Help | Advanced Search
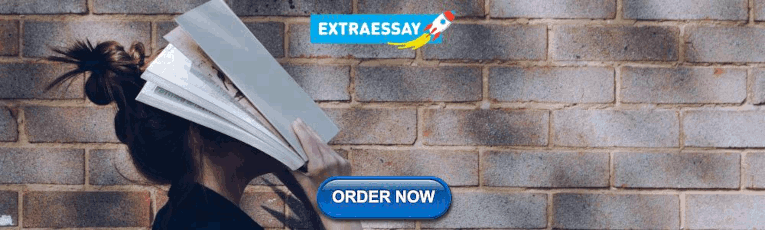
Computer Science > Hardware Architecture
Title: a survey of network-on-chip tools.
Abstract: Nowadays System-On-Chips (SoCs) have evolved considerably in term of performances, reliability and integration capacity. The last advantage has induced the growth of the number of cores or Intellectual Properties (IPs) in a same chip. Unfortunately, this important number of IPs has caused a new issue which is the intra-communication between the elements of a same chip. To resolve this problem, a new paradigm has been introduced which is the Network-On-Chip (NoC). Since the introduction of the NoC paradigm in the last decade, new methodologies and approaches have been presented by research community and many of them have been adopted by industrials. The literature contains many relevant studies and surveys discussing NoC proposals and contributions. However, few of them have discussed or proposed a comparative study of NoC tools. The objective of this work is to establish a reliable survey about available design, simulation or implementation NoC tools. We collected an important amount of information and characteristics about NoC dedicated tools that we will present throughout this survey. This study is built around a respectable amount of references and we hope it will help scientists.
Submission history
Access paper:.
- Other Formats
References & Citations
- Google Scholar
- Semantic Scholar
DBLP - CS Bibliography
Bibtex formatted citation.

Bibliographic and Citation Tools
Code, data and media associated with this article, recommenders and search tools.
- Institution
arXivLabs: experimental projects with community collaborators
arXivLabs is a framework that allows collaborators to develop and share new arXiv features directly on our website.
Both individuals and organizations that work with arXivLabs have embraced and accepted our values of openness, community, excellence, and user data privacy. arXiv is committed to these values and only works with partners that adhere to them.
Have an idea for a project that will add value for arXiv's community? Learn more about arXivLabs .
- Search in titles only Search in Epigenetics only Search
- Advanced Search
You are currently viewing the SEQanswers forums as a guest, which limits your access. Click here to register now , and join the discussion
Seqanswers Leaderboard Ad
Announcement.
- Latest Activity
- Time All Time Today Last Week Last Month
- Show All Discussions only Photos only Videos only Links only Polls only Events only

- Join Date: Oct 2007
- Posts: 1353
A brief review of recent ChIP-Seq tools literature
- F-Seq: a feature density estimator for high-throughput sequence tags. , Duke University. F-Seq Project Homepage
- CisGenome: An integrated software system for analyzing ChIP-chip and ChIP-seq data ., Johns Hopkins. CisGenome homepage
- ChromaSig: a probabilistic approach to finding common chromatin signatures in the human genome. , UC San Diego. ChromaSig homepage
- An HMM approach to genome-wide identification of differential histone modification sites from ChIP-seq data. , Genome Institute of Singapore. ChiPDiff Homepage
- Model-based Analysis of ChIP-Seq (MACS). , Dana-Farber Cancer Institute and Harvard School of Public Health. MACS Homepage
- A Poisson mixture model to identify changes in RNA polymerase II binding quantity using high-throughput sequencing technology. , Indiana University School of Medicine
- Genome-wide identification of in vivo protein-DNA binding sites from ChIP-Seq data. , NHLBI, NIH. SISSRs Homepage
- Modeling ChIP sequencing in silico with applications. , Yale University. ChIP-Seq Simulator Homepage
- Genome-wide analysis of transcription factor binding sites based on ChIP-Seq data. , Stanford University Medical Center (woohoo!), QuEST Homepage
- FindPeaks 3.1: a tool for identifying areas of enrichment from massively parallel short-read sequencing technology. , BCGSC (First author is our very own apfejes !). Vancouver Short Read Analysis Package Homepage . Version 3.2 is out.

- Join Date: Aug 2008

- Join Date: Feb 2008

- Join Date: Nov 2008

- Join Date: Jun 2008

- Join Date: Mar 2009

- Join Date: Jul 2008

- Join Date: Feb 2009

- Join Date: Apr 2009
Latest Articles
- Channel: Articles
ad_right_rmr
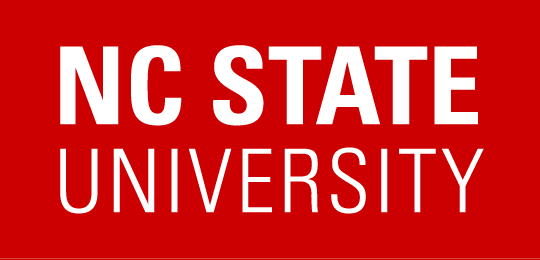
BioResources
- About the Journal
- Authors & Reviewers
- How to Self-Register
- Full Site Navigation
- Editorial Board
- Meet the Staff
- Editorial Policies
- General Instructions
- Ethics & Responsibilities
- Article Preparation
- Submission Instructions
- Acknowledgment of your Peer-Reviewing
- Writing Style Suggestions
- Reviewer Guidelines
- Back and Current Issues
- Scholarly Reviews
- Special Conference Collection Issues
- Competition Print Edition
- FRC: Pulp and Paper Fundamental Research Symposia Proceedings
- Paper Manufacturing Chemistry
- BioResources Early Career Investigator Award
- Distance Education: Online Masters Degree & Individual Courses
- Upcoming Conferences
- Hands-On Courses
- Affiliate Journal
A review of wood machining literature with a special focus on sawing
In this review, fundamental wood machining research is evaluated to determine the general cutting mechanics of simple, orthogonal, and oblique cutting tools. Simple tool force trends and chip formation characteristics are indentified here, along with the cause and effects of tool wear. In addition to this, specific methods of evaluating sawing processes have been investigated. These include the use of piezoelectric dynamometers to record tool forces and high speed photography to evaluate chip formation. Furthermore, regression analysis has been previously used to identify tool force trends with respect to both tooth geometry parameters and work-piece properties. This review has identified the original findings of previous research. This will allow for further original research to be conducted.
Full Article
A Review of Wood Machining Literature with a Special Focus on Sawing
Andrew Naylor,* and Phil Hackney
Keywords: Wood Machining; Tool Forces; Tool Wear; Sawing
Contact information: a- School of Computing, Engineering and Information Sciences, Ellison Building, Northumbria University, Newcastle Upon Tyne, NE1 8ST, United Kingdom
* Corresponding author: [email protected]
INTRODUCTION
Throughout history the handsaw has proven to be one of the most widely used hand tools. This dates back to the first flint saws used during the Neolithic revolution circa 9500 BC (Jones and Simons 1961). In subsequent eras the technology continued to advance through the bronze and iron ages. Applications of the hand saws widened through the Roman era, where they became increasingly used in construction and even as a method of execution (Suetonius-Tranquillus, AD 119). The closed handle handsaw that we recognize today has its origins at the turn of the 18 th century. Prior to this, saws with an open handle or “pistol grip” were the norm. The teeth were manually filed and set using a small hammer and anvil. In the developing world, where carpenters see their tools as an investment rather than a replaceable good, this method is still widely used. The saw teeth are re-set and filed when the edges become too worn for functional use, thus increasing the life of the saw. Since the latter part of the 20 th century, the developed world has opted for hardened saw teeth. This is achieved by inducing an electromagnetic field at the edge of the blade heating the steel and hence forcing martensitic transform-ation. This makes the saw teeth extremely resilient to tool wear, removing the need to re-sharpen. Additionally, grinding and setting are fully automated processes.
Research performed into optimum wood machining conditions (Eyma et al. 2004; Méausoone 2001) states that there are generally three types of factors that affect the cutting mechanics:
- Factors attributed to the machining process
- Factors associated with wood species/intrinsic properties
- The moisture content of the wood
Analysis of the wood cutting process in the published literature (Franz 1958; Kivimaa 1950; Koch 1964; McKenzie 1961) examines these three effects, with publications investigating defects in the wood grain such as knots (Axelsson 1994).
Wood has three planes of symmetry; axial, radial, and tangential. Corresponding to these planes of symmetry are the cutting directions by which machining processes can be described (Fig. 1). When referring to a machining direction, the established labeling system employs two numbers separated by a hyphen. The first number denotes the orientation of the cutting edge to the wood grain direction; the second number denotes the movement of the tool with respect to the grain direction. To illustrate this, the three main cutting directions are listed:
- 90°-90° – The axial plane or the wood end grain. Both the cutting edge and tool movement are perpendicular to the grain.
- 0°-90° – The radial and tangential planes, cutting across the grain. The cutting edge is parallel to the grain but the tool movement is perpendicular.
- 90°-0° – The longitudinal plane, cutting along the grain. The cutting edge is perpendicular to the grain but the tool movement is parallel.
Previous research into wood-cutting mechanics investigated machining parallel and perpendicular to the grain (Axelsson 1993, 1994; Franz 1955, 1958; Huang 1994; Koch 1964; McKenzie 1961; Woodson and Koch 1970). Additionally, more recent studies have investigated the effects of cutting across the grain at various angles with and against the annual growth rings (Costes et al. 2004; Goli et al. 2002b, 2003, 2005, 2009).
Contrary to wood machining, a significant volume of research has been performed in the area of metal cutting, the most fundamental of which describe it as a plastic deformation process of an isotropic material (Ernst 1938; Merchant 1944). Wood is a material that is both heterogeneous and anisotropic, making it very unpredictable during
Fig. 1. Wood machining directions
any machining process. On a macroscopic level, wood gains its non-uniform structure from its concentric annual growth rings composed of earlywood cells (formed during the darker, cooler spring months) and latewood cells (formed during the warmer, lighter summer months). These cells grow longitudinally through the trunk of the tree. Additionally, wood contains knots where limbs grow out from the trunk; these weaken wood as a material as they are poorly bonded to the surface which surrounds them.
THE PLAINING PROCESS
Orthogonal Plaining
Plaining is a process by which a knife edge removes a layer of material on the top surface of a work-piece. As there is clearly material removal in the form of chip or swarf, analysis of the chip formation is often used to characterize the process. Early research into the metal-cutting process by Ernst (1938), Merchant (1944), and Lee and Shaffer (1951) has established relationships between the cutting conditions and the deformed chip. These relationships have successfully explained the process as plastic deformation of an isotropic material. As wood is an anisotropic material, chip formation changes with respect to the machining direction.
The first comprehensive investigation into wood machining (Kivimaa 1950) investigated the effects of varying tool geometry and species factors for plaining operations. In experimental work evaluating the cutting action of the tool, the work-piece properties were not varied, standardizing on Finnish birch as the sole species. It was found that the main cutting force was inversely proportional to the sharpness of the tool, i.e. the sharper the tool, the lower the force. It also can be stated at this point that the thrust force is caused by contact between the rake face and the chip. Larger rake angles result in greater chip thickness hence lower thrust force. This is because the chip is not being compressed at the extreme cutting edge. Although it is observed that there is no significant effect of cutting velocity on the major cutting force, the orientation of the tool with respect to the grain does have a significant effect on the cutting forces. The highest cutting forces are observed to be in the 90°-90° direction (wood end grain), with the lowest cutting forces in the 90°-0° direction (cutting along the grain).
In other experimental work (Axelsson et al. 2003) the tool sharpness and rake angle remain constant for the testing of 21 different species of wood. Analysis of data found a linear trend between the density of the wood and the major cutting force. From this empirical data, a predictive model for cutting force was created.
For orthogonal wood cutting, extensive work into the chip formation produced through varied cutting conditions has been carried out by Franz (1955, 1958), McKenzie (1961), and Woodson and Koch (Koch 1964; Woodson and Koch 1970). The cutting tools used in the experiments represent a planing tool that removes material across the entire width of the work-piece. This set-up typically consists of the tool being attached to a strain gauge rosette (measuring cutting and thrust force components). Cutting along the grain gives three types of characterized chip (Fig. 2):
- Type I chip is caused by a large rake angle producing negative thrust forces (acting in a positive vertical direction relative to the work-piece). The wood fibres split ahead of the tool and finally fail due to bending. This type of chip is beneficial where quick removal of material is required.
- Type II chip is formed by a very sharp tool edge and a diagonal plane of shear. Excellent surface finish is achieved due to the continuous chip formation.
- Type III chip is caused by dull tool edges and very small or negative rake angles. It is also suggested that very large depths of cut may form this chip where there is too much contact with the blade surface. This type of chip causes a raised fuzzy grain where wood fibres protrude, hence a poor surface finish.
Further work done by Woodson and Koch (1970) cutting across the grain demonstrates that higher moisture contents increase the length of chip type II before failure. The forces observed in the latewood fibers are approximately double that of the earlywood fibers with a positive correlation between cutting force and moisture content. The same publication documents the effects of cutting across the grain in what is described as the veneer peeling process. This process uses high rake angles (approximately 70°) and small depth of cut (less than 1 mm) with a nosebar used to compress the cells before cutting to ensure that the veneer remains a single unbroken sheet. The chip is formed by an initial compaction of the wood fibres (3) followed by an ongoing shearing process (2) with some tensile failure also observed (1) (Fig. 3). This form of cutting results in higher forces and discontinuous chip compared to veneer peeling. Cutting forces for ealywood and latewood in this direction are the same.
McKenzie (1961) investigated the effects of cutting across the grain and discovered two distinct chip types (Fig. 4). Type I is typical for cutting wood with a very high moisture content and type II for low moisture content. The cutting mechanics for both conditions specify a tensile failure mode causing parallel gaps to propagate between the fibers; however, these gaps become larger with decreased moisture content. Cutting forces in this direction are strongly affected by cell type, moisture content, depth of cut, and rake angle, where the values of the cutting force for latewood are approximately three times the values for earlywood.
