
- Lean Philosophy
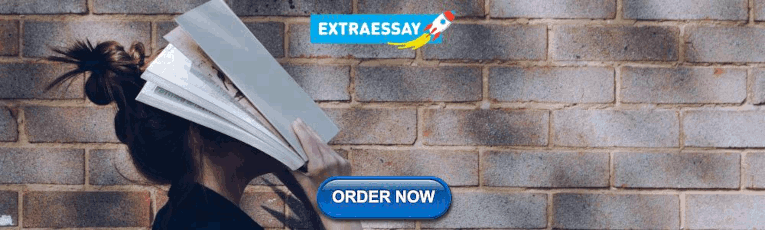
Eight Steps To Practical Problem Solving

The Toyota Way To Problem Solving
The art of problem solving is constantly trying to evolve and be re-branded by folks in various industries. While the new way might very well be an effective method in certain applications. A tried and true way of identifying and solving problems is the eight steps to practical problem solving developed by Toyota, years ago. The system is structured, but simple and practical enough to handle problems of the smallest nature, to the most complex issues.
Using a fundamental and strategic way to solve problems creates consistency within an organization. When you base your results off facts, experience and common sense, the results form in a rational and sustainable way.

The Eight Step Problem Solving Process
- Clarify the Problem
- Breakdown the Problem
- Set the Target
- Analyze the Root Cause
- Develop Countermeasures
- Implement Countermeasures
- Monitor Results and Process
- Standardize and Share Success
The eight steps to practical problem solving also include the Plan, Do, Check and Act (PDCA) cycle. Steps one through five are the planning process. The doing is found in step six. Step seven is the checking . Step eight involves acting out the results of the new standard.
This practical problem solving can be powerful tool to issues facing your organization. It allows organizations to have a common understanding of what defines a problem and what steps are going to be taken in order to overcome the problem efficiently.
The Eight Steps Broken Down:
Step 1: clarify the problem.
A problem can be defined in one of three ways. The first being, anything that is a deviation from the standard. The second could be the gap between the actual condition and the desired condition. With the third being an unfilled customer need.
In order to best clarify the problem, you have to see the problem with your own eyes. This gives you the details and hands-on experience that will allow you to move forward in the process.
Step 2: Breakdown the Problem
Once you’ve seen the problem first hand, you can begin to breakdown the problem into more detailed and specific problems. Remember, as you breakdown your problem you still need to see the smaller, individual problems with your own eyes. This is also a good time to study and analyze the different inputs and outputs of the process so that you can effectively prioritize your efforts. It is much more effective to manage and solve a bunch of micro-problems one at a time, rather than try and tackle a big problem with no direction.
Step 3: Set the Target

Step three is all about commitment and focus. Your attention should now turn towards focusing on what is needed to complete the project and how long it will take to finish. You should set targets that are challenging, but within limits and don’t put a strain on the organization that would hinder the improvement process.
Step 4: Analyze the Root Cause
This is a vital step when problem solving, because it will help you identify the actual factors that caused the issue in the first place. More often than not, there are multiple root causes to analyze. Make sure you are considering all potential root causes and addressing them properly. A proper root cause analysis, again involves you actually going to the cause itself instead of simply relying on reports.
Step 5: Develop Countermeasures
Once you’ve established your root causes, you can use that information to develop the countermeasures needed to remove the root causes. Your team should develop as many countermeasures needed to directly address any and all root causes. Once you’ve developed your countermeasures, you can begin to narrow them down to the most practical and effective based off your target.
Step 6: Implement Countermeasures
Now that you have developed your countermeasures and narrowed them down, it is time to see them through in a timely manner. Communication is extremely important in step six. You’ll want to seek ideas from the team and continue to work back through the PDCA cycle to ensure nothing is being missed along the way. Consider implementing one countermeasure at a time to monitor the effectiveness of each.
You will certainly make mistakes in throughout your problem solving processes, but your persistence is key, especially in step six.
Step 7: Monitor Results and Process
As mistakes happen and countermeasures fail, you need a system in place to review and modify them to get the intended result. You can also determine if the intended outcome was the result of the action of the countermeasure, or was it just a fluke? There is always room for improvement in the problem solving process, but you need to be able to recognize it when it comes to your attention.
Step 8: Standardize and Share Success
Now that you’ve encountered success along your problem solving path, it is time to set the new processes as the new standard within the organization and share them throughout the organization. It is also a good time to reflect on what you’ve learned and address any possible unresolved issues or troubles you have along the way. Ignoring unresolved issues will only lead to more problems down the road.
Finally, because you are a true Lean organization who believes continuous improvement never stops, it is time to tackle the next problem. Start the problem solving process over again and continue to work towards perfection.
Additional Resources
- 8D for Problem Solving – creativesafetysupply.com
- Training to Use 8D Problem-Solving Tactics – blog.creativesafetysupply.com
- The Great Root Cause Problem Solving Debate – realsafety.org
- Design Thinking: Empathy and Iteration for Innovation and Problem-Solving – creativesafetypublishing.com
- 10 Commandments to Continuous Improvement – lean-news.com
- Lean Manufacturing Implementation – The First 5 Steps – iecieeechallenge.org
- No Problem is a Problem – jakegoeslean.com
- The Transitional Steps Involved In The 5s Principles During Implementation – 5snews.com
- The Tools of Kaizen – blog.5stoday.com
Related posts:
- 3P and Lean
- The Vacation Paradox
- Why Single Minute Exchange of Die (SMED)?
- Total Quality Management And Kaizen Principles In Lean Management
- An Engaged Employee is a Productive Employee
- Jim Womack’s Top Misconceptions of the Lean Movement
- Muda, Mura, and Muri: The Three Wastes
Toyota’s 8 Step Practical Problem Solving, Revisited
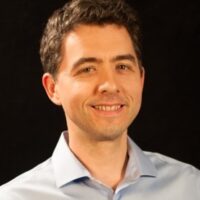
- It is too early to talk about solutions.
- It is still too early to talk about solutions.
- Did someone mention countermeasures?
- Yes, now we can talk about solutions.

Jon has dedicated his 25+ year career to the field of kaizen, continuous improvement, and lean management. Jon spent the first eighteen years of his life in Japan, then graduated from McGill University with a bachelor’s in linguistics.
Mohamed Abbassi
What the best book & preactice for lean manufacturing
Ron Pereira
Lots of great books out there! The new edition of the Toyota Way by Jeff Liker would be a good place to begin. Here’s a podcast where he talks about the book.
https://blog.gembaacademy.com/2021/02/04/ga-357-revisiting-the-toyota-way-with-jeff-liker/
Completely agree. Very good analogy
DIDIER RABINO
Totally agree! I also learned that “solutions” only exist in maths. There is always a better way.
Have something to say? Cancel reply
Leave your comment and let's talk!
Save my name, email, and website in this browser for the next time I comment.
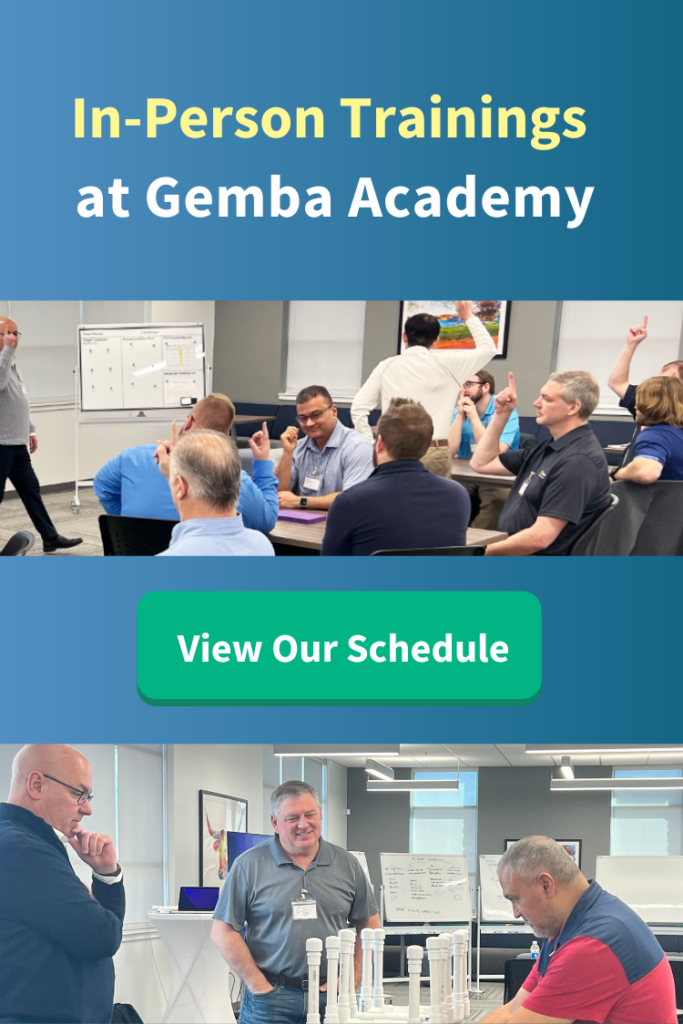
Recent Articles

