevenly spaced ribs inside the nut and indentations that wide the deeper they go in, it’s impossible for thieves to make a wax impression of these locks without breaking the wax.
Making wheels more secure and offering more product personalisation are further proof that 3D printing is a game-changer for car production.
6. Local Motors & XEV: on the road towards 3D-printed cars?

While still some way away, a number of companies are striving to make fully 3D-printed cars a reality. Local Motors, based in Arizona, is one company with a goal to 3D printing entire vehicles possible.
The company made a splash in 2014 when it announced what it claimed to be the first-ever 3D-printed electric car — Strati — at the International Manufacturing Technology Show (IMTS). The car was manufactured in collaboration with Oak Ridge National Laboratory (ORNL) and Cincinnati, Inc.
Two years later, Local Motors unveiled Olli, a 3D-printed, autonomous electric shuttle designed for local, low-speed transportation. The shuttle has been designed primarily for use in urban centres in cities, business and university campuses and hospitals.
So how has the company achieved this?
Local Motors used some of the world’s largest 3D printers — ORNL’s Big Area Additive Manufacturing (BAAM) and Thermwood’s Large Scale Additive Manufacturing (LSAM) machines — to produce most of Olli’s components, including the roof and lower body of the vehicle.
Similarly, Strati was printed using Cincinnati, Inc.’s large-scale 3D printer, and took only 44 hours to complete. The wheels and hubcaps of the car were produced using a direct metal 3D printing process.
Since Olli was first introduced, Local Motors has tested over 2,000 combinations of printing material and fortifying additives, and is now able to print the entire minibus in roughly 10 hours.
Local Motors attributes its success to its ‘digital vehicle manufacturing model’ . This business model enables the company to bring products to market in an entirely new way by co-creating new designs with a global community of experts. The company uses digital manufacturing technologies, like 3D printing, to manufacture and assemble vehicles in local microfactories.
3D printing is a natural fit to this distributed manufacturing model, as it provides a way to quickly iterate designs, customise parts and products on an as-needed basis, saving resources and reducing the need to keep the inventory.
While it will take some time to see fully 3D-printed vehicles on the roads, projects like Local Motors’ Olli could take us one step closer to that exciting possibility.
Local Motors is not the only company pursuing 3D-printed cars. Similarly, Italian automaker, XEV, is developing a low-speed electric LSEV car with the help of 3D printing.
Using large-format FDM technology and four different grades of polyamide and TPU, the company is able to reduce its production costs by 70% and take advantage of the lightweighting 3D printing offers.
The finished LSEV weighs only 450 kilograms and features just 57 plastic components, meaning it can be produced in a matter of days. XEV has also made the decision to produce 2,000 of its own large-format extrusion 3D printers to use inside its factories for production.
While mass production of the vehicle will begin later this year, pre-orders have already been made by Italian postal service, Post Italiane, who has commissioned 5,000 customised vehicles for its operations.
7. Greater customisation with 3D printing
With the growing demand for customised products and personalised experiences, automakers are increasingly offering their customers the ability to customise their vehicles.
One way to make this customisation economically viable is with 3D printing.
Japan’s oldest car manufacturer, Daihatsu, launched a vehicle customisation project for its Copen car model in 2016.
In partnership with Stratasys, Daihatsu customers can design and order custom 3D-printed panels for their front and rear bumpers, with a choice of more than 15 base patterns in 10 different colours.
The customised parts are printed with ASA , a durable and UV-resistant thermoplastic, using Stratasys’ Fortus 3D printers. The ability to produce personalised, one-off designs quickly and cost-effectively was one of the key reasons for choosing 3D printing over traditional processes.
In Europe, Volkswagen is now implementing HP’s Metal Jet technology with an eye towards customised metal parts such as tailgates, gear-shift knobs and key rings.
The company plans to give its customers the option of adding individualised lettering to these components. Volkswagen also notes that these personalised components will serve as a proof of concept for developing 3D-printed structural parts for its cars within the next two to three years.
One advantage of using 3D printing for customisation is that it allows automakers to reduce lead times and production costs for low-volume parts. This is partly because the technology eliminates the need to create individual tooling aids for each personalised part — a prospect that would be financially unfeasible.
Going forward, automakers will still need to develop more use cases for customised 3D-printed components to go beyond simple trim parts. That said, as the technology advances, the possibilities for car customisation with 3D printing look set to expand at a much greater pace over the next few years.
Read also: 3D Printing and Mass Customisation: Where Are We Today?
8. Chasing victory: 3D printing for motorsports

In Formula One racing , how a race car performs will often mean the difference between a win or a loss. However, engineering a successful race car is a challenge, not least because of the high costs involved and the rapid development cycle required.
Wind tunnel testing is one of the essential stages of the race car development process.
Automakers use wind tunnels to verify and adjust the aerodynamic properties of a race car. During the wind tunnel testing stage, a model of a car is placed on a treadmill to test how the car will perform in a simulated racing environment.
Currently, 3D printing is most commonly used within motorsports to create parts to be tested out on this replica race car. For example, Swiss Alfa Romeo Sauber F1 Team is reported to have used a 60% scale model of a Formula 1 race car, with many of its components 3D printed with SLS and SLA technologies.
Engineers at Sauber are able to print parts like front wings, brake ducts, suspension and engine covers much faster and with greater design flexibility than traditional manufacturing would allow.
Another example comes from Volkswagen Motorsport, which used 3D printing for the development of its electric I.D. R Pikes Peak race car . Having only eight months to develop the car, the Volkswagen team bet on 3D printing to speed up the process and meet its development deadlines.
The technology was used to produce parts for the 50% scale model of the I.D. R Pikes Peak car. Around 2,000 individual parts for the wind tunnel model have been manufactured, with parts produced within a few days instead of the weeks it would take with CNC machining or moulding.
By enabling an extremely flexible and very rapid development process, 3D printing has helped Volkswagen Motorsport to get the car on the road on schedule. And this effort was recently rewarded: just last year, the I.D. R Pikes Peak race car set a new record for the hill climb in Pikes Peak racing.
With proven effectiveness in reducing development times, 3D printing is now making its way into end-part applications that could offer racing teams significant performance advantages.
9. 3D printing spare parts for classic cars

Spare parts are yet another application of 3D printing in automotive — and one Porsche Classic is taking full advantage of.
The division of the German car company supplies parts for its vintage and out-of-production models, and is using 3D printing to produce rare, low-volume spare parts for its older inventory.
Many of these parts are no longer in production, and the tooling required to manufacture them either don’t exist or are in poor condition. Manufacturing new tooling aids with traditional methods is inherently cost-prohibitive, particularly considering the low volumes in question.
With a view to solving these challenges, Porsche Classic has begun to 3D print these parts (in metal and plastic) on demand.
The printing process involves melting the metal powder (or sintering for plastics) with a high-energy laser beam in a precise pattern, thus building the three-dimensional object up one layer at a time. The advantage is that parts can be made without any additional tools and only when needed, helping Porsche to save on tooling and storage costs associated with making these spares using conventional methods.
3D printing parts that are rarely ordered or stopped being produced is a growing trend within the automotive supply chain. Mercedes-Benz Trucks, Volkswagen and BMW are also embracing 3D printing for this application, enabling the carmakers to cut costs, increase operational efficiency and optimise inventory.
Read also: How 3D Printing is Transforming the Spare Parts Industry
10. Will future motorcycles be 3D-printed?
So far, we’ve seen companies 3D printing components for cars and even entire car bodies — but what about motorcycles?
While there are no commercially available 3D-printed bikes on the road yet, there are a number of projects that offer a glimpse into what could be the future of motorcycle production.
APWORKS’ Light Rider is one of the most well-known examples of the potential of using 3D printing for motorcycle production.
The German company unveiled the 3D-printed, topologically optimised, electric motorcycle in 2016. The motorcycle also showcases the properties of APWORKS’ proprietary Scalmalloy material. Using Scalmalloy, the 3D-printed motorcycle frame is 30% lighter than its traditionally made counterparts.
While APWORKS has seen huge success with the project, with a great deal of customers wanting to purchase the Light Rider, being able to make production commercially viable remains a challenge.
Another, more recent, example of a 3D-printed motorbike comes from German FDM 3D printer manufacturer, BigRep.

The company’s NERA motorcycle — a fully functional prototype — took just 12 weeks to produce, and was designed to demonstrate the capabilities of 3D printing.
To create it, BigRep used its large-scale 3D printers and a range of materials including PLA, Pro FLEX (a TPU-based flexible material) and the engineering-grade ProHT filament. With the exception of electronics, all of the 15 parts were 3D printed, including the rims, frame, airless tires, seat and a flexible bumper.
While these and other projects offer an exciting glimpse into the potential of 3D printing for motorcycles, it will be quite some time before them on the road. But 3D printing’s ability to create lightweight parts, enhance performance and enable faster and cheaper production makes us excited about its future potential for this application.
Driving the future of automotive production
While this list showcases the key application areas for 3D printing within automotive, it only scratches the surface of its possibilities. However, as automakers recognise the potential of the technology to provide a leg up on the competition, the number of applications will surely expand.
Looking into the future of 3D printing in automotive, the technology will continue to permeate into product development, production, assembly and the supply chain, enabling new designs, competitive business models, and, ultimately, superior vehicles.
Subscribe to our newsletter
Get our best content straight to your inbox
Related posts
07 May 2024 CNC Acrylic CNC Machining: A Comprehensive Guide

Thank you for subscribing!
You'll receive our latest content every week, straight to your inbox.
Request sent successfully!
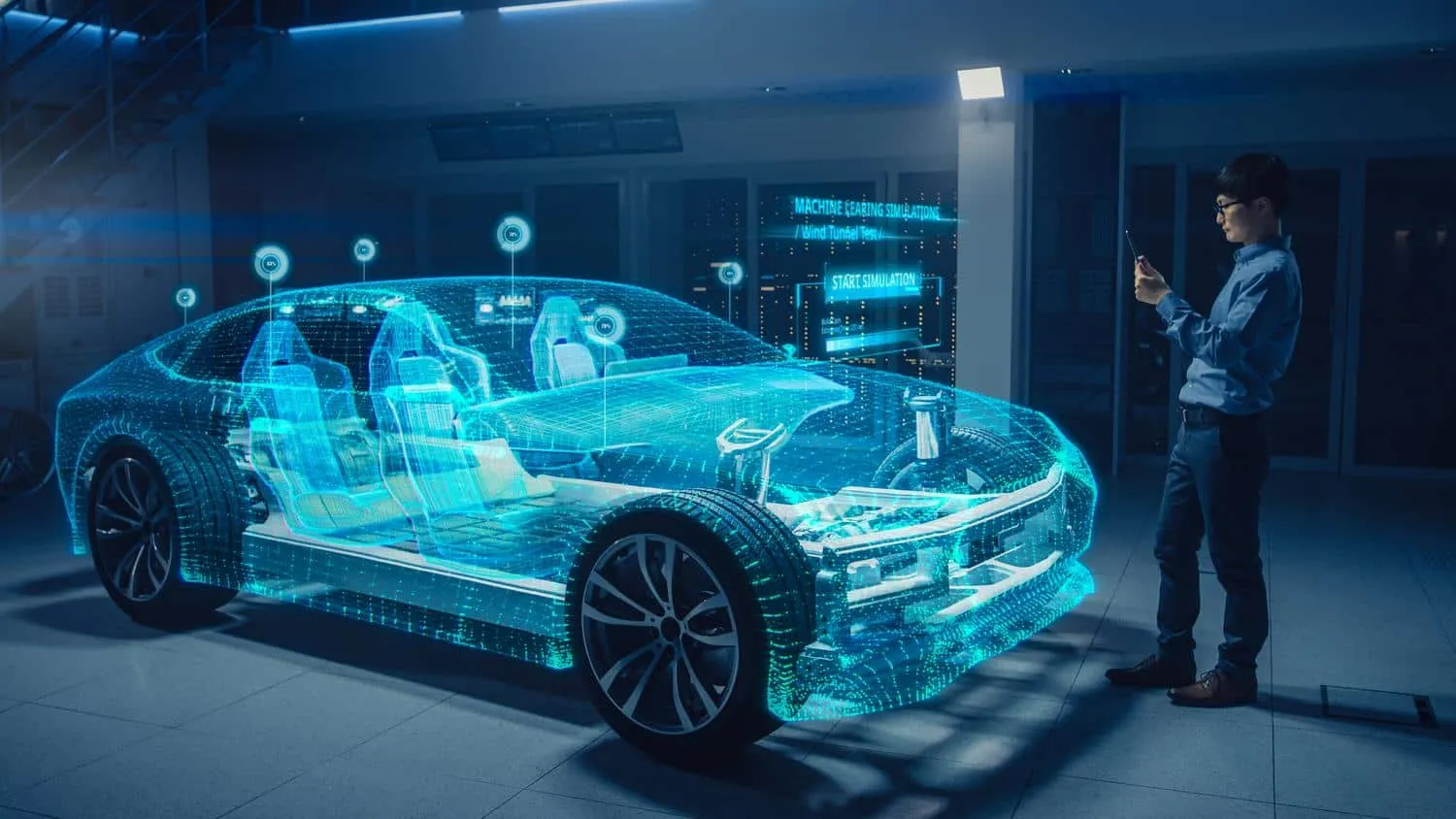
Automotive 3D Printing
Automotive 3D printing is transforming vehicle production by enabling engineers to design and manufacture parts that are stronger, lighter and more cost-effective.
What is 3D printing?
3D printing, or additive manufacturing, is a production technique that creates a three-dimensional object from a computer-aided design (CAD) file. The term covers several different processes, all involving one or more materials—typically plastic, metal, wax or composite—being deposited layer by layer to build a shape.
The entire process is computer controlled. This makes 3D printing a cost-effective, efficient and accurate method to create objects of almost any geometry or complexity. Today, 3D printing is used in every industry to produce everything from prototypes, tools and jigs to components and end-use parts.
3D printers come in various sizes, from small enough to fit on a benchtop to large-format industrial machines.
Large printers can produce bigger objects but the machines take up more space and are significantly more expensive compared to benchtop printers. Achieving a successful print is also more complex on large-format machines due to the volume of material and printing time involved.
To learn more, visit our 3DEXPERIENCE GUIDE TO 3D PRINTING
How is 3D printing transforming the automotive industry?
Automotive 3D printing brings many advantages to the industry, including:
- Streamlining the design workflow
- Producing lighter, stronger parts
- Consolidating previously separate parts into a single unit
- Minimizing raw material wastage
- Shortening time to market
- Optimizing inventory and supply chain management
- Simplifying ways for customers to personalize vehicles
Automotive is a major user of 3D printing technology, second only to aerospace. That makes sense given how similar the two industries are in terms of their core objectives. Like aircraft manufacturers, automotive brands are highly focused on improving fuel efficiency and performance while reducing weight.
3D printing is well suited to achieve these goals thanks to its ability to produce lighter parts that are as strong if not stronger than those made using traditional manufacturing methods.
Furthermore, 3D printing brings a new level of design freedom. The technology can produce highly complex part geometries that would be hard if not impossible to make any other way. It also provides a cost-effective and efficient means of making a vehicle unique to each customer through bespoke interior trim pieces, for example.
Little wonder automotive 3D printing is now firmly established in every car maker, from Audi to Volvo. Examples can be found in all operational areas, from research and development (R&D) and assembly to aftersales support and classic car restoration.
Although the mass-produced cars of today contain few 3D-printed parts, the range of applications continues to expand and we’re likely to see much greater use of automotive 3D printing shortly.
Case study 1: ONE MILLION 3D-PRINTED PARTS IN 25 YEARS
Volkswagen has been using 3D printing for 25-plus years, with an initial aim to accelerate vehicle development and reduce costs.
Today, there are 13 units at the Wolfsburg Volkswagen Factory—the Group’s global HQ and one of the largest manufacturing plants in the world—all using 3D printing processes to make both plastic and metal parts.
Typical examples of plastic components are for prototypes such as center consoles, door cladding, instrument panels and bumpers. Printed metal parts include intake manifolds, radiators, brackets and support elements.
To date, Volkswagen has produced more than one million 3D-printed parts.
Its latest 3D printing innovation, a metal binder jetting process, co-created with external partners, is helping to make automotive 3D printing more cost-effective and suitable for production-line use.
Whereas conventional automotive 3D printing uses a laser to build a component layer by layer from metallic powder, the binder jetting process uses an adhesive. The resulting metallic part is then heated and shaped.
The first components made using this new process were parts for the A-pillar of the Volkswagen T-Roc convertible. These weigh almost 50% less than conventional components made from sheet steel. This reduction alone makes the process especially interesting for automotive production applications.
How is 3D printing used in the automotive industry?
The four most common applications of automotive 3D printing are:
PROTOTYPING
Whether simple mock-ups or detailed scale models, rapid prototypes are a vital part of product development. These early-stage concept models allow engineers to see how a product truly looks and feels. Crucial elements where visual appeal and driver experience are paramount.
Rapid prototyping also provides the opportunity to see how different components relate to each other and to assess whether a part functions correctly and meets the design specification.
Prototypes used to be hand-made or created using molds that also needed to be designed and manufactured, often by an external company. This was both expensive and time-consuming.
Automotive 3D printing accelerates product development by producing design iterations in a fraction of the time versus traditional manufacturing techniques. This allows more testing to be conducted in the same or shorter period and helps to highlight potential issues earlier.
For example, placing a scale model in a wind tunnel to measure the aerodynamic forces created by a particular vehicle design. Advantages such as these enable automotive manufacturers to stay ahead in a fast-paced, competitive market.
TOOLING, JIGS AND FIXTURES
The creation of low-cost rapid tooling and manufacturing aids is one of the most common uses of automotive 3D printing.
A car contains many thousands of separate components and subassemblies. Fitting each of these to the vehicle frame becomes much faster, easier, safer and more consistent thanks to manufacturing aids such as jigs, grips, fixtures and templates.
3D printing these tools quickly onsite or close-by generates substantial time and cost savings compared to conventional production methods.
Additionally, 3D printers are employed to make tools such as thermoforming molds used to form heated sheets of extruded plastic. This is a common technique to manufacture form-fitting packaging for all manner of components.
PRODUCTION PARTS
There are two main categories of 3D printed production parts used in automotive:
- Vehicle trim such as dashboards, seat frames, control panels, trim pieces, cooling vents and ducting, light fittings, covers and console accessories. These are typically 3D printed using a thermoplastic or polymer material such as ABS, nylon or resin.
Vehicle trim currently represents the majority of 3D-printed parts found in vehicles as they are non-safety related. This makes gaining approval from automotive regulatory bodies relatively straightforward.
However, these parts are often visible to the driver and passengers and frequently interacted with. This requires them to be not only functional but also visually pleasing.
A key advantage automotive 3D printing offers is the ease at which it can produce very low volumes or even one-off items, bringing a wide range of personalization options to the mass market.
In the past, producing bespoke parts such as a gear stick, key fob, seat or set of pedals was highly expensive and time-consuming. This meant customization was largely reserved for luxury car brands.
Thanks to 3D printing, items such as these can be easily, quickly and affordably customized to suit a buyer’s specific demands.
- Mechanical components such as mounting brackets, housings, suspension wishbones and brake components. The mechanical and temperature stresses these parts experience mean they are usually 3D printed from a metal such as titanium or an aluminum alloy.
Only a handful of parts have so far been approved as road-safe as the validation process for safety-critical components is far more stringent. That number will increase as automotive 3D printing becomes a more trusted technology by manufacturers and regulatory authorities.
MAINTENANCE SPARES AND REPAIRS
Ensuring the availability of spare parts has long been a challenge for the automotive industry. There have been thousands of different cars makes and models over the past 130-plus years, from single-digit concept cars to those mass-produced in their millions. Each one contains tens of thousands of components sourced via notoriously complex, extended supply chains.
Having the right part in the right location with minimal time delay leads to stockpiling large quantities in warehouses at considerable expense. The alternative is to make to order using traditional manufacturing methods, which can be costly and have a long lead time (the period between ordering and delivery)
In the case of rare or classic cars, spare parts may be prohibitively expensive or not available. Original tooling or build specifications may have been lost or suppliers may have closed their doors.
The speed, flexibility and efficiency of automotive 3D printing enable replacement parts to be quickly and cost-effectively manufactured on-demand. Furthermore, digital CAD files can be stored on servers and simply downloaded when needed. This helps to optimize stock levels and eliminates the need to maintain storage facilities.
Additionally, hard-to-obtain or obsolete components can be digitally scanned and reverse-engineered to be 3D printed. This brings substantial time, cost and labor savings and frequently results in lighter parts with superior performance.
Case Study 2: 3D PRINTING INNOVATION MEETS AUTOMOTIVE HERITAGE
For collectors of rare classic cars, the availability of spare parts can mean the difference between driving a vehicle or being forced to keep it in storage. The rarity of these vehicles means part demand is both limited and infrequent.
In some cases, specific parts are reproduced using the original tools and techniques. However, sometimes new tooling is needed. Investing the required time and money to manufacture new tools can be hard to justify against such small production volumes.
Porsche Classic has overcome this challenge by utilizing 3D printing to produce rare parts that are only required in low volumes.
For example, the clutch release lever on the Porsche 959. This component, made from gray cast iron, is subject to stringent quality requirements but is in very low demand—not least because fewer than 300 of these super sports cars were ever produced.
This makes the part an ideal candidate for metal additive manufacturing. Indeed, Porsche is currently manufacturing several such parts using 3D printing—both steel and alloy and plastic.
All 3D printed parts are rigorously inspected to ensure they meet the quality requirements of the original production period as a minimum, though they usually meet higher standards. Accuracy in terms of size and fit is ensured by performing tests with the part installed.
Porsche Classic is currently testing whether 3D printing is suitable to produce a further 20 components. According to a spokesperson, as the quality of the technology continues to improve with costs generally decreasing, this form of manufacturing presents a very real “economic alternative for the production of small quantities.”
What are the growth opportunities for automotive 3D printing?
Improvements in the size of industrial printers, the speed at which they print and greater design and material flexibility are all helping to make automotive 3D printing a more viable mainstream manufacturing method. This is especially true for low to medium-volume production runs of high-value, geometrically complex components.
As a result, new applications for automotive 3D printing are continuously emerging. Some of the areas expected to see substantial growth over the coming years include:
GREEN MOBILITY
Automotive, like every industry, is under pressure to become more sustainable. A clear advantage 3D printing provides is lightweighting—i.e., using lighter parts to reduce the total weight of a vehicle and therefore reducing fuel consumption without comprising performance or safety.
A rough guideline is that a 10% weight reduction generates a 6% improvement in fuel efficiency. For electric vehicles, fuel economy improvements can be even greater. A 10% weight saving in an EV can boost driving range by up to 14%.
3D-printed automotive parts also eliminate the carbon emissions inherent to global supply chains. Instead, digital CAD files can be sent to a 3D printer anywhere in the world with the click of a button.
Furthermore, 3D printers generate dramatically less material wastage during the manufacturing process compared to machining, where as much as 98% of a block of metal can be machined away.
ELECTRIC VEHICLES
Closely aligned with the automotive industry becoming more sustainable is the move away from the internal combustion engine to alternative propulsion systems.
Every international car manufacturer has introduced or soon will introduce some form of electric vehicle, from family saloons and futuristic concepts to SUVs and supercars. Industry and consumer interest are accelerating due to many countries and cities stating they will ban the sale of passenger cars powered by fossil fuels.
Lightweight 3D-printed automotive parts can help offset the added weight of batteries and reduce overall vehicle weight. This helps increase the maximum potential driving range and prolong battery life.
Additionally, the buzz surrounding electric vehicles has seen the emergence of many new vehicle manufacturers. These new players won’t be mass-producing cars anytime soon, but they do have the advantage of not being tied to decades-old manufacturing processes and globe-spanning supply chains.
Their search for low to mid-volume production methods that are agile, flexible and scalable has naturally led them to automotive 3D printing technology.
3D PRINTED CARS
Fully 3D-printed cars driving on public roads may happen sooner than we think. Several companies are taking the concept extremely seriously.
California-based Divergent, for example, aims to revolutionize automotive manufacturing with its 3D-printed nodes connected by carbon fiber tubing. The result is an industrial-strength chassis that can be assembled in minutes. Its engineering prototype, Blade , has been described as “the world’s first 3D-printed supercar.”
By using lightweight materials to create strong and efficient complex structures, Divergent is looking to cut down on the tooling, cost and time associated with traditional car making, while simultaneously raising sustainability and innovation.
The resulting vehicle may be prohibitively expensive but the technology and thinking behind it could provide a substantial boost to more mainstream car production, as well as prove beneficial to other fields like aerospace and space exploration.
Case Study 3: LUXURY CAR BRAND DOUBLES DOWN ON 3D PRINTING
Bentley Motors recently invested an additional £3 million to double its 3D printing capacity at its headquarters in Crewe, England, where all Bentley models are built.
The high-tech facility has been applied to a range of uses and produced more than 15,000 components in 2021 alone. These include on-the-job assisted tools like lightweight sanding blocks and historically accurate tooling equipment needed to make parts for Bentley’s Blower Continuation model.
Additionally, automotive 3D printing has been employed to create physical components for several prototype Bentleys, including full-scale powertrain models and aerodynamic wind tunnel models.
The advanced techniques have also been used to produce parts for the record-breaking Bentley models that were driven in the demanding Pikes Peak Challenge in America.
The significant expansion to the facility will see the luxury car brand utilize 3D printing technology to create low-volume vehicle components and offer even greater personalization in customer cars.
The state-of-the-art equipment installed enables a 50% cost saving on parts and by operating around the clock, the facility is capable of producing thousands of components in more than 25 different material options.
Employees from across the company are receiving training to understand how they can benefit from using 3D printing in their work, a strong indication of how central the technology is becoming to Bentley’s operation.
A spokesperson called automotive 3D printing a “cornerstone” of Bentley’s “Dream Factory” ambition. They noted that a key benefit of automotive 3D printing is the efficiency improvement it provides by cutting down on the cost and complexity of countless jobs.
What are the limitations of automotive 3D printing?
Lack of familiarity.
Though growing in prevalence, automotive 3D printing is not yet ubiquitous—certainly outside of prototyping and tool making. That time may come, possibly sooner than expected, but for now, the technology remains secondary to more conventional production methods.
The complexity and rigorous standards integral to manufacturing safety-critical automotive parts mean replacing tried and tested machining techniques with something new carries a level of risk some companies aren’t comfortable with.
LARGE VOLUMES
In many cases, automotive 3D printing can produce a single item or small batch of items faster and more efficiently than traditional manufacturing methods. However, each machine can only print a certain number of objects at any one time, depending on machine size and object, so may not be the most suitable or cost-effective method for large production runs.
3D printers have inherent size constraints that make them incapable of producing large components. In some cases, multiple smaller parts can be joined together, though this may not always be an ideal solution.
Manufacturers of 3D printers are working to address the size limitations of existing machines, such as by removing the barriers present in typical print chambers.
INCONSISTENT QUALITY
3D printers can’t yet print perfect results every time. Failure rates depend on the machine and material used and the object being printed. Also, removing surface irregularities or textures may require additional manual processing steps to achieve the desired finish.
Factors like failure rates and post-processing will likely reduce as the technology improves and people become more familiar with using automotive 3D printing .
Get multiple quotes for your parts in seconds
- Shopping Cart
The Transformative Capabilities of 3D Printing in Automotive Manufacturing
By using 3D printing in the automotive world, engineers can be more confident going into production and avoid any errors that may have occurred.
For resilient prototypes and parts made from high-performance engineering thermoplastics, Stratasys has Fused Deposition Modeling (FDM) Technology. For beautiful models requiring rubberlike or clear materials with a smooth finish right out of the 3D printer, we offer PolyJet technology.
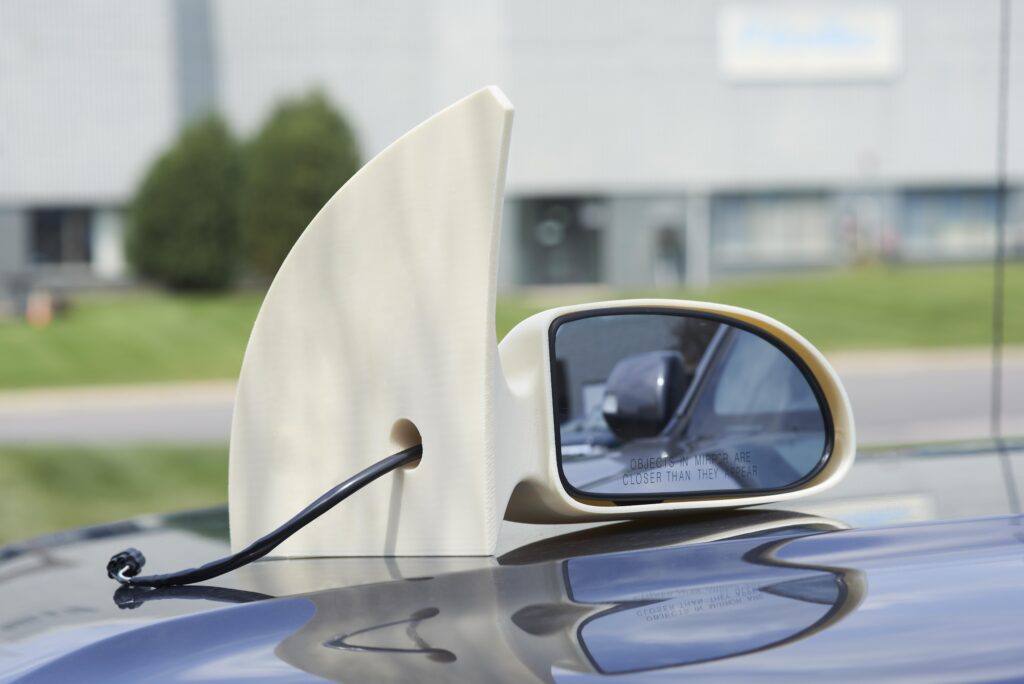
3D Printing in Automotive Industry Case Studies
- Dash CAE – Reducing Lead Time
- Elkamet – Creating Production Tools & Prototypes
- EPSI – Creating Rubber-like Prototypes
3D printing in the automotive industry has become a game-changer in the manufacturing process, and the automotive sector is no exception. The capabilities of industrial 3D printers are transforming the automotive industry by enabling faster prototyping, reducing production costs, and enhancing vehicle performance.
Capabilities and Advantages of Industrial 3D Printing in the Automotive Industry
Talk to a 3d printing expert.