Further research (Goli et al . 2001a, 2002a,b, 2003, 2005, 2009) delves into the change in cutting mechanics when machining at different orientations with respect to the grain. The grain orientation that provides the highest forces and leaves behind the most protruded distorted grain is cutting in the 90°-90° direction (Goli et al. 2005). As previously discovered by Kivimaa (1950), cutting parallel to the grain provides the lowest cutting force values (Costes et al. 2004) with chip formation characteristic of the Franz type 1 chip. Furthermore cutting at angles with the annual growth rings produces smaller cutting forces and less distorted grain compared to cutting against the growth rings (Goli et al. 2009).
Analysis of the formation of the surface finish also has been investigated (Goli et al. 2001a,b, 2002a; Goli and Uzielli 2004). Surface roughness measurements using a perthometer (optical 3D roughness measurement) and a profileometer (surface roughness stylus) were taken to quantify the surface finish of the woods. Machining in the standard machine directions (90°-0°, 0°-90°, 90°-90°) provides results concurrent to the respective chip formation types of Franz, McKenzie, and Koch.
Typically cutting along the grain provides a better surface finish than cutting across the grain, where the effects of moisture content, rake angle, depth of cut, and edge sharpness all affect the surface finish in the same way as previously investigated in the fundamental studies (Franz 1958; Koch 1964; McKenzie 1961). In reflection, when cutting at angles with and against the annual growth rings it is established that the surface
Fig. 2. McKenzie chip types, along the grain (McKenzie 1961) with permission from the University of Michigan
Fig. 3. Veneer Peeling, Across the Grain (Woodson and Koch, 1970) with permission from the U.S Department of Agriculture
Fig. 4. Machining the wood end grain (Woodson and Koch 1970) with permission from the U.S Department of Agriculture
roughness is significantly larger when cutting at angles against the growth rings as opposed to with the growth rings. This has been verified by both surface roughness measurement techniques.
Oblique Plaining
In orthogonal cutting, it has been known for tools with large rake angles (>25°) to produce negative thrust forces (acting in a positive vertical direction relative to the work-piece), although this observation is usually attributed to a larger depth of cut (Franz 1958; Woodson and Koch 1970). For oblique cutting parallel to the grain, the cutting and thrust forces decrease as the oblique edge angle increases (Jin and Cai 1996, 1997). As observed with orthogonal cutting, it is also recognized that negative thrust forces can also occur when wood is machined using oblique tools (Jin and Cai 1997). This occurs for the same cutting conditions as with oblique cutting (large rake angles and depths of cut) for oblique edge angles over 30°. It is recognized that the negative thrust forces cause the propagation of longitudinal cracks in front of the knife edge during cutting (Franz 1958; Stewart 1971, 1986). By decreasing the rake angle and depth of cut, the magnitude of the negative thrust force becomes lower and eventually changes from negative to positive. This reduces the roughness of the surface caused by the chip splitting ahead of the tool, instead leaving behind a slight fuzzy grain (Fernando 2007).
It has been observed that fibers have been pulled out or up-rooted from the work-piece when cutting perpendicular to the grain (de Moura and Herandez, 2006). After further investigation, this phenomenon has been explained as being caused by lateral forces exerted on the work-piece by the oblique tool (de Moura 2006). This causes greater observed surface roughness when compared to that of surfaces that have been machined using orthogonal tools. Furthermore, an increase in the oblique edge angle causes more fibers to be pulled out, and hence, an increase in the surface roughness of the work-piece.
A study investigating cutting with extreme oblique angles (Fischer et al. 2011) states that cutting with very large oblique angles (45° to normal and above) provides a much better surface finish when compared with orthogonal cutting. This is a result of the time delayed edge engagement and an increased cutting edge contact with the work-piece. This effect also results in lower forces acting on the tool, which in turn, reduces tool wear.
Causes of Tool Wear
In a comprehensive review on wood cutting tool wear (Klamecki 1979), it was concluded that the abrasive wear plays the largest role in the edge recession of tools. From recent studies (Bailey et al. 1983; Bayoumi et al. 1983, 1985; Mohan and Klamecki 1982; Scholl and Clayton 1987) it is evident that cemented carbide tools are extremely sensitive to corrosive wear, suggesting that high speed steel is a better corrosion resistant alternative. Having said this, corrosive wear has been known to significantly affect high speed steel when cutting green wood (McKenzie and Hillis 1965; Mohan and Klamecki 1982). This is due to much higher moisture content values as well as naturally occurring acids and phenolic compounds.
The presence of silica and other mineral entrapments is known to play a role in corrosive wear (Müller et al. 2011); however, further study has shown that the silica residue found within the wood cell walls plays a very small role. Instead, contamination with coarse silica during the harvesting and storage of timber/lumber is seen to contribute in a larger way to corrosion. It is also suggested that the mechanical properties of tool material at the tip, or even coating materials, can be altered by corrosive wear (Gauvent et al. 2006). This can allow the effects of abrasive wear to become more prominent or even result in brittle failure.
Effects of Tool Wear on Cutting Mechanics
Kivimaa was the first to notice an increase in cutting forces due to the dulling of the cutting edge (Kivimaa 1950). It has been documented that all of the tool forces (cutting, thrust, and side force) are sensitive to tool wear (McKenzie and Crowling 1969) with side force said to be the most affected by wear.
Further research documents a rise in the cutting force with respect to continuous length of cut (Pahlitzsch and Jostmeier 1965). Cutting force vs . length of cut has a similar trend to edge recession vs . length of cut (Bartz and Breier 1969); both exhibit a rapid exponential rise which then levels off. A more detailed study offers an explanation of how tool forces increase due to wear (Bier and Hanicke 1963), describing the wear and cutting force increase over a continuous length of cut in three stages:
- An exponential increase in cutting force which plateaus. This is caused by the initial blunting of the tool.
- A linear increase with small gradient. The tool is now blunt and this trend is caused by edge rounding where the radius gradually increases.
- An exponential increase and then failure. When critical edge radius has been reached, the clearance face starts to wear, eventually causing the failure of the tooth.
Using this knowledge, research into a predictive model for tool wear was conducted (McKenzie and Cowling 1971), revealing a linear relationship between the main cutting force and the square root of the edge radius. It was also noted that the relationship between the main cutting force and wear on the clearance face was approximately linear.
When compared to the machining of wood using sharp tools, it is widely accepted that worn edges generally lead to a more compressed chip formation and to a work-piece with a fuzzier, protruded grain (Franz 1958; Kivimaa 1950; Koch 1964; McKenzie 1961; Woodson and Koch, 1970). This is true for all of the major machining directions.
MECHANICS OF WOOD SAWING
Tooth and Blade Geometry
Nomenclature for tooth geometry is detailed by British Standards (British-Standards-Institute 1999). The geometry of the saw teeth can be varied to suit the end use of the saw. Rip saws have unbeveled cutting edges and small rake angles to remove material parallel to the grain. Cross cutting saws, however, need negative rake angles and sharp beveled edges to sever the wood fibers perpendicular to the grain. Compound saw teeth have more than one cutting edge so that they can generally perform well cutting both parallel and perpendicular to the grain. Fleam teeth are usually seen on bow-saws for cutting green wood, where the rake and flank angles are the same to allow cutting in both directions.
The thicknesses for the blade raw material is also specified (British Standards Institute 1999) with the prospective user in mind. The teeth should be alternately set on either side of the blade. Approximately two-thirds of each tooth measured from the tip shall be set, and the method of setting shall be such that the remainder of the tooth will remain undeformed. The set width of the left and right set teeth should be equal and shall be expressed as a ratio of the thickness of the blade. For cross cutting and general use saws, this should be no less than one-fifth and no more than two-fifths the thickness of the blade on each side of the tooth. For rip saws no less than one-quarter and no more than one-half the thickness of the blade should be on each side. Saw blades use a variety of different set patterns depending upon the wood grain direction and the driving method (either manual or machine driven). Hands saws use a variation of the raker set.
During rip sawing, the wood fibers are initially compressed and then sheared (Lundstrum 1985). Post shearing the compressed fibers adjacent to the shearing edge causes them to spring back nearly to their original position. For this reason, the set of the saw must be large enough to prevent the sprung back fibers from making contact with the body of the saw. Softwoods produce fuzzy grain leaving the kerf not as cleanly cut as hardwoods, hence sawmills processing mainly softwoods apply greater set widths to the saw teeth.
Increased gullet size limits the number of teeth per unit of length of blade ( i.e. decreases pitch). The feed velocity during sawing must be reduced for decreased pitch saws to prevent an excessive depth of cut per tooth, known as over-biting. Conversely, small gullet sizes tend to increase the tooth pitch (Lundstrum 1985). In band sawing, the cutting velocity needs to be reduced, as sawdust can become compressed within the reduced gullet. The reciprocating cutting stroke does not provide enough of a respite for the sawdust to be removed from the kerf. In order to overcome these problems, it is recommended that the area of the gullet should be approximately the same as the area of the tooth. Furthermore, the bite of the tooth should be approximately one third of set width. This is to ensure that the smallest of the sawdust particles will not be any larger than the set width and hence will be completely swept out of the machined groove by the set teeth, whereby reducing lateral cutting forces.
Using a blade with uniform tooth pitch results in the set and unset teeth having the same bite profile, and hence, the same principle cutting and thrust forces (Andersson et al. 2001). Using a differential pitch ( i.e . the gullet size of the set teeth is smaller than that of the neutral teeth) means that the set teeth have only a fraction of the bite of the neutral teeth. This results in the role of the set teeth to be that of removing swarf from the kerf rather than actually performing any of the cutting action. Reduced lateral cutting forces and wear are observed for the set teeth.
Beveling the outer lateral edge of the set teeth reduces the bite profile and improves the surface quality through less damage to the fibers (creating cleaner cuts) (McKenzie 2000). Beveling the inner lateral edge of the set teeth can increase the bite profile up to two fold. This in turn can cause an increase in the cutting forces and a reduction in observed surface quality. Overall, beveled teeth reduce the cutting forces, hence improving cutting performance. Uniform tooth pitch and geometry results in high surface quality and accurate sawn dimensions. The number of teeth/points per 25 mm shall be in accordance to British Standards (British Standards Institute 1999).
Tool Forces
Cutting forces for single saw tooth tests are generally measured and recorded using one or more piezoelectric transducers. A piezoelectric transducer is a quartz crystal that generates an electric charge in response to an applied load. They can be calibrated to measure exact forces with very small margins of error. The simplest of data acquisition systems consist of a single transducer connected to a single saw tooth, aligned to measure the force in the direction of cutting (Ratnasingam and Scholz 2011). Where three transducers are simultaneously used to measure forces in the X, Y, and Z directions, they are collectively referred to as a force dynamometer. Dynamometers are generally set up to constrain the work-piece (wood), and thus, record the resultant forces applied by the single tooth. The transducers aligned in the X, Y, and Z directions are set up to record cutting, lateral, and thrust forces. Usually the X and Y directions record cutting or later forces and the Z direction records the thrust force, although this is completely dependent on orientation of the tool path with respect to the work-piece. This method has also been used for a constrained tooth with the work-piece attached to a moving feed bed (Loehnertz and Cooz 1998). Regarding wood cutting mechanics, the tool forces are the most important measured response attributed to the tooth for a repeatable work-piece ( i.e . if the work-piece stays the same but the tooth changes). This can either be in the pure, unaltered force form (Axelsson 1994; Axelsson et al. 1993; Cristóvão et al. 2011; Ekevad and Marklund, 2011; Lhate et al. 2011; Porankiewicz et al. 2011), or as a specific force value with respect to depth of cut or volume of material removed (Cooz and Meyer 2006; Ko and Kim 1999; Orlowski et al. 2011; Orlowski and Palubicki 2009).
For band-sawing operations, machining across the wood fiber direction positive rake angles of 15°-30° are used for high power driven processes (Lundstrum 1985). The tooth is allowed to “hook” or “barb” onto the work-piece to allow for quick machining. These rake angles would be far too large for hand sawing operations, as the forces required for cutting would be too large to perform manually. Clearance angles are varied (between 6° and 16°) for varying feed velocities. This is to prevent the flank of the tooth from making unnecessary contact with the work-piece during sawing. This will decrease the overall friction hence reducing thrust forces. Research into the effects of changing the rake angle of band-saw teeth when machining the wood end grain (the 90°-90° direction), has yielded interesting results with regard to the force in the direction of cutting (Vazquez-Cooz and Meyer 2006). Three teeth with 25°, 30°, and 35° rake angles were examined. It was found that the largest rake angle produced the lowest cutting forces and the smallest rake angle produced the largest cutting forces.
A comparison of the performance between individually set teeth and swaged teeth show a reduction in lateral forces for the swaged teeth (Okai et al. 2006). Furthermore a quadratic relationship has been established between the variation (standard deviation) of lateral forces and side clearance. Through analysis of the cutting and thrust and side forces, a mechanistic cutting force model could be developed evaluating the individual roles of the set and neutral teeth (Ko and Kim 1999). It was found that the unset teeth contribute to the majority of the cutting and thrust force, and the set teeth cause the majority of the lateral forces measured.
Regression analysis has been frequently used to develop predictive cutting force models for simple rip tooth geometries (Axelsson et al. 1993; Cristóvão et al. 2011; Lhate et al. 2011; Porankiewicz et al. 2011) where a linear decrease in the cutting force for an increased positive rake angle (10° to 30°) has been observed (Axelsson et al. 1993). At the same time a linear increase in cutting forces is observed for increased edge radii (5 to 20 m). This shows that in the ripping scenario, sharp teeth with small rake angles provide the lowest cutting forces. Factors that are considered to have a significant effect on the major cutting force are depth of cut, rake angle, and edge radius. Cutting force increases with depth of cut, increases with edge radius, and decreases with rake angle. Furthermore, cutting the wood end grain yields the largest cutting forces with the lowest cutting forces observed machining along the fiber direction. Work-piece parameters have been used as predictors in statistical modeling to describe force trends. The most often used parameters are density, moisture content, and grain direction. In addition to this, numerical coefficients have previously been determined to discretely quantify wood species (Porankiewicz et al. 2011). Adding additional moisture to a piece of timber leads to swelling; likewise, removing moisture from timber leads to shrinkage. As a result of this change in volume, the density did not dramatically change with respect to moisture content. Higher tool forces are observed when cutting wood species of greater density (Cristóvão et al. 2011; Lhate et al. 2011). It is generally accepted that tool forces decrease with increased work-piece moisture content, although an exception to this rule has been found for frozen wood specimen (Porankiewicz et al. 2011). Increased moisture content for frozen wood leads to an increase in tool forces. Furthermore, work-pieces at decreasing sub-zero temperatures lead to a significantly higher tool forces.