Enhancing Organizational Efficiency through Supplier Process Improvement

GA 524 | Connection Before Correction with Royden Johnson

GA 523 | The Cleveland Clinic Improvement Model with Tim Pettry

GA 522 | Continuous Improvement at Jack Henry with April Bell

GA 521 | Celebrating Quick Wins with Alen Ganic
Start your lean & six sigma training today..
A3 8 Step Practical Problem Solving – Skill Level 1: Knowledge
How the a3 came to be toyota’s go-to management process..
by Isao Yoshino August 2, 2016
The discussion below between John Shook and Isao Yoshino first appeared on The Lean Enterprise Institute website www.lean.org .
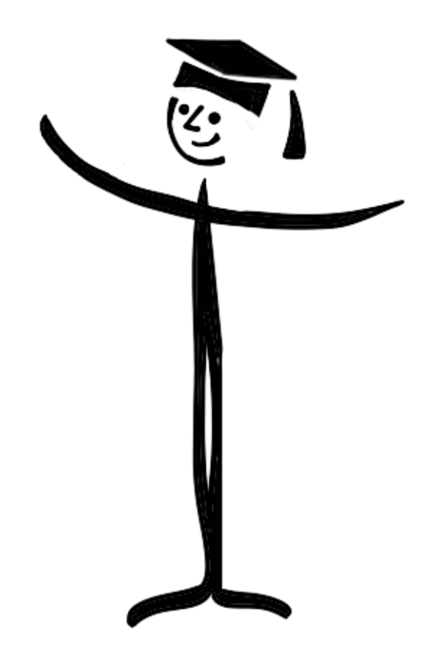
As context, John Shook defines the A3 process as “… the A3 is a visual manifestation of a problem-solving thought process involving continual dialogue between the owner of an issue and others in an organisation. It is a foundational management process that enables and encourages learning through the scientific method.” pp11 of Managing to Learn
Understanding A3 Thinking has evolved over time. In 2016, John said he would change the term “scientific method” to “scientific thinking” in that definition because the scientific method is but one of a number of ways of structuring to do science. In addition, John clarified that the A3 process is a process to help teams do science together. It’s much more than a structure for a problem solving process – it can become a way of enabling people to work together effectively.
The history of the A3 process provides context. Context to the “problem(s)” Toyota was attempting to solve by developing such a process. You may not have exactly the same problems as Toyota did when it started its journey, but we are sure any organisation will be more successful if they are deliberate in the development of management skills, capability building and thinking. It’s not enough just to hire great people, we need to build capability and behaviours over time.
We hope you find that this interview helps you think through why developing such processes are so important.
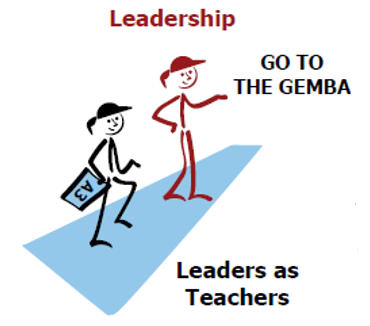
In the late 1970s, Toyota decided to invest in cultivating the managerial capabilities of its mid-level managers. Masao Nemoto, the same influential executive who led Toyota’s successful Deming Prize initiative in 1965, led a development program especially for non-production gemba managers called the “Kanri Nouryoku Program” – “Kan-Pro” for short. Nemoto chose to structure this critical management development initiative around the A3 process.
The A3 is well established now in the lean community. As a process, as a tool, as a way of thinking, managing and developing others. The question often comes up of where did it come from and how did it become a common practice. The basic answer is that it dispersed mainly from Toyota. But how did it become so prevalent in Toyota? And how did it evolve from its humble beginnings as a tool to tell a PDCA quality improvement story on an A3-sized sheet of paper, as it had been commonly used by many Japanese companies since the 1960s?
What had started as a simple tool to tell PDCA stories grew at Toyota into something more: the A3 process came to embody the company’s way of managing in an extraordinarily profound sense. How did this happen?
My first “kacho” (manager) at Toyota (in Japan starting in 1983), Mr. Isao Yoshino, was a member of Nemoto’s four-man team that created and delivered the “Kan-Pro” manager-development initiative that directly answers that question. The program has been unknown outside Toyota … until now.
—John Shook