Rapid Prototyping and Design Iterations
With industrial 3D printing, automotive manufacturers can create prototypes of various components and vehicle designs with unparalleled speed. This capability allows for rapid design iterations, enabling engineers to fine-tune their designs and bring new vehicles to the market more swiftly than ever before.
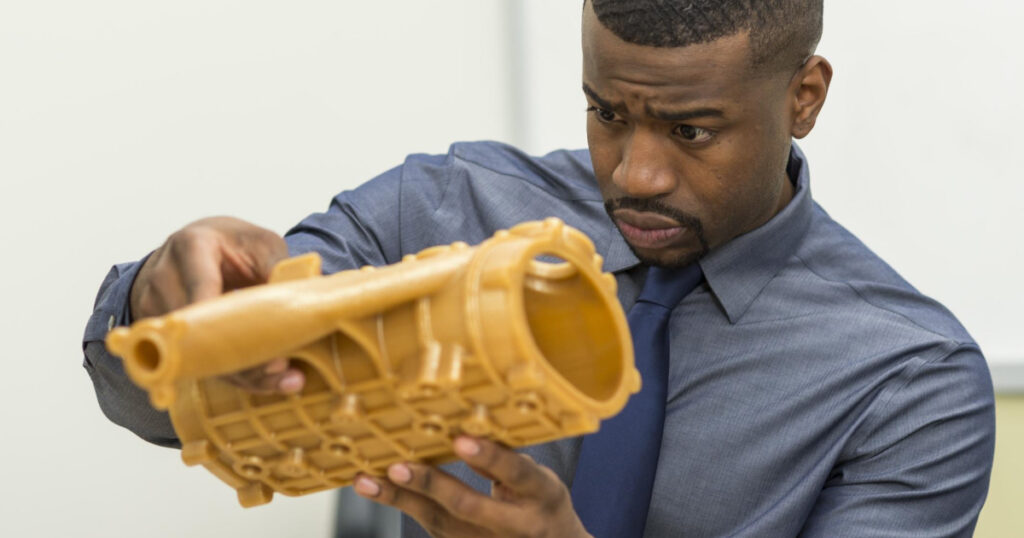
Complex Geometries and Lightweight Structures
One of the key strengths of automotive 3D printing is its ability to fabricate intricate geometries that traditional manufacturing processes cannot replicate. This advantage is particularly significant in the automotive industry, where lightweight structures are crucial for improving fuel efficiency and overall vehicle performance.
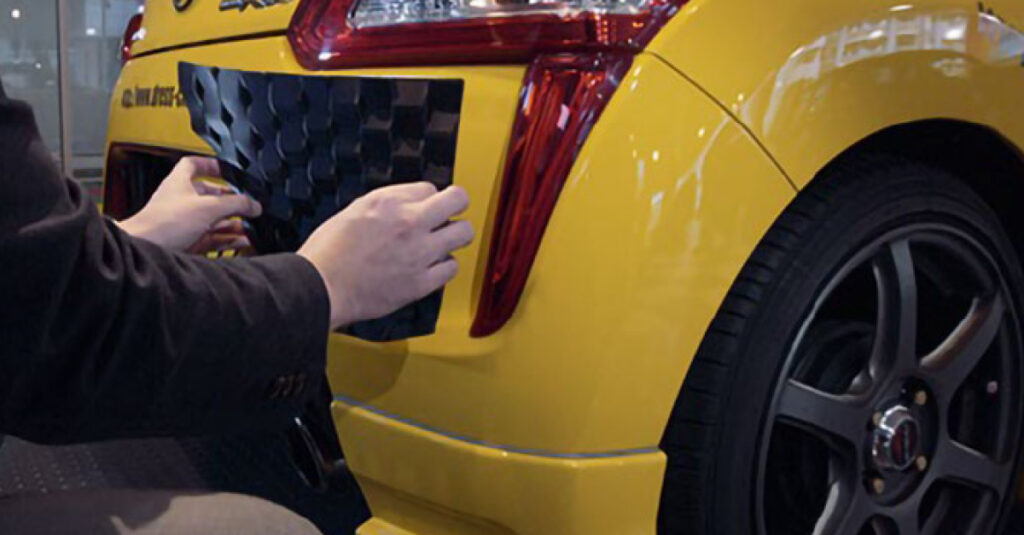
Customization and Personalization
Industrial 3D printing empowers automakers to offer customizable vehicles tailored to individual customer preferences. From personalized dashboard designs to unique exterior features, automotive 3D printing enables a level of customization that was previously unimaginable in mass production.
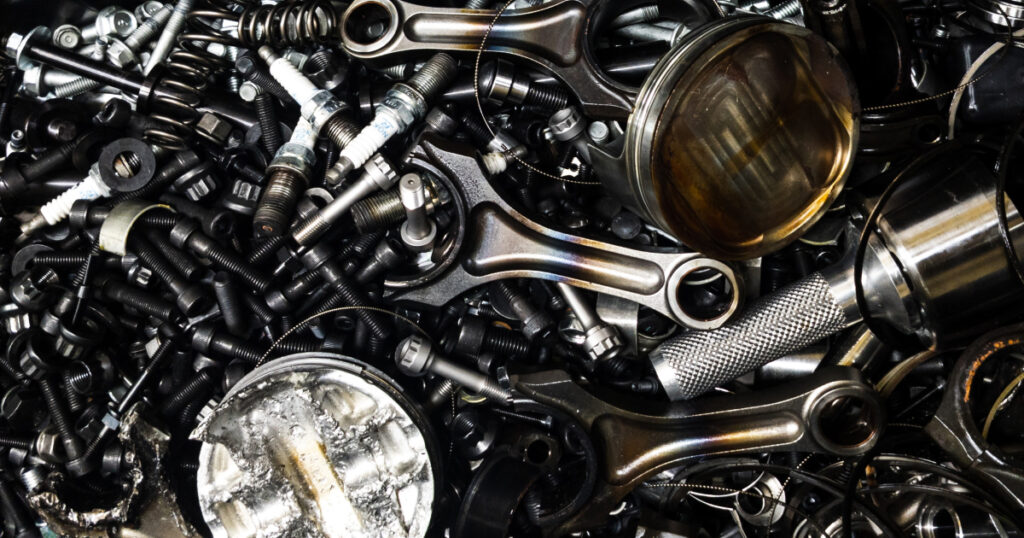
Reduced Material Waste and Sustainability
Traditional manufacturing processes often lead to significant material wastage. In contrast, 3D printing for the automotive industry builds components layer by layer, minimizing material waste and promoting sustainability in automotive manufacturing.
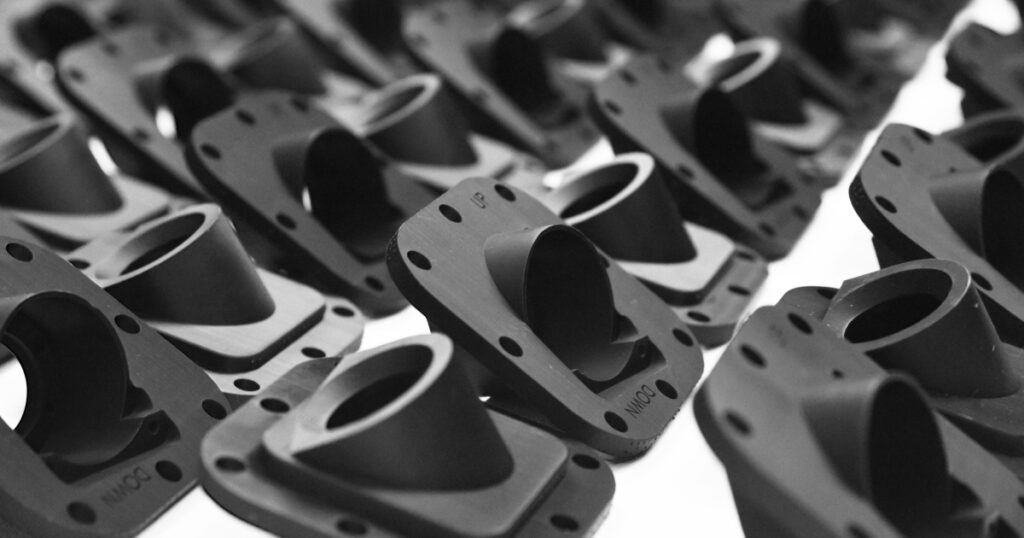
Faster Replacement Parts Production
Industrial 3D printing for automotive parts facilitates on-demand production of replacement parts, reducing the need for large warehouses to store a vast inventory of components. 3D printed car parts not only reduces costs but also ensures that essential parts are readily available when needed, minimizing vehicle downtime.
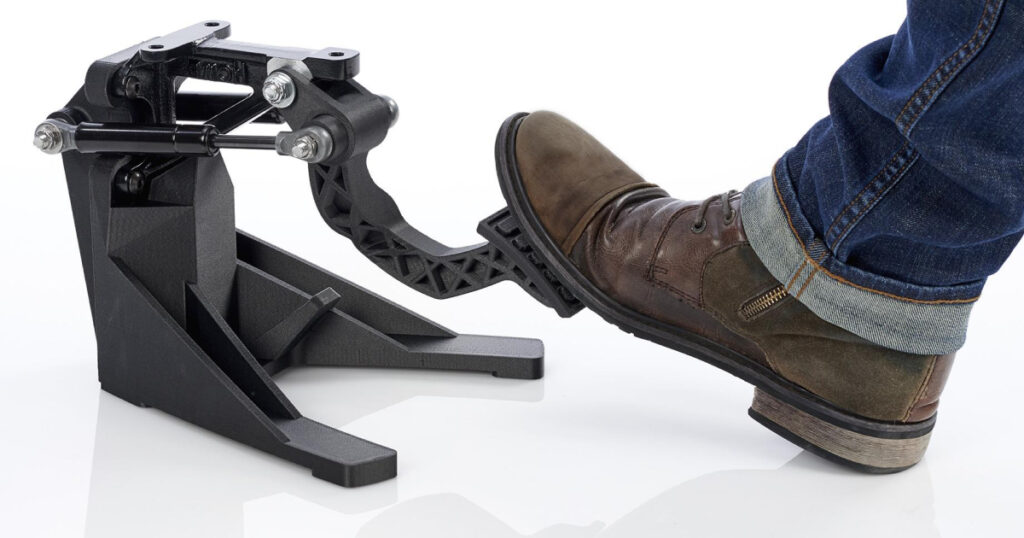
Improved Performance with High-Quality 3D Prints
Advancements in 3D printing materials, such as carbon fiber 3D prints and other durable 3D printed parts, have unlocked new possibilities for lightweight and high-strength automotive components. These materials enhance vehicle performance and safety.
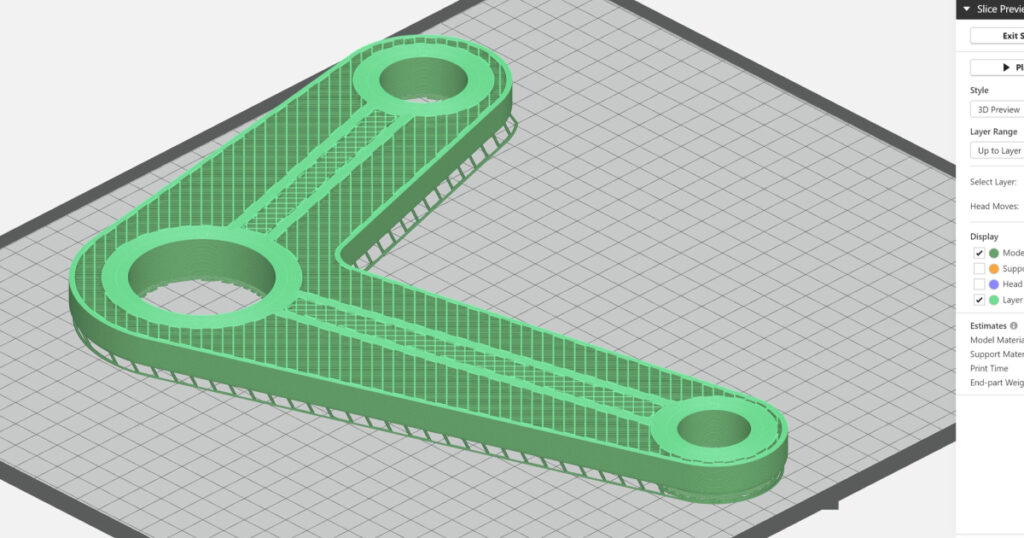
Digital Inventory Management
3D printing allows for the creation of digital inventories, where designs are stored electronically and can be readily accessed and printed on demand using efficient 3D printers. This digital approach saves physical storage space and simplifies inventory management.
Best Fit 3D Printing Technologies for Automotive Industry
Product development.
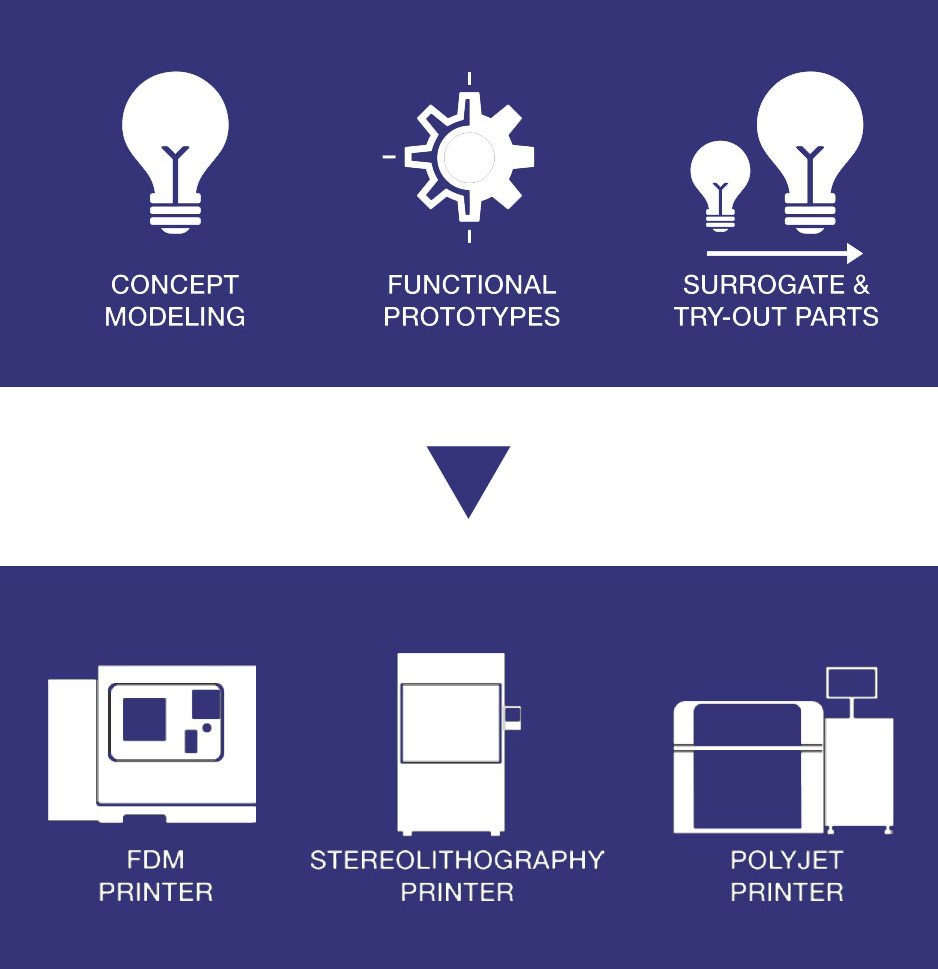
Production Support
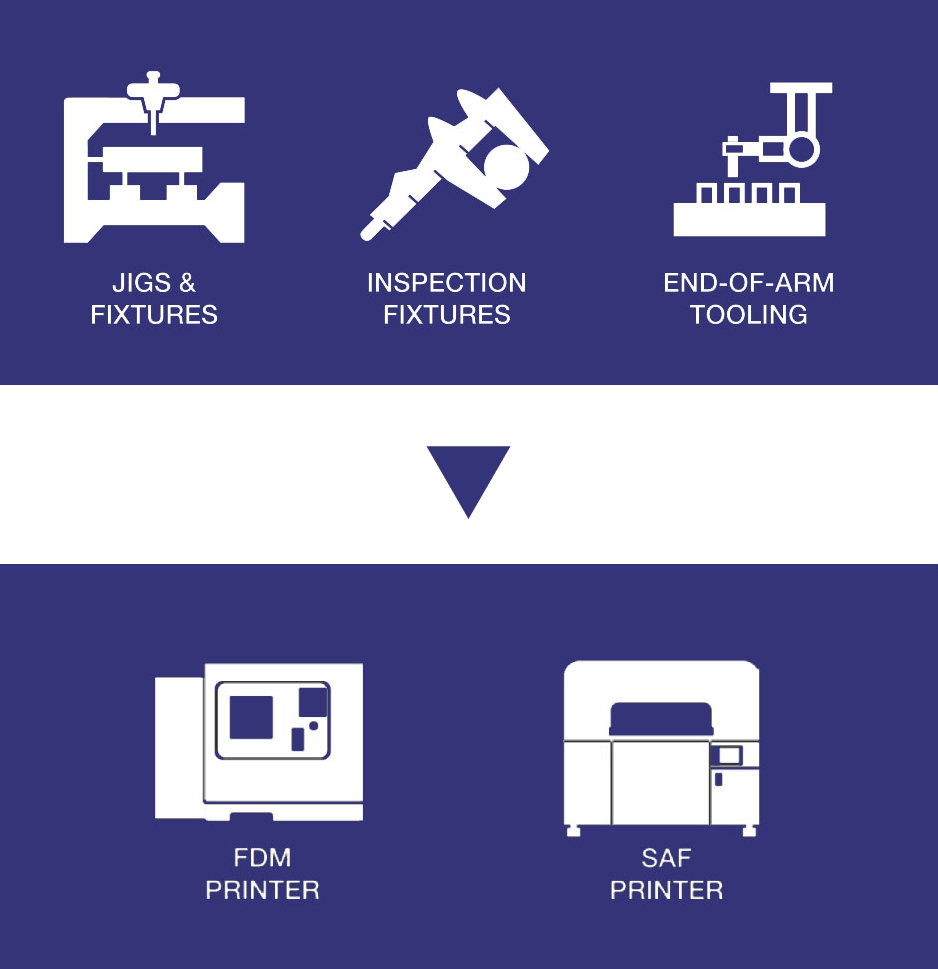
Production Ramp Up
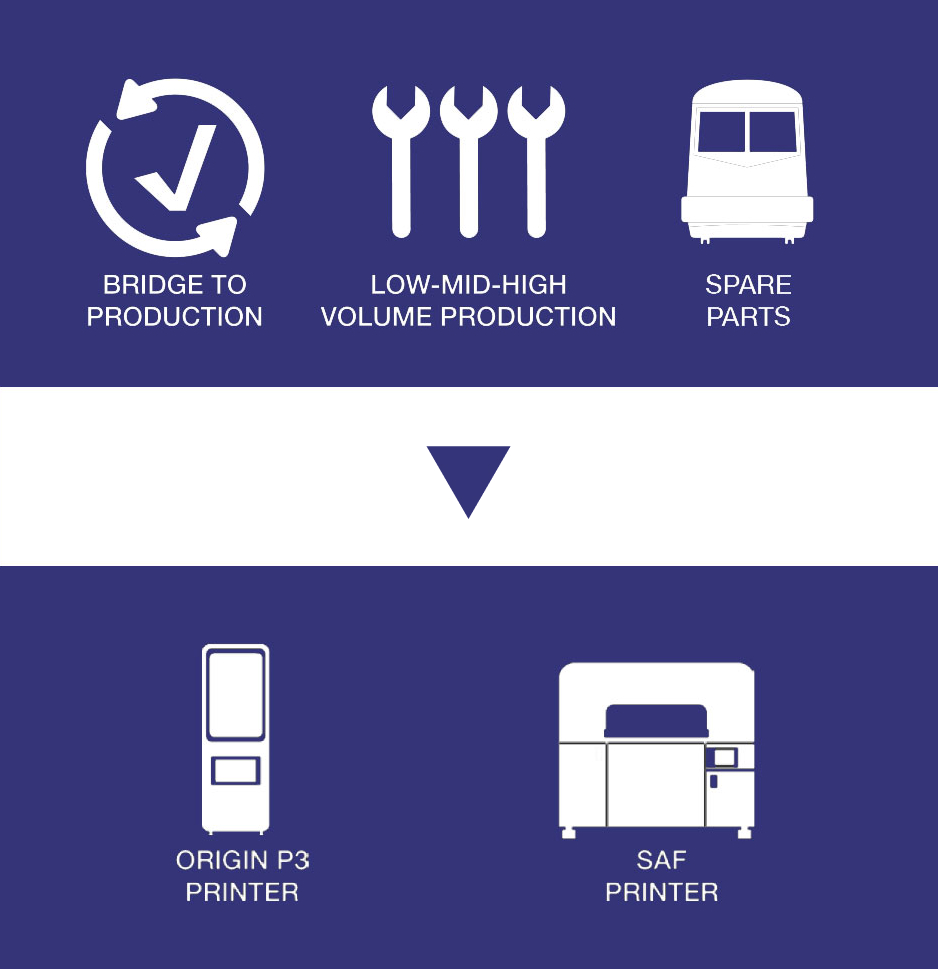
Related Posts
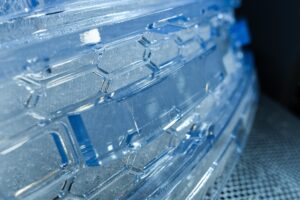
3D Printing in Automotive Industry: What can you make?
The aftermath of the global pandemic has spurred a rapid transformation in the automotive industry, impacting both its products and manufacturing processes. In the midst
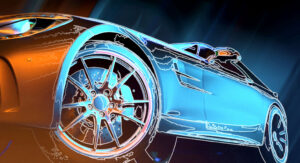
The Automotive Revolution: How 3D Printing is Driving Change
In the fast-paced world of car and truck manufacturing, innovation is key to staying ahead of the competition. One such breakthrough that has transformed the
Industrial 3D printers excel in large-scale, high-precision applications for industries like aerospace and automotive. They offer advanced technologies and automation features. In contrast, commercial 3D printers are more affordable and suited for small-scale projects, prototyping, and consumer goods production.
3D printing offers advantages in automotive manufacturing, such as rapid prototyping and complex part creation. However, it is unlikely to fully replace traditional methods like injection molding and stamping, which are more suitable for mass production and cost-efficiency. A hybrid approach that combines both technologies is more probable.
Adopting 3D printing in the automotive industry faces challenges like high costs, slower speed, material limitations, and ensuring consistent quality. Scaling for mass production and addressing intellectual property concerns also pose obstacles. Nonetheless, ongoing research aims to overcome these challenges, making 3D printing increasingly valuable for prototyping, customization, and niche applications.
Subscribe to get the latest news and product updates from R&D
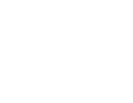
A TOP RESELLER OF
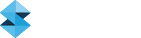
- Instant Quote
- 3D Printers & Systems
- 3D Printing Services & Consultation
- Shop Materials & Consumables
- Tech Support
- Material Specs & Docs
- About R&D
© 2023 R&D Technologies Inc. All rights reserved.

Ready to start your next project? Talk to our expert team today. Get on-demand production and rapid prototyping.
Interested in purchasing a 3D printer? We’ll help you find the perfect fit. Request a sales quote .
- 3D Printing Videos
- Company News
- Company Events
- Quoting Tool
- Material Specs and Docs
- 401-885-6400
Your browser is not supported
Sorry but it looks as if your browser is out of date. To get the best experience using our site we recommend that you upgrade or switch browsers.
Find a solution
Welcome to www.automotivemanufacturingsolutions.com. This site uses cookies. Read our policy .
- Skip to main content
- Skip to navigation
- hot-topics IN FOCUS
- Sustainable Production
- Electric Vehicle Production
- Manufacturing Engineering
- Digitalisation and Automation
- Newsletters
- Sustainable Steel Survey

Discover our latest print and digital editions
- Back to parent navigation item
- Press and Stamping
- Additive/3D Printing
- Casting/Forging
- Measurement
- Video and Audio
- AMS Automotive Evolution Summit On-Demand
- Live Lounge
- AMS Automotive EVolution Livestream
- Hyundai Kia
- Mercedes-Benz
- Two-wheeler
- Heavy vehicle
- Factory Investment
- Factory Expansion
- Factory Closures and Consolidation
- Lightweighting
- Automotive Materials Innovation
- Lean manufacturing
- Operational Excellence
- Smart Factory and Industry 4.0
- Cost Efficiency
- Case Study: ArcelorMittal Webinar
- Whitepapers
- DESIGN4PRODUCTION
- Automobil Produktion Kongress
- Automotive Wire Harness
- Automotive Evolution North America
- Automotive Evolution Europe 2022
- Automotive Wire Harness 2022
- Watch past events on-demand
- North America
- South America
- Africa and Middle East
- AMS Media Pack 2024
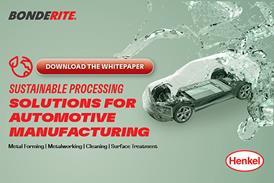
- More navigation items
3D Print Case Study: Volkswagen
2020-06-24T11:14:00+01:00
- No comments
Volkswagen is investigating the potential of additive manufacturing to take its applications beyond prototyping

VW glovebox 3D print
With the introduction of a material with end-use properties, 3D printing is now considered a serious production tool – especially for small series manufacturing.
The challenge: Prior to embracing additive manufacturing, The Plastic Business Segment (a division belonging to Volkswagen Group Components) had no ability to test component parts in an end-use material – instead having to rely on prototyping with materials such as PA12, which were not comparable to the final part.
The solution: Volkswagen realised the cost efficiencies of using selective laser sintered (SLS) parts in the prototyping phase. Having employed Ricoh 3D’s manufacturing capabilities and polypropylene material, VW is now able to print parts to test production systems before investing in a final injection mould. Consequently, VW process engineers can prepare and optimise the production chain weeks, if not months, before the first injected parts are ready.
Materials such as PA12 can only be used to test the geometry of a part, but with polypropylene Volkswagen engineers also have the benefit of testing processes like welding and assembly as the prototype is created in the final end-use material.