An investigation into lateral tool forces was conducted for sharp beveled tooth geometries (Ekevad and Marklund 2011). Very sharp teeth yielded insignificant lateral forces in all machining directions. Lateral forces only became noticeable when the teeth became worn or damaged. In this instance, high lateral forces were observed machining both the wood end grain (90°-90° direction) and the across the fiber direction (0°-90° direction), with lower lateral forces machining along the grain (90°-0° direction).
Evidence from fundamental literature suggests that cutting velocity has negligible effect on the forces acting on the tool. This is for the ranges of 0.2 m/s to 6.3 m/s along the grain (McKenzie 1961) and 2.5 m/s to 50 m/s across the grain (Kivimaa 1950).
Chip and Surface Formation
Research into the effects of varied rake angle band-saw teeth on the on surface formation was conducted (Vazquez-Cooz and Meyer, 2006). This was performed machining in the 90°-90° direction (wood end grain). Three teeth with 25°, 30°, and 35° rake angles were examined. Initially, it appeared that the 25° and 35° rake angles produced a smooth work-piece finish after machining, whilst the 30° rake angle produced a rough finish with fuzzy grain. Microscope images showed that the 25° rake angle only appeared smooth, when in fact the machining caused fuzzy grain which was then compressed due to the comparably lower rake angle of the tooth.
A high speed camera has been previously utilized to capture footage of the cutting process for single circular saw teeth (Ekevad et al. 2011). The camera was set up to record 40,000 frames per second for a circular saw rotating at a speed of 3250 RPM. Green, dry, and frozen wood were machined in the 90°-0° direction (along the grain) using single rip teeth with rake angles of 0°, 10°, 20°, and 30°. The only observed continuous chip formation was for green wood, with the dry and frozen work-pieces yielded smaller broken wood particles. Furthermore the footage was able to evaluate the action of the gullet. Reduced rake angle leads to a reduction in gullet volume; still images from this footage show a build up of wood particles for the larger rake angles (lower gullet volume), as the wood chips/particles are prevented from curling past the much smaller root radii. This results in an impaction of wood particles in the gullet, which impedes removal of the material from the kerf.
CONCLUSIONS
- The fundamental mechanics of wood machining have been well established through the published literature. These are illustrated here by the Franz, McKenzie, Woodson, and Koch chip formation types.
- The primary mode of tool wear is abrasion. The worn tools cause excessive compaction of fibers during cutting, resulting in a fuzzy chip and respective poor surface finish to the work-piece.
- Recorded tool forces and observed chip formation are the most common methods of evaluating the cutting mechanics of saw-teeth. Predictive force models have been developed using both tooth geometry parameters and work-piece (wood) properties.
- The original findings from previous research have been identified. This will allow for further research to be conducted in the field of wood-sawing in order to investigate novel, previously unexplored areas. This includes (but is not limited to) the influence of geometric parameters associated with the saw-tooth on tool forces.
Andersson, C., Andersson, M. T., and Ståhl, J. E. (2001). “Bandsawing. Part I: Cutting force model including effects of positional errors, tool dynamics and wear,” Int. J. Mach. Tool Manuf. 41(2), 227-236.
Axelsson, B. (1994). “Lateral cutting force during machining of wood due to momentary disturbances in the wood structure and degree of wear of the cutting tool,” Eur. J. Wood Wood Prod. 52(3), 198-204.
Axelsson, B., Lundberg, Å., and Grönlund, J. (1993). “Studies of the main cutting force at and near a cutting edge,” Eur. J. Wood Wood Prod. 51(2), 43-48.
Bailey, J. A., Bayoumi, A. E., and Stewart, J. S. (1983). “Wear of some cemented tungsten carbide tools in machining oak,” Wear 85(1), 69-79.
Bartz, E., and Breier, H. (1969). “ Kurzverfahren zur Prüfung der Verschleißwirkung und der Zerspanbarkeit von Holz und Holzwerkstoffen,” Holz Roh Werkst . 27(4), 148-152.
Bayoumi, A. E., Bailey, J. A., and Stewart, J. S. (1985). “Comparison of the wear resistance of selected steels and cemented carbide cutting tool materials in machining wood,” Wear 105(2), 133-144.
Bayoumi, A. E., Bailey, J. A., and Stewart, J. S. (1983). “Comparison of the wear resistance of various grades of cemented carbides that may find application in wood machining,” Wear 89(2), 185-200.
Bier, H., and Hanicke, P. (1963). “Die spezifische Schnittkraft als Funktion der Schneidenabstumpfung beim Fräsen,” Holztechnologie 4(2), 158-162.
British-Standards-Institute. (1999). BS 3159-1: Woodworking saws for hand use – Part 1: Specification for hand saws. London.
Cooz, I., and Meyer, R.W. (2006). “Cutting forces for tension and normal wood of maple,” Forest Prod. J. 56(4), 26-34.
Costes, J.-P., Ko, P.L., Ji, T., Decès-Petit, C., and Altintas, Y. (2004). “Orthogonal cutting mechanics of maple: Modeling a solid wood-cutting process,” J. Wood Sci. 50(1), 28-34.
Cristóvão, L., Broman, O., Grönlund, A., Ekevad, M., and Sitoe, R. (2011). “Main cutting force for two species of tropical wood,” In: 20 th International Wood Machining Seminar , Skellefteå, Sweden.
de Moura, L., and Herandez, R. (2006). “Characteristics of sugar maple wood surfaces produced by helical planing,” Wood Fiber Sci. 38(1), 166-178.
Ekevad, M., and Marklund, B. (2011). “Lateral cutting forces for different tooth geometreis and cutting directions,” In: 20 th International Wood Machining Seminar, Skellefteå, Sweden.
Ekevad, M., Marklund, B., and Gren, P. (2011). “Wood chip formation in circular saw blades studied by high speed photography,” In: 20 th International Wood Machining Seminar, Skellefteå, Sweden.
Ernst, H. (1938). “Physics of metal cutting,” In: National Metal Congress – American Society for Metals , Detroit.
Eyma, F., Méausoone, P.-J., and Martin, P. (2004). “Strains and cutting forces involved in the solid wood rotating cutting process,” J. Mater. Process. Technol. 148(2), 220-225.
Fischer, R., Gottlöber, C., Oertel, M., Wagenführ, A., and Darmawan, W. (2011). “Effects of wood cutting with extreme inclined cutting edges,” In: 20 th International Wood Machining Seminar, Skellefteå, Sweden.
Franz, N. C. (1955). “An analysis of chip formation in wood machining,” Forest Prod. J. 10(3), 332-336.
Franz, N. C. (1958). An Analysis of the Wood-Cutting Process . University of Michigan Press, Ann Arbor, MI.
Gauvent, M., Méausoone, P. J., and Brenot, P. (2006). “Corrosion of materials used as cutting tools of wood,” Wear 261(9), 1051-1055.
Goli, G., Bleron, L., Marchal, R., Uzielli, L., and Negri, M. (2002a). “Formation and quality of wood surfaces processed at various grain angles: Douglas-fir and oak,” In: Wood Structure and Properties, Arbora Publisher, Zvolen, Slovakia , pp 91-98.
Goli, G., Bleron, L., Marchal, R., Uzielli, L., and Negri, M. (2002b). “Measurment of cutting forces in routing wood at varous grain angles: Initial results with Douglas-fir,” In: Wood Science and Engineering in the Third Millennium , Transilvania University.
Goli, G., Fioravanti, M., Marchal, R., Uzielli, L., and Busoni, S. (2009). “Up-milling and down-milling wood with different grain orientations – The cutting forces behaviour,” Eur. J. Wood Wood Prod. 68(4), 385-395.
Goli, G., Fioravanti, M., Sodini, N., Uzielli, L., and Del Taglia, A. (2005). “Wood processing: A contribute to the interpretation of surface origin according to grain orientation,” In: COST Action E35 , Rosenheim, Germany.
Goli, G., Marchal, R., and Negri, M. (2001a). “Industrial machining of Douglas fir with varous tools and materials,” In: Proceedings of the 15 th International Wood Machining Seminar ,Los Angeles, California.
Goli, G., Marchal, R., Negri, M., and Costes, J.-P. (2001b). “Surface quality: Comparison among visual grading and 3D roughness measurements,”In: Proceedings of the 15 th International Wood Machining Seminar , Los Angleles, California.
Goli, G., Marchal, R., Uzielli, L., and Negri, M. (2003). “Measuring cutting forces in routing wood at various grain angles – Study and comparison between up- and down- milling techniques, processing Douglas fir and oak,” In: 16 th International Wood Machining Seminar , Matsue, Japan.
Goli, G., and Uzielli, L. (2004). “Mechanisms of wood surface formation and resulting final condition after planing,” In: Proceedings of the 2nd International Symposium on Wood Machining – Properties of Wood and Wood Composites related to Machining . Vienna, Austria.
Huang, Y. (1994). “Cutting force components in orthogonal cutting parallel to the grain (90-0) 1 – Effects of the rake angles,” Mokuzai Gakkaishi 40(10), 1134-1140.
Jin, W., and Cai, L. (1996). “Study and analysis on cutting forces of oblique cutting of wood,” Holz Roh Werkst . 54(4), 283-286.
Jin, W., and Cai, L. (1997). “Study on the normal component force in oblique cutting of wood,” Holz Roh Werkst . 55(2-4), 118-120.
Jones, P. D. A., and Simons, E. N. (1961). Story of the Saw , Spear and Jackson, Ltd, Sheffield, England.
Kivimaa, E. (1950). “Cutting force in woodworking,” Vol. 18, VTT Julkaisu, Helsinki, Finland, 101 pp.
Klamecki, B. E. (1979). “A review of wood cutting tool literature,” Holz Roh Werkst. 37(7), 265-276.
Ko, T. J., and Kim, H. S. (1999). “Mechanistic cutting force model in band sawing,” Int. J. Mach. Tools Manuf. 39(8), 1185-1197.
Koch, P. (1964). Wood Machining Process , Ronald Press Co, New York.
Lee, E. H., and Shaffer, B. W. (1951). “The theory of plasticity applied to a problem of machining,” J. Appl. Mech. 18, 405-413.
Lhate, I., Cristóvão, L., Ekevad, M., and Sitoe, R. (2011). “Cutting forces for wood of lesser used speceis from Mozambique,” In: 20 th International Wood Machining Seminar , Skellefteå, Sweden.
Loehnertz, S., and Cooz, I. (1998). “Sawtooth forces in cutting tropical hardwoods native to South America,” USDA Forest Services, Forest Products Labortory Research Paper FPL – RP – 567, 16 pp.
Lundstrum, S. J. (1985). Balanced Saw Performance , Un USDA Forest Services, Forest Products Labortory Technical Report No. 12, 19 pp.
McKenzie, W. M. (1961). Fundamental Analysis of the Wood Cutting Process , Department of Wood Technology, University of Michigan, Ann Arbor, MI.
McKenzie, W. M. (2000). “Effects of bevelling the teeth of rip saws,” Wood Sci. Technol. 34(2), 125-133.
McKenzie, W. M., and Cowling, R. L. (1969). “The early stages of edge wear in cutting wood,” In: IUFRO – Section 41 Meeting .
McKenzie, W. M., and Cowling, R. L. (1971). “A factorial experiment in transverse-plane (90-90) cutting of wood: Part 1 – Cutting force and edge wear,” Wood Fiber Sci. 9(3), 204-213.
McKenzie, W. M., and Hillis, W. E. (1965). “Evidence of chemical acceleration of wear in cutting plant materials,” Wear 8(3), 238-243.
Méausoone, P. J. (2001). “Choice of optimal cutting conditions in wood machining using the coupled tool–material method,” In: Proceedings of the 15 th International Wood Machining Seminar , pp. 37-47.
Merchant, E. (1944). “Basic mechanics of the metal-cutting process,” J. Appl Mech. 66, 168-175.
Mohan, G. D., and Klamecki, B. E. (1982). “The susceptibility of wood-cutting tools to corrosive wear,” Wear 74(1), 85-92.
Müller, C., Deetz, R., Schwarz, U., and Thole, V. (2011). “Agricultural residues in panel production – Impact of ash and silica content,” In: 20 th Internationa Wood Machining Seminar , Skellefteå, Sweden.
Okai, R., Mitchual, S. J., and Frimpong-Mensah, K. (2006). “Optimisation techniques for minimising saw teeth deflection and lumber thickness variation,” Precis. Eng. 30(1), 39-46.
Orlowski, K., Ochrymiuk, T., and Atkins, A. (2011). “Applications of fracture mechanics for energetic effects predictions while wood sawing,” In: 20 th International Wood Machining Seminar , Skellefteå, Sweden.
Orlowski, K., and Palubicki, B. (2009). “Recent progress in research on the cutting processes of wood,” Holzforschung 63(2), 181-185.
Pahlitzsch, G., and Jostmeier, H. (1965). “Beobachtugen uber das – Abstumphfungsver-halten beim Fasen von Schichtstoff-Verbundplatten,” Holz Roh Werkst . 23(4), 121-125.
Porankiewicz, B., Axelsson, B., Grönlund, A., and Marklund, B. (2011). “Main and normal cutting forces by machining wood of Pinus sylvestris ,” BioResources 6(4), 3687-3713.
Ratnasingam, J., and Scholz, F. (2011). “Optimising the cutting of tension wood in rubberwood: An economic and quality perspective,” In: 20 th International Wood Machining Seminar , Skellefteå, Sweden.
Scholl, M., and Clayton, P. (1987). “Wear behaviour of wood cutting edges,” Wear 120(2), 221-232.
Stewart, H. A. (1971). “Chip formation when orthogonally cutting wood against the grain,” Wood Sci. 3(4), 193-203.
Stewart, H. A. (1986). “Fixed knife-pressure bar system for surfacing dry wood,” Forest Prod. J. 36(6), 52-56.
Suetonius-Tranquillus, C., AD 119, Caligula , Chapter 27.
Vazquez-Cooz, I., and Meyer, R. W. (2006). “Cutting forces for tension and normal wood of maple,” Forest Prod. J. 56(4), 26-34.