Interview with Mr. Isao Yoshino
Q: what was the purpose of the kanri nouryoku program.
A: The main purpose was to nurture “Management Capabilities” of employees who were at manager (kacho) level and above. There were four rudimental capabilities for managers:
- Planning capability, judging capability
- Broad knowledge, experiences and perspectives
- Driving force to get job done, leadership, kaizen capability
- Presentation capability, persuasion capability, negotiation capability
Q: Why did Toyota decide it needed this program?
A: After introducing Total Quality Control (TQC) in 1961 and receiving the Deming Prize in 1965, TQC-based perspective had taken root widely across the company. In the late ‘70s, Mr. Nemoto (one of the main people behind launching TQC) noticed that management capabilities and TQC awareness was decreasing among managers, particularly within the non-manufacturing gemba or office divisions. Mr. Nemoto decided to take actions to reinvigorate the managers (especially administrative) and help heighten awareness of their role. And so, in 1978, he formed a task force that promoted a two-year program (the Kanri Nouryoku Program) for two thousand managers from all over the company. I was one of the four staff members on the task force in Toyota City.
Q: What sort of tools and activities did the Kanri Nouryoku employ?
A: All the managers went through “a presentation session” twice per year (June and December). The officers in charge of each department attended to have a Question and Answer session with the managers. Officers tried to focus on the problems each manager was facing as well as the effort and process needed to solve the problems. Officers focused more on “What is the major cause of the problem?”, rather than “Who made those mistakes?” This problem-focused attitude (as opposed to the who-made-the-mistake attitude) of the officers encouraged managers to share their problems rather than hide them.
The key to giving the presentations was that they had to be done using an A3. The managers learned how to select what information/data was needed and what was not needed, since an A3 has only limited space. This helped them acquire the seiri and seiton functions of the 5S concept as applied to knowledge work. A3 was also a great tool for officers. They could easily see, at a glance, all the key points that the presenter wanted to convey. As it is just one single document, you can quickly see from the left top corner to the right bottom of an A3 and grasp the key things the writer wants to communicate. This is something that you cannot get from a written document or PowerPoint presentation.
Q: What was your personal experience with the program?
A: First, I was fortunate to get acquainted with many admirable managers, who inspired me in many ways. I also learned how to express myself more effectively by studying A3 documents from two thousand managers. Strikingly, I discovered that managers whose A3s were excellent were also excellent managers at work.
Nemoto-san highly praised managers who took a risk to report their mistakes (not success stories) on A3s with a hope of finding a solution. Nemoto valued their sincere and proactive attitudes. “Nemoto Lectures” were held for managers three or four times a year. Mr. Nemoto went through every single impression memo from the audience as feedback for his next speech.
Mr. Nemoto also appreciated the efforts by managers who tried to nurture excellent subordinates. This created a new company-wide notion that “developing your subordinates is a virtue.” It was amazing to see managers in their 40s and 50s willing to give 100 percent of their energy to work on hoshin kanri and A3 reporting, because they were convinced the program was practical and useful and worth using to bring themselves up to a higher level. Seeing all this happen at work truly helped me grow professionally.
Q: What was the effect of the program on Toyota?
A: Well for one, every mid-level manager who was involved in this program over the two years came to clearly understand their roles and responsibilities and also learned the importance of the hoshin kanri system. People at Toyota don’t hesitate to report bad news, which has been Toyota’s heritage since day one. The Kanri Nouryoku program has further reinforced this tradition because of its praise toward managers and others who were honest about their mistakes. And after the program was implemented to the back-office managers, the level of their awareness of their role rose up to the same level of that of manufacturing-related managers, which significantly strengthened the management foundation.
Everybody became familiar with using the A3 process when documented communication was needed – A3 thinking eventually became an essential part of Toyota’s culture. People learned how to distinguish what is important from what is not.
Isao Yoshino
Lecturer , Nagoya Gakuin University
Isao Yoshino is a Lecturer at Nagoya Gakuin University of Japan. Prior to joining academia, he spent 40 years at Toyota working in a number of managerial roles in a variety of departments. Most notably, he was one of the main driving forces behind Toyota’s little-known Kanri Nouryoku program, a development activity for knowledge-work managers that would instill the A3 as the go-to problem-solving process at Toyota.
Now move onto the next Topic
- Find a Dealer
- MyToyota Login
- Parts & Services
- Resource Library
About Toyota
Electric forklifts.
Electric Pallet Jacks
Electric Pallet Stackers
Reach Trucks
Order Pickers
Internal Combustion: Cushion Tires
Internal Combustion: Pneumatic Tires
Heavy Duty Forklifts
Tow Tractors & Tuggers
Hand Pallet Jacks
Automated Guided Vehicles
Aerial Work Platforms
- Toyota Assist
- Smart Environment Sensor
- Rental & Used
- Find a Forklift
- Compare Forklifts
- Industry Solutions
- Automation Solutions
- Energy Solutions
- Consulting Solutions
- Financial Solutions
- Fleet Solutions
Food Storage
General Warehouse
Cold Storage
General Manufacturing
Building Materials
Automate Receiving Processes
Automate Material Transportation
Automate Storage Systems
Automate Picking Solutions
Automate Shipping Systems
Become a Greener Business
Lithium-Ion Batteries
Convert from IC to Electric
Analyze Warehouse Space
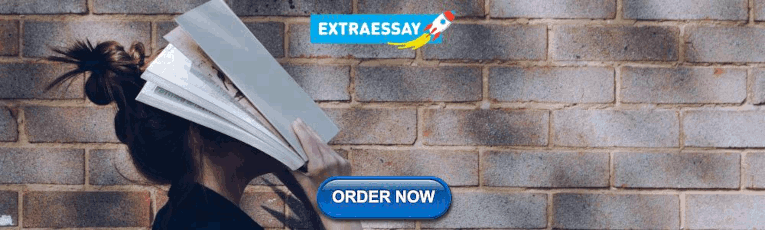
Increase Employee Education
Improve Operation Safety
Improve a Process
Toyota Commercial Finance
Financing with Toyota
MyToyota Credit Card
Benefits of Buying Toyota
Highest Quality Parts
Toyota forklift dealers are a one-stop-shop, full service forklift solutions provider.
- Model & Serial Number
- Part Number
How to Find Your Equipment Model Number
Finding the right parts for your equipment is easy when you have your model and serial number which can be found on the data plate. Luckily, a forklift data plate is installed on every truck on the market to help you understand what your forklift can do and provide vital information.
Model Number: The model number of your toyota forklift is extremely important for relaying information to your dealers about repair or technical assistance and for looking up replacements part!
Serial Number: The serial number on your lift is the most important number.The model serial number combination will allow us to provide you with the parts that will fit your particular piece of equipment.
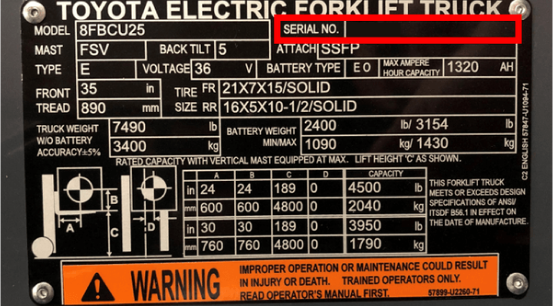
How to Find Your Equipment Serial Number
Model Number: The model number of your toyota forklift is extremely important for relaying information to your dealers about repair or technical assistance and for looking up replacements part!
Serial Number: The serial number on your lift is the most important number.The model serial number combination will allow us to provide you with the parts that will fit your particular piece of equipment.
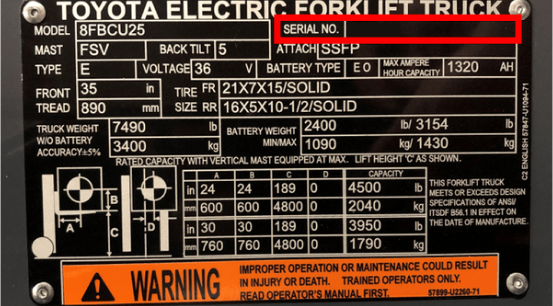
Need some help? For further assistance or more information, contact your local Toyota Dealer .
- Request a Parts Quote
- Toyota Genuine Parts
- Toyota Starlift Parts
Industry Leading Service
Increase your productivity, overall up-time and lifespan of your forklift.
- Request Service Quote
- Maintenance Plans
- 360 Support
- All Resources
- Customer Stories
- Whitepapers
- Management Guides
- Video Library
Toyota Careers
Management Team
Toyota Dealers
Sustainability
Corporate Social Responsiblity
- National Accounts
- Toyota Production System
- Forklift Safety
- Toyota Powered Engines
Press Enter to Search
Problem Solving Through Toyota Lean Management
Albert Einstein once wrote, “We cannot solve our problems with the same thinking we used when we created them.” Simply put, coming up with creative and innovative solutions to problems oftentimes requires you to look at the problem with a fresh perspective. As we’ve discussed in previous Toyota Lean Management blog posts , recognizing and cutting down on waste is critical to increasing your efficiency, reducing costs, and improving throughput. However, in order to make these improvements and see positive changes in ROI, a key step is recognizing where problems exist and working to solve them.
To recognize and solve these problems, it is often helpful to view them with a different lens to reach a newfound conclusion. Toyota’s 8 steps for problem-solving act as the lens that allows you to view different aspects of your operation from a new perspective.
Consider these eight steps as you start on the path to continuous improvement.
1. Clarify the problem
The first step in solving a problem is realizing that one exists. You can define a problem by asking yourself the following questions:
- Does my current process deviate from the standard?
- Is there a gap in my current process with what I am trying to accomplish vs. what I am accomplishing?
- Are my customer’s needs being met with my current process?
If the answer to any of these questions is no, then you know you have a problem that could use some improvement.
2. Break down the problem
Now that you’ve verified the problem, you can begin to break down the issue into smaller, more detailed pieces. It can be helpful to analyze the different inputs and outputs of your process so you can effectively see where you are currently placing your efforts. Don’t bite off more than you can chew. It is much easier to manage and solve smaller problems rather than attack one large problem with little direction.
3. Set a target
The third step is all about commitment and consistency. Now that you’ve broken down the problem, how are you going to go about solving it? How are you going to meet your new deadline, and how long will it take to complete? Allot adequate time for each activity to ensure you are giving each aspect of the project enough attention.
4. Analyze the root cause
Analyzing the root cause allows you to identify each of the factor(s) that caused a problem in the first place. Sometimes there is more than one cause, and it is important to consider each one as you work to address the issue.
5. Develop countermeasures
Establishing the root cause is only half the battle. Now, you must develop countermeasures for each of those root causes to prevent the same issues from occurring again.
6. Implement countermeasures
Now that you’ve established your countermeasures, it is time to put them into action. You may want to seek ideas from other team members to ensure you are not missing any steps. Also, it can be helpful to track how effective each countermeasure is performing along the way and making adjustments where necessary.
7. Evaluate Results and Process
The seventh step is all about implementing a system to review and evaluate how your new process is working. Countermeasures will fail, but it is important to develop an effective system that always looks for areas of improvement in order to reach the desired result.
8. Standardize Successful Processes
After receiving successful results from your previous evaluation, it is time to standardize the process within your team and the entire organization. As you work through the standardization process, continue to look for possible unresolved issues that you may have missed the first time.
Remember, the road to establishing a lean organization doesn’t stop once you improve a few processes. Lean isn’t just about identifying where you can do better; it’s about instilling a culture of respect and developing to create a workplace that your associates enjoy working in. Achieving business goals and leaner processes requires dedication and teamwork from every individual in the organization. Encourage open communication and empower your employees to bring problems to your attention when they are detected.
Related Articles

Toyota Practical Problem Solving (PPS)—Countermeasures and Implement

A Quick Recap

- Clarify the Problem
- Break Down the Problem
- Set a Target
- Root-Cause Analysis
Develop Countermeasures and Implement
- Monitor Process and Results
- Standardize and Share

Developing Multiple Countermeasures
Developing, or at least considering, multiple countermeasures is actually quite common at Toyota. In the West, the first solution is often followed through, no matter how good the solution actually is. At Toyota, they often consider multiple solutions and compare them.

Hence, let your creativity run wild and think of anything you can that could improve the root cause for your problem. Don’t worry too much about the feasibility (yet), since this will be looked at during the next step. Similar to brainstorming, there are no bad ideas, as any idea with not-so-much potential could be an inspiration for an even better idea. More is clearly better here. Do this for all of your root causes.
Selecting Countermeasures

Hopefully you have more than one countermeasure for every one of these root causes you identified. If you have multiple root causes, some countermeasures may impact only one root cause, while other countermeasures impact multiple root causes. Now you need to pick which root causes you actually want to implement.
You may not need to look at eighty different possible solutions to resolve your root cause. But you should definitely take more than one solution under consideration. Look at multiple ideas on how to resolve the root cause, compare them, and pick the most promising ones for implementation. When comparing different solutions, you should consider how effective the solution will address your root cause(s), but you should also consider factors like safety , quality , productivity , cost , timing , and the ease of implementation , as well as its impact on other functions . It is probably best to make a table here with one row for every countermeasure and one column for these performance parameters.

Also, do not to get sidetracked to implement something completely different just because it is a nice idea; instead, make sure that your possible actions do improve the root cause! Additionally, try to see it from the view of different stakeholders, answering the question “What is in it for me?” from the point of view of the customer, company, employee, and also yourself. For the Prius, they went with a single final and most promising concept, as they wanted to design only one car model. For your problem-solving, you could implement multiple solutions.