VW is able to print parts to test production systems before investing in a final injection mould
Volkswagen is able to use the polypropylene sintered parts in its production line welding stations without modifying the process parameters, unlocking significant gains in efficiency.
Volkswagen realise the potential of AM to take their applications beyond prototyping. The Ricoh technology and polypropylene material were put to use for a short run of glove box compartments in customised emergency vehicles, where conventional manufacturing methods were not cost effective and unable to meet the lead time.
The glove compartment was tested for high-cycle fatigue by opening and closing 20,000 times at different temperatures (23°C, 70°C, -23°C and 55°C), passing every test. This would simply not have been possible with PA12.
The parts were then welded together with injected moulded components, demonstrating that SLS parts can be included in manufacturing processes without any extra steps.
If SLS parts can replace injection moulded parts 1:1, engineers can effectively predict the life of a final injected part using polypropylene sintered equivalents. An advance such as this in the accuracy and efficiency of Volkswagen’s manufacturing process, is opening the doors for customisation and small series production.
Related articles
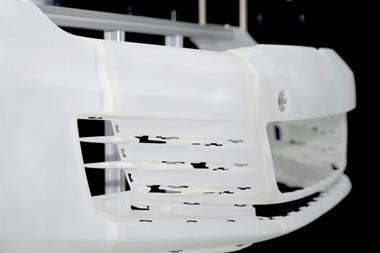
Five ways that 3D printing is transforming automotive manufacturing
2020-06-24T11:23:00Z
By Mark Dickin, 3D printing specialist
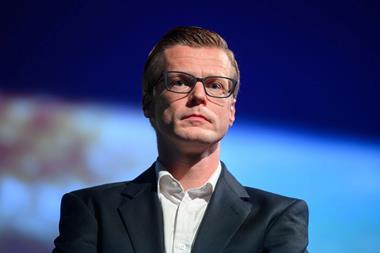
Danny Auerswald to lead VW Saxony, bringing global production expertise
2024-05-10T13:45:00Z
By Ilkhan Ozsevim
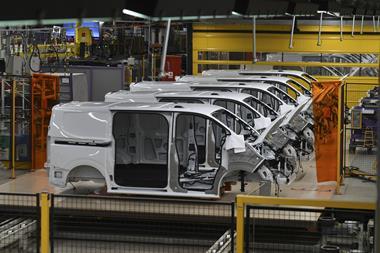
Ford Otosan manufacturing for an economy in transition
2024-05-08T15:50:00Z
By Mark Smyth
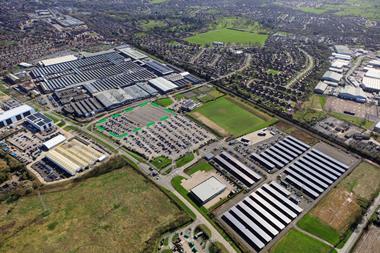
Bentley prepares electric future with groundbreaking for new paintshop
2024-04-30T13:49:00Z
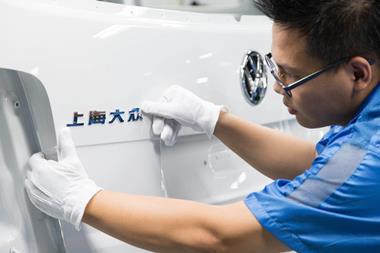
VW focuses on Chinese market boosting cost competitiveness and local partnerships
2024-04-29T17:53:00Z
By Nick Holt
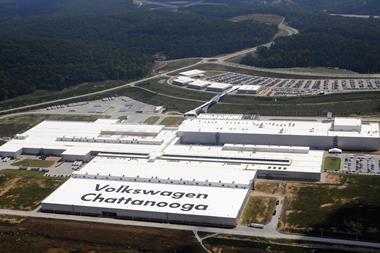
Volkswagen workers in Tennessee vote to join UAW
2024-04-23T14:32:00Z
By Anushka Dixit
No comments yet
Only registered users can comment on this article., more volkswagen.
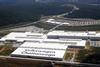
2024-04-23T14:32:00Z By Anushka Dixit
The result of the vote was clear, with 2,628 workers casting their support for the union against 985 nays. This victory makes VW’s Chattanooga’s the first foreign-owned car plant in the southern US to unionise through an election since the 1940s, marking it as a monumental win for the UAW.
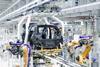
Floods affect manufacturing facilities in Slovenia
2023-09-11T15:23:00Z By Megan Kelly
The effects of the worst natural disaster ever to hit the country are spreading across the continent.
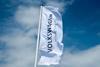
VW and Audi strengthen partnership with SAIC and Xpeng to expand EV production and development in China for China strategy
2023-08-04T12:06:00Z By Ilkhan Ozsevim
Volkswagen invests $700m in Xpeng and will partner on tech and platform, while Audi expands partnership with SAIC and will produce vehicles on one of its platforms.
Automotive Manufacturing Solutions (AMS) is the essential resource for automotive manufacturing professionals and suppliers globally.
Join us today and access AMS’s wealth of global news, insights, intelligence and content, and to make valuable connections with your peers from across the automotive industry.
Register FREE today
Your free registration includes:
- Weekly AMS News and twice quarterly AMS In Focus newsletters
- Regular podcast series
- Twice yearly magazine (digital)
- Special offers
- Reports from key manufacturing shows
- Access to the digital news archives
- Your Data Matters
- Cookie Policy
- Advertising specifications
Site powered by Webvision Cloud
- Driving Innovation in The Automotive Industry with 3D Printing
- Case Studies

case-studies Description
- Automotive & Transportation
Henkel and GENERA Partner with KTM Technologies to Drive Innovation in The Automotive Industry
The Challenge
KTM is an Austrian manufacturer of motorcycles and sports cars. They were looking for a solution to improve a specific clamping component used on the rear suspension system on the Duke and RC 390 Bike. This component is used to mount a part of the performance suspension from WP Suspensions. The KTM Technologies team knew that a more traditional manufacturing method such as injection molding would simply be too expensive given the small series production.
The Solution
KTM found that leveraging additive manufacturing with the GENERA G2/F2 system was the best fit for their production goals. After evaluating the Loctite 3D printing materials portfolio, KTM determined that Loctite 3D 3843 HDT60 High Toughness Matte Black was the best solution to meet part requirements. This material offers the characteristic of a high strength engineering plastic, similar to ABS, with good impact resistance and excellent surface finish.
By leveraging 3D Printing and the additive process, KTM Technologies were able to create a cost-effective solution using LOCTITE 3D 3843 HDT60 High Toughness Matte Black that was registered on the International Material Data System (IMDS), the automobile industry’s material data system used by majority of OEMs across the globe. With this system, all materials are collected and archived, to ensure automotive manufacturers and suppliers are meeting all standards, laws, and regulations. By securing a registration from IMDS, the visibility for 3D printing in automotive production sharply increases, highlighting it’s potential as a cost-effective, compliant, and agile solution to small series production. Using GENERA printing technology and LOCTITE material, the part designed was among the first IMDS listed and end-use approved automotive parts manufactured with photopolymer technology.
Developed together with

Related Case Studies

Betatype Case Study Illustrates Cost and Time Savings of Using 3D Printing to Fabricate Automotive Components

Share this Article
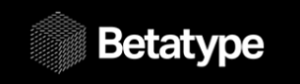
Some of the benefits provided by 3D printing include high cost-per-part, productivity, and volume, especially when it comes to using metals. Betatype recently completed a case study that demonstrates how the advantages of metal 3D printing can be properly leveraged for applications in automotive parts production. It focuses on Betatype’s use of laser powder bed fusion (LPBF, also called Powder Bed Fusion, DMLS and SLM) 3D printing and optimization technology to, as the case study puts it, challenge “the current status quo” by producing 384 qualified metal parts in one build, which helped lower both lead time and cost per part.
“When it comes to automotive and other consumer-facing industries focused on producing high volumes of parts at low costs, the current generation of Additive Manufacturing (AM) processes is generally considered incapable of meeting these needs,” Betatype explained in its study. “The key to making AM productive enough for wider adoption across these high-volume industries, however, lies in process economics – choosing the most effective manufacturing process for each part. Combining these principles with Betatype’s knowledge of the limits of additive – as well as how and when to push them – together with the company’s powerful optimisation technology, supports customers with the design and production of parts that not only perform better, but that are economically viable against existing mass production technologies.”
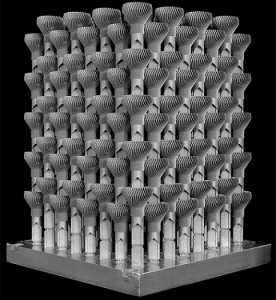
Production build of automotive LED heatsinks by Progressive Technology on an EOS M280.
You’ll often hear people in the 3D printing industry saying that one of the benefits of the technology is its ability to offer greater design freedom than what you’d find in more conventional manufacturing process. While this is true – 3D printing can be used to produce some pretty complex geometry – that doesn’t mean it’s without its own problems. It’s necessary to understand these constraints in order to find applications that can fit with the technology, and be used in high volume manufacturing as well.
Processes like die casting are capable of creating millions of components a year. 3D printing is valuable due to its capability of using the least amount of material to provide geometrically complex parts. Often 3D printing just doesn’t have the manufacturing volume or part cost to be an economical choice. But, this may not be the case for long.
According to the case study they looked at, “how it is possible to combine the innate geometric capabilities of AM with increased production volumes of cost-effective parts and improved performance” The team looked at “the Automotive industry’s switch to the use of LED headlights, which brings with it new challenges in thermal management.”
Most LED headlights need larger heatsinks, which are typically actively cooled. Betatype realized that the geometry of these metal parts would make them a good candidate for metal 3D printing, which is able to combine several manufacturing processes into just one production technique.

Betatype realized that LPBF would be ideal during the component’s initial design stage, and so was able to design the component with in-built support features. This made it possible to stack multiple headlight parts without requiring any additional supports; in addition, the company maintains that completed parts could be snapped apart by hand without any other post-processing required. This claim is something that we are highly skeptical about. No destressing or tumbling, shot peening, HIP or other processes usually result in parts that look different from the ones in the images given to us.
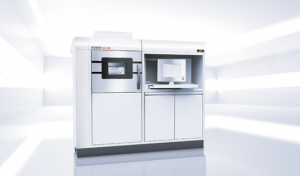
[Image: EOS]
“Through specific control parameters, the exposure of the part in each layer to a single toolpath where the laser effectively melted the part was reduced significantly, with minimal delays in between.”
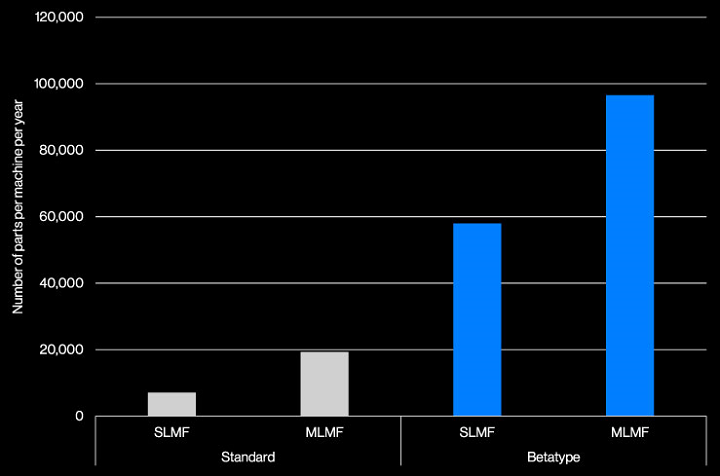
13 x the productivity per system. Estimated Number of Parts per Machine per Year/Model built on build times provided by Progressive Technology for SLMF system (EOS M 280) and Renishaw AMPD for MLMF system (RenAM 500Q).
One of the large drivers in part cost is equipment amortization, and it’s important to lower build time in order to make parts more cost-effective. By using LPBF 3D printing and its own process IP and optimization algorithms, Betatype claims to have reduced cost-per-part from over $40 to less than $4, and lower the build time from one hour to less than five minutes per part – ten times faster than what a standard build processor is capable of performing. This would be a huge leap in capability for metal printing if these cost estimates stack up.
On single laser systems, like the EOS M 280 and Renishaw’s RenAM 500M , Betatype says that lowered the build time for all 384 parts from 444 hours to less than 30 hours; this number went down even further, to less than 19 hours, by using new multi-laser systems like the SLM Solutions 500 and the RenAM 500Q .
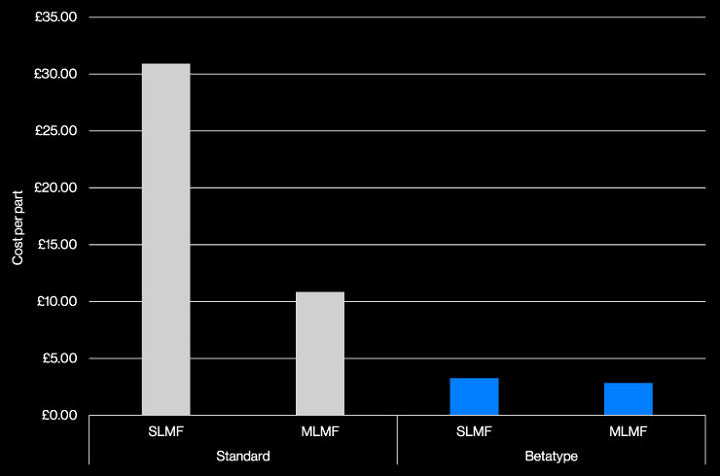
Up to 90% reduction in part cost. Estimated Cost per Part / Model built on build times provided by Progressive Technology for SLMF system (EOS M 280) and Renishaw AMPD for MLMF system (RenAM 500Q).
Betatype’s claims that their customer was able to achieve a productivity gain of 19 times the old figure per system in a year – going from 7,055 parts to a total of 135,168.
The case study concludes, “With an installation of 7 machines running this optimised process, volumes can approach 1 million parts per year — parts that are more functional and more cost-effective.”
It always good to show performance that is a step change ahead of what everyone thought possible. It is also significant that companies are making detailed case studies and verifiable claims as to output and yield. Betatype’s Case Study shows very promising numbers and we hope that productivity can indeed reach these heights with their technology.
Discuss this story and other 3D printing top ics at 3DPrintBoard.com or share your thoughts in the Facebook comments below.
Subscribe to Our Email Newsletter
Stay up-to-date on all the latest news from the 3D printing industry and receive information and offers from third party vendors.
- Enter your email address *
- Name This field is for validation purposes and should be left unchanged.
Recent News
Boring Company Alum Score $9M for Advanced Composites Manufacturing
3D Printing News Unpeeled: Hypersonics, Tidal Power, Indian Rocket Engine
3D Printed Art
3D Printed Food
3D Printed Guns
You May Also Like
3dpod episode 198: high speed sintering with neil hopkinson, vp of am at stratasys.
Neil Hopkinson, a pioneering 3D printing researcher, played a pivotal role in developing a body of research that is widely utilized today. He also invented High Speed Sintering (HSS), also...
GE Additive Transforms into Colibrium Additive in New Brand Move
One of the largest and most compelling companies in the 3D printing industry, GE Additive, has undergone a rebrand. Now, known as Colibrium Additive, the company and its new name...
HP & INDO-MIM Collaborate to Boost Metal 3D Printing in India
HP Inc. and INDO-MIM, a US- and India-based supplier of metal injection molding (MIM) powders and contract manufacturer, have announced that the two companies will collaborate to accelerate additive manufacturing...
Nylon 3D Printed Parts Made More Functional with Coatings & Colors
Parts 3D printed from polyamide (PA, Nylon) 12 using powder bed fusion (PBF) are a mainstay in the additive manufacturing (AM) industry. While post-finishing processes have improved the porosity of...
Print Services
Upload your 3D Models and get them printed quickly and efficiently.

- 3DPrinting Business Directory
Site Sponsor
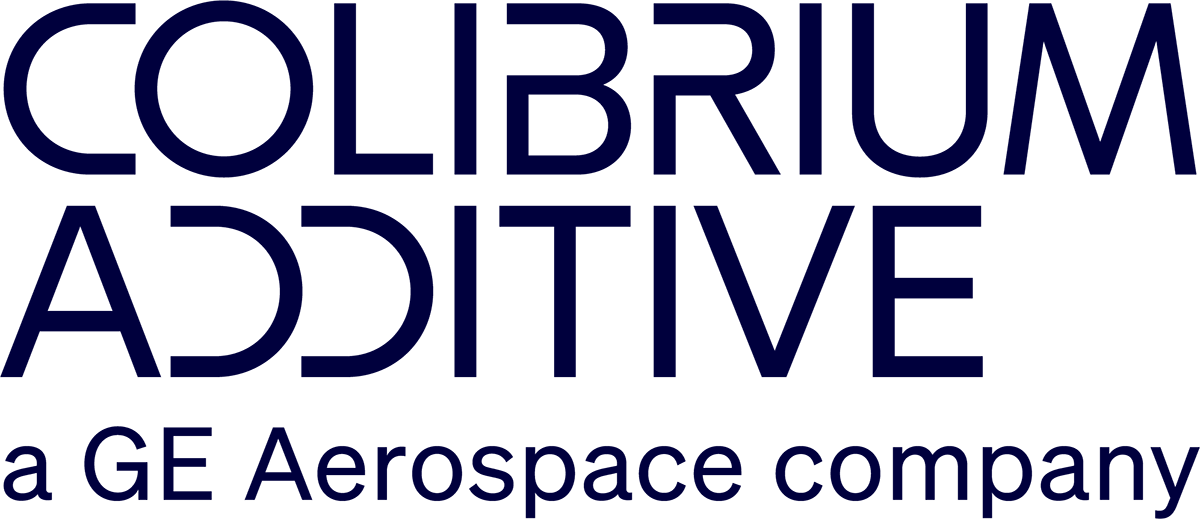
Additive Manufacturing Strategies
Networking & Intelligence Summit, February 4-6, 2025
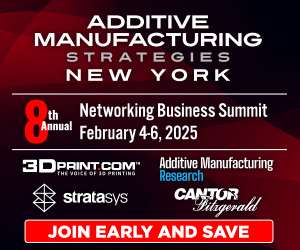
3D Printing jobs around the world.
- I would like to also register for free and access proprietary industry data from SmarTech and 3DPrint.com
3D Printing Guides
- Desktop 3D Printer Buyer’s Guide
- 3D Scanner Buyer's Guide
- Metal 3D Printer Guide
- Industrial Polymer 3D Printer Guide
- The 3D Systems Zone
- The HP Zone
- Desktop Metal Zone
- Bioprinting Zone
- The Space Zone
- 3D Printing Stocks Zone
Register to view and download proprietary industry data from AM Research and 3DPrint.com Questions? Contact [email protected]
Already have an account?
- First name *
- Last name *
- Password * Enter Password Confirm Password
- I agree to receive the 3DPrint.com Daily newsletter and promotional email correspondence.
- Phone This field is for validation purposes and should be left unchanged.
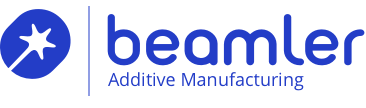
Business cases: 3D printing in the automotive industry
- On August 23, 2018

This article discusses how 3D printing in the automotive industry is largely impacting all the segments of the sector and provides you with successful business cases .
1. Introduction
2. Automotive driving AM growth or AM driving automotive growth?
3. Processes and quality improvements through Rapid Prototyping
4. Customized Tooling
5. Decreasing tooling costs
6. Inventory reduction
7. Weight reduction driven by the complexity of designs
8. Part simplication leads to a shorter assembly process and lower production cost
9. Simplified supply chain
10. Conclusion
Introduction
Having several years of experience in the 3D printing industry, we have come across many examples of when additive manufacturing helped companies from various industries improve the technical and business aspects of parts and products. For instance, 3D printing in the automotive sector has helped manufacturers decrease the cost of product development while, in the aerospace industry, it allowed aircraft makers to build lighter planes.
Even though the implementation of a new approach to manufacturing might have been challenging at the beginning, these companies experienced a positive impact on their production process and, consequently, in their end-products. In fact, the benefits were perceived in so many aspects of their operations that these companies intensified their investments in the technology and transformed it into a vital part of their manufacturing process. In my opinion, that is one of the main indicators that industrial 3D printing is here to stay and is the future of manufacturing.
For that reason, we have decided to write a series of articles with real-life business cases to demonstrate the impact of 3D printing in the automotive, medical and other industries. The first article of this series focuses on the automotive industry and the significant gains obtained by companies in the sector through additive manufacturing.
Automotive driving AM growth or AM driving automotive growth?

When additive manufacturing emerged as a production technique, automotive companies were using it to create prototypes of parts with the goal of checking their form and fit . At the time, the technology allowed them to produce aesthetically pleasant parts. However, these parts lacked the required strength and durability. It was clear that the technology still had a long way to go. Nonetheless, the automotive industry, which was one of the first sectors to identify the potential of additive manufacturing, played an important role in accelerating the growth of this revolutionary manufacturing technique. The major players in the market spent (and spend) an enormous amount of time and money into research and development of additive technologies.
Nowadays, 3D printing has advanced to the point where carmakers are able to also use it for the production of end parts. It is safe to say that these advancements are paving the way for interestingly new approaches for conceiving and producing cars. Most importantly, additive manufacturing technologies are playing an important role in driving competitiveness and will exert great influence as a source of product innovation and as a driver of supply chain transformation.
Automotive companies who implemented additive manufacturing are benefiting from reduced lead times, decreased costs and new ergonomic designs. This compilation of business cases highlights some of these benefits and explains how AM has played an important role in the development of products in the sector.
Processes and quality improvements through Rapid Prototyping
The design phase of a new product usually requires several iterations before the final design is decided. Depending on the project, this process can take weeks, if not months. However, AM is giving carmakers the ability to streamline and speed up this crucial stage of product development. One of the most considerable advantages of the technology is that it provides companies with the ability to build various alternatives of a product at an extremely low cost. Being able to produce a physical model for each variation makes it easier to visualize and compare all the design alternatives. Thus, supported by these physical models, carmakers are able to refine the design of their products in a shorter period of time and with little additional cost.
A good example comes from one of the major tire producers in the world. During the design phase, the company uses rapid prototyping to produce several variations of the product being developed. The final design is decided after checking the touch and feel of all the alternatives. What is curious in this case, is that aside from the benefit of providing its OEM customers with prototypes of customized options, the company also gains a valuable competitive advantage over its competition. Why? Because some of its competitors are restricted to designs specifications when sharing newly developed products with their customers.
Another advantage of AM is the high degree of design flexibility the technology offers. This allows companies to build a large number of prototypes, enabling car manufacturers to test for quality well ahead of the production schedule. For instance, during the preproduction and design process of its products, GM’s rapid prototyping department produces test models of more than 20 000 functional components .
Customized Tooling
The production line of automotive vehicles heavily relies on tooling for assembling and manufacturing high-quality products with consistency. Additive manufacturing allows automotive companies to customize car assembly tools by improving its functionality and reducing its weight at a lower cost than traditional manufactured tools. There are even cases where completely new tools are developed for specific, customized designs.
This type of tool customization results on a productivity increase in the assembly line of the factory floor. Let’s take BMW as an example. The automotive giant customizes hand tools for their line production staff. These customized versions are ergonomically designed and are 72% lighter than the original counterparts. According to Deloitte , BMW’s customization of these hand tools helped the company reduce the overall costs and the project time by 58% and 92%, respectively.
Curious about the cost for custom 3D printed parts?
Decreasing tooling costs.
Automotive OEMs prepare tooling and investment castings for a specific component during the design phase of a new product. As the preparation of tooling and castings for particular designs happens well before production starts, manufacturers are usually faced with one expensive and time-consuming problem: every time there is a change in design means that tooling will also need to be adjusted.
Another advantage of AM is that it enables companies to be less dependent on tooling and casting since it allows for the creation of prototypes that do not require either of them. According to Ford, developing and creating a prototype for an engine manifold with traditional manufacturing can take up to four months and cost around half a million dollars . However, with 3D printing, the company was able to develop several iterations in only 4 days and 99.4% cheaper – only $3000. In the video below Ford explains how they use additive manufacturing, check it out.
Inventory reduction
An important competition aspect of the sector’s aftermarket segment consists of the availability and the time to deliver parts. The majority of part distributors tends to keep in stock only the most common sold parts due to the high prices of maintaining an inventory of parts which are sold sporadically. For that reason, low demand and high-priced parts are usually kept at remote locations.
Another segment of the market which has a similar problem in regards to demand is the performance parts segment. As most consumers consider these optional parts a luxury, distributors are faced with a high fluctuation in demand .
A great solution to solve that issue and quickly supply the demand for less requested components lies in the capabilities to produce parts on-demand using 3D printing technologies. Not only will distributors be able to maintain the availability of these components without the need for inventory but also will experience a reduction in operational costs. One company taking advantage of additive manufacturing to create replacements for spare parts of its classic cars is Porsche . The production run for this type of vehicles is extremely short and, as a consequence, the costs of storing replacement components are nearly prohibitive. Therefore, the company is using the technology to make these rare components available for collectors.
But the distributors of these 2 segments are not the only ones that can benefit from on-demand production. Additive Manufacturing may also be the ideal way to go to supply parts for vintage vehicles and more recent models that are not in production anymore. If combined with 3D scanners, dealers and consumers are able to easily scan the design of the component and replace it with a 3D printed functional part. If this seems farfetched to you, I am pleased to tell you that it is already happening. The American television host and vintage car collector, Jay Leno, owns over 280 vehicles . His collection is estimated to be worth more than $50 million . Leno uses a software known as Rapidform, which was acquired by 3D systems in 2012 , to transform 3D scan data into a CAD model enabling him to 3D print and replace components for his car collection.
Weight reduction driven by the complexity of designs
Fuel efficiency improvement is a constant effort amongst carmakers due to the rise in demand for compliance of industry standards and for the revenue growth it generates through delivering value to consumers. Weight reduction is certainly one of the ways to go to improve mileage in automotive vehicles. Additive Manufacturing provides car manufacturers with the ability to perform alterations at a structural level of the desired parts. The redesign of these parts using lattice structures does not compromise its structural strength and results in significant weight reductions.
The aerospace industry is a great example of how the automotive sector can use additive manufacturing to produce lighter cars. Since fuel accounts for a third of the revenues, reducing the aircraft’s weight is crucial. Airbus, for instance, uses AM to produce lightweight versions of components used in all their aircraft. The company used direct metal laser sintering (DMLS) to optimize the design of nacelle hinge brackets for the Airbus A320. The additive manufactured part was 64% lighter and it was still as strong as its counterpart, without any decrease in performance.
Part simplification leads to a shorter assembly process and lower production cost
One of the major limitations of traditional manufacturing techniques is the lack of flexibility when designing components. As a result, one component may require a large number of parts. The problem with that lies in the fact that every new part added results on a longer and more complicated assembly process.
Additive manufacturing enables companies to create complex designs that require fewer parts to produce these components. Consequently, companies are able to decrease the assembly time and also experience a reduction in quality problems.
Delphi, an Irish tier 1 supplier for the automotive industry, was able to make an aluminum diesel pump as a single piece using a metal 3D printing technique known as Selective Laser Melting. By doing so, the company achieved an impressive reduction in the number of parts needed for the pump which prevented a number of postprocessing steps and simplified the assembly process. The end result was a final product of higher quality, since it decreased the fluid low time and is less susceptible to leakage , and with lower production costs.
Simplified supply chain
The automotive sector currently operates with gigantic supply chains. Each OEM deals with hundreds, if not thousands of companies that supply different automotive components. This requires an extremely efficient and complex supply chain management process which requires a lot of time and money. For that reason, OEMs are starting to put a lot of effort to simplify their supply chain.
During the third quarter of 2013, Ford announced plans to decrease the number of suppliers in 40% – for the record, the company was sourcing components and parts from more than 1250 companies. As the American automaker became faster at producing innovative parts with little involvement from suppliers, they saw an opportunity to decrease time and money spent on sourcing parts.
Sign up to Newsletter
About beamler.
We help manufacturers unlock the full potential of industrial 3D printing.
Trusted by engineers in some of the largest multinationals, Beamler offers 24/7 access to the massive production capacity that only a global network of dedicated manufacturing partners can provide.
Latest articles

Is 3D Printing with Silicone possible?
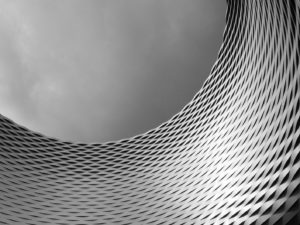
Scalmalloy: high performance aluminum for 3D printing
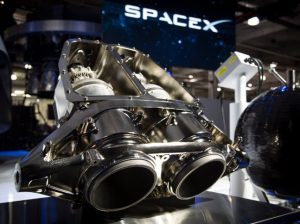
3D printing for satellites and space industrie
Suggested articles.

3D Printing PEEK, PEI and ULTEM
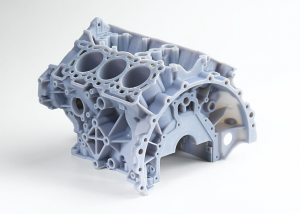
What is 3D Printing?