Woodson, G. E., and Koch, P. (1970). Tool Forces and Chip Formation In Orthogonal Cutting Of Loblolly Pine , USDA Forest Services, Southern Forest Experimental Station Research PaperSO-52, 29 pp.
Article submitted: February 15, 2013; Peer review completed: March 25, 2013; Revised version received and accepted: April 5, 2013; Published: April 9, 2013.
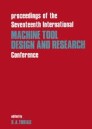
Proceedings of the Seventeenth International Machine Tool Design and Research Conference pp 103–116 Cite as
A Comprehensive Literature Survey of Chip Control in the Turning Process
- B. Worthington 2
26 Accesses
In the turning process, when a continuous chip is being produced, the increasing problems of adequate chip control resulting from the application of higher cutting speeds, are discussed.
Although various techniques for controlling the chip have been developed, the most common method is to use obstruction or groove type chip forming devices. The chip breaking action of these devices is examined under four headings and the previously published work and current commercial developments are critically appraised.
This is a preview of subscription content, log in via an institution .
Unable to display preview. Download preview PDF.
STABLER, G.V. ‘The Fundamental Geometry of the Cutting Process’, Proc.I.Mech.E. 165, 14, 1951
Article Google Scholar
MERCHANT, M.E. ‘Ten Years Ahead — What’s in it for Metal Cutting’, American Machinist , May 18, 1959.
Google Scholar
KLOPSTOCK, H. ‘Berichte Des Versuchfeldes Fur Werkzeugmaschinen an der Technische Hochschule Berlin’, V.8 , 1926
NAKAYAMA, K. J.Soc. Prec. Mech. Japan, V. 26, No. 8, 1960, p. 482
SPAANS, C. and VAN GEEL, P.F.H.J. ‘Break mechanisms in cutting with a chip breaker’, Annals of the C.I.R.P. V. 18 , pp. 87–92, 1970.
HAHN, R.S. ‘Some observations on chip curl in the metal cutting process, under orthogonal cutting conditions’, Trans.A.S.M.E. V. 75 , 1953, pp. 581–590.
RUBENSTEIN, C. and DAWE, C.C. ‘Analysis of chip curvature’, 10th M.T.D.R. Conference, Sept. 1969 .
BARANOV, V.N., ZAKHAROV, Yu.E., MOISEEV, V.E. and BEZRUKOV, I.M. ‘Chip breaking methods in turning ductile metals’, Machines and Tooling , V. 34, No. 1, 1963, pp 16–10.
IOFFE, N.M. ‘Dynamic chipbreaker’, Stanki i Instrument, No. 11 , 1949, pp. 18–20.
KONDRATOV, A.S. ‘The results of tests with a dynamic chip breaker’, Stanki i Instrument , V. 21, No. 4, April 1950, pp. 21–22.
KISELEV, G.I. ‘Results of a study of the performance of a dynamic chip breaker’, Stanki i Instrument, V. 21 , No. 4, April 28, 1951.
STABLER, G.V. Proc. 5th Int. Mach.Tool Des. Res. Conf. 1964 .
OKUSHIMA, K. and MINATO, K. ‘On the behaviour of the chip in steel cutting’, J.S.M.E. V. 2 , No. 5, 1959, pp. 58–64.
ZOREV, N.N. ‘Metal Cutting Mechanics’, Pergamon Press, 1966 , p. 360 etc.
HENRIKSEN, E.K. ‘Chip breaking — a study of three dimensional chip flow’, A.S.M.E. paper No. 53–5–9 .
NAKAYAMA, K. ‘A study of the chip breaker’, J.S.M.E. V. 5, No. 17 , 1962, pp. 142–150.
TRIM, A.R. and BOOTHR0YD, G. ‘Action of the obstruction type chip former’, Int. J. Prod. Res. (1968) V. 6, No. 3.
OKUSHIMA, K., HOSHI,T. and FUJINAWA, T. ‘On the behaviour of the chip in steel cutting — the case of the parallel type chip breaker’, J.S.M.E. V. 5 , No. 17, 1962, pp. 142–150.
SUBRAMANIAN, T.L. and BHATTACHARRYA, A. ‘Mechanics of chip breakers’, Instn. Engrs. (India) V. 46 , pt. ME2, Nov. 1965 pp. 56–r.
LUTOV, V.M. ‘Selecting the optimum size of chip breaking grooves’, Machines and Tooling, V. 33 , No. 7, 1962, pp. 27–30.
TAKEYAMA, H., SEKIGUCHI, H. and TAKADA, K. ‘One solution for chip hazard in turning’, Seimitsu Kikai 1970 , 36 (2) 150–156.
WORTHINGTON, B. ‘The effect of rake face configuration on the curvature of the chip in metal cutting’, Int. J. Mach. Tool Des. Res. Vol. 15 1975, pp. 223–239.
SCHALLBROCH, H. ‘Machinability testing methods for light alloys’, Z. Aluminium, V. 19 , 1937, p. 157.
NAKAYAMA, K. ‘Mechanical properties of chips produced in metal cutting’, A.S.M.E. Proc. Sept. 1963, pp. 58–64.
TAKEYAMA, H., MIYASAKI, K. ‘A Study of chip control in machine tool operation’, Seimitsu Kikai 1970 35 (11) 700–705.
WORTHINGTON, B. ‘The operation and performance of a groove type chip forming device’, Int. J. Prod. Res.
SUBRAMANIAN, T.L. and BHATTACHARRYA, A. ‘Mechanics of chip breakers’, Int. J. Prod. Res. V. 4 , No. 1, 1965, pp. 37–49.
PROSKURYAKOV, Yu.G., PERTOV, V.N. and FEDOROV, G.A. ‘Chip breaking in the machining of steel’, Machines and Tooling, V. 33 , No. 7, 1962, p. 26–27.
NODEL’MAN, M.O. ‘Cutting tools with fine chip breaker grooves’, Machines and Tooling, V. 33 , No. 12, 1962, p. 39–40.
NODEL’MAN, M.O. ‘Effect of wear on chip-breaker-grooved tools’, Russian Eng. Journal, V. 52 , No. 8, 1972, p. 66–67.
SKURATOV ‘New type of chip breaking step’, Machines and Tooling V. 33 , No. 1, 1962.
IGOSHIN, V.V. ‘Tools with chip-curling grooves’, Machines and Tooling, V. 36 , No. 12, 1965, p. 37–38.
WORTHINGTON, B. ‘Surface integrity, cutting forces and chip formation when machining with double rake angle tools’, Int. J. Mach. Des. Res. Vol. 14, 1974, pp 279–295.
DZANASHVILI, G.P. and KHARCHEVENIKOV, N.E. ‘Diamond grinding chip breaker grooves in tools’, Machines and Tooling, V. 36 , No. 1, 1965, p. 46–47.
LUNDGREN, E. ‘Cutting tool inserts with sintered chip breakers’, Machinery and Production Engineering, 2nd May 1973 , p. 572–575.
Download references
Author information
Authors and affiliations.
Department of Mechanical Engineering, The City University, UK
B. Worthington
You can also search for this author in PubMed Google Scholar
Editor information
Editors and affiliations.
Department of Mechanical Engineering, University of Birmingham, UK
S. A. Tobias ( Chance Professor and Head of Department ) ( Chance Professor and Head of Department )
Copyright information
© 1977 The Department of Mechanical Engineering, University of Birmingham
About this chapter
Cite this chapter.
Worthington, B. (1977). A Comprehensive Literature Survey of Chip Control in the Turning Process. In: Tobias, S.A. (eds) Proceedings of the Seventeenth International Machine Tool Design and Research Conference. Palgrave, London. https://doi.org/10.1007/978-1-349-81484-8_13
Download citation
DOI : https://doi.org/10.1007/978-1-349-81484-8_13
Publisher Name : Palgrave, London
Print ISBN : 978-1-349-81486-2
Online ISBN : 978-1-349-81484-8
eBook Packages : Palgrave Social & Cultural Studies Collection Social Sciences (R0)
Share this chapter
Anyone you share the following link with will be able to read this content:
Sorry, a shareable link is not currently available for this article.
Provided by the Springer Nature SharedIt content-sharing initiative
- Publish with us
Policies and ethics
- Find a journal
- Track your research
Accessibility Links
- Skip to content
- Skip to search IOPscience
- Skip to Journals list
- Accessibility help
- Accessibility Help
Click here to close this panel.

As a society-owned publisher with a legacy of serving scientific communities, we are committed to offering a home to all scientifically valid and rigorously reviewed research. In doing so, we aim to accelerate the dissemination of scientific knowledge and the advancement of scholarly communications to benefit all.
Engineering Research Express supports this mission and actively demonstrates our core values of inclusive publishing and trusted science . To find out more about these values and how they can help you publish your next paper with us, visit our journal scope .
Purpose-led Publishing is a coalition of three not-for-profit publishers in the field of physical sciences: AIP Publishing, the American Physical Society and IOP Publishing.
Together, as publishers that will always put purpose above profit, we have defined a set of industry standards that underpin high-quality, ethical scholarly communications.
We are proudly declaring that science is our only shareholder.
A review on cutting fluids used in machining processes
Jasjeevan Singh 1 , Simranpreet Singh Gill 2 , Manu Dogra 3 and Rupinder Singh 4
Published 18 March 2021 • © 2021 IOP Publishing Ltd Engineering Research Express , Volume 3 , Number 1 Citation Jasjeevan Singh et al 2021 Eng. Res. Express 3 012002 DOI 10.1088/2631-8695/abeca0
Article metrics
5057 Total downloads
Permissions
Get permission to re-use this article
Share this article
Author e-mails.
Author affiliations
1 Research Scholar, IKGPTU, Kapurthala, Punjab, India
2 Department of Mechanical Engineering, Beant College of Engineering & Technology, Gurdspur, India
3 Department of Mechanical Engineering, Punjab University SSG Regional Centre, Hoshiarpur, Punjab, India
4 Department of Mechanical Engineering, University Institute of Engineering, Chandigarh University, Gharuan, Mohali, Punjab, India
Jasjeevan Singh https://orcid.org/0000-0001-7444-4075
Rupinder Singh https://orcid.org/0000-0002-0877-3847
- Received 27 January 2021
- Accepted 8 March 2021
- Published 18 March 2021
Peer review information
Method : Single-anonymous Revisions: 1 Screened for originality? Yes
Buy this article in print
Cutting fluids provide cooling at the cutting tool and on the surface of work piece, lubricate the tool-workpiece interface and evacuate chips from the cutting zone in the machining processes. The primary reason for using cutting fluid is to reduce the temperature at cutting zone and friction wear either through cooling or lubrication. To maximize the efficiency of cutting fluids in machining processes the knowledge of machining conditions and cutting fluid types are critically important. However, misemploy of the cutting fluid and non efficient method of disposal can raise health issues and environmental impact. In this paper, an attempt has been made to provide overview of cutting fluids type, cooling techniques and main alternatives as dry machining, cryogenic cooling, minimum quantity lubrication and hybrid cooling minimizing use of cutting fluids. The inclusion of solid lubricants, nano fluids in lubrication/cooling techniques results in increase in the productivity of the process due to reduction in friction and heat at the cutting zone. The cutting parameters and type of tools utilized by various researchers have been summed up and introduced in this paper to provide useful information to various researcher works.
Export citation and abstract BibTeX RIS
1. Introduction
Cutting fluids are generally applied in machining operations as milling, drilling and turning. A cutting fluid should have excellent lubricating and cooling properties. Cutting fluids decrease the friction, improve surface finish, prevent the formation of built up edge (BUE), evacuate chips from the cutting zone and protect work from corrosion. Today the interest is developing in manufacturing industry for good quality product, low cost and high profitability. High productivity is essentially associated with high cutting speed, depth of cut and feed rate resulting high temperature in the cutting zone. Consequently, the quality of a product, dimensional accuracy and tool life are deteriorated. If the feed rate and cutting speed are reduced just for smoothness of surface, it is just wastage of resources without significant gains in productivity. Therefore, to produce a quality product the efficiency of cutting fluids and optimization of parameters should be well determined. The selection of cutting fluid depends upon the factors as shown in figure 1 .
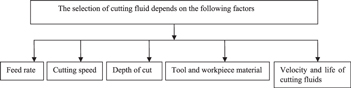
Figure 1. The selection of cutting fluid depends upon the following factors.
Download figure:
The use and disposal of cutting fluids with combination of legislation on environmental and health protection led towards green machining. The development of vegetable based cutting fluids is safe for disposal, less toxic, renewable and is environmentally friendly and can be disposed easily [ 1 , 2 ]. Cutting fluids improve tribological process, during machining operations which occurs when workpiece and tool make contact. Inclusion of cutting fluids removes debris and reduced heat generation during machining [ 3 ]. Minimum quantity lubrication (MQL) and dry machining has been successfully applied in some machining processes and have classified as environmentally friendly techniques. Nowadays, the advancement in technology has identified solid lubricants, nano-lubricants and ionic fluids increasing the productivity and performance of the product. Most common cooling techniques has been widely used as flood cooling, MQL, dry cutting and cryogenic cooling possess characteristic in terms of efficiency, cost, energy consumption, disposal and environmental hazard.
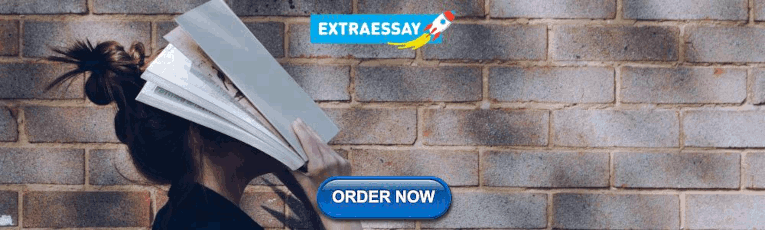
2. Functions of cutting fluids
The primary functions of a cutting coolant are cooling and lubricating the workpiece in a machining process [ 4 ]. Lubrication property in cutting coolant reduces the abrasion and adhesion at low cutting speeds as well as greases the contact areas between chips and tool rake face [ 5 ]. Today vast variety of cutting fluids are available and effectiveness of cutting fluid depends upon various factors such as cutting parameters, strategies for cutting fluid application and types of machining.