It is really helpful to also build a consensus here, including employees, management, and other impacted departments. This will greatly improve the acceptance of your countermeasures. But if you did the right thing and already involved these stakeholders while clarifying the problem, breaking down the problem, setting a target, doing the root cause analysis, developing countermeasures, and evaluating them, then these stakeholders should already be on board and supportive of your plans. Also consider who has to be informed and who has to approve.
Based on this, you should create a plan for which solution to implement or try out first (probably the most-promising one/highest-value-adding one unless there are other reasons not to), which one second, and so on. For each you should decide what needs to be done by whom and by when.
And then, finally, just do it! Follow through with your plan and implement or at least test these countermeasures. In my next post we will look at the “Check” and “Act” parts of PDCA, where we monitor the process and results as well as standardize and share the learning. Now, go out, do something about your problems (preferably the right thing after a thorough “plan” of PDCA), and organize your industry!
PS: Many thanks to the team from the Toyota Lean Management Centre at the Toyota UK Deeside engine plant in Wales, where I participated in their 5-day course. This course gave us a lot of access to the Toyota shop floor, and we spent hours on the shop floor looking at processes. In my view, this the only generally accessible course by Toyota that gives such a level of shop floor involvement.
6 thoughts on “Toyota Practical Problem Solving (PPS)—Countermeasures and Implement”
Christoph thank you again for one more “very rich” article. I’m not sure if what I’ll said is really correct or not since I didn’t find a definition in the “Lexical Lean” book about the word “Countermeasure”. In my understanding the meaning of “countermeasure” is some action to improve the current status, not exactly “solving” the problem to assure it’ll no more happen again, as the definition for “corrective action” in the ISO9000 standard. In this way the mindset is the continuous improvement, always pursuing the perfection, doing the PDCA runs very quickly and all the time. Is my understanding correct?
Hello Mario, I think this is a question of wording. At Toyota, improvement almost always starts with a problem to be resolved. This could be for example a defect (clearly a problem), or merely to improve cost (a wider definition of a problem). Generally, for Toyota, a problem is any situation that is not how it should be. The difference to ISO9000 seems to be only wording (although I am neither familiar with nor a fan of ISO 9000)
Interesting! Frankly, I’m out of all this now having retired a few years ago, but what is meant under the PDCA headings seems to vary a lot. Briefly: P – involved defining the problem and installing temporary c’measures and mapping out the game plan with 5Ws+1H. D – was gathering & analysing data; considering possible cms and planning trials. C – was trials & checking A – was installing new standard, maiuntenbance procedures and process review. A 12-step PDCA was developed at NMUK as the ‘process’ for kaizen teams, and a similar problem solving process adopted. Further afield, Ford used an 8D process, and there were others. All worked if applied as intended, but understanding and application varied, and if permanent countermeasures were not forthcoming it was usually the process rather than the practitioners that was blamed. I would say that the number of steps is significant – too few and they become too general and open to (mis)interpretation; too many and people want to take short cuts.
Hi Steve, PDCA is sometimes defined slightly different, but the source of the above is straight from Toyota. But I have also seen the root cause analysis as part of the “do” section.
As for the 12 steps from NMUK (Nissan Motor UK), my source is from the UK, but from Toyota (TMUK, Deeside), and they teach an 8 step process (1 Clarify the problem; 2 Breakdown the problem; 3 Set a target; 4 Analyse the root cause; 5 Develop countermeasures; 6 See countermeasures through; 7 Monitor the process and results; 8 Standardise successful processes; ) For this post series I found it better to merge step 5 and 6, and hence here you find only 7 steps. The 12 steps seem to be very similar, but a bit finer graded (1. Select theme ; 2. Give reasons ; 3. Set targets ; 4. Plan activity ; 5. Gather data ; 6. Analyse data ; 7. Consider solutions ; 8. Plan trials ; 9. Conduct trials ; 10. Standardise changes ; 11. Review the process ; 12. Further improvement;) Either works. Thanks for the input 🙂
Best re-read “The Toyota Way” pp254 and 255 before p256 and also ISO 9001:2015 Clause 10 “Improvement” and 10.1 “NOTE” on for examples of Improvement and where is fits / is the step as in the Toyoya PPS: “Clarify the Problem Break Down the Problem Set a Target Root-Cause Analysis”
This is true in Toyota as stated above but they use and many others now: use:
“Concern” (The ‘problem’ with supporting evidence and statistical / graphical analysis to clearly define such “Pareto / Juran” being the most common in Toyota – “The Toyota Way” p255) “Containment” (to protect the customer and other stakeholders impacted by the Problem / Concern) “Causes (Dr Ishikawa’s 2 types of Basic Causes Analysis for Event Problems and more useful in production, his Type 3 “Process Classification” C&E Diagram – Ishikawa NEVER called his Type A and B Cause Analysis Diagrams the common term of “Fishbone Diagrams”. See his “Guide to QC” ~ 1962 and “Introduction to QC” 1989 books); THEN, “Containment” Finally “Corrective Action” (See ISO 9000:2015 “Action” on page 45.)
Of course all such problems and causes should have been identified in the PFMEA and as The Toyota Way Book says on p255 “comparing actual situation to the standard”. Otherewise there is no problem without a Standard.
Hello MWMcLean, just grabbed my copy of the Toyota Way, and indeed on pg 256 are quite similar. Differences are that at Toyota 1) they clearly define a prioritized target, 2) root cause analysis is not only 5 why (which i find suitable mostly for smaller problems) and 3) at the end Toyota shares the ideas with other plants/locations. Either works. Not sure where the difference comes from, maybe Toyota evolved the method since 2004 (when the book was printed) to 2023 (when I got the info directly from Toyota).
Making a sequence with all “C” words (concern, containment…) is interesting, but for me more confusing than the “normal” text. Thanks for sharing!
Leave a Comment
Notify me of new posts by email.
People, Purpose, Performance - Future State Consulting
- Facilitation
- Tools and Tips
- Audio and Video
- Books and Articles
- About James
Toyota 8 Step Practical Problem Solving Process
Click the link below to read an explanation of the Toyota 8 Step Practical Problem Solving Process as a PDF:
Toyota 8 Step Practical Problem Solving Process PPS TBS
Join our mailing list
Recent tweets.
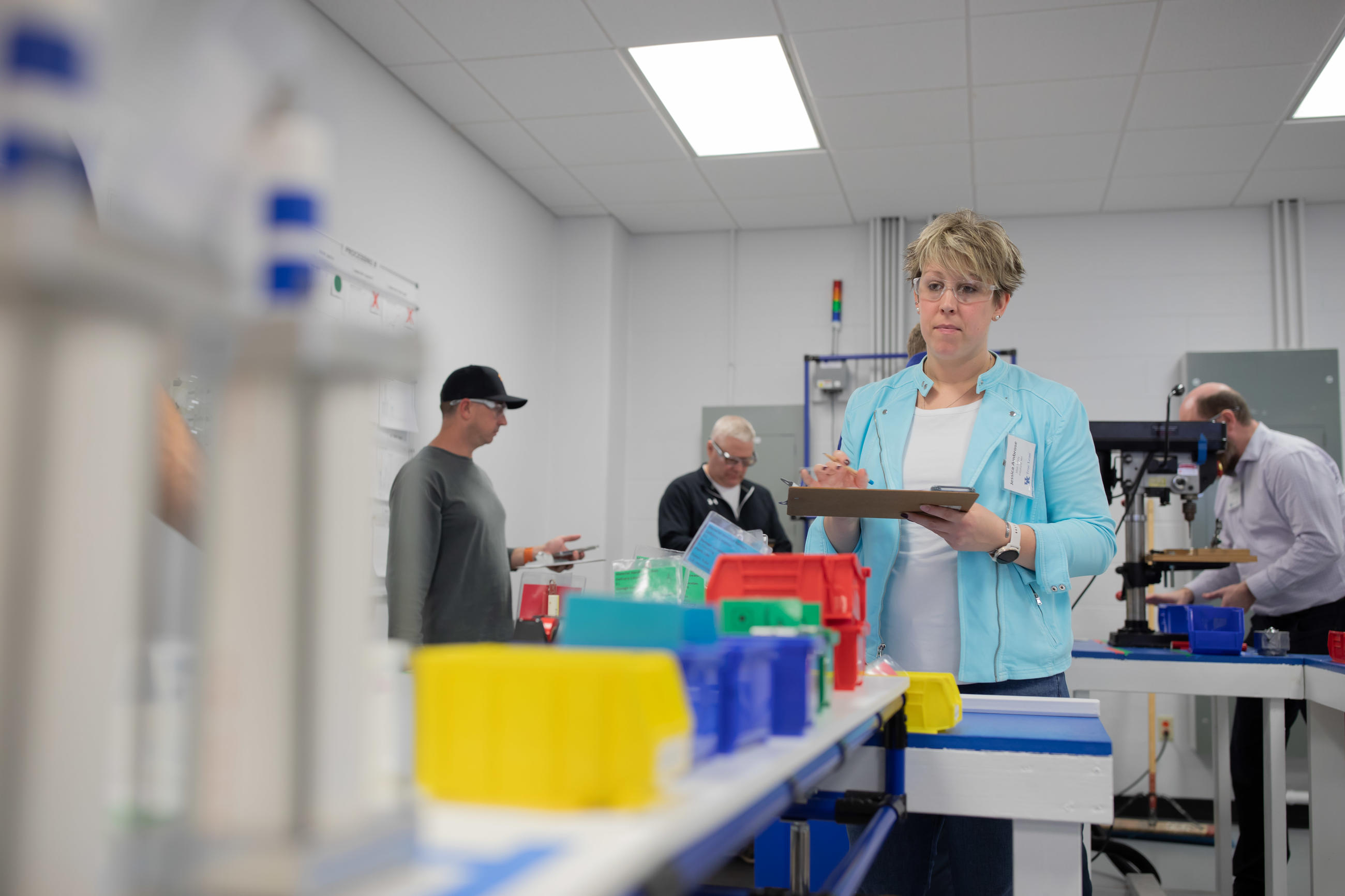
Eight-Step Problem Solving
Systematic problem-solving is a core element of a True Lean™ organization. This course teaches the 8-Step problem-solving method used within Toyota at all levels and functions to practice effective continuous learning and improvement. We use a learn-by-doing format as teams will work through real problems selected within their organization and be coached through the process to achieve tangible results while developing their problem solving and critical thinking skills. Properly implemented, this systematic problem-solving approach delete: also becomes integral to the organization’s behavior habits at all levels that support the True Lean™ culture.
Designed for
Organizational Professionals at all levels and Departments
The knowledge you will gain
- Guiding Principles behind the Eight-Step methodology
- Understanding the universal application for all functions and all levels in your organization.
- The role and use of “A3 documents” separate from the problem-solving itself.
- Utilizing Eight-Step to return to a proven performance level OR advance the performance level. Both deliver tangible results.
- Application of temporary measures and long-term countermeasures to prevent recurrence and achieve sustainable improvements.
- How it engages all to “own their workplace” and drive positive moral and personal development.
Interactive with Gap Analysis “Takeaway”
- This interactive session includes dynamic learning with open discussions
- Participants will learn the 8-step process and how to write an A3 summary using real problems from their workplace.
- Participants will be able to describe the philosophy, principles, and practice of the methodology and determine their needs-based next steps
Coaching Available
- Executive and Operational Coaching for Individuals based on the organizational level
- Ongoing needs-based Coaching on Eight-Step Problem Solving
Registration Information
Dates: September 19 – 20, 2023 Location: Virtual Fee: $1,995 per participant
Register Today
For information on fees for a dedicated session, contact [email protected] .