What are the advantages of metal 3D printing?
Do you to 3d print a custom part.
3D Printing in Silicone
3D Printing in TPU
3D Printing in Nylon
3D Printing in Stainless Steel
3D Printing in ABS
3D Printing in TPE
3D Printing in Aluminum
3D Printing in Copper
3D Printing in Tungsten
Beamler: Online 3D Printing Service • Global network • ISO 9001 partners • Specialized in 3D printing silicone, tungsten, tungsten carbide, copper, composites and technical ceramics.
Customer service: E-mail: [email protected] Phone: +31 (0)6 5789 7508
Beamler BV The Netherlands
AM processes
3d printing materials, services and resources.
Accepted payment methods: Creditcard, iDEAL, PayPal
Copyright 2021 Beamler

- 877-219-6757

3D Printing helps to develop the Concept Cars of Tomorrow
Vital Auto is an industrial design studio with rooted expertise in the automotive industry. It is situated in the heart of the UK’s auto industry. The company’s portfolio of clients includes a variety of the major automotive manufacturers. Some of these are Volvo, Nissan, Lotus, McLaren, Geely, TATA, and more.
Vital Autos VP of Innovation & Experiential Technology Shay Moradi said “Clients typically come to us to try and push the boundaries of what’s possible with the technology available”. Manufacturers rely on Vital Auto when they don’t have time for experimentation themselves. They take on any challenge to turn ideas, initial sketches, drawings or technical specifications into a fully realized physical form.
The Making of a Concept Car
Founded in 2015, Vital Auto’s story began when three friends quit their jobs. They then decided to set up a shop, fittingly – in a garage. The first contract the company took on was for NIO EP9 supercar concept. This immediately set the team on a course to producing extremely realistic, high-fidelity vehicular prototypes.
The team at Vital Auto develop cars from a blank sheet. They design all the mainframes, all the exterior and interior elements, open/closings, and interactive elements. Dependant on the client request, the team will start anywhere within the range of a sketch on a piece of paper to an already designed vehicle. Between five to 30 people work on a single concept. A project could typically take anywhere from three to 12 months.

A typical show car goes through a lengthy design stage with up to a dozen core design iterations in this time. Until the design meets the expectations of the customer, there can be continuous further iterations of smaller components.
“It’s all well in our industry to look at virtual properties as a means of evaluating a product before it goes to market. However, I think there’s always going to be a place for physical manufactured objects as well. There’s nothing that beats the sensation and feeling of holding an object in your hands with the correct weight. With the correct proportions. And the dynamics of how the physical environment changes your perception of that physical object.“
How Vital Auto have Developed their 3D Printing Department
“Most of our customers will come to us with a new idea, an innovative idea. Something that’s never been done before. The challenges for us are new every single day and they’re endless”. said Anthony Barnicott, Design Engineer in charge of additive manufacturing. “These challenges can range. How can we produce this number of parts in this amount of time. Or how can we make a part that achieves a particular weight while still achieving a particular performance.”
Traditional show cars are usually made just from milling clay. The team at Vital Auto also uses three- and five-axis CNC milling, hand forming, hand clay modeling, and GRP composites. Often these traditional processes are not ideal for producing custom parts required for one off concepts.

“We’ve used 3D printing from day one. We wanted to introduce it to our manufacturing processes. Not only to reduce costs, but to give the customer more diversity with their designs and their ideas,” said Barnicott.
Today, Barnicott runs the whole 3D printing department. This includes 14 large-format FDM printers, five Fuse 1 SLS Printers and three Formlabs 3L large-format SLA printers.
“In terms of capacity, all those printers have run 100%, 24/7, pretty much since day one. We use these printers for all areas of our concepts and designs. Typically, we would use the Fuse 1s for our production-based parts. We would use our Form 3Ls for our concept-based parts,” said Barnicott.
Manufacturing Complex Designs From Multiple Materials With the Form 3L
“We use the Form 3L machines for anything that is an A-class finished surface. So typically in an automotive environment, an interior where you have parts that are not being trimmed with leather or Alcantara or some sort of cloth material. Formlabs materials give us a nice, smooth finish for our painters to work with. We can use these parts straight out the printer, straight onto a vehicle,” said Barnicott.
“What interests me most about the Form 3L machines is their versatility. The ability to do a material change in less than five minutes. The variability of those materials going from a soft, flexible material to a hard and rigid material for us is priceless,” said Barnicott.
The 3L has multiple materials that are used by the whole team for applications. For example:
“It’s a common challenge for us as a business where customers will approach us with a proprietary product and want to encase it in their own design. Once, a customer approached us with a proprietary air vent from another vehicle that they wished to have inside their own interior. We used 3D scanning technology to reproduce this part digitally and then created an external skin. We first produced this in the Draft material to test out the design and allow the customer to verify it. From there, we moved to the White material to produce a production-ready part.”

Switch Packs
“When working with incredibly intricate designs, such as small switch packs, what we’re able to do is use multiple materials to achieve a mechanical product that not only functions correctly, but can be used in a real-world environment. [For these switch packs], we combined harder materials, such as the Tough 2000 for the top surface, with the lighter, more cost effective materials for the internals.”

“Typically, door seals for automotive applications can be incredibly costly to produce. There’s simply no other way other than extrusion molding to produce them. This comes at, not only a very large tooling cost, but also a long lead time as well. We were able to experiment with one of Formlabs’ newest materials, the Flexible 80A . The Form 3L enabled us to produce sections of this door seal overnight. This was to test various geometries and was printed within 50 microns of the actual design.”

The Form 3L empowers the team to produce multiple iterations of parts, all within 24 hours in most cases. Vital Auto ended up buying three different machines. This is so they could produce three iterations of a part all at once, even using three different materials. They can then pass on cost savings to the customer and offer better value for money. They do this by showcasing multiple options for the same price.
“ One of the beauties of using additive manufacturing is the compression of a time frame. So what do you do in that span of time that you have freed up? We sort of see it as extending the possibility space into imagining alternatives. Adding more iteration loops in the process,“ said Moradi.
“There are many products we produce that we simply wouldn’t be able to without our Form 3Ls. With some of the most advanced manufacturing techniques, such as seven-axis CNC machining, we’d be able to produce these parts. But it would come at a huge compromising cost”
Complementing CNC Machining for Mechanical Parts With the Fuse 1
“The Fuse 1 one was our first venture into SLS technology. As a small business, this is a technology we thought we would never be able to have on site. With the Fuse 1, not only do we have one of the machines. But we actually have five of the machines on the site.
What these machines enable us to do is produce structural mechanical parts very quickly. Not only for testing but for physical applications in most of our concepts. This process would have typically been done by CNC machining. Either on our site or off site, depending on the geometry. And we would have to wait two to four days to get the parts in our hands. The Fuse 1 enables us to cover all of this on site and have parts in our hand in most instances less than 24 hours.” said Barnicott.

The Fuse 1 is mainly used by the team for mechanical parts. Such as door hinges, door internals, door handle inners and structural applications. These parts can be used straight off the printer with minimal finishing. Some of the applications where the team used the Fuse 1 include:
“A lot of automotive interior parts can be incredibly tricky to produce without going down the traditional injection molded route. Items such as internal air ducts and vents, are items that are never seen. But yet require a large cost to produce. We use the Fuse 1 to produce these parts. It allows us to be much more versatile with the designs we put in the vehicle without incurring the large costs that they would typically have.”

Brake Caliper
“Sometimes we produce parts where the customer simply wants to see what their brand will look like on a specific part. That means we have to produce a part rather quickly so we can apply their brand to it. We use the Fuse 1 to produce these parts. Such as a brake caliper, and we can produce the logo in different areas of the caliper in different colors for the customer to review.”

Interactive Concept for a Supercar
“3D printing has allowed us to combine both the SLA and SLS materials to work our way through design iterations on a specific project. This allows us to quickly produce multiple iterations, combining both processes, using them for their specific properties, to achieve a final design. This can be anything from mechanical parts to clear parts to check their optical quality and output.”

It’s often said that additive manufacturing is here to replace subtractive manufacturing. The Vital Auto team sees benefits in combining different technologies to leverage their best qualities.
The Vital Auto team don’t agree with the belief that additive manufacturing is here to replace subtractive manufacturing. They see the benefits in combining both technologies to utilize their best qualities.
“We use the two processes together to help support each other. We have many parts where we would use subtractive manufacturing. And then use additive manufacturing to produce all the finer details. This allows us to have a much more cost-effective way of producing a lot of our concept models,” said Barnicott.
Creating High Fidelity Concept Cars With 3D Printing
“The progression in technology and 3D printing over the last 10 years is phenomenal. When I first started, producing low volume, niche vehicles, some of the products that we produce today would simply have been inaccessible. And not only am I able to produce these parts today, but I’m also able to produce them very cost-effectively, very quickly,” said Barnicott.
3D printing not only helps the teams to create enhanced products faster, but also to attract new business. They found that many of their customers know they can rely on them to access the latest technologies and they want their components made using the latest cutting edge materials.
“There are certain things that you just can’t class as emerging technologies anymore. 3D printing is one of those things. It’s advanced to a point where everything that we produce is good enough for use in the final presentation stage with all the layers of making that we apply on top of that. 3D printing has gone from almost a novelty to becoming an absolutely inseparable part of what we do,“ said Moradi.
Find more resources for topic:
More content.
How to Choose the Right 3D Printing Material
Dyeing SLS 3D Printed Parts: Benefits and Workflow
Intro to Stereolithography 3D Printing
Dassault Systèmes Completes IQMS ERP Software Acquisition
Jabil Packaging Solutions leveraging DELMIA | Works to stay on top of Plant Floor Operations
SEA-LECT Designs for Manufacturability with DELMIAWorks ERP & SOLIDWORKS
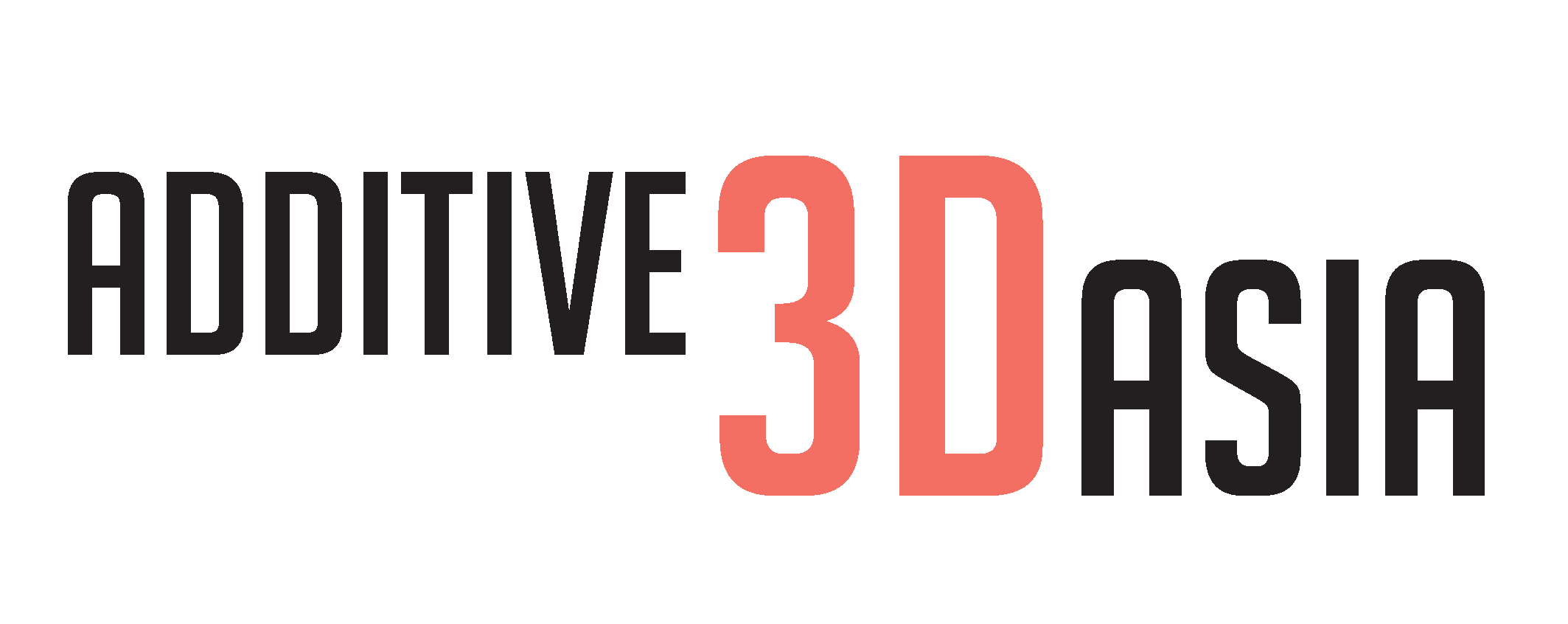
- 3D Printing for Production – HP MJF
- 3D Printing for Industrial – SLA
- 3D Printing for Industrial – FDM
- 3D Printing for Production – SLS
- Metal 3D Printing for Industrial - SLM
- Vacuum Casting
- Laser Cutting & Engraving Services
- Our Gallery
- 3D Printing News
- 3D Printing eBooks
- Case Studies
- Customer Satisfaction Survey
- Instant Order
Case Study: Remodeling an Automotive Spare Part
Providing start-to-end solutions for spare part replacement

3D Modeling of spare part to obtain a 3D file for production of final part
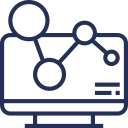
- SLA 3D printing
- SLS 3D printing
- CNC Machining

- Glass-Filled Nylon
- Polyoxymethylene (POM)
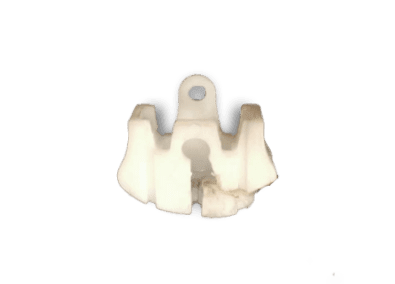
Broken Automotive Spare Part
Our client, Hong Seh Motors , is a luxury car importer and dealer who came to us with a broken spare part from a Tesla car. More specifically, this spare part is situated underneath a Tesla car seat. The challenge was to create an exact replica of the spare part to replace the broken part. As no replacement parts were available in the market, the only other alternative was to replace the entire car seat, which is not a cost effective option.
Therefore, our client decided to engage our services to remodel the spare part they needed. Firstly, our engineers worked on 3D Modeling (CAD as a Service) to create the 3D file in STL format before proceeding to the next step, 3D printing.
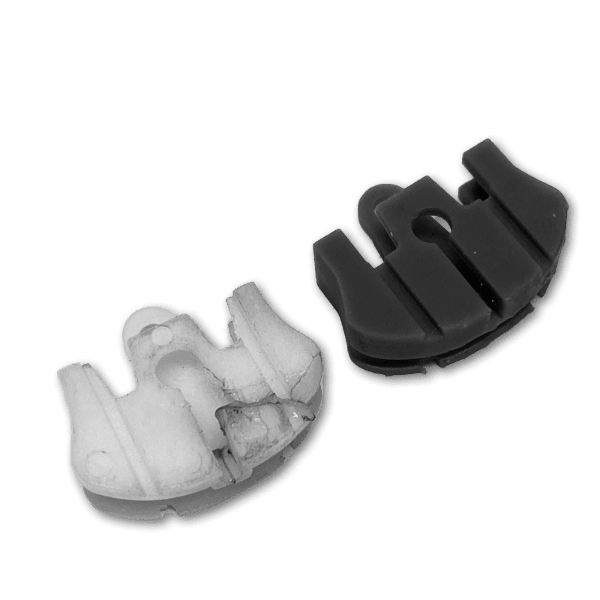
For fitting checks, the prototype part was first 3D printed in standard low cost grey resin using SLA 3D printing . This is to ensure that the 3D modelled spare part is as dimensionally accurate as possible, and check if there needs to be any further changes made to the design of the STL file at an early stage.
After going through the first round of checking, the part was 3D printed in Glass-Filled Nylon using SLS 3D printing . As Glass-Filled Nylon contains glass particles which makes it stronger than standard PA12 Nylon , our client tested if this 3D printed piece could be used as a functional part.
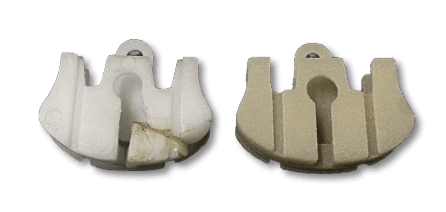
Final Product
After prototyping and testing, our client found that the Glass-Filled Nylon part was not strong enough to withstand the necessary load.
Based on their feedback, we suggested to produce the end part with two different CNC Machining materials for testing, using polyoxymethylene (POM) material and steel. POM is an engineering thermoplastic used in precision parts requiring high stiffness, low friction, and excellent dimensional stability.
With our recommendations and start-to-end services where we helped from 3D Modeling, to prototyping, to manufacturing of the final part, our client successfully reduced costs by more than 75% compared to if they were to replace the seat entirely.
*Produced in steel with CNC machining
Ready to bring your production to the next level?
Click one of our contacts below to chat on WhatsApp
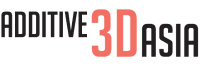
Email us for further assistance at: [email protected]

- Multi Jet Fusion (MJF)
- Design & Engineering
- Quality & Validation
- Post Processing
- Fulfillment
- Polymer Materials
- Metal Materials
- Consumer Products
- Oil & Gas
- E3D Capabilities Document
- In the News
Case Study – Automotive Tooling
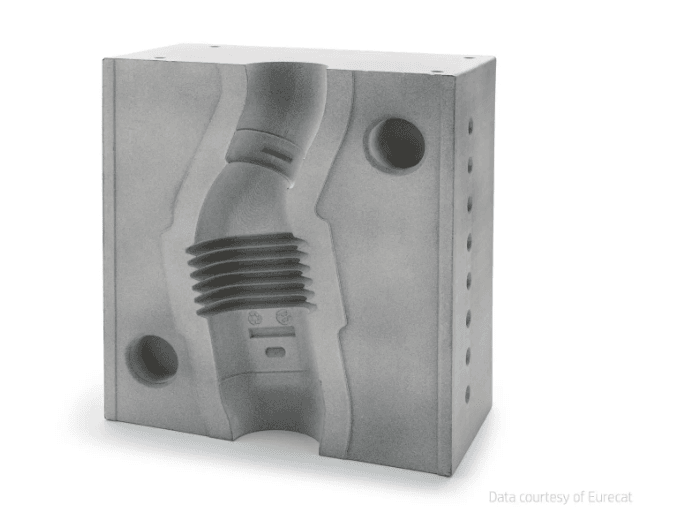
Industry: Automotive
Application: tooling, eurecat uses mjf to produce mold cavities that save time and money.
Problem: Eurecat wanted to improve the way it manufactures mold cavities it uses when extrusion blow molding automotive air ducts
Solution: MJF enabled them to additively manufacture mold cavities
Benefit: MJF enabled simultaneous printing of both cavities. It also reduced the cost by 46% and and reduced lead times from two weeks, to two days.
Read the full case study here .
Learn more about 3D printing automotive molds and tooling here – link to contact us
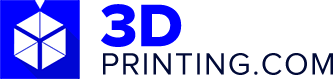
Case Study: Exco Engineering Uses Metal AM For Automotive Die Cast Tooling
November 18, 2019
As we’ve previously reported, the automotive sector is pushing the frontier of metal 3D printing by fabricating prototypes, production jigs and fixtures, and end-use parts for automobiles around the world. Exco Engineering is especially ambitious as they 3D print diecast inserts and have been experimenting with printed water jackets. These components have to withstand incredibly harsh environments so Exco had to blaze this AM trail.
Wes Byleveld is the Director of Additive Manufacturing for Exco Engineering, which is the largest high-pressure diecast tool builder in North America. While they don’t make engines themselves, they make the dies for engine components; they can weigh hundreds of thousands of pounds each. Exco is 3D printing the die inserts that go into the cast molds. Inserts are typically machined from H13 tool steel because they bear the brunt of the casting process, which involves high-pressure molten aluminum being injected into the mold.
Years ago, Byleveld sent water jackets to several metal AM companies to find out if they could be printed. “If you can build this part for us, we’ll buy your machine,” Byleveld said. EOS was the only company that took it on and said, “Yes, we’ll give it a try and we’re going to succeed no matter what it takes.” Exco ended up buying an EOS M 400 in 2015 to develop a path to printed die components.

Forged H13 Versus 3D Printed H13
Material performance was the main obstacle to overcome. 3D printed H13 tool steel doesn’t have the same properties as forged H13 steel as Byleveld explains, “It’s extremely hard to produce additively. When you look at some of the parts printed with H13, they’re cracked and full of porosity. When you’re injecting metal at 13,000 PSI in 20 milliseconds, and you have a waterline 1 mm from the surface, if that water line bursts during metal injection it blows open the machine. It’s a big safety concern for me.”
We’ve printed die inserts from maraging steel that have lasted more than 150,000 cycles. Wes Byleveld, Director of Additive Manufacturing for Exco Engineering
The Solution: 3D Printed Maraging Steel
Instead of trying to develop a new material, they decided to look back. In the 1960s, maraging steel was developed for high-pressure applications like rocket motor casings. So Exco commissioned a few feasibility studies with a local university and landed on a proprietary heat-treating process that imparts 3D printed maraging steel with mechanical properties that meet or exceed those of H13 tool steel. “The material lasts,” he says. “We’ve printed die inserts from maraging steel that have lasted more than 150,000 cycles.”
Achieving a high cycle count is important because a printed insert cost several times more than a machined insert; savings can still be achieved if the longevity is significantly improved. But there are other costs to consider, such as cycle times, which can be reduced with better conformal cooling patterns enabled through AM. Additionally, downtime is drastically reduced with printed inserts as machining is incredibly time consuming. Those individual savings add up to some serious coinage over the lifetime of a mold.
All of those factors also apply to the printed water jackets that Exco is developing. They’re currently working with one of the Big Three automakers to test their printed water jackets. If the tests go well, automakers will have yet another avenue to increase production efficiency with AM.
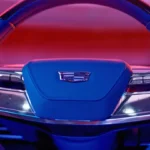
Recap: Automotive Additive Manufacturing in 2022
For further reading you can find the full interview with Wes Byleveld here .
Researchers Enhance Thermo-optical Properties of 3D Printed Building Facades
A recent study from researchers at ETH Zurich, has introduced a novel modeling approach to evaluate the performance of 3D printed facade (3DPF)... read more »
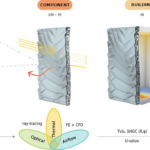
Aerojet Rockets Ahead with Pentagon’s Hypersonic Additive Manufacturing Contract
The US Department of Defense has awarded Aerojet Rocketdyne a $22 million contract to spearhead the development of a hypersonic propulsion prototype. Over... read more »
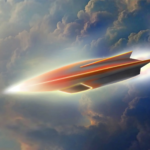
3D Printing Transforms Wind Turbine Tooling
TPI Composites, the University of Maine, and ORNL are embarking on a mission to utilize large-scale 3D printing for wind turbine tooling. The... read more »
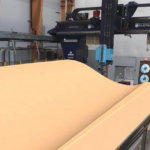
YouTuber Achieves 317 MPH with 3D Printed Quadcopter
Luke Maximo Bell has secured the Guinness World Record for the fastest battery-powered quadcopter, reaching a staggering 317 MPH. The quadcopter's primary structure... read more »
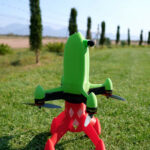
Blurred Light Used for High-Quality Optical 3D Printing
Canadian researchers have introduced a novel 3D printing technique called blurred tomography. The process is capable of swiftly producing microlenses with commercial-grade optical... read more »
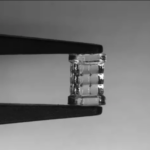
DIY Foldable Y6 Hexacopter Drone with Raspberry Pi Camera Mount
YouTuber Mech Ninja showcases his foldable Y6 Hexacopter. It features a 2-axis gimbal for a Raspberry Pi camera and weighs 1.4kg. Download the files now and start building your own.
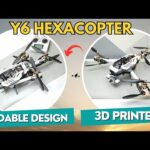
US Air Force Demonstrates Rapid Deployment of 3D Printed Drones
The US Air Force has successfully demonstrated the assembly and deploying of a 3D printed drone within an incredibly short 24-hour window. This... read more »
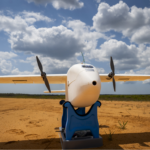
Les Fines Lames Unveils Fancy 3D Printed Cigar Knife Handle
Les Fines Lames has partnered with German Engineered Cigars to introduce the Le Petit Kentron cigar knife, featuring a 3D printed handle which... read more »
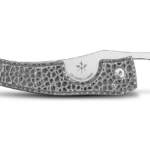
Navy Slashes Cost of F/A-18 Wheel Replacement with 3D Printing
The U.S. Navy is drastically reducing the costs of F/A-18 tyre replacements thanks to additive manufacturing. Normally the cost is around $100,000, and... read more »
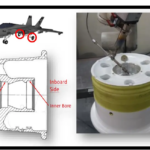
IperionX and Vegas Fastener Manufacturing Collaborate on Titanium Fasteners for US Army
IperionX and Vegas Fastener Manufacturing have joined forces to develop and produce titanium alloy fasteners and precision components. This partnership aims to leverage... read more »
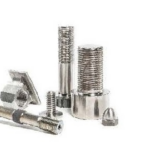
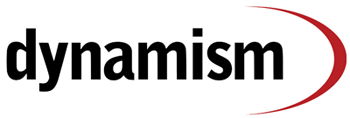
- shopping cart
- 1-800-310-7968
Which Car Brands Use 3D Printing?
- Post author By Dominic Filipponi
- Post date March 25, 2022
From prototypes and parts, to producing best-sellers in the automotive industry, 3D printing has enabled cars to truly evolve for the better. No longer is the 3D printer considered a piece of niche technology, but it has resulted in major success for a litany of car brands.
Which car brands have added value, cut costs, or even expedited their manufacturing processes with 3D printing? Take a look at just some of them below!

As the company that introduced the world to the car and the assembly line, it’s only right that Ford is still at the forefront of pushing the boundaries of technology. For years, Ford has utilized what 3D printing has to offer, especially in their manufacturing process .
Even more exciting, though, is that Ford is embracing change by offering its customers the ability to modify their vehicles post-purchase with 3D printed add-ons. More specifically, Ford’s Maverick Pickup is letting users be creative with the FITS system ; “a series of slots at the rear of the center console and the under-seat storage bins designed to use with accessories.”
Interested in specific Case Studies from our trusted 3D Printer Makers? Take a look at one from Ultimaker, Desktop Metal, and BigRep.
The Toyota Corolla is known for its dependability and reliability. Consequently, the Japanese automotive giants turned to 3D printers to get their cars to market sooner.
Ricoh 3D, a 3D printing industry service provider, enlisted their workshop to print and manufacture prototypes for Toyota.
Why? So they could get a better idea on how parts would print, react to conditions, and overall impact their final product.

What do you get when you mix Germany’s top automotive and automation companies? A perfect marriage of innovation and an increase of production. Both Volkswagen and Siemens have teamed up to implement adhesive in their binder jetting process .
Adoption of this world-class technology is propelling them to move forward and actually make this form of production suitable for many years to come. This is hardly a surprise to those that have taken notice of Volkswagen’s process the past few years.
Why? Many of our 3D maker partners have worked closely with the German giant as of late, specifically Ultimaker in their 2017 Case Study.
When you think of Chevrolet, what do you think of? The Corvette? The Camaro? The Chevy Silverado? Well, we do too. Not just because they are industry staples, but because those models effectively use the power of 3D printing.
The Racing Team at Chevy, employing 3D printing technology , have equipped their race cars , specifically the Corvette C8.R, INDYCAR, Silverado race truck and NASCAR Camaro, with 3D printed parts.
This has successfully allowed themselves to not only support over 80,000 miles of production, but to take home a whole trophy case worth of awards in the process. Suffice it to say, 3D printing has done its job, and then some.

Debuting as a concept car in 2016 and finally hitting the market in 2019, the Kia Telluride was able to first be envisioned through 3D printing. In a 2016 press release, the company announced a new model, and was able to display their concept at the 2016 North American International Auto Show.
Their final model features a “steering wheel, dash, and even door panels” that were produced with 3D printing technology.
This may not seem like that big of a deal to some, but their implementation of cutting-edge technology has proved to be very successful for the Telluride, propelling the model to be a best-seller in the United States .
In an effort to embrace new technologies that advance the market-share of electric vehicles and to help combat climate change, Hyundai has established a key relationship with Nanyang Technological University, Singapore to further delve into the true potential of 3D printing.
They aim to do this by establishing top-notch production facilities dedicated to improving their additive manufacturing and giving customers some truly unique options. With customization in mind, Hyundai believes that they will be able to offer their cars to customers on a more personal level, adding specifically tailored functionality.
Additionally, 3D printing is pushing them to cut their time spent on the design cycle drastically. This enables them to reap the reward of huge cost savings which can be reinvested into the company’s daily operations.