The properties of cutting fluids should not change within a range of pressure, temperature and time having same stable chemical composition. For instance, cutting liquids must prevent corrosion between workpiece material and cutting tool as well as lubricating oil of slides and machine bearing [ 6 ]. According to the principle of metal cutting, heat generation occurs in three deformation zones during metal removal process namely as primary deformation zone, secondary deformation zone and tertiary deformation zone as shown in figure 2 . Metal cutting is the process of removing a layer of thin material from workpiece during machining. In the figure a sharp edge tool is set to a certain depth of cut and moves relative to the workpiece. The formation of chips occurs in all machining processes; this occurs due to deformation of work material on the surface of job with aid of cutting tool. Chips are produced in different sizes and shapes depending on work material, cutting conditions and tool geometry. The main aim of machining operations is to improve quality and productivity by reducing machining costs. The parameters affecting the machining performance are shown in fishbone (cause & effect) diagram figure 3 .The application of cutting fluids can reduce cutting power in machining operations. The cutting fluids also help in chip evacuation, prevent clogging of tool and BUE. Evacuation of chips depends on viscosity and flow rate of cutting fluids. Cutting fluids having higher viscosity are less capable to evacuate chips from machining zone as compared to less viscosity cutting fluids.
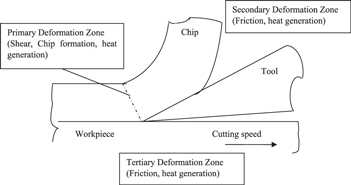
Figure 2. Sources of heat generation in metal cutting.
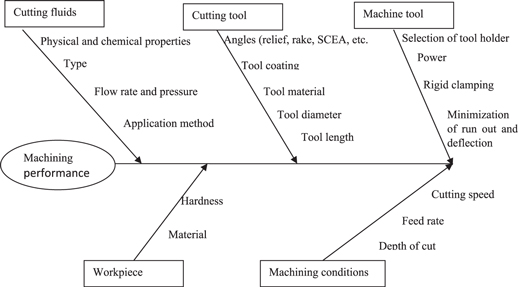
Figure 3. Effect of machining parameters in performance.
3. Chemistry and properties of cutting fluids
The time available for establishment of chemical equilibrium on the metal surface varies, depending on the cutting process used will affect the performance of cutting fluid. At the point when the metal is cut a clean nascent surface at atmospheric pressure results that is very reactive and readily adsorbs either by chemisorption or physisorption any substances (gases or liquids) in adequately closeness to itself. Additives fatty acids, fatty esters and fatty alcohols are added to base mineral oils to increase friction characteristics and adequate load carrying capacity. Chemisorption is adsorption to a surface due to covalent bond while phsisorption is adsorption to a surface due to Vander walls forces from polar interactions between atoms. The cutting fluid is under high temperature and high pressure during cutting process; the fresh machined surface is with high activeness and adsorption, reaction and diffusion layer will be formed on surface, chemical and electrochemical effect between cutting coolant and piece of work will result in loss of alloying elements and damage of the workpiece in scope of grain and grain boundaries [ 7 ].
The choice of cutting fluid is very important and has a direct effect on productivity, tool and cost. The selection of cutting fluid varies with the different machining conditions and processes. The physical and chemical properties of cutting fluid have a great effect on surface quality. The usage of cutting fluid will dynamically change the geometry and material property of machined surface. The cutting fluid should have desirable properties such as high thermal conductivity (sufficient cooling increases the life of tool and surface finish), low viscosity (helps to rapid settling of dirt and chip), high flash point (reduces the risk of fire), large specific heat (to dissipate heat at cutting zone), low surface tension and low coefficient of friction (ensures smooth flow) and less evaporative and stability (long life).
4. Literature review methodology
This study is rigorously focused on the use of cutting fluids in the machining processes. The main objective of review is to provide comparative analysis of types of cutting fluid and cooling techniques used in machining (turning, milling and drilling) in light of the most novel works published in the literature. The literature was conducted using different like use of Google search engine, Science direct data base, Springer data base, Taylor and Francis and other significant works available as open resources from 1997 to 2021.
Data was collected in away so that in the work reports the significant findings of the past two decades which includes use of nanofluids, ionic fluids, solid lubricants in MQL. A content analysis has been made based on selection of papers that considers the influence of lubrication process on the tribological capacity of the processes in terms of tool life, surface roughness, cutting temperature and cutting forces. The primary strength of review methodology used herein is significant and classification of involved papers based on machining process, cooling techniques and different variables researched and analyzed by the authors.
5. Cutting fluid classification
Cutting fluids are generally categorized into three different classes as shown in figure 4 .
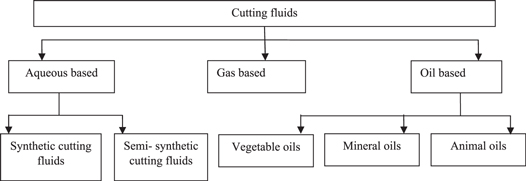
Figure 4. Cutting fluid classification.
5.1. Types of cutting fluid
5.1.1. straight oils.
The cutting fluids are mainly categorized as straight cutting oils and water soluble oils. These cutting oils are not diluted and improve the wetting and lubricating properties, corrosion resistance and under extreme pressure conditions addition of sulphur, chlorine compounds improve surface finish and enhance tool life. Straight oils and have high flammability and poor cooling characteristics. Straight oils save energy by reducing cutting forces. In high speed cutting operations straight oils do not work effectively because they do not dissipate heat effectively.
Straight oils are used for low speed applications, where temperature is not significant [ 8 ]. The reduction in smoke formation and fire hazard can be achieved by vegetable oils due to higher viscosity [ 9 ]. Vegetable oils are preferred than mineral oils in reducing surface roughness and tool wear. Generally, vegetable oils are appealing substitutes for oils got from petroleum having minimal social, economic and environmental effects attracting industries to attain sustainability [ 10 , 11 ].
Lawal et al (2014) used taguchi method to investigate the effect of cutting fluids while turning AISI 4340 steel and concluded that vegetable oils palm kernel oil (PKO) and cottonseed oil (CSO) does not cause any hazard to worker. They have environmentally friendly properties and better heat conductivity due to high percentage of water in oil. PKO with 2.977 mm 2 /s viscosity shows more influence on surface roughness as compared to other cutting fluids. The pH values for CSO (10.98) and PKO (10.46) does not cause any health hazard to worker during machining process. The results shows cutting speed and feed rate are significant factors affecting surface roughness whilst cutting fluid and depth of cut are significant factors affecting cutting force [ 12 ]. Virgin coconut oil (VCO) has shown good physio-chemical properties and oxidant nature as compared to coconut oil [ 13 ]. Vegetable oil castor enhances surface roughness and reduces tool wear with MQL technique in machining of hardened stainless steel. The author reported that MQL can be effectively used for turning hardened steel with cutting parameters up to feed 0.24 mm/rev and cutting speed 170 m/min using coated carbide tools. A lubricant of 50 ml h −1 provides longer tool life with MQL technique as compared to dry cutting [ 14 ]. Vegetable oils show equivalent or better performance in reaming and tapping stainless steel than mineral oils [ 15 ]. Vegetable oils show promising results than mineral oil in drilling austenitic stainless steel in terms of long tool life and less environmental impact [ 16 ]. Khan et al (2006) used MQL technique in machining AISI 1060 steel using vegetable oil as cutting fluid. The cutting performance of MQL was observed better as compared to dry machining due to reduction in cutting temperature at the cutting zone. MQL jet enhanced surface roughness, improved life of tool and reduced tool wear as compared to dry machining of steel [ 17 ].
Kumar et al (2016) assessed performance of vegetable oils with inclusion of extreme pressure (EP) additives while turning steel using coated carbide tools. They concluded that inclusion of EP additive like CCF5 effectively reduced cutting tool temperature as compared to other VBCFs and conventional cutting fluids without additive. The high cutting tool temperature was observed for conventional cutting fluid (SO) due to low thermal conductivity and viscosity [ 18 ]. The better machining performance was achieved with higher rate of EP additives in terms of reducing cutting speed and feed forces but due to chemical interaction with machined surface affects surface roughness values negatively. The result shows vegetable based cutting fluids can be better substitute as they reduce occupational health risks and biodegradable [ 19 ]. MQL technique using vegetable oil protects the environment than mineral oil which is not operator friendly and also non biodegradable. The surface roughness and tool wear were reduced by 6.7 and 0.14% using aloe vera oil as compared to conventional cutting fluid [ 20 ].
5.1.2. Emulsifiable oils
Emulsifiable oils (also referred as soluble oils) are mineral based oil include emulsifiers, EP and other additives. Soluble oils are low cost; provide good cooling capability at higher speeds. Soluble oils have better cooling capacity than straight oils and provide rust protection. The main problems related with soluble oils are toxic mist, bacterial attack, susceptible to hard water. Adekunle et al (2015) carried out turning of mild steel and assessed performance of vegetable oil using carbide cutting tool. Soluble oils produced lesser surface finish than vegetable oil and highest surface finish was obtained by melon oil. The chips produced are more ductile and continuous in nature using vegetable oil as compared to soluble oil and dry cutting. Soluble oil absorbs heat better than other coolants as shown in figure 5 at spindle speed 80 rpm respectively [ 21 ]. Machado et al (1997) studied performance of mineral soluble oil and synthetic oil during turning of steel. Soluble oils show less mean tool-chip interface temperature than dry cutting conditions but higher than synthetic and semi-synthetic fluids during machining of AISI 8640 steel. The tool life was extended with the semi-synthetic fluid based on flank wear parameter. The tool was observed diminishing with increase in cutting speed at same cooling/lubricating conditions. [ 22 ].

Figure 5. Variation of temperature and depth of cut at 80 rpm. Reproduced from [ 21 ] CC BY 4.0 .
Soluble oil was used by employing MQL technique in turning of stainless steel as reported by Sohrabpoor et al (2014). The low surface roughness and tool wear was observed under MQL as compared to dry, cool air and wet strategies [ 23 ]. The flank wear was reduced by 24% by employing soluble oil in machining of Al-MN alloy. Neem seed oil was found more effective than soluble oil as a cutting fluid. The surface roughness was reduced by using neem oil as compared to soluble oil and dry machining. The least surface roughness was obtained with neem seed oil at spindle speed of 250 rpm. The highest reduction in flank wear was observed with neem oil at spindle speed of 250 rpm during machining Al-MN alloy [ 24 ].
5.1.3. Synthetic fluids
Synthetic fluids are water based solutions of synthetic lubricants, EP, corrosion inhibitors, antibacterial additives, water softeners and other additives. They possess excellent cooling capability, better lubrication properties, superior corrosion protection with limitations of easily contaminated with foreign oils, some toxicity and high cost. Groover (2002) reported that synthetic fluid especially used for low force applications where cooling is an essential prerequisite [ 25 ]. Suda and Yogota (2002) studied secondary performance such as oxidation stability, biodegradability and storage ability employing conventional cutting fluids and lubrication oils. They concluded that biodegradable synthetic esters are seen as an ideal cutting fluid for MQL machining [ 26 ]. Inclusion of EP additive in synthetic ester results a multifunctional fluid used for both machining and lubricating machine parts [ 27 ].
Vierira et al (2001) investigated the performance of cutting fluids during face milling of steel using cemented coated carbide tools. The cutting temperature was reduced by using synthetic cutting fluid. An improvement in surface finish and tool life was observed during dry machining as compared to other cutting fluids. The application of synthetic and semi-synthetic cutting fluids increased the power consumption [ 28 ].
5.1.4. Semi-synthetic fluids
Semi-synthetic fluids are solution and emulsion of synthetic lubricants, (2% to 30%) mineral oil, emulsifiers and additives. They have good cooling and wetting capabilities, better corrosion protection with limitations of little toxicity and easily contaminated by foreign oils. Ozcelik et al (2013) concluded that semi-synthetic fluid was not suitable for drilling of stainless steel because of excessive tool wear [ 29 ]. Tool wear was not observed with semi-synthetic fluid, mineral oil and vegetable oil during drilling of stainless steel. The drilling depth is not an influential factor in terms of surface roughness for all the cutting fluids [ 30 ]. The application of semi-synthetic fluid by employing coated carbide insert during end- milling of stainless steel improved the tool life. With elevated speed, the cooling efficiency becomes insignificant [ 31 ].
5.1.5. Gas -based fluids
In general gas based fluids are referred to the substances that are in gaseous form at room temperature and in machining applications can be pressure-cooled or gas cooled. Gas based fluids are air, carbon dioxide, nitrogen and helium. The air, obviously, was the first machining coolant. Compressed air from an air compressor, released from a nozzle focused on the tool, is in some cases proved a valuable coolant. Compressed gas based coolants find applications in heavy cutting conditions where traditional cooling techniques not able to penetrate tool chip interface. De Lacalle et al (2006) studied spraying of oil micro-drops in air when milling wrought Al alloy in high speed. The tool flank wear was significantly reduced up to 44% with the application of oil spray into the machining zone. The cutting temperature and forces were also reduced with the application of oil spray into the machining zone [ 32 ].
The coolant liquid nitrogen has been widely used in machining of hard materials such as titanium, hard steels etc The reduction in cutting zone temperature and enhancement of tool life was observed using liquid nitrogen while machining titanium alloy [ 33 , 34 ]. The cryogenic coolant liquid nitrogen improved the surface integrity in machining of titanium alloy. The cryogenic machining is environment friendly and improved the overall product performance [ 35 , 36 ]. Table 1 throws light on summary of cutting fluids used in machining processes.
Table 1. Summary of cutting fluids used in machining processes.
6. Ecological aspects, environmental issues and disposal of cutting fluids
The growth of cooling-lubricant fluids and rise in global production volume induced negative environmental effects and threat for employee's health. According to Celik et al (2014) green machining should be one that uses effective cooling technique to produce quality part with supportive utilization of cutting fluid and minimizing environmental impact [ 37 ]. A ring of sustainable machining techniques as dry cutting, minimal amount of coolants and lubricants, HPC, cryogenic cooling and biodegradable oils can be used to improve environmental performance as shown in figure 6 [ 38 ].
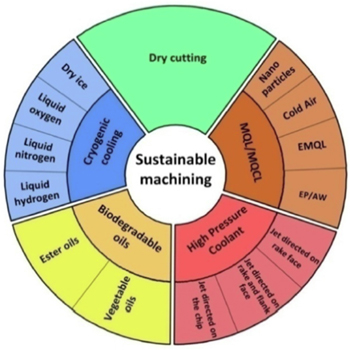
Figure 6. Ring of sustainable machining. Reprinted from [ 38 ], Copyright (2019), with permission from Elsevier.