8 Steps to Problem Solving: Implement Continuous Improvement in Your Organization
The 8 Steps to Problem Solving Method was developed by Toyota Motor Corporation as a practical, structured, and simple way to handle any problem from the smallest issue to the most complex roadblock.
What is the 8 Step Problem Solving Method?
This problem-solving method helps teams identify and solve problems in a clear and structured way, ensuring that there is consistency within an organization.
This process is an expansion of the Plan, Do, Check, and Act (PDCA) cycle. Steps one through five are part of the planning process, step six is the doing process, step seven is the checking process, and step eight is the acting part of the cycle.
Following this method ensures that your problem-solving technique can be repeated in a sustainable way with the least amount of impact on your customers.
What are the benefits of the 8 Step Method?
There are a few key benefits to using this method to solve your problems:
You get to the root cause of the issue, ensuring the problem is not repeated in the future.
You can better identify and prevent any weak points in your process.
Long-term, effective solutions are generated.
Problems will be reduced over time, increasing your bottom line.
What are the 8 Steps in this Methodology?
Clarify Problem
Break Down Problem
Root Cause Analysis
Develop Countermeasures
See Countermeasures Through
Monitor Results and Processes
Standardize Successful Process
A Detailed look at the 8 Steps to Problem Solving Templates
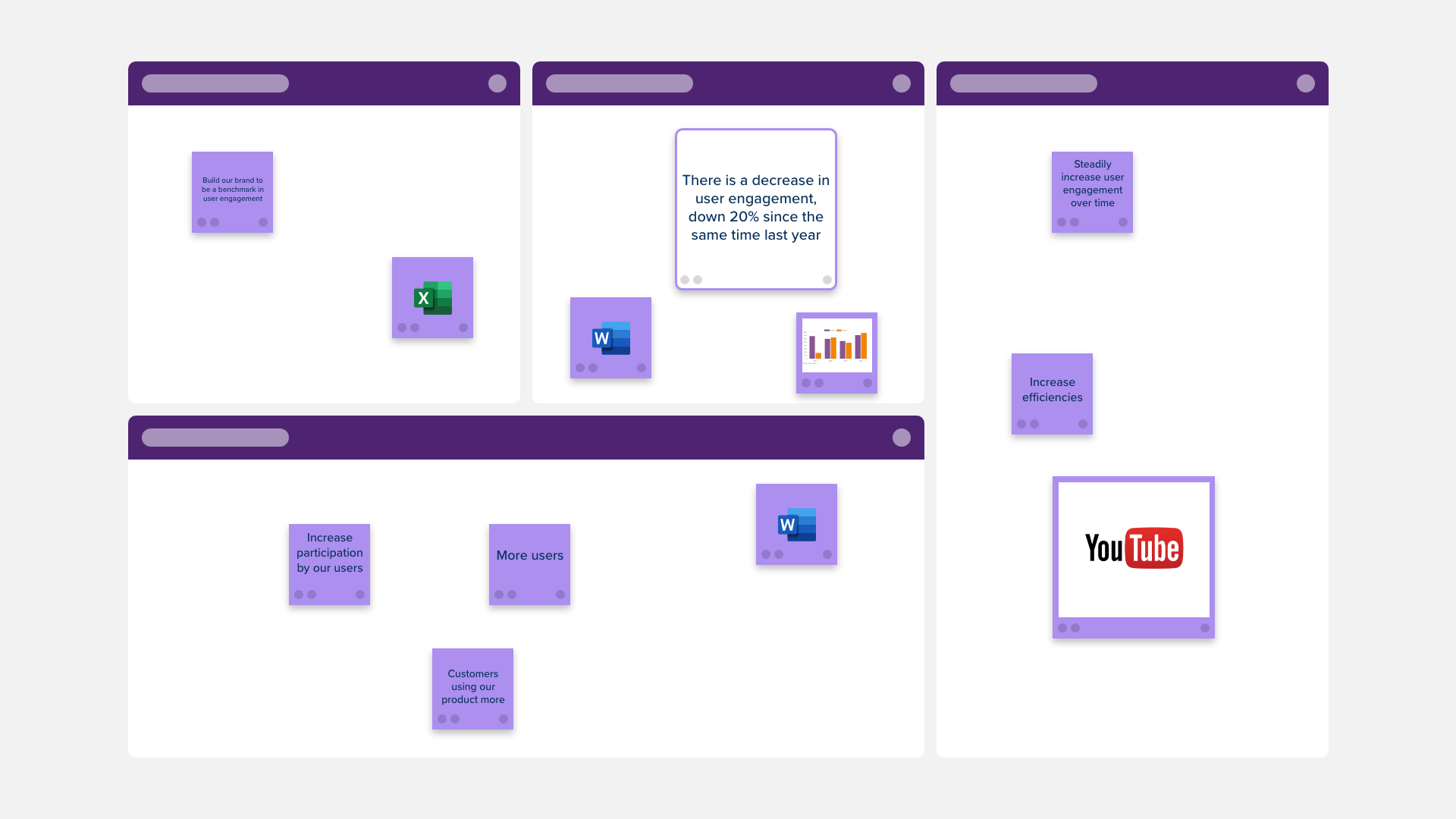
Step 1: Clarify The Problem