Fiat Chrysler
It’s no secret that companies embracing 3D printers are often looking to improve their manufacturing efforts. Unsurprisingly, that’s exactly what Fiat Chrysler is aiming to do.
The Fraunhofer Research Institution for Additive Manufacturing Technologies’ (IAPT) research team along with engineers from Fiat Chrysler teamed up to embrace innovation through 3D printing, creating “a 3D printed suspension part for one of its sports cars.”
Even more exciting is that the Italian-American corporation features high-powdered and prestigious brands like Maserati, Lancia, and Alfa Romeo. We’re certainly excited to see where the brand evolves with their increasingly robust use of 3D printing.
We don’t know about you, but when we think of a luxurious, modern, and sleek car that’s just begging to be driven, we think of the BMW i8 Roadster . BMW, a leading pioneer in the automotive industry, has constantly been at the forefront of car production.
For over 28 years, the company has been researching and perfecting the use of additive manufacturing. This has not only enabled them to make better looking vehicles, but they have had exceptional measurable results which have produced parts that are lighter and sturdier.
As time progresses, we anticipate BMW to continue leading the way on utilizing 3D printing in the automotive industry, whether it’s in their most premiere models, or along the assembly line.

When Audi needed a quick solution to replacing and implementing parts in the assembly process, they looked to their team of engineers, who, in turn, looked to their collection of 3D printers.
The printers in their Audi R8 factory in the Böllinger Höfe allow them to custom build parts on a case-by-case basis, and give their engineers immediate feedback on how they will fit and work in their vehicles.
Using CAD technology , they were able to print crucial parts that place key sensors in their vehicles. This has made their production process incredibly seamless and helps to build faster and better.
Aston Martin
When you stumble upon a bump in the road, you better have some confidence in your suspension. In order to increase their performance, British Luxury Sports Car Icon Aston Martin turned to the team at Domin to embrace 3D printing “for the development of a “world-leading” suspension system.”
Aston Martin’s end goal is to achieve implementation of their 3D printed suspension system in their final products through rigorous testing and prototyping in the production process.
From the outside looking in, we have the utmost confidence that the car brand will have success in this venture, considering this is far from the first time they have deployed additive manufacturing.

Lamborghini
When the Italian supercar brand takes on a new technology to produce some of the most stunning vehicles the world has to offer, you should take notice. Their Sián Coupé and Roadster feature modern design through the capabilities of 3D printing, namely in their air ventilation system.
Although they are using the technology in relatively small capacities, we anticipate that they, and other luxury brands, will continue to adopt it in the future. Why? Because additive manufacturing is continually growing and proving its worth among others.
What works for me?
In our experience, all of our customers all come from unique backgrounds. Some printers don’t offer the capabilities that fit your needs quite like you need them to. Do you have any questions about our selection of products, potential savings opportunities, or anything in between? Fill out the contact form below and we will be in touch shortly!

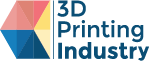
- Case Studies
- Kickstarter, etc
- Art & Sculpture
- Post Processing
- 3DP Applications
- 3D Platforms
- Uncategorized
- On demand manufacturing
- 3D Printing
- Market Insights
- Entertainment
- Open source
- Executive Interview Series
- 3D Printing News Digest
- Stock Market
- Medical & Dental
- 3D Software
- Legal and Regulatory
- Crowd Funding
- 3D Scanners
- 3D Printers
- Consumer Products
- Construction
- Electronics
- Applications
- Laser Cutters
Mantle 3D printers reduce tooling lead times by 50%, new customers announced
US-based metal 3D printer manufacturer Mantle has expanded the reach of its 3D printing technology, including the P-200 metal 3D printer, with three new customers. These new customers include Spectru…
Velo3D technology cuts lead-time of Upwing Energy’s gas-compressor module
US-based natural gas service provider Upwing Energy has leveraged technology from metal 3D printer manufacturer Velo3D to 3D print its Subsurface Compressor System (SCS) compressor module. By using Ve…
Evolve Additive Solutions launches program for 3D printing at high volume
Evolve Additive Solutions, a Minnesota-based 3D printer manufacturer, has launched a Production Assessment Program. “This is an exciting time in the growth of Evolve,” said Joe Allison, CE…
HP’s digital manufacturing offering ‘opening new markets’ to 3D printing service providers
Multinational printing firm HP has published a series of use cases that reflect how its 3D printers for manufacturing are increasingly ‘opening new markets’ to service bureaus. For those making …
3D printed marine parts validated after successful tests on-board Endeavour oil tanker
3D printing service provider 3D Metalforge has successfully tested three different 3D printed parts on board ConocoPhillips Polar Tankers’ Endeavour oil tanker. As part of a pioneering project, 3D Met…
Enel’s Geyser project deploys 3D printing for geothermal plant replacement parts
Subscribe to our YouTube channel for the latest 3D printing video shorts, reviews and webinar replays. Italian renewable energy company Enel Green Power has developed replacement technical c…
Customized production in the packaging industry with Stratasys 3D printing
Marchesini Group S.p.A., an Italian manufacturer of automated packaging machinery, has adopted an entirely customized production business model using Stratasys 3D printing technology. Located within …
3D printing used to protect bus drivers at Seattle Children’s Hospital
Californian rapid prototyping service provider GoProto and design and engineering specialist Function Foundry, have collaborated to help protect high-risk bus drivers at Seattle Children’s Hospital us…
Additive Manufacturer Green Trade Association commissions first research project
Global trade group Additive Manufacturer Green Trade Association (AMGTA) has announced a systematic review into the environmental sustainability of metal 3D printing. The organization’s first literary…
HİDROMEK reduces costs of machinery end-use parts with LOOP PRO 3D Printer
HİDROMEK, a manufacturer of construction machinery based in Turkey, is using the LOOP PRO 3D printer to produce end-use parts for its agricultural vehicles. Seeking to reduce its downtimes and avoid …
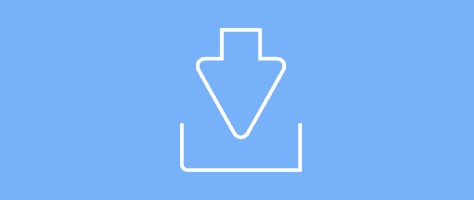
3D Printing Solutions 3D Printing Solutions
- 3D Printing Solutions
- Consumer goods and electronics
- Healthcare and medical
- Manufacturing services
- Molded Fiber
- Orthotics and prosthetics
- Transportation and automotive
- Multi Jet Fusion technology
- Jet Fusion 5600 Series
- Jet Fusion 5400 Series
- Jet Fusion 5200 Series
- Jet Fusion 5000
- Jet Fusion 4200
- Metal Jet S100
- All 3D Printers
- 3D Solution Services
- 3D Professional Services
- 3D as a Service
- Financial Services
- MJF parts production
- Metal Jet parts production
- 3D Print Learning Center
- Case studies & resources
- Events & Webinars
- MJF Handbook
FIND PARTS SUPPLIER
Contact an HP 3D Print expert
Choose the phone number for your country to speak to a local HP 3D Printing sales expert today.
België/Belgique
+32 78 48 44 69
Czech Republic
+420 239 050 531
- Deutschland
+49 7031 9869013
+34 93 003 45 95
+33 (0)675 196 196
+39 02 8295 2406
+31 20 241 5685
+47 23 96 00 13
+43 1424 0091
+48 71 881 14 09
+40 376 300 174
+46 8 446 891 49
Suisse/Switzerland
+41 44 511 2333
- United Kingdom
+44 20 7365 8158
- United States
+1 877 468 8369
3D PRINTING IN SUPPORT OF COVID-19 CONTAINMENT EFFORTS. LEARN
Case studies and resources
APPLICATION TYPE
SPECIALIZATION
RESOURCE TYPE
CASE STUDY | GOPROTO
GoProto ventures into new markets with HP 3D HR TPA enabled by Evonik
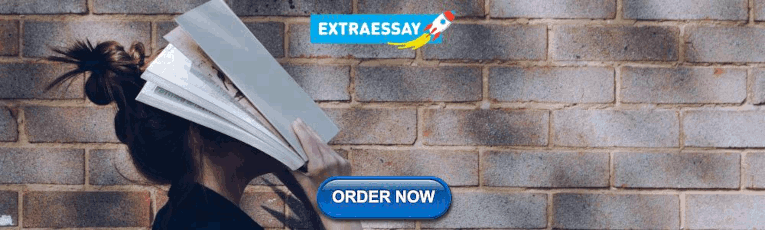
CASE STUDY | PRENSILIA & ELASTICO DISEGNO
Bringing functionality and aesthetics to robotic prosthetics
CASE STUDY | GOPROTO & ROPES EDGE
Producing high-quality parts and streamlining manufacturing
CASE STUDY | UBI MAIOR
Lightweight, customized parts with complex geometries for boats and yachts
CASE STUDY | HEYGEARS
More comfortable, more versatile orthotics
CASE STUDY | DUNDON MOTORSPORTS
Fast-tracking production of auto racing parts
CASE STUDY | CHABLOZ ORTHOPÉDIE
Leveraging HP 3D Printing to improve treatment of cranial deformities
CASE STUDY | ORTHO-TEAM
HP 3D Printing as an innovation partner for future growth
CASE STUDY | AERECO
Eliminating outsourcing by adopting HP Multi Jet Fusion technology
Optimizing entire 3D printing process
CASE STUDY | HP
Achieving industrial-level OEE numbers
HP 3D Printing supports APCC’s high-volume production of packaging
CASE STUDY | VAN RAAM
Achieving efficient short-run production of bicycle parts
CASE STUDY | CUPRA
HP 3D Printing helps CUPRA launch Léon Competición racecar
CASE STUDY | ACTIVARMOR
ActivArmor fashions customized orthotic devices
CASE STUDY | EXTOL
Extol leverages polypropylene and HP MJF to help customers decrease time to market
CASE STUDY | MATERIALISE & AVULAR
Customized, on-demand parts for drones
WHITE PAPER
How 3D printing can optimize insole production
CASE STUDY | WEERG
Pushing the limits with HP 3D Printing
How many parts and which machine makes sense?
How can additive manufacturing improve product development?
HP Multi Jet Fusion technology: From metals to plastic
How can additive manufacturing complement injection molding?
Advanced topics in design for automotive additive manufacturing
Design and process optimization
Transforming digital design and manufacturing
Tooling jigs and fixtures for automotive product development
10 design tips you need to know
CASE STUDY | TRIPLE EIGHT RACE ENGINEERING
Accelerating production while decreasing costs
CASE STUDY | SMILE DIRECT CLUB
Delivering straighter smiles to millions
CASE STUDY | SKORPION ENGINEERING
Redesigning and customizing motorbike parts
CASE STUDY | SINTHESI ENGINEERING
Design freedom and short-run production capabilities
CASE STUDY | MEIDAI
Faster production and opportunities for customization
How 3D printing can improve a 3D printer
CASE STUDY | HORIZONS OPTICAL
End-to-end solution for customized eyewear
CASE STUDY | HAVATEC
Improving and accelerating production
CASE STUDY | GLAZE PROSTHETICS
Quickly producing prosthetics tailored to individual needs
CASE STUDY | EVEREX
Less-expensive medical devices at faster speeds
CASE STUDY | BREEZM
Ramping up production of custom-designed eyewear
CASE STUDY | BIOTECH DENTAL
Reducing the costs of implant molds
CASE STUDY | FAST RADIUS
Reaching a new level of innovation
Transforming prosthetics and orthotics
The guide to design optimization
CASE STUDY | VOLKSWAGEN
Mass customization and manufacturing acceleration
CASE STUDY | PARMATECH
Disrupting metal parts production
CASE STUDY | OT4
Producing complex designs to improve patients’ lives
Designing orthoses for patients' needs
Improving patients' lives with flexible orthoses
CASE STUDY | NIVELLMEDICAL
Reinventing dental aligner production
CASE STUDY | MOTORSPIRIT
Design freedom to achieve more and perform better
CASE STUDY | LANGHORNE CARPET
Applying 21st-century technology to 20th-century devices
Transforming the spare parts supply chain
CASE STUDY | GKN
Reaching production at scale
CASE STUDY | DUSTRAM
Lowering costs, accelerating production, and building strong parts
CASE STUDY | CRISPIN
Making cosmetic, lightweight, and affordable orthotics
CASE STUDY | BIOTEC
Electromedical parts faster, better, and more affordably
CASE STUDY | PROSFIT
HP Multi Jet Fusion helps reinvent the prosthetics industry
CASE STUDY | MECHATRONIC
Building better parts at a lower cost
CASE STUDY | INVENT MEDICAL
Improved medical outcomes with HP Multi Jet Fusion
CASE STUDY | HULOTECH
Customizing prosthetic parts with HP Multi Jet Fusion
CASE STUDY | FDM DIGITAL SOLUTIONS
Helping enhance performance in the aerospace industry
CASE STUDY | EURECAT EBM
HP Multi Jet Fusion helps automotive industry save costs
CASE STUDY | DI LABS
HP Multi Jet Fusion improves pipe-cutting process in manufacturing
CASE STUDY | CNC-AUTOMATION WÜRFEL
HP Multi Jet Fusion leads to faster, more agile production
HP Multi Jet Fusion saves time and costs when producing tooling applications.
CASE STUDY | BOWMAN
HP Multi Jet Fusion helps produce better-performing bearing cages
Design optimization and easier assembly from HP Multi Jet Fusion
HP leverages its own technology to create final parts
CASE STUDY | ARCESSO DYNAMICS
Reducing costs and time in molds production
CASE STUDY | AEROSPORT
3D printing rudder trim system helps reduce number of parts
Creating jigs and fixtures, prototypes, and final parts with HP MJF
CASE STUDY | OPTIMUS 3D
Better orthotics customized to patients
CASE STUDY | MOTOR l'ESCALA
Custom 3D printed car parts for motorsports team
HP MJF technology helps facilitate assembly in HP build units
Improving air flow performance
Simplifying parts assembly
Enhancing performance of air manifolds
Improving manufacturing of fixtures
CASE STUDY | HELI RACING
Simplifying production of race car manifolds
CASE STUDY | ED LIGHTING
Easier manufacturing and custom-designed furniture
CASE STUDY | CAF
HP Multi Jet Fusion helps strengthen train door structures
CASE STUDY | BAREL
HP Multi Jet Fusion leads to lightweight part production
Faster manufacturing process
CASE STUDY | AUREA AVIONICS
Accelerating production for the intelligence industry
CASE STUDY | ADDIT-ION
Creating customizable furniture parts
CASE STUDY | SIGMADESIGN
Improving overall design and reducing costs
CASE STUDY | SHAPEWAYS
Growing the business with consumer applications
CASE STUDY | MATERIALISE
Moving from prototyping to end-part production
CASE STUDY | LOOKREAL
Taking personalization to a new level
CASE STUDY | KUPOL PROJECT
Reinventing sport headgear
CASE STUDY | JABIL
Staying competitive by speeding time to market
CASE STUDY | iORTHOTICS
iOrthotics finds a better way to match patients' feet, more quickly
CASE STUDY | IAM 3D HUB
Excellent air tightness
Enabling design versatility and part optimization
Multiple advantages of using our own technology
Reducing time and cost
Time and cost savings
Making it easier to meet clients' needs
CASE STUDY | GIMATIC
More competitive in the fast-paced robotics industry
CASE STUDY | FORECAST 3D
Moving from short-run production to high-volume runs
CASE STUDY | FICEP S3
Accelerating production and improving productivity
CASE STUDY | BIESSE
Enabling more design freedom and faster time to market
How HP Multi Jet Fusion can complement CNC machining
Producing manufacturing aids
3D applications for manufacturers of machinery and production line equipment
Streamlining machinery and production lines
How to complement CNC production
Creating functional parts faster
CASE STUDY | CONDUCTIX WAMPFLER
Conductix improves time to market and simplifies product design with HP MJF
CASE STUDY | L´OREAL
L´Oreal quickly responds to shifts in its manufacturing processes with HP MJF
CASE STUDY | YASOJIMA PROCEED
Yasojima Proceed produces battery and substrate cases for neurosurgery with HP MJF
Extol quickly delivers low-cost, lighter weight robotic tooling thanks to HP MJF
CASE STUDY | KOCH-PAC SYSTEME
Producing cost-efficient, customized and sustainable packaging machinery parts
Discover how HP Metal Jet technology works and all the details behind the process
Discover how HP Multi Jet Fusion technology works and all the details behind the process
3D printing with polypropylene - From prototypes to production parts
CASE STUDY | COBRA
Cobra turns to HP Metal Jet to create and adapt designs quicker and innovate faster
CASE STUDY | SCHNEIDER
Schneider Electric improves efficiency by mass producing 3D printed metal parts at scale
CASE STUDY | BRINTER®
HP MJF helps Brinter launch its innovative bioprinting solutions faster and more affordably
CASE STUDY | UNLIMITED TOMORROW
Through collaboration, Unlimited Tomorrow makes high-tech prosthetics more accessible
CASE STUDY | HOFFMANN
Hoffmann + Krippner revolutionizes production of small series for plastic enclosures
CASE STUDY | CGX
CGX achieves a leaner supply chain and the ability to adapt to market demand with HP MJF
CASE STUDY | OPTIMA
HP 3D printing helps startup cost-effectively design and produce new medical device
CASE STUDY | FORERUNNER
Forerunner 3D develops innovative medical device for oxygen therapy patients
CASE STUDY | AMUFACTURE
HP MJF allows AMufacture to design and 3D print a light, watertight, complex manifold
CASE STUDY | UNION BINDING
Union Binding company make their ideas a reality with HP MJF technology
CASE STUDY | THINKTEC 3D
thinkTEC 3D uses HP 3D Printing for end-of-arm tooling designs
CASE STUDY | WAITKUS360ª
Waitkus360° adopts MJF technology to match high levels of flexibility with productivity
CASE STUDY | BMW Group
BMW Group relies on HP MJF for 3D printed keycaps
Competitive accelerated weathering study between HP 3D HR PA 12 W and SLS materials
Sterilization study of HP 3D High Reusability PA 12 W
CASE STUDY | MIGHTY OAK
Spinal surgery outcomes improve with new 3D printed models and tools
CASE STUDY | JOHNSON SCREENS
Johnson Screens increases cost efficiency through innovative 3D printing
CASE STUDY | JOHN DEERE
HP Metal Jet technology powers John Deere tractors
The potential of Metal Additive Manufacturing
CASE STUDY | SCULPTEO
Sculpteo streamlines 3D printing processes with HP 3D Automatic Unpacking Station
CASE STUDY | 3Faktur
3Faktur automates post-processing workflow with HP 3D Automatic Unpacking Station
Is an additively manufactured socket comparable to a conventionally manufactured carbon fiber one?
CASE STUDY | VECROS
HP 3D Printing fosters flexible drone design that enhances aesthetics and ensures optimal functionality
CASE STUDY | WIMBA
Wimba improves pet mobility with HP 3D printed orthotics
CASE STUDY | ZELTA3D
Zelta3D turns to HP MJF to meet customer needs with greater speed, quality, and accuracy
CASE STUDY | EDSER
EDSER ramps up production of customized orthotic devices
CASE STUDY | CAMPETELLA ROBOTIC CENTER
HP Multi Jet Fusion helps Campetella Robotic Center reduce cost and lead time
CASE STUDY | IFC