Shashidhara et al (2010) reported that about 80% of all job-related infection of the operators was because of skin contact with cutting fluids [ 39 ]. The fluid application generates mists and mist droplets can cause respiratory problems, throat, pancreas and prostate problems [ 40 ]. The bacterial growth in the cutting coolant may cause hazardous to operators. Inclusion of chemical additives such as phosphorus, sulphur and biocides in cutting fluids cause mist, fumes and smoke causing skin and respiratory problems. The above problems can be overcome by environment friendly techniques. A huge data base can be created by experimentation on ecological aspects for other sustainable techniques.
The disposal of fluids is necessary after its use in manufacturing operations. The cutting fluids after use degrade quality and lose efficiency. The chemical stability, flame resistance and viscosity properties sometimes preferred chlorinated paraffin as additives used in cutting fluid. Disposal of chlorinated cutting fluids is allows to burn in incineration sites because of toxic dioxins. Therefore, it is categorized as hazardous waste to environment as well as life of human [ 41 ]. The ultimate goal of disposal of fluid is to protect the environment from pollution. The alternatives of disposal of cutting fluids can be ultra-filtration, reverse osmosis, chemical treatment, biological treatment and by evaporators one can reduced their volume. Dispose MWFs with prior sanction by the authority directly in to sewer keeping in mind fluid free of chips and fines, treated with biocides, non toxic, non toxic concentrations of heavy metal ions, dissolves in water etc.
7. Methods of application of cutting fluids in traditional machining
The deteriorating of the tools and surface roughness of work piece is due to friction and heat generation during machining of the materials. The cooling techniques employing cutting fluids can successfully reduce the heat generation resulting in efficient machining of the materials.
7.1. Flood cooling techniqu e
Flood cooling is a feature, that usually available on CNC machines. The steady fluid comes through a nozzle that aimed at tip of tool for cooling purpose. Flood cooling is eliminating in machining operations due to environmental impact, huge use of coolants/lubricants, handling of waste disposal and negative impact on workers health. Volume flow rate of cutting fluid is significantly higher. For single point cutting tool operation a typical coolant flows range rate is around 10 L min −1 and 225 L/min/per tooth for multiple points cutting tool operation [ 42 ].
Better cooling can be performed with flood cooling technique under pressure of 300 Kpa or more with flood cooling fluid if applied in the clearance face [ 43 ]. At low cutting speeds flood cooling produced cooling effects which results in lowering surface roughness, subsurface damage of machined component during machining of Inconel 718. However, the favorable effect of flood cooling is not obvious at higher cutting speed may be due to seizure effect or bubble carrier that prevents heat transfer between a piece of work and cutting fluid [ 44 ].
Jayal et al (2009) studied the effects of cutting fluid application methods on tool wear using coated carbide tools during machining of steel. Flood cooling shows mean tool life better than other cutting fluid applications with flat faced and grooved PVD tools on the basis of one tailed t-test at 0.05 level of significance as illustrated in figure 7 . MQL application of oil with inclusion of EP additives shows worst condition [ 45 ]. Sun et al (2007) investigated tool life and cutting conditions under dry cutting and cooling techniques during end milling titanium alloy. A little adhesion was observed in end milling of titanium alloy, but overall high quality of workpiece was achieved by MQL. The MQL application shows better results for higher machining conditions and can replace flood cooling and dry cutting [ 46 ].
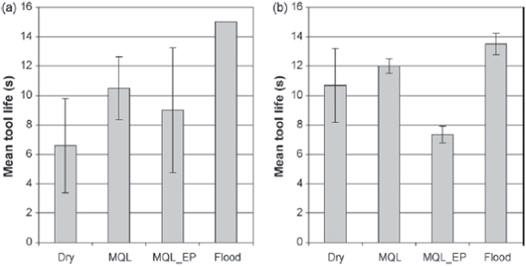
Figure 7. Mean tool life under different cutting fluid applications at higher cutting speed (400 m/min) for (a) flat-faced PVD tools (b) grooved PVD tools. Reprinted from [ 45 ]. Copyright (2009), with permission from Elsevier.
7.2. Mist cooling technique
In mist cooling a 'mist' is sprayed on to the cutting operation and preferred where flood cooling is to eliminate in machining the materials. The water based cutting fluids mostly used in mist cooling. Mist cooling reduces the environmental impact and has higher efficiency than flood cooling. The reduction of lubricant use is a plus point in mist cooling system.
Mist application of cutting fluid uses a flow rate of 50 to 500 ml h −1 which is about 3 to 4 orders of magnitude lower than the amount used in flood conditions. Mist application has three components mist generator, nozzle and compressor and requires high pressure and impinged at high speed through nozzle at the cutting zone as shown in figure 8 . The tool wear was noticed less for mist condition as compared to dry and flood conditions. The tool wear was observed less under flood conditions as compared to dry may be due to lubrication and reduction in cutting zone temperature. Mist application system was found effective as compared to dry and flood conditions depending upon the cutting parameters. Even under mist conditions the increase in temperature during turning was observed with increase in speed and depth of cut may be due to higher removal rate and increase in energy consumption reported by Hasib et al (2010) [ 47 ]. Nandgaonkar et al (2016) assessed the effect of water oil mist sprat (WOMS) using ester oil based cutting fluid during drilling titanium alloy. The WOMS method enhanced tool life by 66% as compared to dry conditions. Drilling under WOMS cooling had better tool life, good cooling effects and optimum cutting parameters [ 48 ].
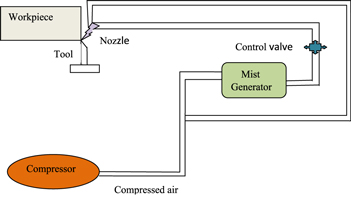
Figure 8. Schematic representation of Mist cooling set up.
Amrita et al (2013) investigated performance of mist cooling during turning steel. The reduction in cutting forces, cutting temperature and enhancement of tool life was observed with mist application by employing nanographite-slouble oil in turning of steel with both cemented carbide and HSS tool. Minimal cutting forces and tool wear were obtained for both HHS tool and cemented carbide tool with 0.5 wt% nanographite-soluble oil at flow rate of 15 ml min −1 [ 49 ].
Mist cooling demonstrated capability of replacing flood technique under the concept of green manufacturing. The result shows more magnitude of adhesion under dry conditions as compared to mist and flood conditions [ 50 ].
Mendes et al (2006) assessed the performance of cutting fluids during machining of aluminium alloys and conclude that the higher power consumption, pressure, torque and lower feed forces were observed with increase in the flow rate of mist during drilling of aluminium alloy. Inclusion of chlorine EP additive produced lower cutting forces and improved surface finish at high cutting speed and low feed rate and depth of cut during turning aluminium alloy [ 51 ]. Dongsheng et al (2016) studied tool wear using pneumatic mist jet impinging cooling (PMJIC) technology during milling titanium alloy. PMJIC technique proved to reduce all types of wear as coating delamination, adhesion, notch wear, micro- chipping except cracks as compared to traditional flood cooling [ 52 ].
7.3. High pressure cooling (HPC)
In general, HPCs are used to cut hard materials, reduces tool wear and production costs. It is an effective method in turning operations for reducing temperature in the cutting zone, higher productivity and effective chip control depending on the pressure and flow rate of fluid. Cutting fluids have a direct influence on the environment.
HPC penetrate deeper in to the cutting interface, provide more cooling effect than conventional cooling [ 53 , 54 ]. Application of HPC has been investigated in turning of titanium alloy by researchers and concluded improvement in tool life due to reduction in tool tip temperature [ 55 – 58 ]. HPC technique was reported to reduce friction [ 59 , 60 ].
Vagnorius et al (2010) investigated the life of SiALON ceramic inserts using HPC technique during machining Inconel 718 alloy. They concluded that HPC technique can extend the life of SiALON ceramic inserts with properly designed machining process. The chips produced were very short, needle like under HPC technique, while long and tubular under conventional flushing [ 61 ]. The ceramic tools improved chip breakability and enhanced tool life by 20% with HPC technique [ 62 ].
The alloy IN718 face was turned by applying conventional and HPC with cutting speed of 30 m min −1 at 8 MPa. HPC reduced flank wear and cutting forces by 30% and 10% respectively [ 63 ]. At 100 bar pressure the life of tool can be increased up to 9 times with assistance of HPC [ 64 ]. Duplex HPC improved performance of tool life as compared to dry conditions. HPC jets reduced the tool wear, force and consequently reduced chip reduction coefficient (CRC) by ensuring effective lubrication. The increased cutting speed and feed rate lowered value of CRC may be due to increment in temperature making chip thinner and stretched as shown in figure 9 [ 65 ].
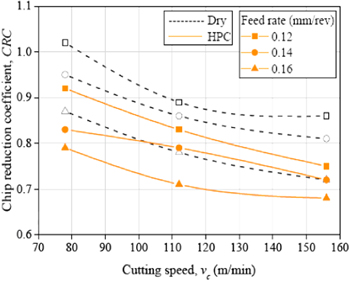
Figure 9. Effect of HPC jets, cutting speed and feed on chip reduction coefficient. Reprinted from [ 65 ], Copyright (2018), with permission from Elsevier.
Textured tools allied with HPC have influential effect on machining of materials. Surface texturing results in enhancement of tool life and increase productivity [ 66 , 67 ].
Table 2 throws light on summary of coolant techniques used in the machining processes.
Table 2. Summary of coolant techniques used in the machining processes.
8. Alternatives to traditional cutting fluids for green machining
The main alternatives to traditional cutting fluids are named as dry, cryogenic, hybrid and MQL as shown in figure 10 .
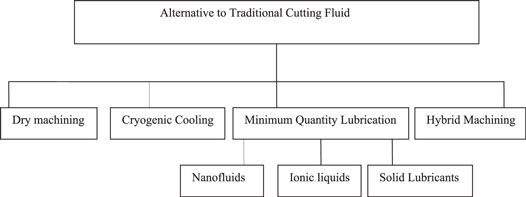
Figure 10. Alternatives to traditional cutting fluids for green machining.
8.1. Dry machining
The developing interest to attain sustainable machining drives researchers to locate out favorable cooling/lubrication techniques. Dry machining is gaining importance in manufacturing world due to environmental friendly and job satisfaction amongst the workers as shown in figure 11 [ 68 ]. Dry machining has some drawbacks like adhesion between tool rake face and chip occurs for some combinations of tool and work materials [ 69 ]. To implement dry machining on the shop floor ultra-hard cutting tool and rigid machine tool required as reported by Arulraj et al [ 70 ].
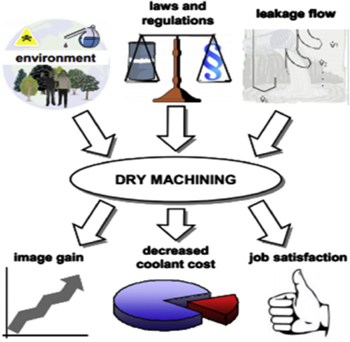
Figure 11. Benefits of dry machining. Reprinted from [ 68 ], Copyright (2004), with permission from Elsevier.
Nouari et al (2003) carried out dry machining of Al alloys using WC-Co carbide drills. The diamond coating improved tool life in machining and produced quality 2000 holes at cutting conditions feed 0.16 mm/rev and cutting velocity 62 m min −1 in machining of aluminium alloy [ 71 ]. The combination of (hard/soft double layers) coating reduces cutting forces and improves chip flow [ 72 ].
PVD (physical vapor deposition) technique by using TiN/TiAlN (Titanium Nitride/Titanium Aluminium Nitride) coated tool provides promising results for rough and finishing conditions under dry conditions for machining Inconel alloy [ 73 ]. CVD (Chemical Vapor Deposition) coated tool reduced tool wear; enhanced surface quality and reduced chip deformation. At cutting speed of 140 and 150 m min −1 nose wear was found prominent failure mode for uncoated carbide insert [ 74 ].
For machining of austenitic stainless steel under dry conditions AlTiCrN (Aluminium Titanium Chromium Nitride) coating is favorable and can be a future coating as reported by Kulkarni et al (2015). The magnitude of force of AlTiCrN coated tool was found low because of decrease in contact length and in shear strength where as AlTiN (Aluminium Tiatnium Nitride) shows higher cutting force owing to its coating properties [ 75 ].
Fan et al (2016) carried out machining of titanium alloy under dry conditions. Elevated cutting speed shows the occurrence of heavy adhesion, oxidation and diffusion in dry machining of titanium alloy using cemented carbide tool. The peeling-off of cutting tool material is due to abrasion resistance and decrease in tool strength [ 76 ].
Pattnaik et al (2017) assessed the performance of tool wear under dry conditions in machining of aluminium alloy. PCD tool outperformed other tools in terms of tool wear, smoother chip and roughness in machining of aluminium. The study of chips shows that voids and cracks generated are less in case of PCD tools as compared to other tools [ 77 ]. PCD tool shows promising results than other tools in machining of aluminium under dry conditions except surface finish. WC tool enhanced surface finish than other tools [ 78 ].
Mishra et al (2018) carried out 3D finite element simulations for machining titanium alloy under dry conditions using textured tools. Dry machining of titanium is possible with textured tools but will be ineffective at higher speeds and feed. In dry cutting little or no effect of depth of texture on cutting forces observed may be due to absence of fluid. In case of dry cutting for textured tools textured area density is considered the most influential parameter [ 79 ].
Rajaguru et al (2017) assessed the tool performance in machining of superduplex stainless steel (SSSS) under dry conditions. High temperature was observed in PVD coating than others in machining owing to low thermal conductivity and high friction. The results shows that [MT-TiCN]-Al 2 O 3 coating provides better performance in terms of surface integrity, tool wear and cutting force as compared to other coatings [ 80 ]. Adhesion wear was observed with PVD coating in machining of superduplex stainless steel (SSSS) and can be lowered with use of lubrication [ 81 ].