In this step, you need to identify and clarify the problem. Determine why it is a problem, what should be happening instead, and how it fits into the business as a whole.
The Stormboard Template for this step is divided into four sections: Clarify Ideal Situation, Clarify Current Situation, Visualize Gap Between Current and Ideal Situations, and Set Ultimate Goal.
Step 2: Break Down The Problem
For this next step, you need to start getting more detailed and specific. Break down the problem into manageable pieces, go see the problem in the process, analyze the issues, and start thinking about priorities.
The Stormboard Template for this step is divided into three sections: Get Your Boots On and Go See, Create a Process Flow, and Identify Point of Occurrence.
Step 3: Set Your Target
This step is where you set clear target dates to resolve the problem. Determine what is needed to reach the target and how long it will take.
The Stormboard Template for this step is divided into three sections: Measurability, Target Point of Occurrence, and What, How Much, and When.
Step 4: Perform a Root Cause Analysis
In this step, you really dig into the factors that are causing the problem. Consider and address all of the causes of the issue — there will usually be more than one.
The Stormboard Template for this step is divided into four sections: Create a Decision-Making Tree, Analyse and Discard Ideas, Ask Why, and Conduct “Why Analysis”.
Step 5: Develop Countermeasures
Use this step to brainstorm countermeasures that will help you remove the root causes of your problem. Come up with as many as possible, and then narrow the criteria matrix and create an implementation plan