IFC advances material handling with HP´s 3D Printing technology
CASE STUDY | Kitfox Aircraft
New gap seals that improve the aerodynamics and aesthetics of its aircraft thanks to HP MJF
CASE STUDY | Sodecia
Increasing efficiency, reducing costs, and improving sustainability in robotic gripper design and production.
Select Your Country/Region and Language
- América Central
- Canada - Français
- Puerto Rico
- Asia Pacific
- Hong Kong SAR
- New Zealand
- Philippines
- 中國香港 - 繁體中文
- Česká republika
- Magyarország
- Middle East
- Saudi Arabia
- South Africa
- Switzerland
- الشرق الأوسط
- المملكة العربية السعودية
HP Worldwide
- Investor relations
- Sustainable impact
- Diversity, Equity and Inclusion
- Press center
- HP Store Newsletter
- HP Printables Newsletter
- Ways to buy
- Shop online
- Call an HP rep
- Find a reseller
- Enterprise store
- Public sector purchasing
- Download drivers
- Support & troubleshooting
- Register your product
- Authorized service providers
- Check repair status
- Fraud alert
- Security Center
- HP Partners
- HP Amplify Partner Program
- HP Partner Portal
- Stay connected
- Product recycling |
- Accessibility |
- CA Supply Chains Act |
- Use of cookies |
- Your privacy choices |
- Terms of use |
- Limited warranty statement |
- Terms & conditions of sales & service |
©2024 HP Development Company, L.P. The information contained herein is subject to change without notice.
Your browser does not support iframes.
Investigating the reversible performance of shape memory composites in 4D printing using magnetic field stimulation: case study of polylactic acid/SrFe 12 O 19 composite filament
- Full Research Article
- Published: 05 May 2024
Cite this article
- Seyed Mohammad Reza Sotoudeh 1 ,
- Milad Sadegh Yazdi 1 ,
- Mohammad Hadi Hosseinzadeh 1 &
- Mohammad Hassanpour 1
29 Accesses
Explore all metrics
4D printing is an advanced manufacturing technology in which the 3D printed structure evolves over time, and this evolution can be a change in appearance, change in material properties, or change in color. The controllability and reversibility of the 4D printing process have received little research attention. In this research, a combination of polylactic acid and microparticles of strontium ferrite (SrFe 12 O 19 ) was used to create a composite filament. After printing and bending shape recovery, the reversibility of the printed parts was tested by N42 grade neodymium magnet and the reversibility of the parts was successfully done. The controllability of the shape recovery process was demonstrated through an experimental test using the obtained model. The difference of 3.65% between the experimental sample shape recovery and the amount of shape recovery obtained from the software shows the high accuracy of the presented model.
This is a preview of subscription content, log in via an institution to check access.
Access this article
Price includes VAT (Russian Federation)
Instant access to the full article PDF.
Rent this article via DeepDyve
Institutional subscriptions
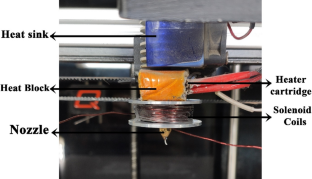
Similar content being viewed by others
Advances in 4D Printing of Shape-Memory Materials: Current Status and Developments
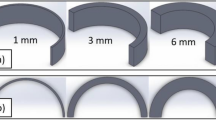
Enhancing shape-recovery ratio of 4D printed polylactic acid (PLA) structures through processing parameter optimization
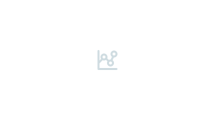
Mechanical properties and shape memory behavior of 4D printed functionally graded cellular structures
Shahrubudin N, Lee TC, Ramlan R (2019) An overview on 3D printing technology: technological. Mater Appl Procedia Manuf 35:1286–1296. https://doi.org/10.1016/j.promfg.2019.06.089
Article Google Scholar
Ngo TD, Kashani A, Imbalzano G, Nguyen KTQ, Hui D (2018) Additive manufacturing (3D printing): a review of materials, methods, applications and challenges. Compos B Eng 143:172–196. https://doi.org/10.1016/j.compositesb.2018.02.012
Tetsuka H, Shin SR (2020) Materials and technical innovations in 3D printing in biomedical applications. J Mater Chem B 8(15):2930–2950. https://doi.org/10.1039/D0TB00034E
Andrzejewski J, Markowski M, Barczewski M (2022) The use of nanoscale montmorillonite (MMT) as reinforcement for polylactide acid (PLA) prepared by fused deposition modeling (FDM)—comparative study with biocarbon and talc fillers. Materials 15(15):5205. https://doi.org/10.3390/ma15155205
Savastano M, Amendola C, D’ Ascenzo F, Massaroni E (2016) 3-D printing in the spare parts supply chain: an explorative study in the automotive industry, lecture notes in information systems and organization. Springer International Publishing, Cham, pp 153–170. https://doi.org/10.1007/978-3-319-40265-9_11
Book Google Scholar
Berrio Bernal JD, Silva ECN, Montealeg Rerubio W (2019) Characterization of effective Young’s modulus for Fused Deposition Modeling manufactured topology optimization designs. Int J Adv Manuf Technol 103(5–8):2879–2892. https://doi.org/10.1007/s00170-019-03747-6
Gul JZ, Sajid M, Rehman MM, Siddiqui GU, Shah I, Kim K-H, Lee J-W, Choi KH (2018) 3D printing for soft robotics—a review. Sci Technol Adv Mater 19(1):243–262. https://doi.org/10.1080/14686996.2018.1431862
Park MJ, Bae J, Ju YK (2022) Structural behavior of a composite curtain wall fabricated by the fused deposition modeling 3D printing method. Polymers 14(7):1431. https://doi.org/10.3390/polym14071431
Andrzejewski J, Gronikowski M, Aniśko J (2022) A novel manufacturing concept of LCP fiber-reinforced GPET-based sandwich structures with an FDM 3D-printed core. Materials 15(15):5405. https://doi.org/10.3390/ma15155405
Tibbits S (2013) The emergence of 4D printing, “TED Talk”. Available online: https://www.ted.com/talks/skylar_tibbits_the_emergence_of_4d_printing . Accessed Feb 2013
Yang C, Wang B, Li D, Tian X (2017) Modelling and characterisation for the responsive performance of CF/PLA and CF/PEEK smart materials fabricated by 4D printing. Virtual Phys Prototyp 12(1):69–76. https://doi.org/10.1080/17452759.2016.1265992
Baker AB, Bates SRG, Llewellyn-Jones TM, Valori LPB, Dicker MPM, Trask RS (2019) 4D printing with robust thermoplastic polyurethane hydrogel-elastomer trilayers. Mater Des 163:107544. https://doi.org/10.1016/j.matdes.2018.107544
Momeni F, Mehdihassani SM, Liu X, Ni J (2017) A review of 4D printing. Mater Des 122:42–79. https://doi.org/10.1016/j.matdes.2017.02.068
Tibbits S (2014) 4D printing: multi-material shape change. Archit Des 84(1):116–121. https://doi.org/10.1002/ad.1710
Zhou Y, Huang WM, Kang SF, Wu XL, Lu HB, Fu J, Cui H (2015) From 3D to 4D printing: approaches and typical applications. J Mech Sci Technol 29(10):4281–4288. https://doi.org/10.1007/s12206-015-0925-0
Leist SK, Gao D, Chiou R, Zhou J (2017) Investigating the shape memory properties of 4D printed polylactic acid (PLA) and the concept of 4D printing onto nylon fabrics for the creation of smart textiles. Virtual Phys Prototyp 12(4):290–300. https://doi.org/10.1080/17452759.2017.1341815
Zhang F, Wang L, Zheng Z, Liu Y, Leng J (2019) Magnetic programming of 4D printed shape memory composite structures. Compos Part A Appl Sci Manuf 125:105571. https://doi.org/10.1016/j.compositesa.2019.105571
Hosseinzadeh M, Ghoreishi M, Narooei K (2023) 4D printing of shape memory polylactic acid beams: an experimental investigation into FDM additive manufacturing process parameters, mathematical modeling, and optimization. J Manuf Process 85:774–782. https://doi.org/10.1016/j.jmapro.2022.12.006
Bodaghi M, Damanpack AR, Liao WH (2018) Triple shape memory polymers by 4D printing. Smart Mater Struct 27(6):065010. https://doi.org/10.1088/1361-665X/aabc2a
Ke D, Chen Z, Momo ZY, Jiani W, Xuan C, Xiaojie Y, Xueliang X (2020) Recent advances of two-way shape memory polymers and four-dimensional printing under stress-free conditions. Smart Mater Struct 29(2):023001. https://doi.org/10.1088/1361-665X/ab5e6d
Wang Y, Li X (2021) 4D-printed bi-material composite laminate for manufacturing reversible shape-change structures. Compos B Eng 219:108918. https://doi.org/10.1016/j.compositesb.2021.108918
Yuan C, Roach DJ, Dunn CK, Mu Q, Kuang X, Yakacki CM, Wang TJ, Yu K, Qi HJ (2017) 3D printed reversible shape changing soft actuators assisted by liquid crystal elastomers. Soft Mater 13(33):5558–5568. https://doi.org/10.1039/C7SM00759K
Zhao W, Huang Z, Liu L, Wang W, Leng J, Liu Y (2021) Porous bone tissue scaffold concept based on shape memory PLA/Fe 3 O 4 . Compos Sci Technol 203:108563. https://doi.org/10.1016/j.compscitech.2020.108563
Moradi M, Dezaki ML, Kheyri E, Rasouli SA, Attar MA, Bodaghi M (2023) Simultaneous FDM 4D printing and magnetizing of iron-filled polylactic acid polymers. J Magn Magn Mater 568:170425. https://doi.org/10.1016/j.jmmm.2023.170425
Lalegani Dezaki M, Bodaghi M (2023) Sustainable 4D printing of magneto-electroactive shape memory polymer composites. Int J Adv Manuf Technol 126(1):35–48. https://doi.org/10.1007/s00170-023-11101-0
Ahmad MN, Ishak MR, Mohammad Taha M, Mustapha F, Leman Z, Anak Lukista DD, Irianto IG (2022) Application of taguchi method to optimize the parameter of fused deposition modeling (FDM) using oil palm fiber reinforced thermoplastic composites. Polymers 14(11):2140. https://doi.org/10.3390/polym14112140
Montgomery DC (2017) Design and analysis of experiments. John Wiley & Sons, New York
Google Scholar
Box GEP, Hunter JS (1957) Multi-factor experimental designs for exploring response surfaces. Ann Math Stat 28(1):195–241
Article MathSciNet Google Scholar
Razavi FS, Ghanbari D, Salavati-Niasari M (2022) Green synthesis of SrFe12O19@Ag and SrFe12O19@Au as magnetic plasmonic nanocomposites with high photocatalytic performance for degradation of organic pollutants. Chemosphere 291:132741. https://doi.org/10.1016/j.chemosphere.2021.132741
T. Sembiring, Y.B. Zebua, M. Muljadi, Analysis of crystal structure and magnetic character strontium ferrite (SrFe12O19) powder made of stoichiometry and non-stoichiometry compositions. In: AIP Conf Proc ., AIP Publishing, 2020. https://doi.org/10.1063/5.0005232
Turi E (2012) Thermal characterization of polymeric materials. Elsevier, Amsterdam, the Netherlands
Roudbarian N, Baniasadi M, Ansari M, Baghani M (2019) An experimental investigation on structural design of shape memory polymers. Smart Mater Struct 28(9):095017. https://doi.org/10.1088/1361-665X/ab3246
Sehhat MH, Mahdianikhotbesara A, Yadegari F (2022) Impact of temperature and material variation on mechanical properties of parts fabricated with fused deposition modeling (FDM) additive manufacturing. Int J Adv Manuf Technol 120(7–8):4791–4801. https://doi.org/10.1007/s00170-022-09043-0
van Manen T, Janbaz S, Zadpoor AA (2017) Programming 2D/3D shape-shifting with hobbyist 3D printers. Mater Horiz 4(6):1064–1069. https://doi.org/10.1039/C7MH00269F
Bodaghi M, Noroozi R, Zolfagharian A, Fotouhi M, Norouzi S (2019) 4D printing self-morphing structures. Materials 12(8):1353. https://doi.org/10.3390/ma12081353
Download references
Author information
Authors and affiliations.
Department of Mechanical Engineering, Faculty of Engineering, Imam Hossein Comprehensive University, Tehran, Iran
Seyed Mohammad Reza Sotoudeh, Milad Sadegh Yazdi, Mohammad Hadi Hosseinzadeh & Mohammad Hassanpour
You can also search for this author in PubMed Google Scholar
Corresponding author
Correspondence to Milad Sadegh Yazdi .
Additional information
Publisher's note.
Springer Nature remains neutral with regard to jurisdictional claims in published maps and institutional affiliations.
Supplementary Information
Below is the link to the electronic supplementary material.
Supplementary file1 (DOCX 393 KB)
Rights and permissions.
Springer Nature or its licensor (e.g. a society or other partner) holds exclusive rights to this article under a publishing agreement with the author(s) or other rightsholder(s); author self-archiving of the accepted manuscript version of this article is solely governed by the terms of such publishing agreement and applicable law.
Reprints and permissions
About this article
Sotoudeh, S.M.R., Yazdi, M.S., Hosseinzadeh, M.H. et al. Investigating the reversible performance of shape memory composites in 4D printing using magnetic field stimulation: case study of polylactic acid/SrFe 12 O 19 composite filament. Prog Addit Manuf (2024). https://doi.org/10.1007/s40964-024-00625-w
Download citation
Received : 14 January 2024
Accepted : 10 April 2024
Published : 05 May 2024
DOI : https://doi.org/10.1007/s40964-024-00625-w
Share this article
Anyone you share the following link with will be able to read this content:
Sorry, a shareable link is not currently available for this article.
Provided by the Springer Nature SharedIt content-sharing initiative
- Additive manufacturing
- 4D Printing
- Polylactic acid
- Shape memory polymers
- SrFe 12 O 19
- Find a journal
- Publish with us
- Track your research
Rapid Prototype with SLA (Stereolithography) 3D Printing
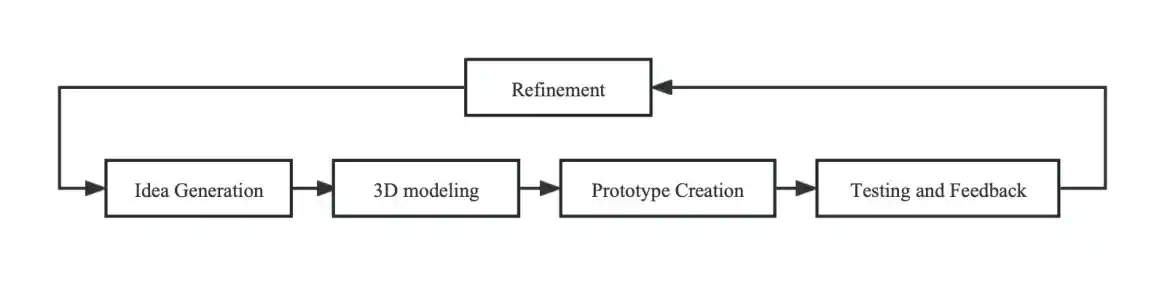
Introduction
What is sla rapid prototyping, the advantages of sla rapid prototyping vs traditional prototyping methods, key principles of sla rapid prototyping, sla rapid prototyping applications, sla rapid prototyping in various industries, sla rapid prototyping: challenges and limitations, the future of sla rapid prototyping, embrace sla rapid prototyping with unionfab.
An overview of how 3D printing enables SLA rapid prototype for fast, high-quality product design and development. Discusses key benefits, materials, processes, and applications.
Rapid Prototyping, often abbreviated as RP, refers to a group of additive manufacturing technologies that can quickly produce physical prototypes.
Rapid prototyping enables fast iterative design, allowing multiple concepts and fits to be tested faster and more cost effectively than traditional techniques.
Key Principles of Rapid Prototyping
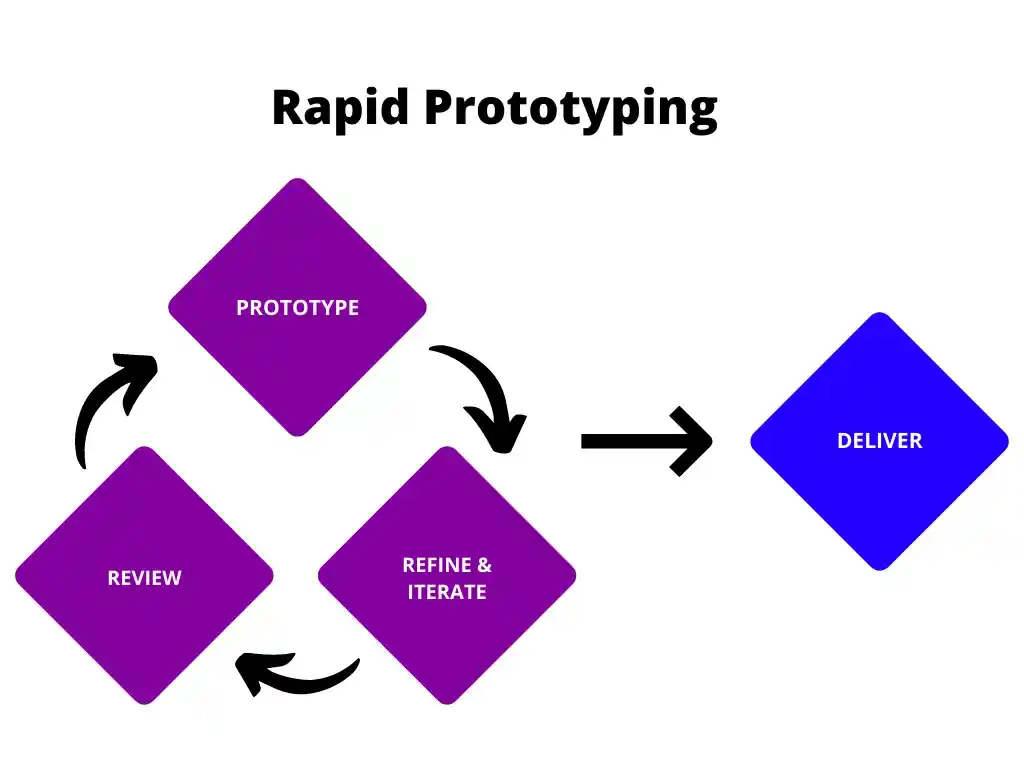
- User-Centered Design : Rapid prototyping enables designers to quickly create prototypes to gather user feedback for iterative improvement.
- Iterative Development : Rapid Prototyping thrives on iteration and refinement.
- Fail Fast, Learn Faster : Rapid Prototyping encourages a fearless attitude towards failure — a valuable source of learning.
Why Rapid Prototyping Matters
- Speeding Up Development : Quicker design feedback and iteration accelerates overall product development and time to market (TTM).
- Reducing Costs and Risks : Testing concepts early with prototypes minimizes costly late stage design changes.
- Enhancing Collaboration and Communication : Physical prototypes provide better understanding compared to concepts alone.
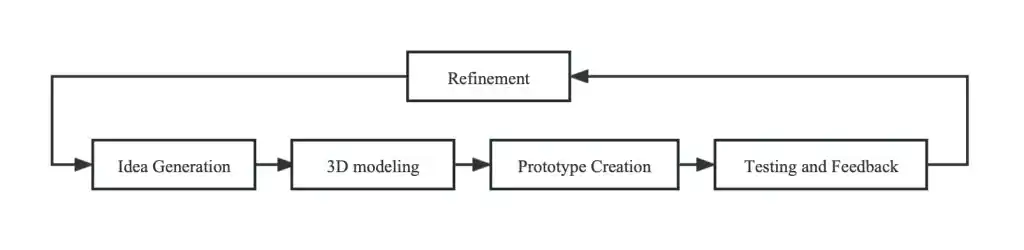
SLA Rapid Prototyping is a technique that utilizes Stereolithography, a 3D printing technology, to create highly detailed and precise prototypes. It involves curing layers of liquid photopolymer resin with ultraviolet (UV) light to build a three-dimensional object layer by layer.
Historical Evolution of SLA Technology
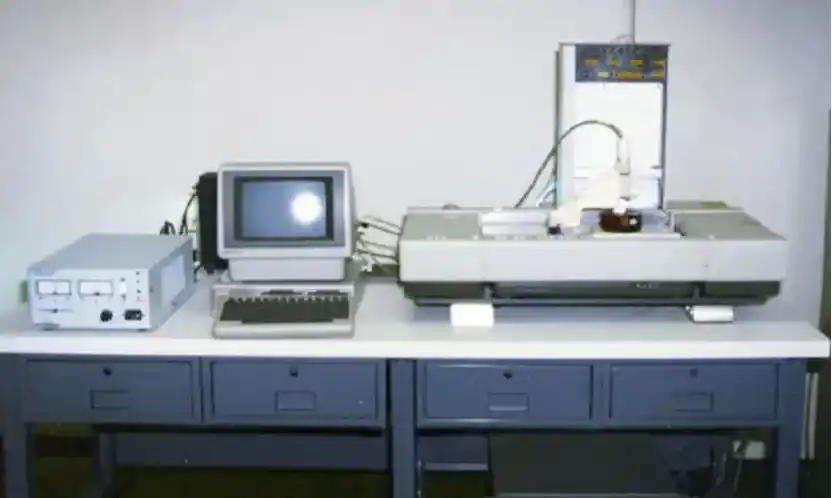
As one of the first 3D printing technologies invented in the 1980s, SLA was utilized with a primary focus on prototyping. During its early years, SLA machines were groundbreaking but prohibitively expensive. They were mostly used by large corporations and research institutions with substantial budgets for research and development.
Throughout the 1990s, SLA technology became more commercially viable. SLA technology expanded its reach to industries like aerospace, automotive, and healthcare. Prototyping remained a core application.
From 2000s on, SLA technology was used in various industries for rapid prototyping and even some limited production runs.
Today, SLA technology became almost ubiquitous. It still stands as a pinnacle of precision and efficiency in the realm of rapid prototyping.
SLA Technology’s Significance
The accuracy, speed, and surface finish of SLA has made it a leading choice for creating high-quality prototypes for concept modeling, fit testing, user research, and visualization.
It has become an indispensable tool in industries such as aerospace, healthcare, and automotive, where precision and performance are paramount.
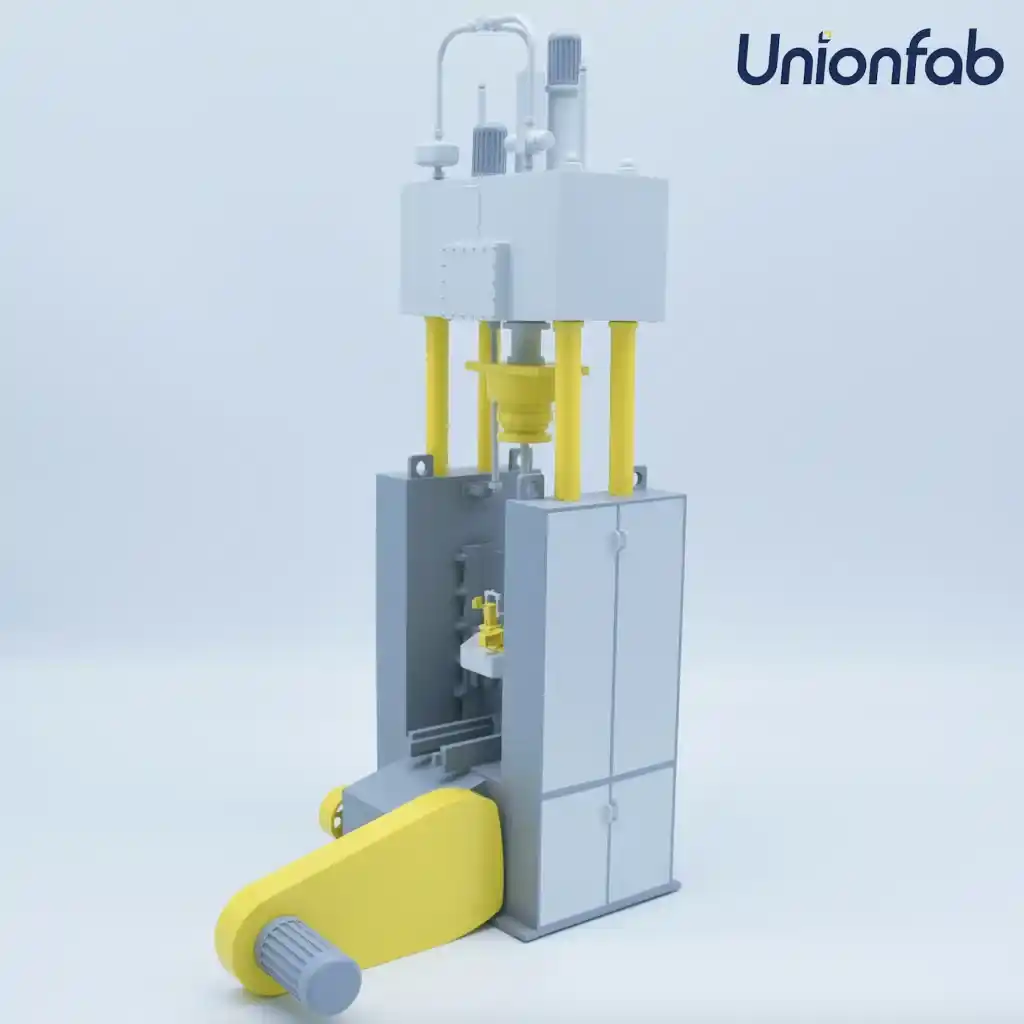
- Unparalleled Precision and Detail – SLA can produce details and tolerances down to 0.001 inches, capturing extremely fine features and complex geometries not possible with traditional methods. This enables high fidelity prototypes.
- Speed and Efficiency – SLA prototypes can be printed in hours or days rather than the weeks required for CNC machining or molding. Minimal setup and post-processing also improves speed.
- Material Variety and Quality – SLA resins range from rigid to flexible with properties engineered for different applications. The materials produce smooth, durable prototype parts.
- Complex Geometries Made Easy – Intricate internal structures, overhangs, and organic shapes are easily fabricated using SLA with no need for supports.
- Low Waste – SLA only uses the required resin, with no milling or leftover material. This makes it more sustainable and cost-effective than subtractive techniques.
- Surface Finishes – SLA parts require little to no post-processing, and have smooth, detailed exterior surfaces right out of the printer.
- Rapid Iteration – The speed of SLA allows designers to quickly print, evaluate, and refine multiple iterations of a prototype.
- Accuracy for Fit and Function – Exceptional tolerances and precision ensure SLA prototypes properly fit together and can be used for functional testing.
Design Optimization for SLA
Orientation for better print quality.
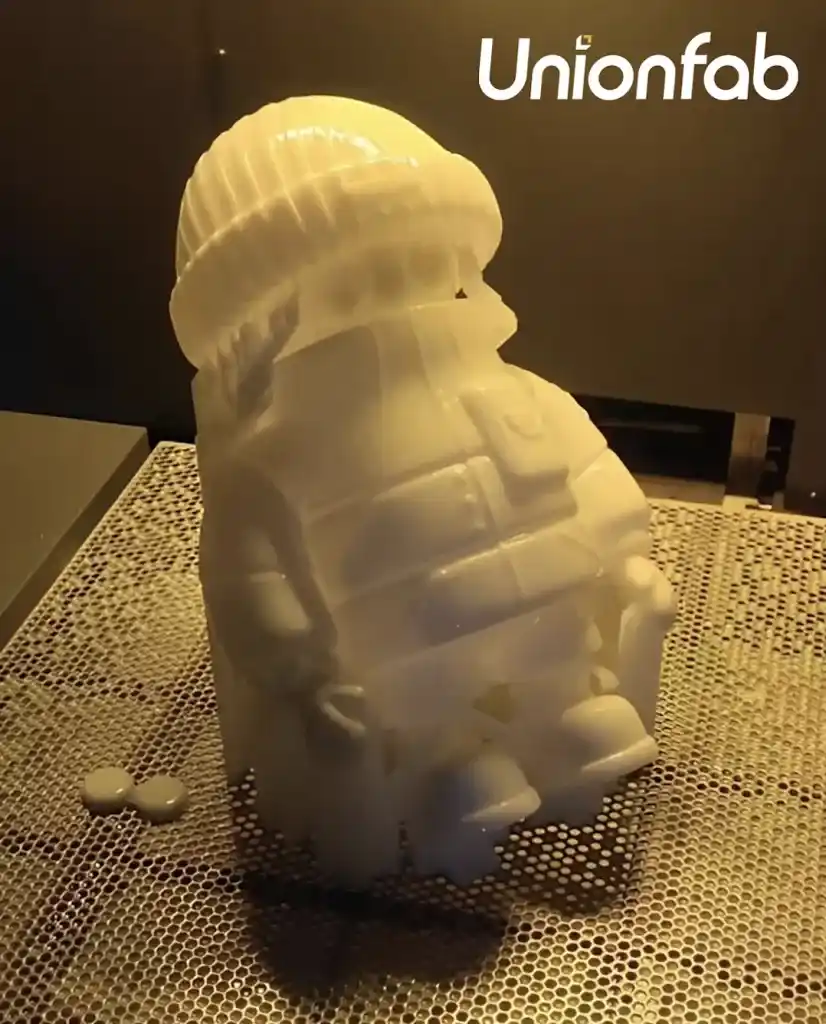
Proper part orientation can help minimize the need for support structures, reducing post-processing and material usage while ensuring successful prints.
Wall Thicknesses and Feature Sizes
There are minimum wall thicknesses based on resin viscosity and laser spot size. Designers must consider the minimum wall thicknesses to achieve the desired part strength and detail. Small features may not fabricate properly.
Accounting for Resin Properties and Post-Processing
Designs must account for resin shrinkage, thermal expansion, and requirements for post-curing, washing, etc. The choice of resin and its properties should align with the desired final characteristics of the prototype.
Troubleshooting Print Failures
Issues like cracking, warping, gaps, or poor detail can be caused by improper orientation, model errors, resin contamination, or machine factors.
Material Selection for SLA Rapid Prototyping