Micro-grooved PCD tool can decrease (main cutting force, tool-chip contact length) in machining of titanium alloy under dry conditions. The micro-grooved PCD tool decreases the thrust force and main cutting force with cutting speed range from 16.485 m min −1 to 125.6 m min −1 as shown in figures 12 and 13 [ 82 ]. Micro hole textured cutting tool lowers cutting force and energy consumption in machining of titanium alloy as reported by Ma et al (2016) [ 83 ]. In general, no coolant is used in the machining of materials so sustainability of dry machining is high. But some limitations as formation of BUE, high tool wear, higher friction and surface roughness inspire researchers to modify dry machining. Applications of coated tools PVD or CVD and employ of textured tools are some modifications in dry machining
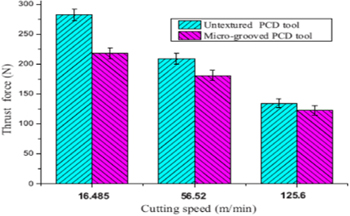
Figure 12. Influence of micro-grooved tools and untextured tools on thrust force under different speeds. Reprinted from [ 82 ], Copyright (2017), with permission from Elsevier.
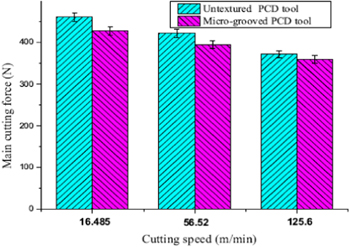
Figure 13. Influence of micro-grooved tools and untextured tools on main cutting force under different speeds. Reprinted from [ 82 ], Copyright (2017), with permission from Elsevier.
8.2. Minimum Quantity Lubrication (MQL)
MQL (NDM) has been designed as pre-eminent alternative to flood cooling and dry conditions. The main benefits of MQL are surface quality and improved performances in cutting operations and reduction of impact to the environment. A small quantity of cutting fluid with the help of compressed air at very high velocity (100 m s −1 ) is injected in the form of ultra-fine droplets into the cutting zone [ 84 ].
Rahim et al (2015) used MQL technique with cutting fluid synthetic ester and reduces cutting temperature, cutting force, tool-chip contact length as compared to dry conditions. MQL improved chip thickness as compared to dry conditions [ 85 ]. The better cutting performance was attained with synthetic ester than using vegetable oil or mineral oil by employing MQL technique [ 86 , 87 ].
Rabiei et al (2015) assessed the grinding performance of soft steels using MQL, dry and conventional fluid cooling techniques. A better surface finish was obtained with aluminium oxide grinding wheel as compared with CBN (Cubic boron nitride) grinding wheel. The MQL technique reduces the tangential force, increases the residual compressive stresses and can be effectively used in grinding process [ 88 ]. CBN and porous wheels, and grinding oils show potential development in grinding process under MQL technique. The grind ability of hardened steel improved under MQL technique using oil than other conditions by reducing grinding forces [ 89 ]. MQL (NDG) technique with cutting fluid aerosol increased the wheel life and better quality of the ground parts as compared to dry turning [ 90 – 92 ].
The MQL technique is favorable for machining AISI D3 type material, produces good results in terms of surface roughness, cutting forces and temperature. The lowest surface roughness value of 0.1236 μ m was found under MQL technique using soluble oil as compared to wet and dry grinding environments. The coefficient of friction value was found better under MQL environment as compared to dry and wet environment due to effective lubrication between abrasive grain and work material [ 93 ]. MQL technique enhanced surface quality of steel as compared to dry and wet conditions [ 94 – 96 ].
8.3. MQL using nanofluids
In general, MQL technique has limitations in high speed machining of materials. The high thermal conductivity of nano a particle in the cutting fluids can decreases or eliminates shortcomings of traditional cutting fluids in MQL techniques. The MQL base liquids reinforced with nanoparticles such as, MoS 2 , Al 2 O 3 , SiO 2 , PCD, ZrO 2 , CNT, and so on, proved enhancement of tribological property and viscosity leading machining efficiently.
Najiha et al (2015) concluded water based TiO 2 (Titanium dioxide) nanofluid can increase sustainability of the machining processes and efficacious for edge integrity [ 97 ]. The performance of TiO 2 nanofluid was higher as compared to other techniques in terms of tool wear, cutting force, surface roughness and chip morphology. The use of TiO 2 nano fluid reduced average surface roughness by 34.7%, 7.22% and 11.64% as compared to dry machining, wet machining and conventional mist respectively [ 98 ]. The MQL technique using nanofluid (Al 2 O 3 +Ag) reduces chip thickness, cutting forces, chip reduction coefficient, and tool wear than dry machining [ 99 ].The main drawback of MQL method as burn marks and form of white layers can be reduced by MQCL( Minimum quantity cooling lubrication) method due to better cooling and lubrication. Inclusion of MoS 2 (Molybdenum disulphide) additives in emulsion based fluid under MQCL technique produced surface roughness, surface profile and surface microstructure of machined surface better than MQL pure fluid, dry and MQCL pure fluid [ 100 ]. The MQL technique using nanofluid reduced the flank wear and central ear of tool [ 101 , 102 ]. The MQL technique using nanofluid and chilly carbon dioxide gas enhance the surface quality and reduces average milling forces. The nanoparticles inclusion in vegetable base fluid can increase thermal conductivity of the fluid [ 103 ].
8.4. MQL using solid lubricants
The tribological performance of MQL method is affected before cooling and lubrication due to abrupt vaporization of cutting fluids at cutting zone. Application of solid lubricants such as MoS 2 , WS 2 (Tungsten disulphide), graphite, HBN (Hexagonal boron nitride), TiC, TiN, TiB 2 (Titanium boride), boron oxide, PTFE (Polytetrafluoroethylene) etc is one of the exceptional improvements of MQL. Paturi et al (2015) reported that the WS 2 addition in emulsifier based cutting fluid increased the surface quality by 35% than MQL machining alone assessed with ANOVA and Taguchi design. The result shows that inclusion of WS 2 in emulsifier oil based cutting fluid can work effectively as an additive [ 104 ]. Inclusion of graphite in oil enhanced the life of tool and surface finish as compared to pure oil and (MoS 2 + oil). Inclusion of solid lubricant to the cutting fluid while machining reduced surface roughness at low cutting speed [ 105 ]. Moura et al (2015) used solid lubricant for turning titanium alloy by PVD coated tools. The life of tool was enhanced by 75% at low cutting speed 130 m min −1 as compared to dry conditions with inclusion of MoS 2 . The reason for longer tool life can be attributed to its superior cooling and better lubrication. The lubricant MoS2 showed best performance among all other fluids tested. Low values of surface roughness were obtained with MoS 2 and higher for dry machining. The reason for lower surface roughness produced by MoS 2 can be attributed due to its strong adhesion [ 106 ]. The performance of machining with solid lubricant is better including surface finish as compared with dry and wet conditions reported by researchers [ 107 – 109 ].
8.5. MQL using ionic liquids
Ionic liquids are usually liquids salts having temperature less than 100 °C and contain organic cation and inorganic anion. MQL technique employing ionic liquids is one of the newest innovative approaches. The inclusion of ionic liquids enhances the properties of base oil. The high cost of ionic liquids prevent for use in machining as neat lubricants, but addition of low concentration of ionic liquids may alter performance of conventional oils.
Davis et al (2015) reported that IL ((BMIM-PF6) based MQL reduced tool wear by 60% as compared to dry and 15% more with water based MQL. Ionic liquid (IL) enhanced the surface roughness [ 110 ]. Ionic liquids (AIL & PIL) in MJO oil reduced the cutting forces, cutting temperature, friction angle, friction coefficient and chip thickness in machining of steel reported by Sani et al (2019) [ 111 ]. The small quantity of ionic liquid is influential in tribological conditions of the machining processes [ 112 ]. Ionic liquids provides a little improvement in surface quality and displayed exceedingly low volatility compared with conventional oil and other lubricants [ 113 ].
8.6. Hybrid cooling/lubrication technology
To attain better effects of cooling/lubrication techniques in machining operations, combination of two or more coolant strategies are now the aim of the researchers. Gupta et al (2019) reported that hybrid cooling N 2 MQL and R-N 2 MQL results in reduction of abrasion and existence of BUE as compared to dry cutting over the tool rake surfaces [ 114 ]. The hybrid cryogenic and MQL technique (CryoMQL) improved surface roughness by 18%, and enhanced tool life almost double in machining of Inconel alloy [ 115 ]. Hybrid nanofluid reduced surface roughness, cutting force and enhanced tool life as compared to cryogenic (CO 2 based) cooling [ 116 ]. The promising results were obtained with hybrid cooling in terms of machining performance as compared to other lubricants [ 117 , 118 ]. Hybrid nano green fluids with 0.3% concentration produced better results in terms of cutting force, feed force, coefficient of friction (at tool-workpiece interface) and surface roughness as compared to other cutting fluids [ 119 ].
8.7. Cryogenic cooling
Cryogenic cooling is gaining importance and considered as effective cooling with clean environment. LN 2 at −196 °C and CO 2 or dry ice at −78.5 °C is used as coolant in cryogenic cooling process. The cryogenic cooling provides better cooling but with limitations of no lubrication and the performance of cryogenic cooling depends on the supply of available cryogen and cost of cryogen is high. Ahmed et al (2015) reported that high thrust values were observed with increase in hardness of the material with the use of LN 2 in drilling of titanium alloy. Surface roughness values were higher and hole quality was not favorable with LN 2 coolant [ 120 ]. In a similar study high thrust forces were observed with increase of hardness in turning of stainless steel with use of LN 2 coolant [ 12 , 121 ]. Conventional cooling was found more effective than cryogenic cooling for long machining operations in terms of machinability and surface integrity [ 122 ]. Cryogenic cooling using LN 2 has improved surface roughness using solid carbide cutters in end milling operations. Cryogenic cooling at low cutting speed (30 m min −1 ) and high feed (0.1) produced lower surface roughness irrespective cutting parameters than dry and wet machining. Samples machined under cryogenic cooling produced lower surface defects as compared to flood and dry cooling [ 123 ]. In similar study cryogenic cooling using LN 2 at −197 °C has improved surface integrity [ 124 ]. Cryogenic machining produces better results than dry machining in turning of titanium alloy produced by additive manufacturing. Cryogenic machining can be applied in the biomedical field [ 125 ].
The cryogenic technique using SCCO 2 (Super critical carbon dioxide) is the best option for improving tool life as compared to dry and MQL conditions. This technique enhanced tool life performance 22% higher than SSCO 2 without lubricant. The use of SCCO 2 in cryogenic can be the ideal candidate for clean manufacturing of high thermal conductivity steel [ 126 ]. The long life of tool and surface quality was obtained in continuous spray mode using SCCO 2 cooling technique [ 127 ].
8.8. Limitations and solution for cooling techniques
All the techniques dry machining, cryogenic cooling, MQL and hybrid machining improve the sustainability related performance of machining processes. Cryogenic cooling enhances the machinability during various manufacturing processes. High cost of production of cryogen, lack of oxygen whilst working with cryogenic in case of leakage, low temperature in the pipes in the event of skin contact can cause severe burns, lack of lubricant, lack of chip evacuation and special set up requirement to deliver cryogenic coolant to the cutting zone are the limitations of cryogenic cooling process. In spite of these shortcomings cryogenic cooling is clean and healthy friendly technique. To overcome these limitations, optimal compressed air assistance can be provided for chip evacuation, for lack of lubrication optional MQL assistance can be incorporated. In dry machining the problems of tool failure arise due to high temperature at cutting zone is the limitation of dry machining. Machining operations such as tapping and drilling cannot be efficiently run dry due to chips accumulation. But coating based on TIN, TiCN and TiAlN have been developed to withstand more severe operating conditions. MQL is the most promising strategy that takes care of environmental, social and economic aspects of sustainable machining. It reduces the process cost by reducing the quantity of cutting fluid. It can be used for milling, turning, grinding and drilling processes. Eco-friendly fluids increase the effectiveness of MQL. Research is still required for ionic fluids with MQL for the turning, milling and grinding processes. The limitations of MQL machining are fine mist difficult to filter and not comparable chip evacuation as compared to wet technique. Air-blow off nozzle can be used to clear chips in MQL. Wet machining is preferred for harder metals like titanium steel etc. The main limitations of wet machining are environmental impact, health risk of workers with exposure of cutting fluid for a long duration and some cutting fluid corrodes machine parts. To overcome the limitation of wet machining flood coolant can be minimized by using MQL method. The main limitation of hybrid machining is the investment and implementation costs associated with the equipment. Lastly, hybrid manufacturing has the versatility to produce custom and complex parts.
9. Critical review on cutting fluids and cooling techniques
Metalworking fluids reduce the cost of machining operations and increase the life of tool, it is posing a very serious threat to the environment and health and safety to workers. As a result, there is huge pressure from environment agencies and global energy authorities to develop any other alternatives to cutting fluids and bio based alternatives. The conventional lubricants have given rise to health hazards such as allergy, skin infection and acute respiratory disorders etc. Disposal of cutting fluids is another major problem associated with the cutting fluids. The discharge of conventional cutting fluids can widely affect the environment due to harmful metal carry-off, oxygen depletion and decrease of nutrient in the soil. To eliminate these problems research is going throughout world to develop alternative cutting fluids. Sustainability of production of vegetable based oil is still questionable due to such factors as farm land use where crops are cultivated and soil fertility reduction. The susceptibility of metalworking fluids to biological contamination leads to health risks associated with hazardous microbial species encouraged researchers for more bio based alternative. MQL technique is a growing class of environmentally adapted lubricants. Today's oil-in-air MQL are appropriate for mild machining operations that do not require significant heat removal. To extend reach of more intense machining processes research is going on to develop new approaches. MQL has been switched from water based to gas based for the sake of environmental, health and economic benefits.
Das et al (2020) evaluated performance of various cutting fluids while hard turning steel using MQL technique. They reported that nanofluid performed the best as per cutting conditions than compressed air and water soluble coolant. Nano fluid produced the least chip serrations as compared to compressed air [ 128 ].
Maruda et al (2020) evaluated turning of AISI 1043 steel in terms of surface integrity and tribological properties using different cooling-lubricating techniques. The high number of seizures and adhesion were found on surface during dry machining, while small areas of adhesion and seizures were observed on surface during MQL. The surface after minimum quantity cooling lubrication with modification of extreme pressure anti-wear (MQCL + EP/AW) method was characterized by bronze adhesion. The instantaneous coefficient of friction and lowest temperature of surface was observed under MQCL + EP/AW method. A uniformly distributed thin layer of tribofilm prevailed on the surface. Using MQCL + EP/AW method Lowest values of sq (root mean square height) factor were observed on surface after turning, while highest values of parameters were obtained with MQL responsible for oil retention in mating parts [ 129 ].