The Stormboard Template for this step is divided into three sections: List Root Cause, List Countermeasures, and Chart and Rate Countermeasures.
Step 6: See Countermeasures Through
In this step, you will implement your countermeasures using a clear plan and share the progress of each countermeasure that you implement with your team.
The Stormboard Template for this step is divided into three sections: Implement Countermeasures, Share progress, and Next Steps.
Step 7: Monitor Results and Processes
Use this step to determine if your countermeasures were successful or if they need to be adjusted and reimplemented.
The Stormboard Template for this step is divided into three sections: Evaluate Results, Report, and Lessons Learned.
Step 8: Standardize The Successful Process
In this step, you will integrate your successful countermeasure into your process, share your results with your team, reflect on what you have learned, and make sure there are no unaddressed issues.
The Stormboard Template for this step is divided into three sections: Standardize, Share, and Start a new Kaizen.
See the template →
Are you interested in trying out Stormboard’s 8 Steps to Problem Solving Templates with your team? Sign up for a FREE trial now !
Keep reading.
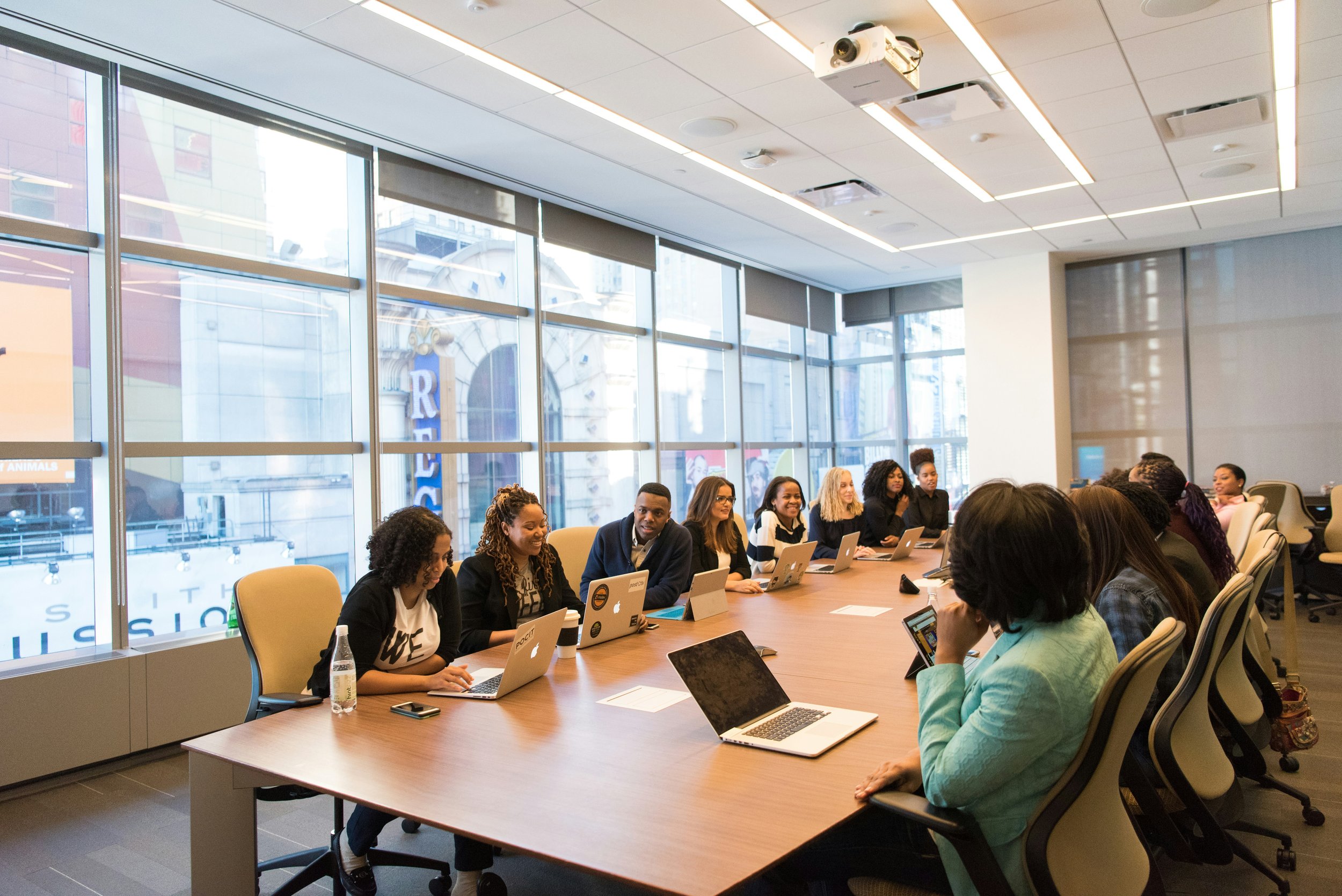
Discover how groupthink poses a significant threat to innovation within agile teams, hindering the emergence of new ideas and impeding progress throughout the scrum cycle. Explore strategies for agile team management to mitigate the impact of groupthink and foster a culture of creativity and innovation.
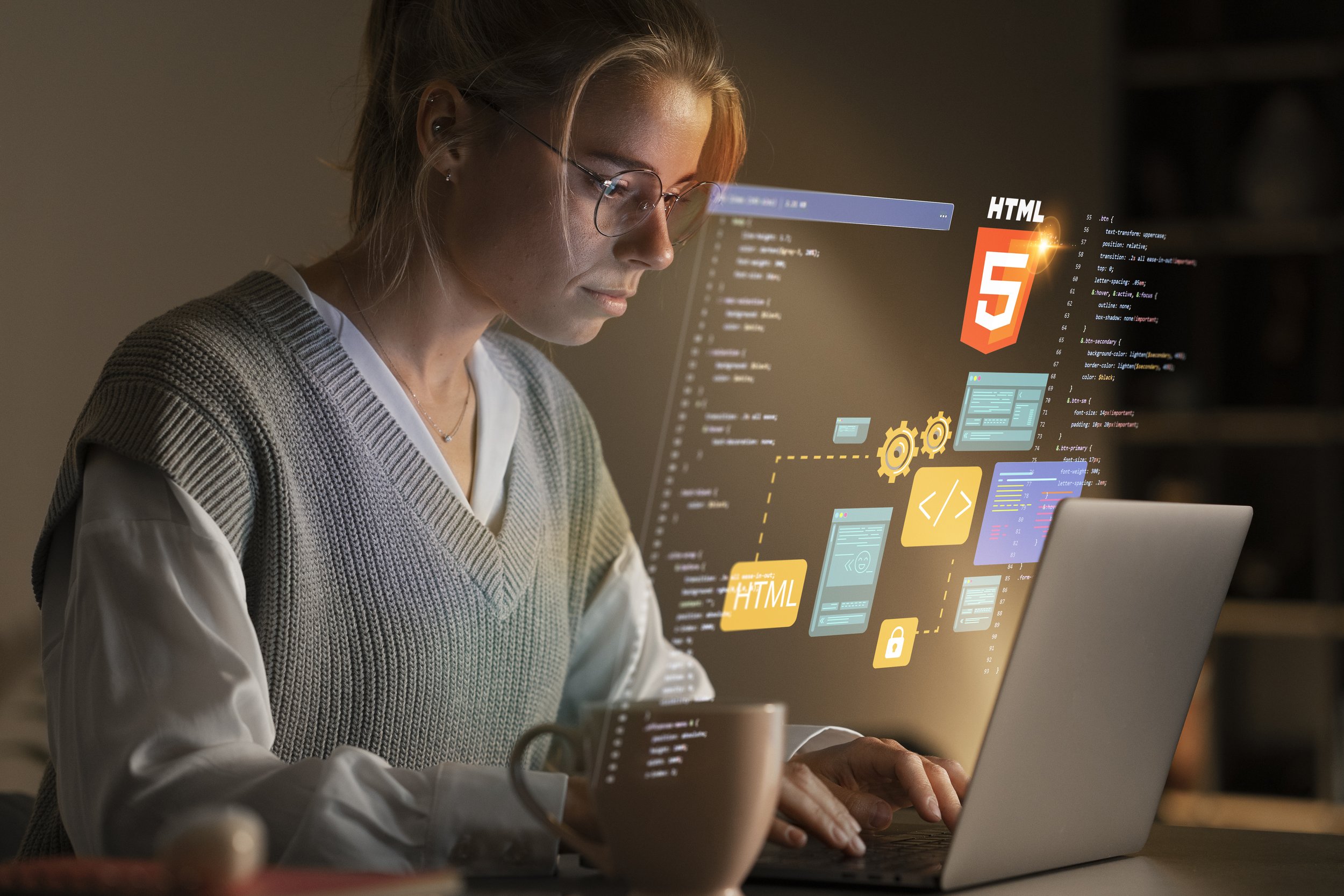