- Hardness: Resins come in a range of hardness from flexible to rigid, tailored to the required physical properties.
- Clear and colored resins provide a versatile range of options for achieving distinct visual aesthetics. Transparent resins, in particular, are ideal for creating see-through effects in mechanical and medical prototyping.
- Biocompatiblity: Bio-compatible resins allow prototyping of implants, medical and dental devices for testing fit and form.
- Strength: Resins with strength need to be considered if functional prototypes will endure stresses, heat or fluids over time.
- Composite resins: can prototype heat-resistant components for form/fit testing.
- Handling and storage for different resins – Different resins may have specific handling and storage requirements to maintain their quality and performance over time.
SLA (Stereolithography) Rapid Prototyping finds versatile applications across various industries, providing solutions for different needs and challenges. Here are some of the key applications of SLA technology:
Concept Models
Concept models are early stage physical representations of design ideas. They allow designers to visualize, test, and refine a concept before committing to a final design.
Functional Prototypes
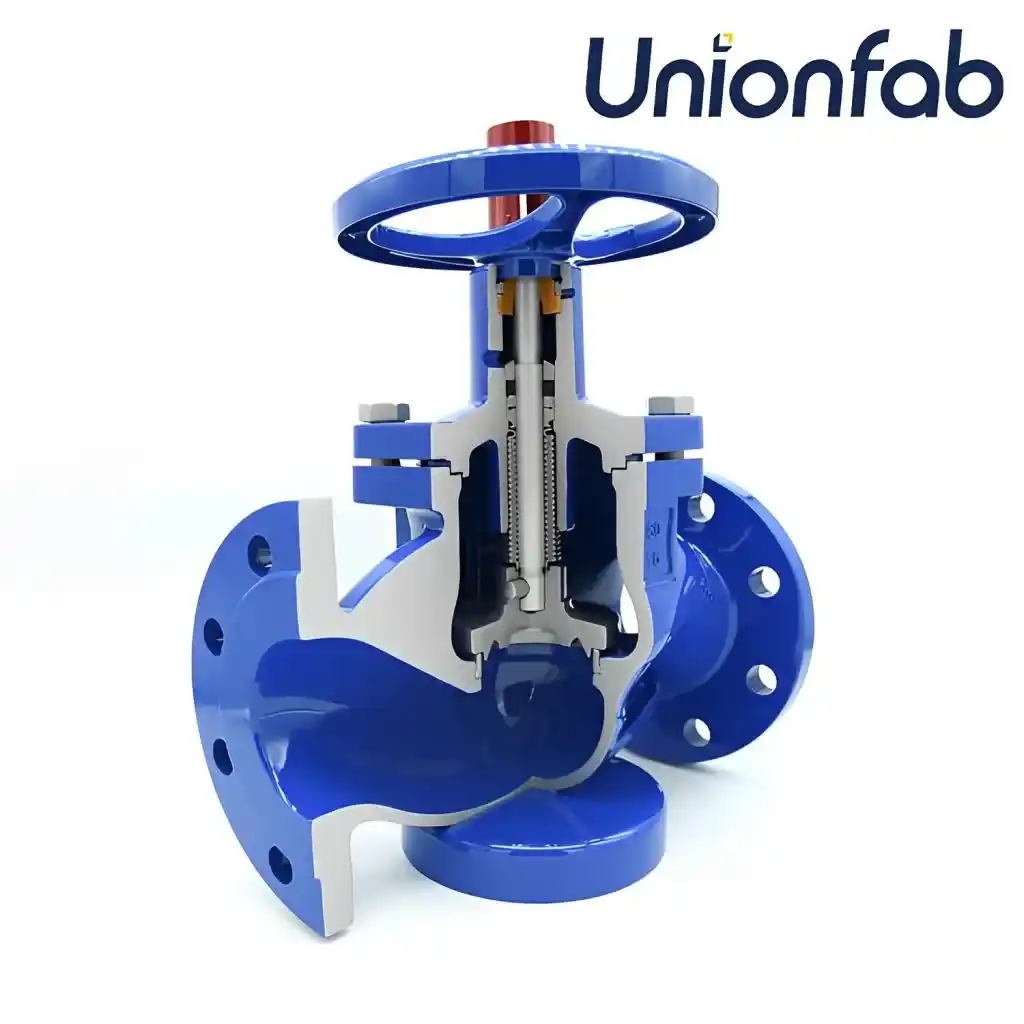
Functional prototypes are more fully developed versions of a design that demonstrate key functionality but may not be finalized in terms of appearance or production feasibility.
Small Batch Production
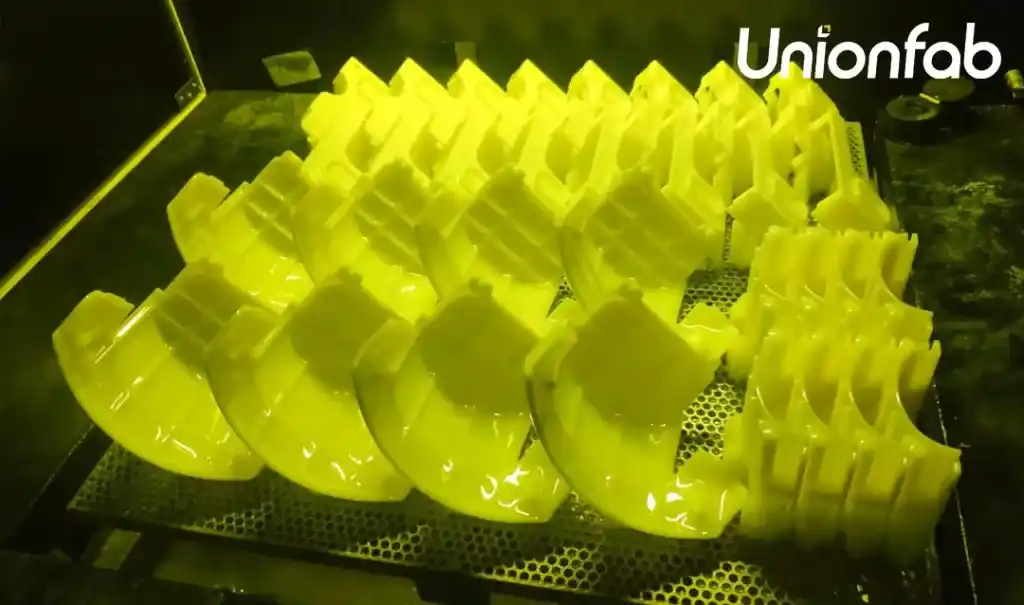
Production runs from a handful to a few hundred parts are well-suited to SLA. Larger volumes may be more cost effective on alternative production technologies.
Industry Applications
Industries like medical devices, automotive, consumer electronics commonly use SLA for design verification casts/tooling or initial low-rate production needs before high-volume manufacturing.
Aerospace and Defense
- Producing functional prototypes and form, fit and function testing of parts for aircraft before switching to another production method like injection molding.
- Customized parts in limited quantities for UAVs.
- Creating assembly and installation jigs, fixtures and tools.
Healthcare and Medical Devices
- Prototyping and testing implants, prosthetics, surgical tools and devices.
- Producing models for pre-operative planning and surgical training/simulation.
- Manufacturing custom fitting models for dental aligners, orthotics and prosthetics, etc.
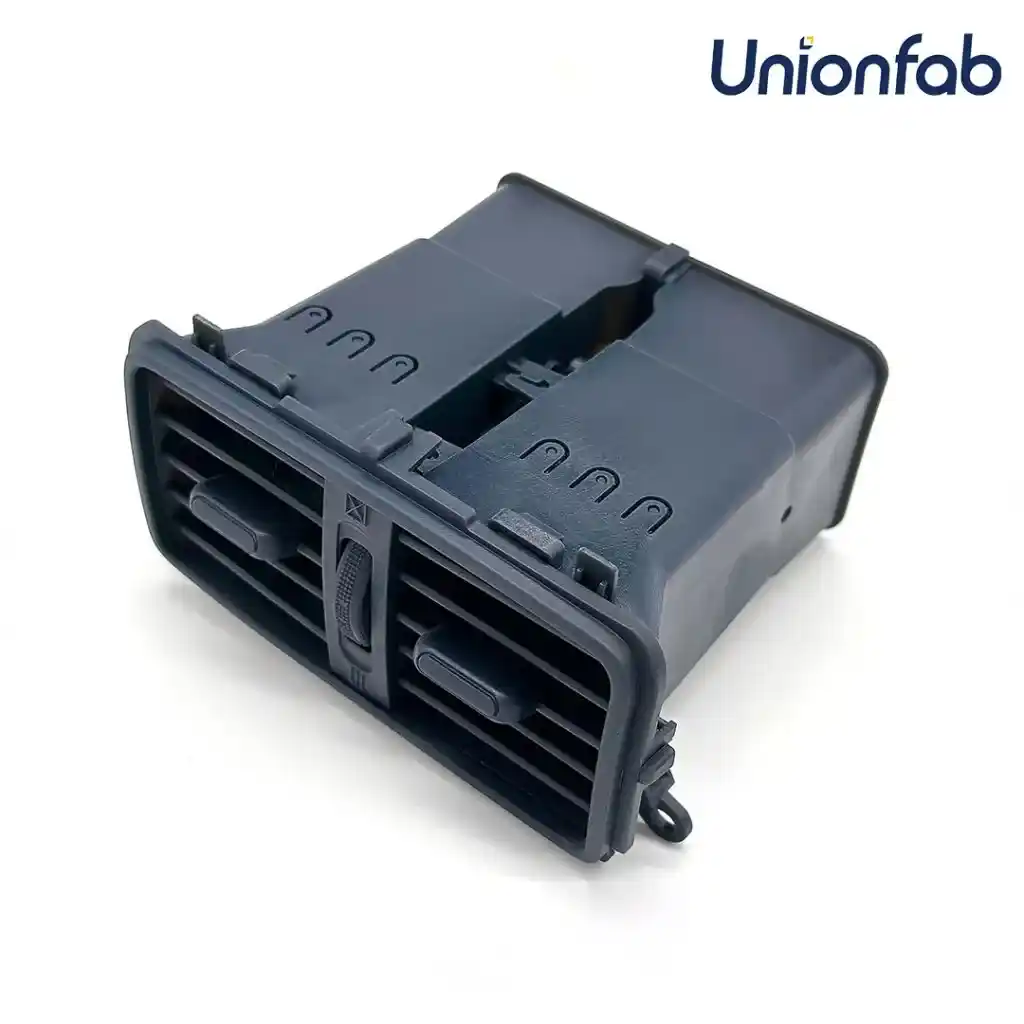
- 3D printed prototypes allow for rapid design iteration of parts, vents, consoles, trims etc.
- Producing low volume custom interior and exterior components.
- Jigs, fixtures and assembly tools improve quality control and efficiency.
Consumer Electronics
- Quickly prototyping devices, components, enclosures prior to manufacturing.
- Printing custom accessories, mounts and cases on-demand.
- Producing presentation models and samples for design validation.
Art and Design
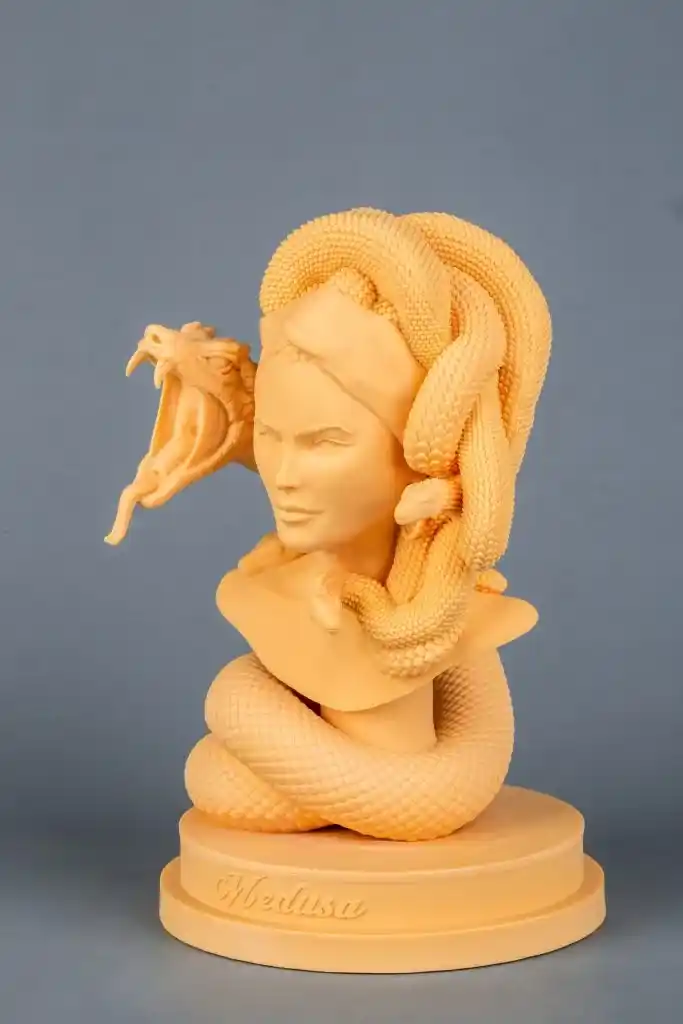
- Creating prototypes for fine art objects, jewelry, sculptural pieces, etc.
- Producing masters and production models for replication processes.
- Manufacturing limited runs of custom functional or decorative design objects.
Material Costs
- Resins used in SLA can be more expensive on a per-volume basis than plastics for injection molding.
- Material costs need to be considered in the number and size of prototypes required.
Size Constraints
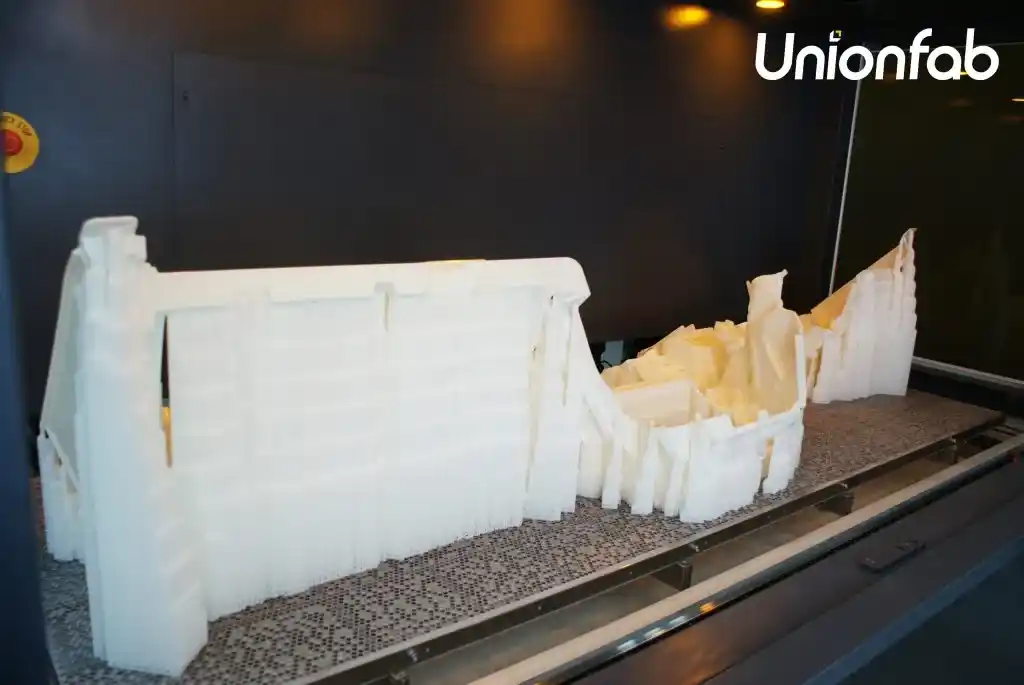
- Build volume is limited by the size of the SLA printer’s vat and build platform (now up to 2100 x 700 x 800mm at Unionfab).
- Large or unusually shaped parts may need to be split into multiple pieces and joined later.
Post-Processing Challenges
- Supports must be removed which can be difficult for complex geometries.
- Parts require washing/curing to complete polymerization which increases time and handling.
- Surface finishing may be needed through additional sanding or polishing.
Other Limitations
- SLA parts are typically made of resin materials that may not have the durability or temperature resistance for long-term use.
- Surface finish is usually rougher than molded plastic parts.
- Moving mechanical joints can degrade more rapidly than production materials.
- Curing and shrinkage result in less accurate dimensions vs production molds.
- Stress concentrations occur more easily than molded plastic.
As SLA technology continues to advance, the future looks promising for further reducing its limitations and increasing its applications:
Improved Material Properties
- New resins will provide improved material properties – tougher, more temperature resistant plastics suitable for end-use prototyping.
- New initiatives like multi-material SLA will introduce elastomers, waxes and other materials for functional molding prototypes.
Advanced Printing Technology
- Higher laser intensities and resolutions will enhance detailing and surface finishes, rivaling injection molded parts.
- Bigger build volumes on SLA machines will accommodate larger prototype sizes without assembly.
Technology Integration
- Integrated hardware and software will optimize printer parameters to fabricate parts with exacting tolerances.
- Cloud-based and mobile solutions will make SLA prototyping even more accessible to designers everywhere.
Sustainability-Focused Innovations
- Bio-Based Resins: Resins made from plant oils or agricultural byproducts offer eco-friendly material options, reducing reliance on petroleum sources.
- Remanufacturing and Refill Stations: Stations for resin cartridges and parts are extending the lifecycle of SLA printers and consumables, minimizing single-use waste.
In this exploration of SLA Rapid Prototyping, we discussed the core principles, applications, and future advancements. Key takeaways include:
- SLA’s layer-by-layer photopolymerization process enables intricate prototypes.
- Design, orientation, material choices, and post-processing play key roles in achieving successful prototypes.
- Material selection considers properties, biocompatibility, handling, storage and compatibility.
- SLA serves industries like aerospace, healthcare for concepts, functions, and small production batches.
- Ongoing developments promise improved materials, detailing, size, multi-material use, technology advancement and sustainability innovations.
Whether you’re a designer, engineer, artist, or entrepreneur, embracing SLA technology opens doors to faster, more efficient product development and design iteration.
Unionfab stands ready to support your prototyping needs. We offers cutting-edge solutions and expertise to help bring your ideas to life with precision and speed. Start you rapid prototyping with us and get a free quote!