Muaz et al (2019) carried out end milling of AISI 4340 steel under MQL technique using solid lubricant assisted cutting fluids. Four cutting fluids were selected and symbols designated as E; Pure emulsion of a water-based cutting fluid Suvocut S with oil-water ratio of 1:20. B; 10 wt% Boric acid dissolved in the emulsion E. G; 10 wt% Graphite mixed with the emulsion E. B+G; Mixture of lubricants in S. No. 2 and 3 in equal volumes. They revealed that inclusion of pure emulsion with MQL results in large resultant force while low forces were obtained when graphite was suspended in the emulsion or boric acid was dissolved may be due to low coefficient of friction of boric acid structure and low viscosity of cutting fluid as compared to other fluids as shown in figure 14 [ 130 ].
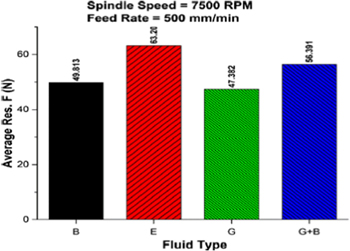
Figure 14. Comparison of fluids in terms of resultant force at optimum cutting parameters. Reprinted from [ 130 ], Copyright (2019), with permission from Elsevier.
Low forces too were obtained when graphite powder was mixed with MQL, however forces again increased with mixing of two powders in equal proportion owing to effect of boric acid was hindered with presence of graphite particles.
Shah et al (2021) evaluated machining performance using vegetable oil under ultra-high voltage electrostatic minimum quantity lubrication (EMQL) and MQL method. In new developed (EMQL) technology mist particles are charged by combining two technologies namely MQL and electrostatic spraying. EMQL showed better performance as compared to MQL as shown in figure 15 . Low value of R a observed at higher electrostatic voltage (EV) 20 and 25 kV. A higher value of R a was observed at low EV is due to obstruction of charged oil particle with tool and workpiece. The tool wear was decreased by 38% under EMQL at optimized EV of 20 as compared to MQL for 2400 mm cutting length as shown in figure 16 . The high performance was due to improvement in droplet quality and penetrability into the cutting zone [ 131 ].
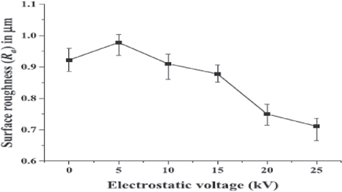
Figure 15. Variation in surface roughness ( Ra ) with a change in electrostatic voltage. Reprinted from [ 131 ], Copyright (2021), with permission from Elsevier.
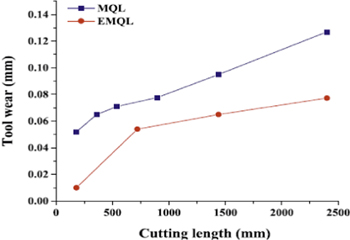
Figure 16. Comparison of tool wear in MQL and EMQL with a change in cutting length. Reprinted from [ 131 ], Copyright (2021), with permission from Elsevier.
Khan et al (2021) carried out turning of titanium alloy under MQL and liquid nitrogen assisted cryogenic method. They revealed that during dry cutting condition highest amount of power 885W was consumed. At flow rate of 0.4 L min −1 , 9.60% less cutting power and machining energy was consumed as compared to dry conditions. As flow rate was increased from 0.4 l min −1 to 5 l min −1 increase in cutting power was observed due to increase in hardness of work material as shown in figure 17 . The cutting power and machining energy was observed decreased under MQL method with increase of low rate from 50 to 200 ml h −1 . However, the power was not affected with further increase in flow rate. An effective lubrication system was provided by MQL system at optimum flow rate of 200 ml h −1 as shown in figure 18 [ 132 ].
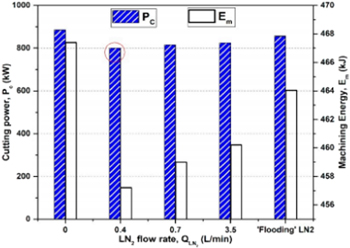
Figure 17. Influence of LN2 flow rate on cutting power and machining energy (vc = 70 m min −1 , ap = 0.8 mm; f = 0.1 mm/rev). Reproduced from [ 132 ], CC BY 4.0 .
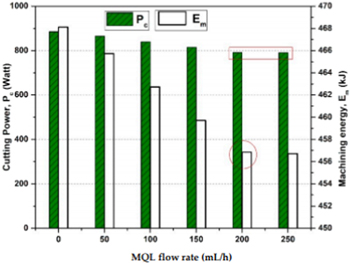
Figure. 18. Effect of minimum quantity lubrication (MQL) flow rate on power and energy consumption (vc = 70 m min −1 , ap = 0.8 mm; f = 0.1 mm rev −1 ; Pp = 0.5 MPa). Reproduced from [ 132 ], CC BY 4.0 .
10. Recommendations for future research
- 1. The study related to air quality in working space during machining using nanoparticles based MQL is not much explored. Also the effect of use nanoparticles in lubrication/cooling on workers is scant in published literature.
- 2. Determination of area of spread of cutting fluid under MQL has not been explored much also the mechanism of heat exchange during MQL using nanoparticles on the basis of heat transfer principles is still unexplored.
- 3. The work pertaining to surface integrity of machined workpiece surface which includes study of machined affected zone, generation of residual stresses and other metallurgical alteration during machining on the workpiece using MQL/Use of nanoparticles has not been studied much.
- 4. Investigation can also be focused on application of MQL with nanoparticles in drilling.
- 5. The modeling techniques pertaining to identifying the physics behind heat transfer using nanoparticles under MQL is still not available in open literature.
- 6. The safety viabilities and cost of implementation of cryogenic machining are yet to be investigated.
11. Conclusion
Preference of environmentally cutting fluids can be cost saving by eliminating wet cooling fluids from the machining processes. The environment legislation, inflation in cost of cutting fluids and increasing demand for robust, reliable, safer and faster cutting materials seeking for alternative cooling/lubricant methods. The following conclusion can be drawn from the review paper.
HPC technique turns in to a reliable solution for turning hard-to-cut materials. In turning HPC technique results in low cutting force, improved tool life and facilitates chip breakability. Ceramic and PCBN tools are not recommended for high speed machining in titanium alloys under HPC technique due to excessive wear. HPC is preferred to machine difficult materials titanium and steel. Cryogenic technology has shown benefits in reducing cutting force, power consumption and improved surface quality. In some of cases in turning high thrust values were observed using liquid nitrogen as coolant. The cryogenic machining has been potential to machine difficult materials such as titanium and hardened steel. The cryogenic technique using SCCO 2 extended tool life and surface quality in some of machining operations. Dry machining is the pre-eminent method being cheaper, environmentally safer, and most sustainable than other cooling/lubrication methods. The selection of appropriate tools and cutting parameters are vital for this method to use. It has limitations in drilling processes or difficult to cut materials where large amount of heat generates. Conventional lubricants should be replaced with biodegradable coolants as vegetable oils because they are less toxic and has ability to improve machine efficiency. Machining efficiency can be further improved under MQL/MQCL technique using vegetable oils. Use of solid lubricants, with MQL has shown promising results in improving tool life and surface quality of the product. Solid lubricant Mos2 has capability to reduce surface roughness due to strong adhesion. The inclusion of nano particles in cutting fluid with MQL showed a remarkable reduction in cutting force, surface roughness, friction angle, friction coefficient, chip thickness during machining. EMQL technology has shown capability to reduce surface roughness and tool wear. The good results were obtained with all types of coolant/lubricant techniques with coated carbide tools.
Acknowledgments
The author extended heartful thanks to IKG, Punjab Technical University Kapurthala, Punjab, India for supporting this study.
Data availability statement
All data that support the findings of this study are included within the article (and any supplementary files).
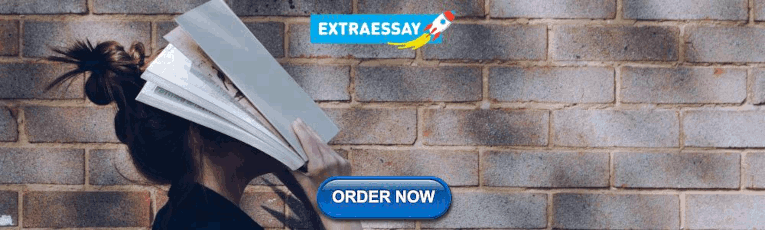
IMAGES
VIDEO
COMMENTS
In view of the preceding literature review, the aim of this study is twofold. Firstly, an appropriate numerical formulation for predicting the segmented chip formation is to be determined. ... (2008) An exploration of friction models for the chip-tool interface using an arbitrary Lagrangian-Eulerian finite element model. Wear 265:452-460 ...
For modeling of material removal of material caused by a machining process (chip formation), some important issues are: how the thicknesses of chips vary with tool geometry, how the thicknesses of chips vary with the friction between the chip and the tool, which influence has the work hardening behavior of the machined material, how the forces on a tool during cutting may be related to the ...
AURA1.pdf. 3. Conducting Literature. Introduction. Reviews. Rachel Show. This chapter will outline lhe general principles of the two main components of conducting a literature review: searching the literature and reviewing what you find. In each section, we guide you through the process, so lhat you will be able to perform your own literature ...
In this study, cutting tests were performed at cutting speeds ranging from conventional to high cutting speed, and tool-chip contact length, chip thickness, sticking and sliding contact phenomena and cutting forces were characterised. Twenty-two contact length models reported in the literature were evaluated and benchmarked to experimental data.
Selection and peer-review under responsibility of the International Scientifi c Committee of “9th CIRP ICME Conference†300 Ashwin Devotta et al. / Procedia CIRP 33 ( 2015 ) 299 â€" 304 The main focus of this study is to assess the ability to use chip curl as a validation tool for FE simulation evaluation. ... temperature ...
porates the effect of chip thickness, "n" and "K" to explain the mechanism of chip formation during machining. 2 Literature Review The influence of cutting parameters and tool damage on surface quality of the heat-treated steel was examined [1]. The steel was machined without coolant. They concluded that machined surface was strongly ...
A Survey of Network-On-Chip Tools. Ahmed Ben Achballah, Slim Ben Saoud. Nowadays System-On-Chips (SoCs) have evolved considerably in term of performances, reliability and integration capacity. The last advantage has induced the growth of the number of cores or Intellectual Properties (IPs) in a same chip. Unfortunately, this important number of ...
An upper bound analysis of free-chip machining has been carried out, where the tool cutting and friction forces were determined from the deformation energy dissipated during the chip separation process. The method employed was based on the classical upper bound theorem, as formulated by Prager and Hodge, and Drucker, Prager, and Greenberg, and its modification by Collins, to deal with the ...
Advances in screening and diagnostic lab-on-chip tools for gynaecological cancers - a review. Sadeka Nujhat a Department of Chemical Engineering ... The scope of this literature review is to report and compare some of the recent advances in gynaecological screening and diagnostic tools and their potential to be incorporated in the healthcare ...
A more recent review on tool-chip ... cutting tools is a modern application of surface structuring that has shown improvements in tribological phenomena at tool-chip interface. Literature suggests ...
The thermomechanical interaction of the tool with the chip in the most loaded secondary cutting zone depends on the contact length of the tool rake face with the chip. Experimental studies of the dependency of the contact length on the cutting speed, the undeformed chip thickness, and the tool rake angle, performed by the optical method, are used for comparison with the contact length obtained ...
In the literature review, ... Additionally, the high temperature near the tool-chip interface could be partly attributed to element distortion. During the chip formation process of the EPSC method, the elongated elements did not fail until the critical plastic strain was satisfied. Consequently, the elements near the cutting tool experienced ...
Received: 2 May 2020; Accepted: 16 June 2020; Published: 18 June 2020. Abstract: Following the advancements in microfluidics and lab-on-a-chip (LOC) technologies, a. novel biomedical application ...
LITERATURE REVIEW ON TURNING OPERA TIONS . Dr. Osama Mohammed Elmardi Suleim an Khayal . ... wet machining in terms chip-tool interface tem perature, chip formation, tool wear and .
A brief review of recent ChIP-Seq tools literature. 11-03-2008, 12:50 AM. Seems I can't go a week without finding a paper describing a new ChIP-Seq analytical tool, so I thought it would be helpful to put together a list of a few of the most interesting papers in this area. For those not familiar with ChIP-Seq, it involves massively parallel ...
This paper reviews the machining characteristics and tool wear mechanism of Duplex stainless steel. The Duplex alloy is a combination of Cr-Ni-Mo-Fe based alloys, it consist an equal grains proportion of γ-Austenite (FCC) and α-ferrite (BCC). Duplex stainless steel indicates the improved yield strength, corrosion resistance, better toughness ...
Full Article. A Review of Wood Machining Literature with a Special Focus on Sawing. Andrew Naylor,* and Phil Hackney. In this review, fundamental wood machining research is evaluated to determine the general cutting mechanics of simple, orthogonal, and oblique cutting tools. Simple tool force trends and chip formation characteristics are ...
ÐÏ à¡± á> þÿ ® ° þÿÿÿ¬ p ...
Summary. In the turning process, when a continuous chip is being produced, the increasing problems of adequate chip control resulting from the application of higher cutting speeds, are discussed. Although various techniques for controlling the chip have been developed, the most common method is to use obstruction or groove type chip forming ...
The cutting fluids also help in chip evacuation, prevent clogging of tool and BUE. Evacuation of chips depends on viscosity and flow rate of cutting fluids. Cutting fluids having higher viscosity are less capable to evacuate chips from machining zone as compared to less viscosity cutting fluids. Figure 2.
A Review on Artificial Intelligence Chip. P. Ebby Darney. Computer Science, Engineering. December 2022. 2022. TLDR. This study summarizes the need of the AI chips and its functionalities and how theAI chips varies from the general ICs and a discussion on the potential AI chip initiatives are provided. Expand.
In this study, cutting tests were performed at cutting speeds ranging from conventional to high cutting speed, and tool-chip contact length, chip thickness, sticking and sliding contact phenomena and cutting forces were characterised. Twenty-two contact length models reported in the literature were evaluated and benchmarked to experimental data.