Revolutionizing Dentistry: Resin and 3D Printing for Dental Care
3d printing vs. cnc vs. vacuum casting: the ultimate comparison, you may also like, tree supports in 3d printing: a helpful guide, 17-4 stainless steel properties: a comprehensive examination, what is titanium alloy and its advantage in..., titanium 3d printing and its role in consumer..., how to 3d print unbreakable screws and bolts, design for additive manufacturing (dfam): maximize 3d printing’s..., leave a comment cancel reply.
Save my name, email, and website in this browser for the next time I comment.
- Reference Manager
- Simple TEXT file
People also looked at
Original research article, virtual surgical planning/3d printing assisted fibula osteoseptocutaneous flap combined with anterolateral thigh flaps for extensive composite oromandibular defects reconstruction: a retrospective study of case series.
- 1 Department of Oral and Maxillofacial Surgery, The Affiliated Hospital of Qingdao University, Qingdao, China
- 2 School of Stomatology, Qingdao University, Qingdao, China
- 3 Dental Digital Medicine and 3D Printing Engineering Laboratory of Qingdao, Qingdao, China
- 4 Shandong Provincial Key Laboratory of Digital Medicine and Computer-Assisted Surgery, Qingdao, China
Oromandibular tumors or osteoradionecrosis often lead to extensive composite defects encompassing intraoral, bone and extraoral tissues. A single flap cannot simultaneously offer sufficient bone and soft tissue. The combination of free flaps could be a prospective approach to overcome the challenge. The study aims to assess the efficacy of virtual surgical planning (VSP) and 3D printing assisted fibula osteoseptocutaneous flap (FOSCF) combined with anterolateral thigh flaps (ALT) in reconstructing extensive composite defects in the oromandibular region. A retrospective analysis was conducted on 8 patients who underwent reconstruction using FOSCFs combined with ALTs. Post-surgical excision of the lesions, we obtained mean values for the defects of intraoral soft tissue, bone, extraoral soft tissue, namely, being 42.7 cm 2 , 96 mm, and 68.9 cm 2 . The mean surgical procedures took 712.5 min. A total of 16 flaps were harvested and transplanted for the 8 patients, with all successfully surviving. Postoperatively, complications manifested as localized intraoral infections in 2 cases, intermuscular vein thrombosis in another 2 cases, and pulmonary infections in 2 patients. Two patients unfortunately experienced tumor recurrence, at 12 and 3 months post-operation respectively. For the surviving 6 patients, the average follow-up period was 12.2 months. Regarding patient satisfaction, one expressed dissatisfaction with the contour of the mandible, and two exhibited moderate trismus. Objective assessments identified 1 case of oral incontinence and 2 cases where external flap contractures were observed. All 8 patients experienced restoration of masticatory function and were able to consume a soft diet within a month post-surgery. VSP/3D printing assisted FOSCFs combined with ALTs can be performed safely to reconstruct the extensive composite tissue defects in our study, with desirable esthetic and functional results, and it is a reliable option in selecting patients with defects involving multiple tissue types. However, the benefits of this method needed more cases to validate.
1 Introduction
Extensive composite oromandibular defects are frequently caused by surgical resection of sizeable primary tumors in the head and neck region, or the result of osteoradionecrosis (ORN) post-radiotherapy. The reconstruction of such complex defects, encompassing multiple structures such as external skin, mandible, and oral mucosa presents a formidable challenge. Free flap reconstruction is the standard of care in these extensive defects, while there may not exist a single free flap capable of simultaneously offering sufficient bone stock and soft tissue. In these instances, the combination of multiple free flaps proves to be an efficacious treatment strategy ( Lee et al., 2010 ; Weitz et al., 2015 ).
Selecting suitable free flap is integral to the reconstructive success and overall outcome. In contrast to iliac or scapular osteocutaneous free flaps, the FOSCF can provide longer bone segments as well as ample skin paddle for intraoral lining ( Taylor et al., 2016 ; Liu et al., 2022 ). The ALT is the most useful workhorse flap employed for microsurgical reconstruction. Depending on requirements, the flap can be harvested as myocutaneous, fasciocutaneous, adipofascial, or in combination with the adjacent tissues or muscles as chimeric flaps. This versatility makes it particularly suited for the reconstruction of extensive extraoral skin defects ( Hsieh et al., 2021 ; Ranganath et al., 2022 ). The advent of VSP and 3D printing marks a significant milestone for the FOSCF. The utilization of these techniques enhances the safety, accuracy, and symmetry of this surgical procedure while considerably reducing the operating time ( Ritschl et al., 2021 ; Al-Sabahi et al., 2022 ; Idris et al., 2022 ).
Despite their advantages, multi-flap approaches for the reconstruction of composite oromandibular defects continue to be challenging and are a subject of ongoing debate. A few reports are available on the functional and aesthetic outcome of double free flap reconstructions in these defects ( Lee et al., 2010 ; Tharakan et al., 2023 ). The objective of this study is to evaluate the effect of the combination of VSP/3D printing-assisted FOSCF with ALT in composite tissue defects reconstruction which could not be solved by one single flap.
2 Patients and methods
This study received approval from the Ethics Committee at the Affiliated Hospital of Qingdao University, Qingdao (ethics number, QYFYWZLL 27958). A retrospective review was conducted of 8 patients who underwent extensive composite oromandibular defects repair using the combination of VSP/3D printing-assisted FOSCF with ALT between July 2019 and December 2022 at our department.
The cohort comprised seven males and one female. All patients had undergone lesion resection, with extensive defects variably involving oral mucosa, mandible, and perioral skin areas. All defects were reconstructed using a FOSCF in combination with ALT. A two-team approach was consistently employed throughout all stages of the operation.
2.1 Preparation of the FOSCF assisted by VSP and 3D printing
All patients underwent routine preoperative three-dimensional CT scan of the mandible and fibula (SOMATOM Force CT, slice thickness 0.625 mm), in addition to lower limb CT angiography (CTA). The acquired data were input into the Mimics 17.0 software (Materialise, Leuven, Belgium) in the DICOM format. The software was used to simulate tumor excision, fibula osteotomy, mandibular reconstruction, and the design of repositioning guides. In the process, the mandibular osteotomy guide and the fibula positioning guide share the same nail track to ensure the accuracy of mandibular reconstruction. For those mandibular defects not traversing the midline, mirror technology was employed to accomplish reconstruction. However, in cases where the defects did cross the midline, a synergistic approach combining mirror and surface reconstruction techniques was adopted. Following the completion of the virtual surgery, the designed guides were materialized using an 3D printer (UltraCraft A2D, HeyGears), and subsequently sterilized with plasma. The reconstruction-team prepared the FOSCF. The skin perforator was located and the skin paddle was incised in accordance with the magnitude of the intraoral soft tissue defect. The fibula osteotomy guide was positioned, leading to the fibula being cut to the length prescribed in the virtual surgery. The distal end of the fibular artery was ligated, preserving the proximal vascular pedicle. The fibula was then contoured using the shaping guide and secured in position with miniplates. Upon completing the FOSCF preparation, the same team proceeded to harvest the ALT.
2.2 Oral lesion excision
The resection-team was tasked with the excision of the tumor at its safe boundary. According to the preoperative virtual surgical design, the mandibular osteotomy guide was positioned, followed by the segmental resection of the mandible. After the complete excision of the tumor, two sets of recipient vessels were prepared. Subsequent to the surgical procedure, patients were admitted to the intensive care unit (ICU), and tracheostomy was not a routine intervention. Patients were typically transferred back to the general ward within a period of 3–5 days postoperatively, contingent upon their stabilized condition. All patients needed nasogastric feeding for 1 week post-surgery. Subsequently, a soft or normal diet was gradually adopted. All patients except No.5 and No.8 underwent postoperative radiation therapy.
Surgical and medical complications were documented. A patients satisfaction questionnaire was administered to make subjective evaluation on chewing, speech, dry mouth and facial appearance, which were divided into three grades: very satisfied, satisfied and dissatisfied. To determine objective evaluation, facial appearance, oral incontinence, speech problems, eating problems, xerostomia, and flap contracture were assessed. Each individual item was scored using a Likert scale (1 = extremely abnormal and 5 = completely normal).
Our study comprised 8 patients including 7 males and 1 female, aged from 45 to 68 years (mean, 60.5 years). Seven of these patients presented with oral malignant tumors, all diagnosed as squamous cell carcinoma, while one patient (No.5) had osteoradionecrosis as a consequence of radiation therapy. A total of 16 flaps were prepared for 8 patients, which consisted 8 FOSCFs and 8 ALTs. Post-excision of the lesions, the dimensions of the intraoral soft tissue defects ranged from 7.5 × 4 cm to 12 × 6.5 cm (mean, 42.7 cm 2 ). The length of the bone defects extended from 76 mm to 125 mm (mean, 96 mm), while the extraoral soft tissue defects varied from 8 × 5 cm to 14 × 9 cm (mean, 68.9 cm 2 ). The anastomosis involved recipient arteries that included the facial artery, superior thyroid artery, and lingual artery. Concurrently, the recipient veins involved were the facial vein, superior thyroid vein, internal jugular vein, and external jugular vein. One case required vascular grafting. The operative duration for these procedures ranged between 600 and 840 min, with an average of approximately 712.5 min ( Table 1 ).
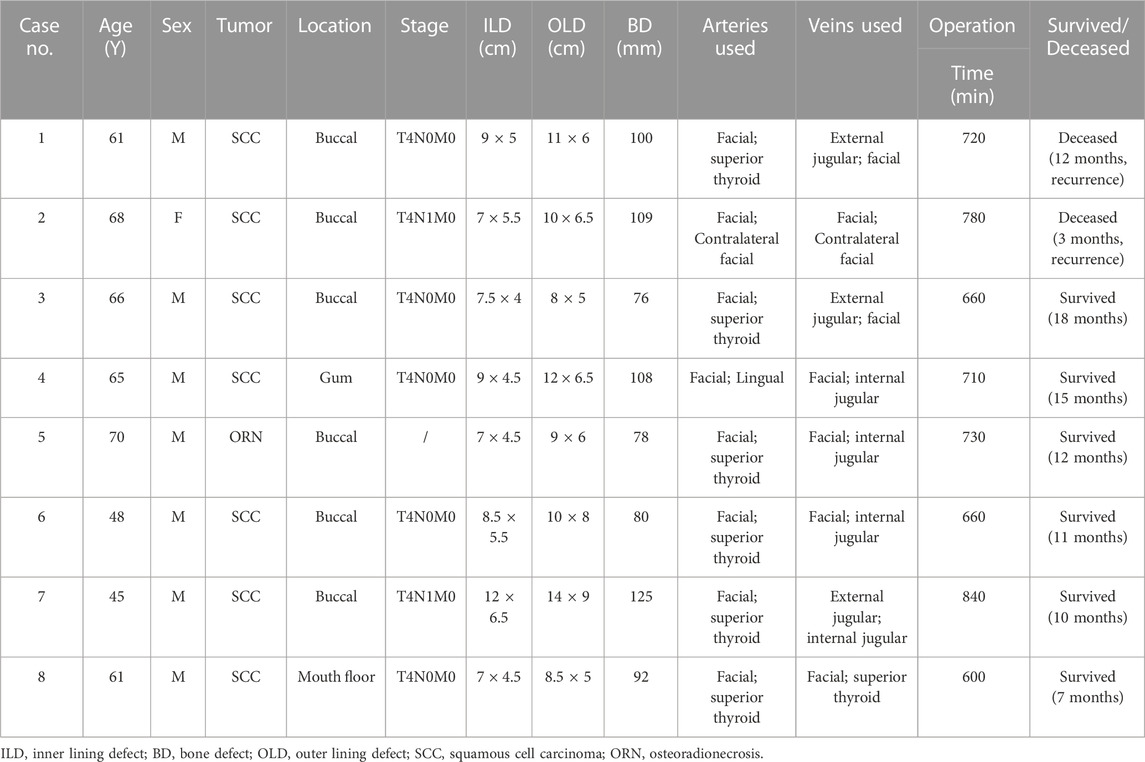
TABLE 1 . Patient data.
Remarkably, all of the flaps survived without any vascular crises or local flap necrosis. Two cases (No.3, No.4) developed local oral infections. Additionally, intermuscular vein thrombosis in the lower limbs was observed 2 patients (No.2, No.5). Pulmonary infection was found in 2 cases (No.2, No.4). Unfortunately, 2 of the 8 patients succumbed due to tumor recurrence at 12 months and 3 months post-surgery respectively. The mean follow-up time of the remaining 6 patients was 12.2 months (range, 7 months–18 months). Patient satisfaction assessments revealed one individual (No.3) was dissatisfied with their post-operative appearance, while two (No.2, No.4) reported moderate trismus. However, the remaining patients all reported satisfaction levels above average. Objective evaluations indicated oral incontinence in 1 case (No.4) and external flap contracture in 2 cases (No.2, No.4). Impressively, all 8 patients regained masticatory function and resumed a soft diet within a month post-operation.
3.1 Case presentation
A 45-year-old male patient diagnosed with a squamous cell carcinoma on his left cheek. The tumor demonstrated regression by radiation therapy (66 Gy) 7 months ago. However, the anterior part was ulcerated and gradually formed a penetrating defect after 1 month. Histopathological examination confirmed squamous cell carcinoma, staged clinically as T4N1M0. With the assistance of VSP and 3D printing technology, the reconstruction utilising both flaps was successfully performed ( Figures 1 , 2 ).
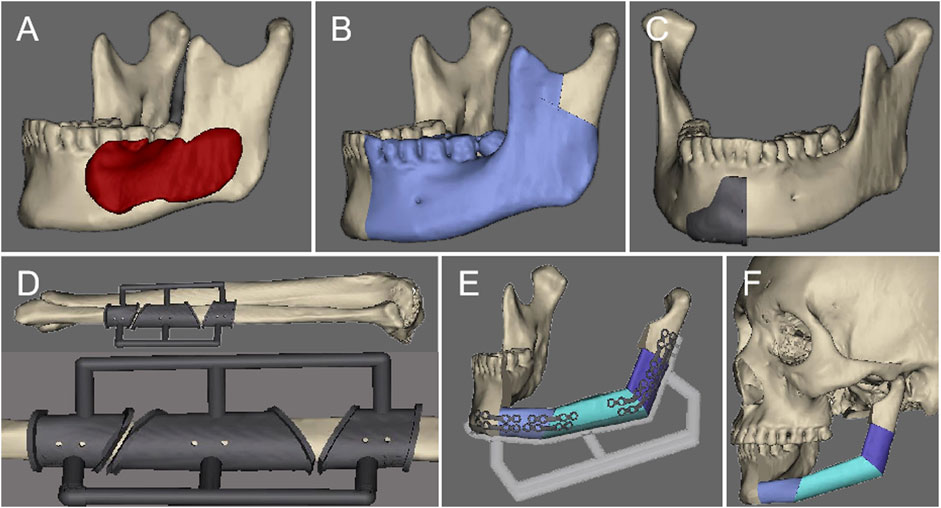
FIGURE 1 . The preoperative virtual surgical design: (A) . Determine the range of the lesion. (B) Simulate the range of bone cutting. (C) Design the bone cutting guide. (D) Design the fibula osteotomy guide. (E) Design the fibula repositioning guide. (F) Restore the mandibular contour.
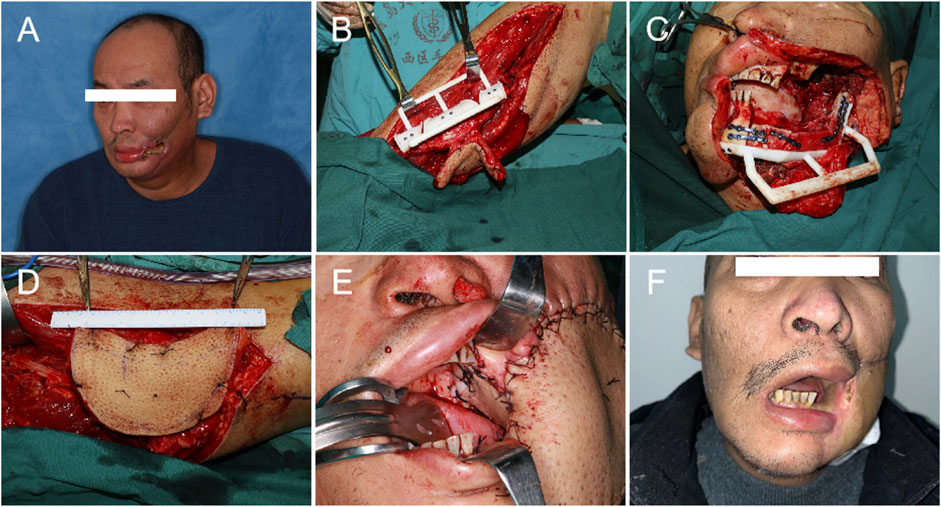
FIGURE 2 . Operational procedure: (A) . Preoperative photo. (B) Fibula shaping. (C) Fibula positioning. (D) Harvest of the ALT. (E) The fibula osteoseptocutaneous flap was used to repair the oral soft tissue and the mandible, and the ALT was used to repair the extraoral tissues. (F) 6 months post-operation.
4 Discussion
Surgical removal of oral tumors or osteoradionecrosis can result in substantial composite tissue defects, presenting formidable challenges for reconstructive repair. A single flap is often insufficient to adequately address these extensive defects. Consequently, the combination of multiple flaps has emerged as an innovative therapeutic approach ( Lee et al., 2010 ; Weitz et al., 2015 ; Hsieh and Bewley, 2019 ; Silva et al., 2019 ; Moratin et al., 2021 ; Raghuram et al., 2021 ; Santilli et al., 2021 ; Tharakan et al., 2023 ). The ALT can furnish sufficient tissue volume and can be fashioned into a chimeric flap with minimal impact on the donor site, rendering it an optimal choice for repair and reconstruction of large soft tissue defects in the oromandibular region ( Thomas et al., 2020 ). The FOSCF is exceptionally suitable for large bone tissue defects. Its accompanying skin paddle can repair tissues both inside or outside the oral cavity, and its associated muscle can effectively fill the surgical dead space ( Dowthwaite et al., 2013 ). Therefore, for large composite tissue defects in the oromandibular region, we opt for the ALT for the repair of extraoral soft tissue defects and the FOSCF for the repair of bone and intraoral soft tissue defects. Nevertheless, surgical alternatives should be carefully considered. The fibular flap can be substituted with a reconstruction plate, iliac bone muscle flap, or scapular bone muscle flap. Soft tissue flap can be replaced with a vascularized free flap or pedicled flap, such as the forearm flap, rectus abdominis flap, or pectoralis major myocutaneous flap. However, the radial forearm flap offers limited soft tissue volume, it is difficult to fill the dead cavity effectively. Its application is further limited by the severe scarring left on the forearm, tendon exposure, and forearm mobility disorders ( Ranganath et al., 2022 ). The rectus abdominis myocutaneous flap can deliver a satisfactory volume of soft tissue, yet it may trigger complications such as reduced abdominal wall strength and incisional hernia. While the pectoralis major flap supplies generous soft tissue, it’s typically considered a backup option. The free iliac flap has insufficient bone length to adequately repair the defects. Besides, the free scapular flap cannot effectively mimic the shape of the mandibula, and has limitations in deficient bone length ( Liu et al., 2022 ). Moreover, reconstruction plates are prone to complications like screw loosening, plate fracture, plate exposure and stress shielding.
A unique aspect of our study is the incorporation of VSP and 3D printing. VSP allows for tailoring surgical approaches, ensuring precise lesion delineation, osteotomy localization, and fibula harvest estimation. Preoperative mandibular modeling not only reduces surgical time but also ensures superior functional and aesthetic outcomes. 3D-printed guides, enhance surgical accuracy, fostering a closer match to the original mandibular structure. Shared screw tracks between the mandibular osteotomy and fibula positioning guides simplify the procedure, further minimizing trauma and operative time ( Seruya et al., 2013 ; Schepers et al., 2015 ; Wu et al., 2021 ). Using the osteotomy guide and positioning guide, the fibula is contoured and then affixed with mini titanium plates. Shaw et al. (2004) proved that there were no significant differences in complications between miniplates and reconstruction plates, but the author also highlighted the defects of reconstruction plates, including stress shielding, interference with the vascular pedicle, and problems of metal fatigue when bending plates in the sagittal plane. In comparison, miniplates which avoid the above drawbacks are a better choice. Intermaxillary fixation was performed after surgery for 1 week, encouraging oral exercises to prevent trismus.
The vascular pedicle is severed after the recipient vessels are prepared, markedly reducing ischemic time and overall duration of the surgery. Literature indicates that when the ALT donor site width is under 8.0 cm, primary closure is feasible; for wider defects, skin grafting becomes necessary ( Chen and Tang, 2003 ). Some reports suggest that direct suturing is feasible when the width is less than 10.0 cm ( Townley et al., 2011 ). Studies have proposed that the ratio of flap width to thigh circumference can serve as a reliable metric for direct wound closure, with a ratio less than 16% indicating direct closure ( Boca et al., 2010 ). In our study, we found that for one patient, the flap width was 9.0 cm, and direct suturing did not induce fascial compartment syndrome or other complications.
While the use of double flaps allows for the repair of large composite tissue defects in the oromandibular region, overcoming the limitations of a single flap or composite flap due to vascular pedicle restrictions, it demands higher provisions for neck vessels. This includes the preparation of two sets of anastomotic arteries and veins in the recipient area. In our study, it was found that arteries were relatively easier to prepare, with a total of 16 arteries prepared. The most frequently used anastomotic arteries were the facial artery and the superior thyroid artery, while the facial vein and internal jugular vein were the most commonly used anastomotic veins. Flow-through flaps, as reported in literature ( Qing et al., 2015 ; He et al., 2021 ), allow the usage of only one set of recipient area vessels. However, this approach carries a significant drawback: if a vascular crisis arises, both flaps are in danger of necrosis. Therefore, we advocate for the preparation of two sets of anastomotic arteries and veins in the recipient area to mitigate such circumstances. Literature suggests that the ligated internal jugular vein can be utilized for end-to-side anastomosis, offering a method for venous anastomosis ( Akazawa et al., 2019 ). Furthermore, it has been reported that the transverse cervical vein and superficial temporal vein can also serve as recipient area vessels ( Hansen et al., 2007 ; Tessler et al., 2017 ; Wang et al., 2021 ).
This method affords greater flexibility and autonomy, but it involves extended operation time, high costs, considerable trauma, and numerous potential complications. It mandates superior surgical skill, restricting its broader implementation. Inexperienced medical institutions and young physicians should first master single flap reconstruction before considering advanced techniques. Without this foundation, there’s a risk of increased surgical complications and irreversible outcomes. Additionally, the inclusion of 3D printing escalates treatment costs, making this approach unfeasible for institutions lacking this technology. In our study, though every flap transplantation was triumphant, five cases did confront complications. Two cases suffered from local oral infections and gradually recovered after conservative treatments. Two patients presented with intermuscular vein thrombosis in the lower limbs, which were successfully managed with oral medication, preventing the progression to potential organ embolisms such as cardiac, pulmonary, or cerebral embolism. Additionally, two cases demonstrated a pulmonary infection, which was effectively controlled with antibiotic therapy ( Tharakan et al., 2023 ). reported postoperative complications in multi-flap surgeries to range from 26% to 50%, aligning with our findings. Earlier research indicated a 5-year survival rate for advanced head and neck cancers between 25% and 56% ( Abdelmeguid et al., 2021 ; Mody et al., 2021 ). Our study, with 2 out of 8 patients succumbing to postoperative tumor recurrence, indicates a marginally superior survival rate, albeit potentially influenced by the relatively shorter follow-up duration. In summary, our study’s outcomes resonate with existing literature, suggesting that this approach doesn’t elevate complications or mortality rates.
It is crucial to acknowledge that patients who are candidates for this procedure are typically in the advanced stages of oral cancer. As such, it is of utmost importance to strictly adhere to the surgical indications:
1) The presence of extensive composite tissue defects, including intraoral, mandibula, and extraoral tissue defects that are too extensive to be repaired with a single flap;
2) The patient must be in good physical health, without obvious surgical contraindications such as congestive heart failure, pulmonary dysfunction, or neck vessel thrombosis;
3) The tumor can be completely resectable without systemic metastasis of lung and bone tissues;
4) The patient must possess a strong desire to combat the disease, as a positive attitude towards treatment is crucial.
However, this study does have limitations. Denture restoration is crucial for patients’ masticatory function ( Sozzi et al., 2017 ). Found that implant survival was high and implant-supported prostheses were a reliable rehabilitation option in patients whose jaws have been reconstruction with fibula-free flap. In our surgical method, fibula was used to prepare for implant repair in the future. However, due to postoperative adjuvant radiotherapy, patients paid more attention to tumor treatment and neglected denture repair. Both function and aesthetics are critically important, yet there is a potential gap in patients’ understanding of these aspects. Consequently, it’s our responsibility to educate them, promoting the benefits of implant restorations to restore masticatory function. Because of the rarity of such patients, we were unable to conduct controlled studies to objectively evaluate the advantages and disadvantages of this method compared to other treatment modalities. Nonetheless, we are confident that as the number of cases increases, the effectiveness of this treatment strategy will be confirmed. Moreover, the success of the double-flap surgery heavily relies on a precise preoperative surgical design and thorough considerations. The surgical approach offers limited flexibility, and the surgical procedure cannot be changed arbitrarily during the operation, as any deviations may result in a mismatch with the original design. Should unforeseen circumstances arise intraoperatively, we are prepared to implement alternative surgical strategies. Developing methodologies to anticipate, mitigate, and adeptly respond to such occurrences will constitute a primary objective in our ongoing research endeavors.
5 Conclusion
In conclusion, VSP/3D printing assisted FOSCFs combined with ALTs offers a safe and effective avenue for reconstructing oromandibular massive composite tissue defects in the study. However, the broader benefits and efficacy of this technique necessitate further validation through an expanded patient cohort.
Data availability statement
The original contributions presented in the study are included in the article/supplementary material, further inquiries can be directed to the corresponding author.
Ethics statement
The studies involving humans were approved by the ethical committee of the Affiliated Hospital of Qingdao University. The studies were conducted in accordance with the local legislation and institutional requirements. The participants provided their written informed consent to participate in this study. Written informed consent was obtained from the individual(s) for the publication of any potentially identifiable images or data included in this article.
Author contributions
YX: Investigation, Writing–original draft. YL: Investigation, Visualization, Writing–original draft. WX: Visualization, Writing–original draft. JY: Data curation, Writing–review and editing. LX: Validation, Writing–review and editing. LL: Data curation, Writing–review and editing. ZX: Formal Analysis, Writing–review and editing. JS: Funding acquisition, Resources, Writing–review and editing.
The author(s) declare financial support was received for the research, authorship, and/or publication of this article. This research was funded by the Qingdao Medical and Health Research Program (grant number: 2021-WJZD193), the Qingdao University Affiliated Hospital Clinical Medicine + X Scientific Research Project (grant number: QDFY+X202101041), the Shandong Province Medical and Health Technology Development Plan Project (grant number: 202208020979), Qingdao Key Health Discipline Development Fund and Oral Medicine Climbing Discipline Project in Qingdao.
Acknowledgments
This study was approved by the ethical committee of the affiliated hospital of qingdao university (NO. QYFYWZLL 27958).
Conflict of interest
The authors declare that the research was conducted in the absence of any commercial or financial relationships that could be construed as a potential conflict of interest.
Publisher’s note
All claims expressed in this article are solely those of the authors and do not necessarily represent those of their affiliated organizations, or those of the publisher, the editors and the reviewers. Any product that may be evaluated in this article, or claim that may be made by its manufacturer, is not guaranteed or endorsed by the publisher.
Abdelmeguid, A. S., Silver, N. L., Boonsripitayanon, M., Glisson, B. S., Ferrarotto, R., Gunn, G. B., et al. (2021). Role of induction chemotherapy for oral cavity squamous cell carcinoma. Cancer 127, 3107–3112. doi:10.1002/cncr.33616
PubMed Abstract | CrossRef Full Text | Google Scholar
Akazawa, T., Sekido, M., Adachi, K., Sasaki, K., Aihara, Y., Shibuya, Y., et al. (2019). End-to-Side venous anastomosis to a ligated vein stump for free flap transfer in head and neck reconstruction. Ann. Plast. Surg. 83, 180–182. doi:10.1097/sap.0000000000001905
Al-Sabahi, M. E., Jamali, O. M., Shindy, M. I., Moussa, B. G., Amin, A. A., and Zedan, M. H. (2022). Aesthetic reconstruction of onco-surgical mandibular defects using free fibular flap with and without CAD/CAM customized osteotomy guide: a randomized controlled clinical trial. BMC Cancer 22, 1252. doi:10.1186/s12885-022-10322-y
Boca, R., Kuo, Y. R., Hsieh, C. H., Huang, E. Y., and Jeng, S. F. (2010). A reliable parameter for primary closure of the free anterolateral thigh flap donor site. Plast. Reconstr. Surg. 126, 1558–1562. doi:10.1097/prs.0b013e3181ef8cb7
Chen, H. C., and Tang, Y. B. (2003). Anterolateral thigh flap: an ideal soft tissue flap. Clin. Plast. Surg. 30, 383–401. doi:10.1016/s0094-1298(03)00040-3
Dowthwaite, S. A., Theurer, J., Belzile, M., Fung, K., Franklin, J., Nichols, A., et al. (2013). Comparison of fibular and scapular osseous free flaps for oromandibular reconstruction: a patient-centered approach to flap selection. JAMA Otolaryngol. Head. Neck Surg. 139, 285–292. doi:10.1001/jamaoto.2013.1802
Hansen, S. L., Foster, R. D., Dosanjh, A. S., Mathes, S. J., Hoffman, W. Y., and Leon, P. (2007). Superficial temporal artery and vein as recipient vessels for facial and scalp microsurgical reconstruction. Plast. Reconstr. Surg. 120, 1879–1884. doi:10.1097/01.prs.0000287273.48145.bd
He, J., Qing, L., Wu, P., Zhou, Z., Yu, F., and Tang, J. (2021). Large wounds reconstruction of the lower extremity with combined latissimus dorsi musculocutaneous flap and flow-through anterolateral thigh perforator flap transfer. Microsurgery 41, 533–542. doi:10.1002/micr.30754
Hsieh, F., Leow, O. Q. Y., Cheong, C. F., Hung, S. Y., and Tsao, C. K. (2021). Musculoseptocutaneous perforator of anterolateral thigh flap: a clinical study. Plast. Reconstr. Surg. 147, 103e–110e. doi:10.1097/prs.0000000000007471
Hsieh, T. Y., and Bewley, A. (2019). Use of multiple free flaps in head and neck reconstruction. Curr. Opin. Otolaryngol. Head. Neck Surg. 27, 392–400. doi:10.1097/moo.0000000000000574
Idris, S., Logan, H., Tabet, P., Osswald, M., Nayar, S., and Seikaly, H. (2022). The accuracy of 3D surgical design and simulation in prefabricated fibula free flaps for jaw reconstruction. J. Pers. Med. 12, 1766. doi:10.3390/jpm12111766
Lee, J. T., Hsu, H., Wang, C. H., Cheng, L. F., Sun, T. B., Huang, C. C., et al. (2010). Reconstruction of extensive composite oromandibular defects with simultaneous free anterolateral thigh fasciocutaneous and fibular osteocutaneous flaps. J. Reconstr. Microsurg 26, 145–151. doi:10.1055/s-0029-1242134
Liu, A. Q., Deane, E. C., Heffernan, A., Ji, Y., Durham, J. S., and Prisman, E. (2022). Patient-reported outcomes and morbidity after head and neck reconstructions: an evaluation of fibular and scapular free flaps. Oral Oncol. 132, 106019. doi:10.1016/j.oraloncology.2022.106019
Mody, M. D., Rocco, J. W., Yom, S. S., Haddad, R. I., and Saba, N. F. (2021). Head and neck cancer. Lancet 398, 2289–2299. doi:10.1016/s0140-6736(21)01550-6
Moratin, J., Horn, D., Heinemann, M., Metzger, K., Mrosek, J., Ristow, O., et al. (2021). Multiple sequential free flap reconstructions of the head and neck: a single-center experience. Plast. Reconstr. Surg. 148, 791e–799e. doi:10.1097/prs.0000000000008432
Qing, L., Wu, P., Liang, J., Yu, F., Wang, C., and Tang, J. (2015). Use of flow-through anterolateral thigh perforator flaps in reconstruction of complex extremity defects. J. Reconstr. Microsurg 31, 571–578. doi:10.1055/s-0035-1555138
Raghuram, A. C., Manfro, G., Teixeira, G. V., Cernea, C. R., Dias, F. L., Marco, M., et al. (2021). Use of single chimeric free flaps or double free flaps for complex head and neck reconstruction. J. Reconstr. Microsurg 37, 791–798. doi:10.1055/s-0041-1727188
Ranganath, K., Jalisi, S. M., Naples, J. G., and Gomez, E. D. (2022). Comparing outcomes of radial forearm free flaps and anterolateral thigh free flaps in oral cavity reconstruction: a systematic review and meta-analysis. Oral Oncol. 135, 106214. doi:10.1016/j.oraloncology.2022.106214
Ritschl, L. M., Mucke, T., Hart, D., Unterhuber, T., Kehl, V., Wolff, K. D., et al. (2021). Retrospective analysis of complications in 190 mandibular resections and simultaneous reconstructions with free fibula flap, iliac crest flap or reconstruction plate: a comparative single centre study. Clin. Oral Investig. 25, 2905–2914. doi:10.1007/s00784-020-03607-8
Santilli, M., D'Addazio, G., Rexhepi, I., Sinjari, B., and Filippini, A. (2021). Multiple free flap reconstruction of a complex intraoral defect after squamous cell carcinoma excision: a case report. Med. Kaunas. 58, 54. doi:10.3390/medicina58010054
CrossRef Full Text | Google Scholar
Schepers, R. H., Raghoebar, G. M., Vissink, A., Stenekes, M. W., Kraeima, J., Roodenburg, J. L., et al. (2015). Accuracy of fibula reconstruction using patient-specific CAD/CAM reconstruction plates and dental implants: a new modality for functional reconstruction of mandibular defects. J. Craniomaxillofac Surg. 43, 649–657. doi:10.1016/j.jcms.2015.03.015
Seruya, M., Fisher, M., and Rodriguez, E. D. (2013). Computer-assisted versus conventional free fibula flap technique for craniofacial reconstruction: an outcomes comparison. Plast. Reconstr. Surg. 132, 1219–1228. doi:10.1097/prs.0b013e3182a3c0b1
Shaw, R. J., Kanatas, A. N., Lowe, D., Brown, J. S., Rogers, S. N., and Vaughan, E. D. (2004). Comparison of miniplates and reconstruction plates in mandibular reconstruction. Head. Neck 26, 456–463. doi:10.1002/hed.10343
Silva, A. K., Humphries, L. S., Maldonado, A. A., and Gottlieb, L. J. (2019). Chimeric vs composite flaps for mandible reconstruction. Head. Neck 41, 1597–1604. doi:10.1002/hed.25606
Sozzi, D., Novelli, G., Silva, R., Connelly, S. T., and Tartaglia, G. M. (2017). Implant rehabilitation in fibula-free flap reconstruction: a retrospective study of cases at 1-18 years following surgery. J. Craniomaxillofac Surg. 45, 1655–1661. doi:10.1016/j.jcms.2017.06.021
Taylor, G. I., Corlett, R. J., and Ashton, M. W. (2016). The evolution of free vascularized bone transfer: a 40-year experience. Plast. Reconstr. Surg. 137, 1292–1305. doi:10.1097/prs.0000000000002040
Tessler, O., Gilardino, M. S., Bartow, M. J., St Hilaire, H., Womac, D., Dionisopoulos, T., et al. (2017). Transverse cervical artery: consistent anatomical landmarks and clinical experience with its use as a recipient artery in complex head and neck reconstruction. Plast. Reconstr. Surg. 139, 745e–751e. doi:10.1097/prs.0000000000003085
Tharakan, T., Marfowaa, G., Akakpo, K., Jackson, R., Zenga, J., Puram, S. V., et al. (2023). Multiple simultaneous free flaps for head and neck reconstruction: a multi-institutional cohort. Oral Oncol. 136, 106269. doi:10.1016/j.oraloncology.2022.106269
Thomas, W. W., Calcagno, H. E., Azzi, J., Petrisor, D., Cave, T., Barber, B., et al. (2020). Incidence of inadequate perforators and salvage options for the anterior lateral thigh free flap. Laryngoscope 130, 343–346. doi:10.1002/lary.28176
Townley, W. A., Royston, E. C., Karmiris, N., Crick, A., and Dunn, R. L. (2011). Critical assessment of the anterolateral thigh flap donor site. J. Plast. Reconstr. Aesthet. Surg. 64, 1621–1626. doi:10.1016/j.bjps.2011.07.015
Wang, L., Ma, C. Y., Shen, Y., Fang, J., Haugen, T. W., Guo, B., et al. (2021). Transverse cervical artery anterior perforator flap for head and neck oncological reconstruction: preliminary study. Head. Neck 43, 3598–3607. doi:10.1002/hed.26873
Weitz, J., Kreutzer, K., Bauer, F. J., Wolff, K. D., Nobis, C. P., and Kesting, M. R. (2015). Sandwich flaps as a feasible solution for the management of huge mandibular composite tissue defects. J. Craniomaxillofac Surg. 43, 1769–1775. doi:10.1016/j.jcms.2015.07.038
Wu, P., Hu, L., Li, H., Feng, L., Liu, Y., Zhang, S., et al. (2021). Clinical application and accuracy analysis of 3D printing guide plate based on polylactic acid in mandible reconstruction with fibula flap. Ann. Transl. Med. 9, 460. doi:10.21037/atm-20-6781
Keywords: flap transplantation, reconstructive surgery, virtual surgical planning, multipleflap, 3D printing
Citation: Xu Y, Li Y, Xiao W, Yue J, Xue L, Li L, Xu Z and Sun J (2023) Virtual surgical planning/3D printing assisted fibula osteoseptocutaneous flap combined with anterolateral thigh flaps for extensive composite oromandibular defects reconstruction: a retrospective study of case series. Front. Bioeng. Biotechnol. 11:1273318. doi: 10.3389/fbioe.2023.1273318
Received: 05 August 2023; Accepted: 23 October 2023; Published: 02 November 2023.
Reviewed by:
Copyright © 2023 Xu, Li, Xiao, Yue, Xue, Li, Xu and Sun. This is an open-access article distributed under the terms of the Creative Commons Attribution License (CC BY). The use, distribution or reproduction in other forums is permitted, provided the original author(s) and the copyright owner(s) are credited and that the original publication in this journal is cited, in accordance with accepted academic practice. No use, distribution or reproduction is permitted which does not comply with these terms.
*Correspondence: Jian Sun, [email protected]
This article is part of the Research Topic
Advanced Oral Disease Therapy: Approaches, Biotechnology, and Bioactive Materials, Volume II
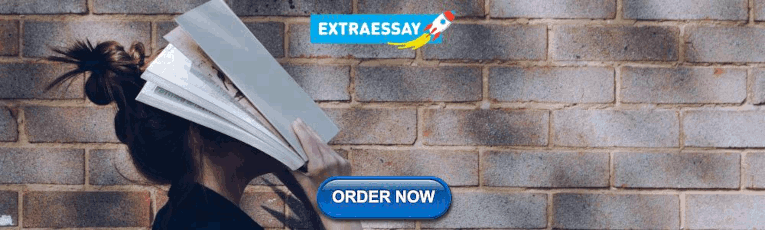
IMAGES
VIDEO
COMMENTS
This article was updated in May 2021. The automotive industry is facing demands on all fronts: the demand for newer, better-performing vehicles, as well as the need to optimise production and streamline supply chains and logistics. One technology that is helping to meet these challenges is 3D printing. 3D printing is increasingly being explored across all areas of automotive production.
Automotive 3D printing is transforming vehicle production by enabling engineers to design and manufacture stronger, lighter and more cost-effective parts. ... Case Study 2: 3D PRINTING INNOVATION MEETS AUTOMOTIVE HERITAGE . For collectors of rare classic cars, the availability of spare parts can mean the difference between driving a vehicle or ...
3D printing in the automotive industry has become a game-changer in the manufacturing process, and the automotive sector is no exception. The capabilities of industrial 3D printers are transforming the automotive industry by enabling faster prototyping, reducing production costs, and enhancing vehicle performance.
"The accuracy of the Objet30 3D Printer enables us to take a full-size part and scale it down to produce a one-tenth scale model," David Hayward, operations and projects manager at the Bentley Design Studio, explained in a case study. "Once we have approval at this scale, we can move on to our larger Objet500 Connex 3D Printer to produce one-
The Results: Speed, Quality & In-House Knowledge. Using 3D printing to build its fixture meant MAHLE reaped many benefits. In less than a week, MAHLE had a redesigned, dimensionally accurate and stable part delivered to them from across the world - a process that would have taken 4 to 5 weeks with conventional manufacturing.
VW is able to print parts to test production systems before investing in a final injection mould. Volkswagen is able to use the polypropylene sintered parts in its production line welding stations without modifying the process parameters, unlocking significant gains in efficiency. With the introduction of a material with end-use properties, 3D ...
By securing a registration from IMDS, the visibility for 3D printing in automotive production sharply increases, highlighting it's potential as a cost-effective, compliant, and agile solution to small series production. Using GENERA printing technology and LOCTITE material, the part designed was among the first IMDS listed and end-use ...
Try our interactive ROI tool to calculate cost per part and lead time when 3D printing on Formlabs 3D printers. Calculate Your Time and Cost Savings. Fog Lamp. 29.5 x 15.3 x 15.2 cm. 11.6 x 6.0 x 5.9 in. With technical resins, such as High Temp Resin and Rigid 10K Resin, we can manufacture tools and prototypes, such as inserts for injection ...
When it comes to industrial 3D printing for automotive applications, London-based Betatype is building up considerable expertise. The 3D printing company was founded in 2012, and works with its ...
After all, 3D printing is a game changer for the sector and the tendency is the consolidation of additive manufacturing throughout all its segments. According to SmartTech ' s forecast for automotive additive manufacturing, the market which generated $1.1 million in 2017 will grow to $5.3 million in 2023.
3D Printing for Automotive. July 22, 2022. By Nick AllenManaging Director,3DPRINTUK. A case study describes how 3D printing can be used for automotive sculptures. The Monster 917 is a sculpture based on a Porsche model. The sculpture is a maze of tubular aluminum and carbon fiber.
Learn how Vital Auto creates high-fidelity prototypes and concept cars, rapidly working through iterations using a variety of advanced tools, including a large fleet of Form 3L and Fuse 1+ 3D printers. Vital is situated in the heart of the UK's auto industry. The company's portfolio of clients includes a variety of the major automotive manufacturers.
Case Study: Remodeling an Automotive Spare Part. Providing start-to-end solutions for spare part replacement. Get A Quote. Challenge. ... 3D printing. For fitting checks, the prototype part was first 3D printed in standard low cost grey resin using SLA 3D printing. This is to ensure that the 3D modelled spare part is as dimensionally accurate ...
The Current Status and Impact of 3D Printing Within the Industrial Sector: An Analysis of Six Case Studies. Centre for Intellectual Property Policy & Management, 2015 (41), 1-15.
Introducing Addigy ® P1210 PBT Powder for 3D Printing. Addigy ® P1210 is a PBT powder engineered specifically for 3D printing using selective laser sintering (SLS) technology. This innovation means electronic components, such as an automotive fuse box, can now be 3D-printed with the same material used in traditional manufacturing.
3D Printing Automotive Fixtures Case Study January 17, 2020. Automotive parts supplier MAHLE gets up to speed on the full capabilities and associated benefits of 3D printing fixtures. Read more Case Study. 3D Printing Snare Drums Case Study December 16, 2019. Panic! At The Disco drummer Dan Pawlovich tours the world with a 3D printed snare drum.
Benefit: MJF enabled simultaneous printing of both cavities. It also reduced the cost by 46% and and reduced lead times from two weeks, to two days. Read the full case study here. Learn more about 3D printing automotive molds and tooling here - link to contact us
Exco is 3D printing the die inserts that go into the cast molds. Inserts are typically machined from H13 tool steel because they bear the brunt of the casting process, which involves high-pressure molten aluminum being injected into the mold. Years ago, Byleveld sent water jackets to several metal AM companies to find out if they could be printed.
The Racing Team at Chevy, employing 3D printing technology, have equipped their race cars , specifically the Corvette C8.R, INDYCAR, Silverado race truck and NASCAR Camaro, with 3D printed parts. This has successfully allowed themselves to not only support over 80,000 miles of production, but to take home a whole trophy case worth of awards in ...
Mantle 3D printers reduce tooling lead times by 50%, new customers announced. Alex Tyrer-Jones February 13th 2024 - 7:29pm. US-based metal 3D printer manufacturer Mantle has expanded the reach of ...
Manufacturing machinery parts with HP MJF 3D printing technology... 3D Printing Orthotic Devices Improves Comfort and Versatility - HP... 3D Printing Industrial Parts - Gimatic 3D Printing Case Study OT4 Creates 3D Printed Hand Brace with HP Multi Jet Fusion - OT4 Case Study HP Jet Fusion 5420W Industrial 3D Printer - White Part Production ...
A case study of automotive parts, i.e. mirror panel of bikes such as racing bikes, bobber bikes and new designs and the results, is compared with customized designed components. ... Additive manufacturing/3D printing is a revolutionary technology that uses layers of material to create objects from 3D digital data for various applications. Now ...
4D printing is an advanced manufacturing technology in which the 3D printed structure evolves over time, and this evolution can be a change in appearance, change in material properties, or change in color. The controllability and reversibility of the 4D printing process have received little research attention. In this research, a combination of polylactic acid and microparticles of strontium ...
Automotive (54) Aerospace (35) Education (34) Dental (26) Art and Fashion (14) Railway (6) Government/Military (6) More Application. ... Read our new case study to learn how GWR uses 3D printing to bring sustainability to the rails. Read more Case Study. How Generative Restoration is Reimagining Korean Cultural Heritage ...
Case Study: Reinventing Opera with 3D Printing and... July 14, 2023. Architecture. ... SLA 3D Printing for Automotive - From Prototyping... August 16, 2023. Consumer Products. ... As one of the first 3D printing technologies invented in the 1980s, SLA was utilized with a primary focus on prototyping. ...
Oromandibular tumors or osteoradionecrosis often lead to extensive composite defects encompassing intraoral, bone and extraoral tissues. A single flap cannot simultaneously offer sufficient bone and soft tissue. The combination of free flaps could be a prospective approach to overcome the challenge. The study aims to assess the efficacy of virtual surgical planning (VSP) and 3D printing ...
The Solution: 5X Surgical Guide Production with DentaJet. Enter the J5 DentaJet 3D printing solution, powered by Stratasys PolyJet technology. By adding the J5 DentaJet to their production center, 3Diemme found a multi-material additive manufacturing production process managed by an advanced software platform.