Discover how technology enables cohesive collaboration for remote web development teams, with 4 out of 5 developers working remotely. Explore the top collaboration tools empowering seamless workflows and website building, regardless of location.
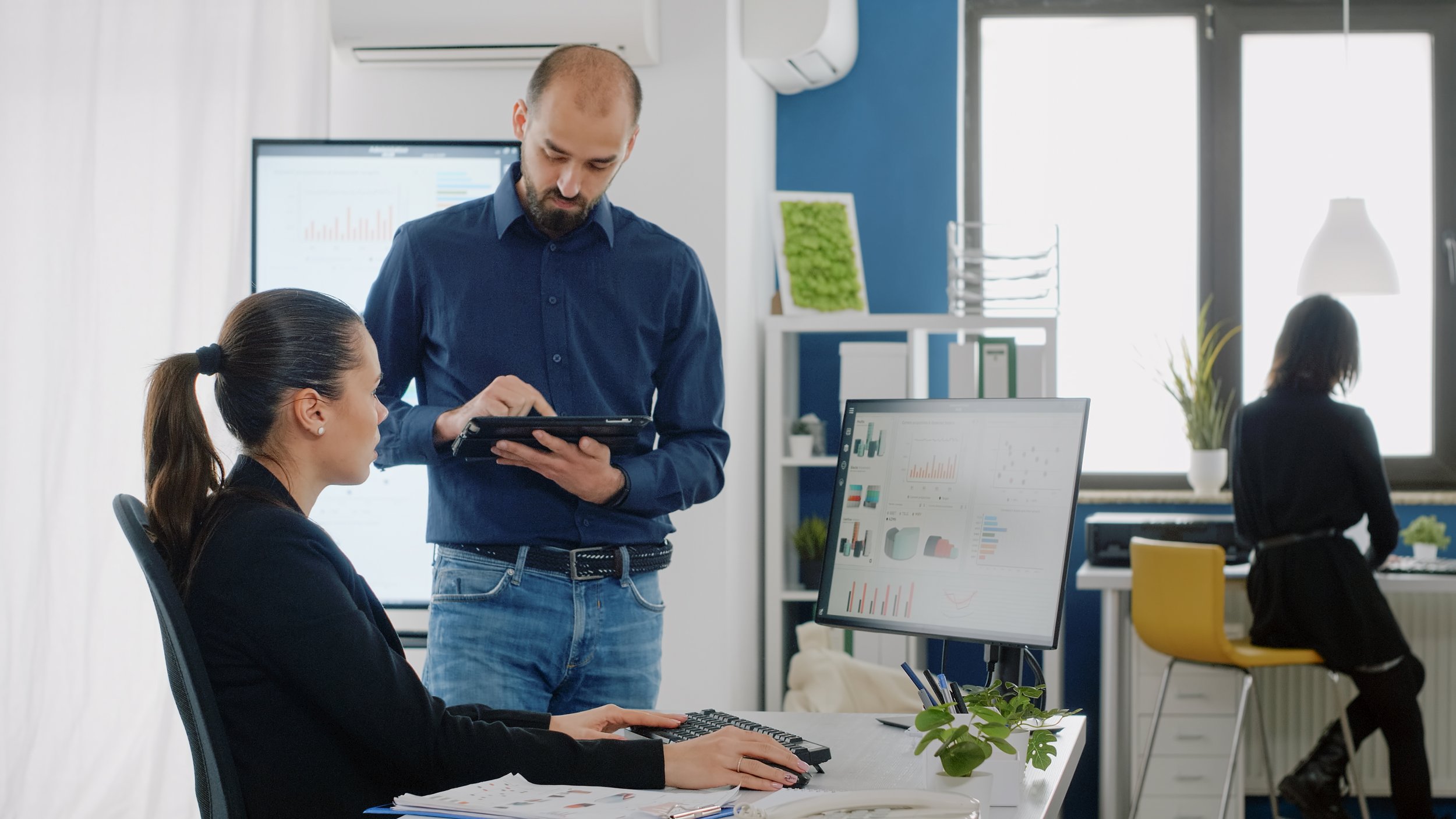
In a fast-paced business world marked by evolving customer needs and technological advancements, staying ahead demands adaptability. Discover how fostering an agile workplace culture can empower your team to innovate, collaborate, and swiftly respond to change, driving efficiency and securing a competitive edge.
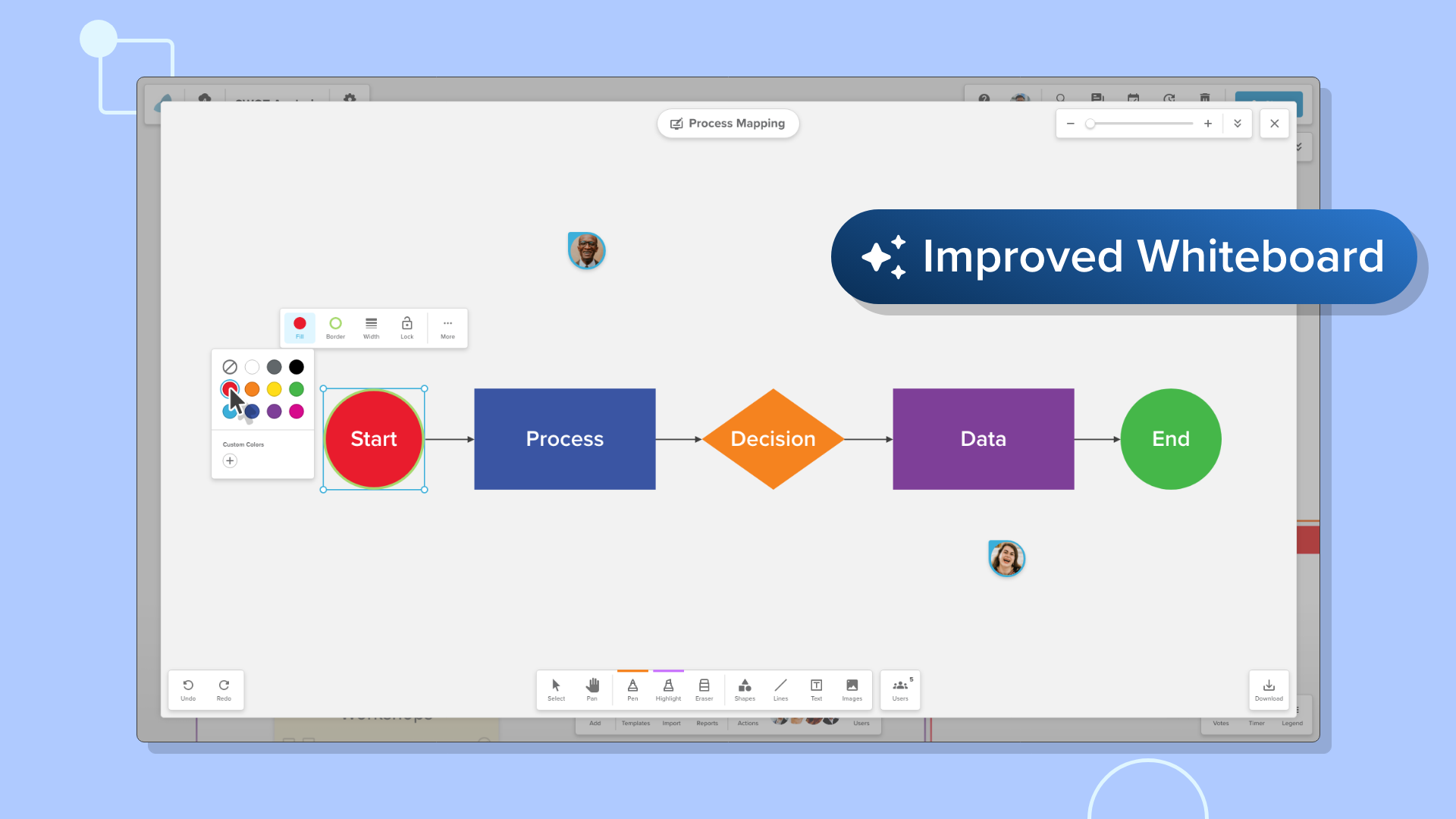
Learn how DevOps is revolutionizing development and operations workflows, enhancing product delivery speed and cost-efficiency. Explore the critical role of continuous security auditing in DevOps to mitigate vulnerabilities and safeguard against threats.
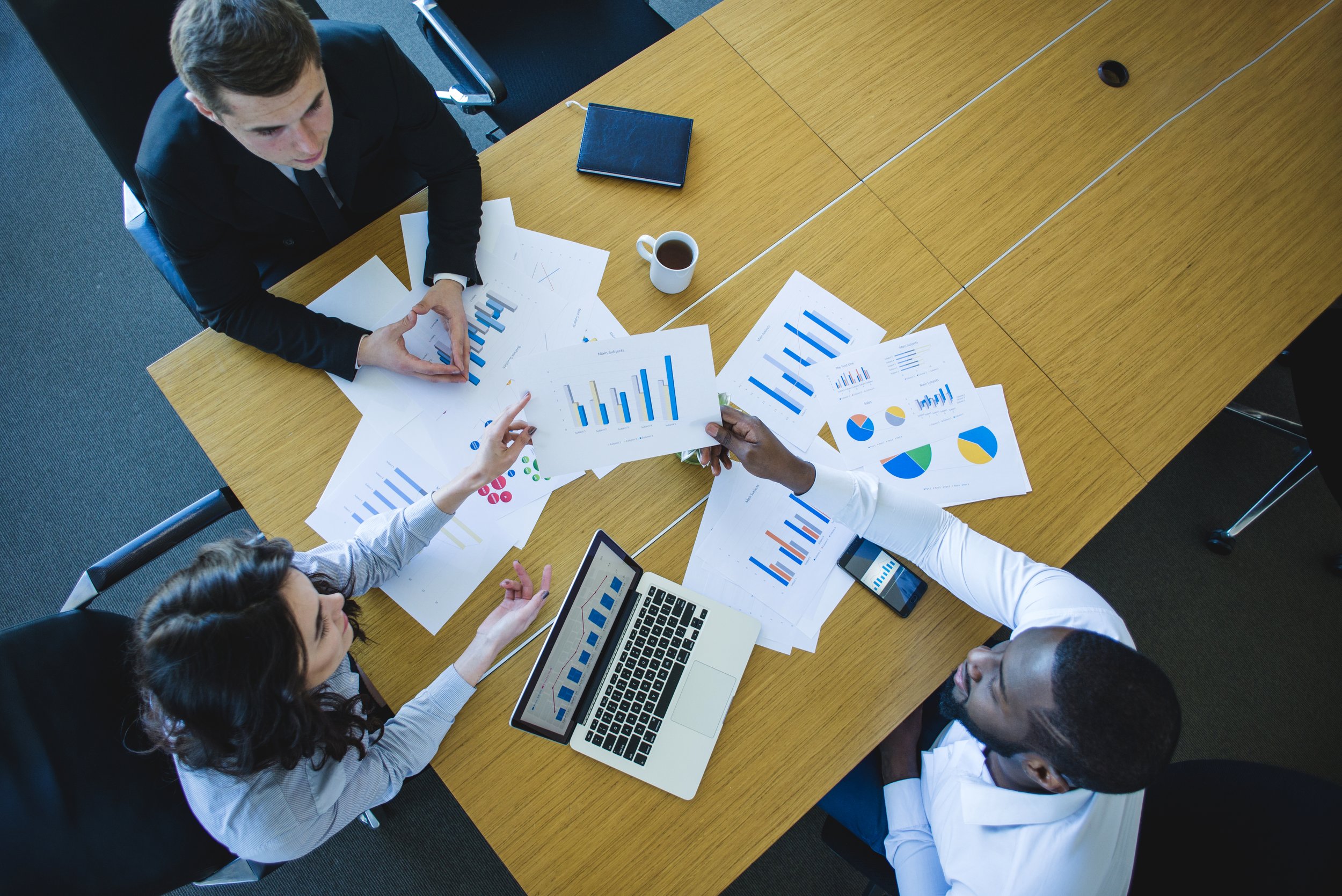
Project management challenges are inevitable. Here are some common problems and how you can stay ahead of them in 2024.
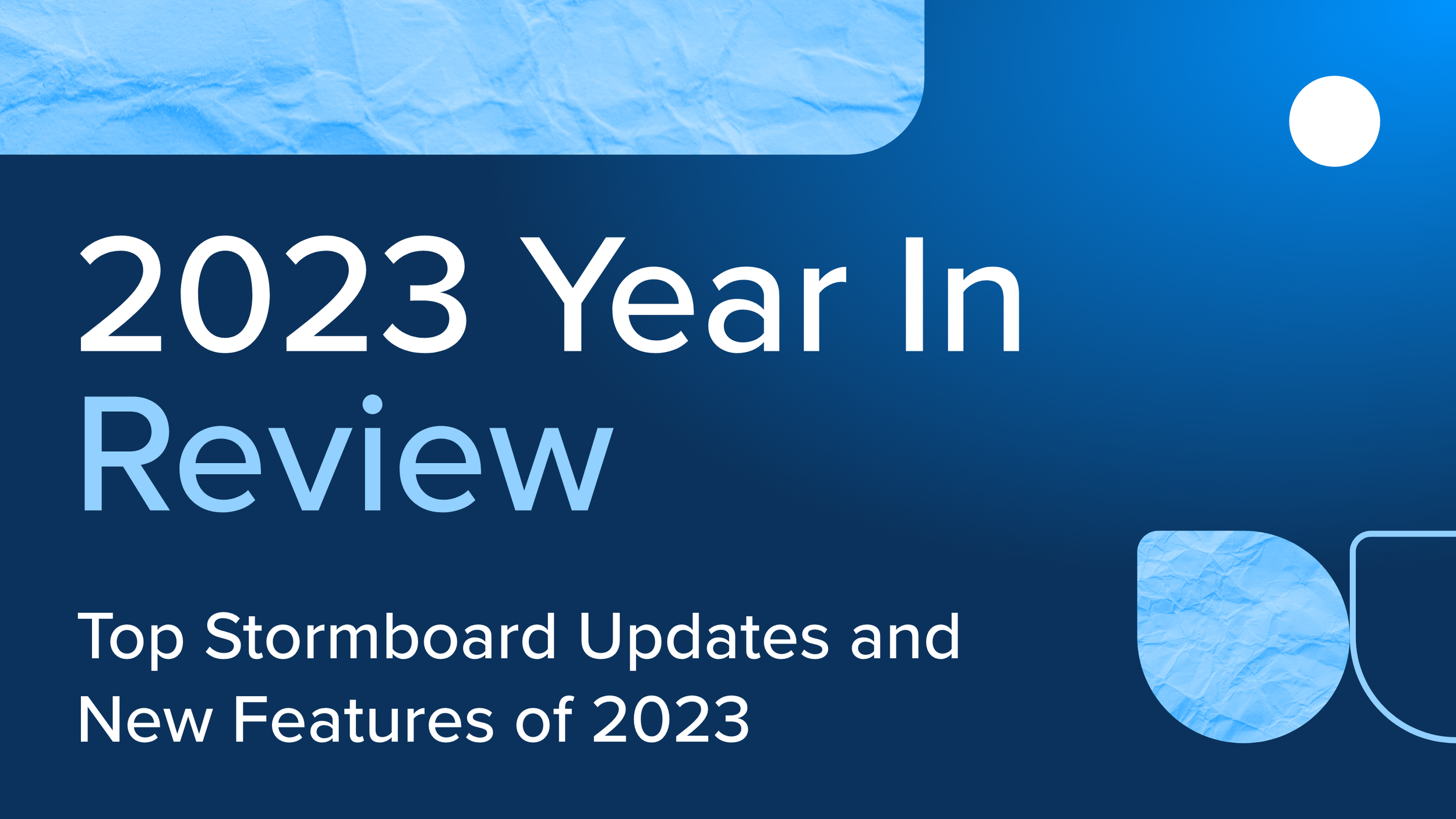
Explore the transformative landscape of 2023 as Stormboard, riding the generative AI wave, celebrates its most significant year yet. Uncover how Stormboard's core product enhancements and advanced workflow integrations respond to the evolving needs of modern businesses, empowering enterprises to reimagine their technology strategy for a dynamic future.
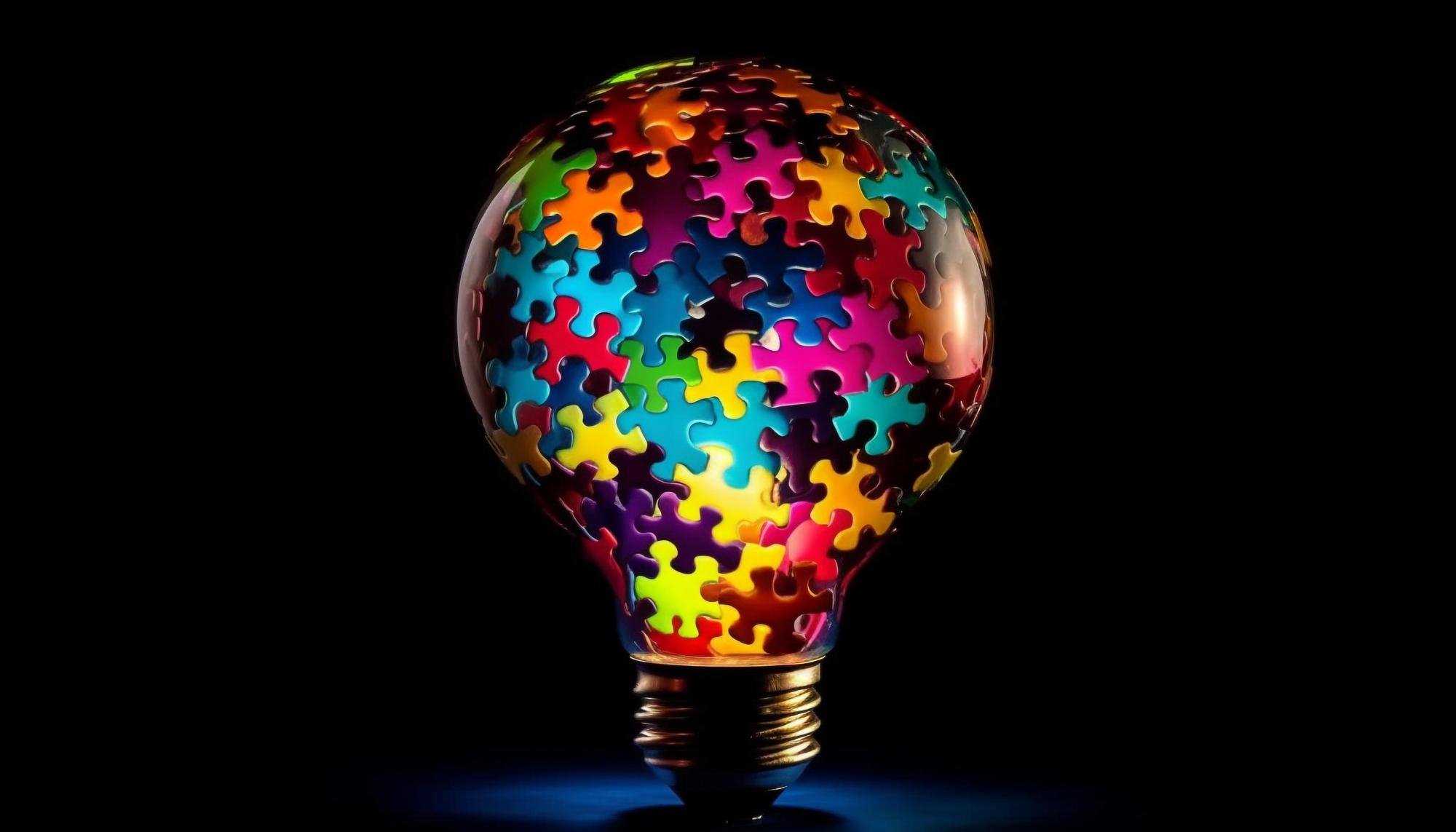
Unlock innovation and embrace diversity in team brainstorming! Learn strategies to navigate cultural differences and create an inclusive environment for effective ideation while overcoming boundaries and enhancing diversity in collaboration sessions.
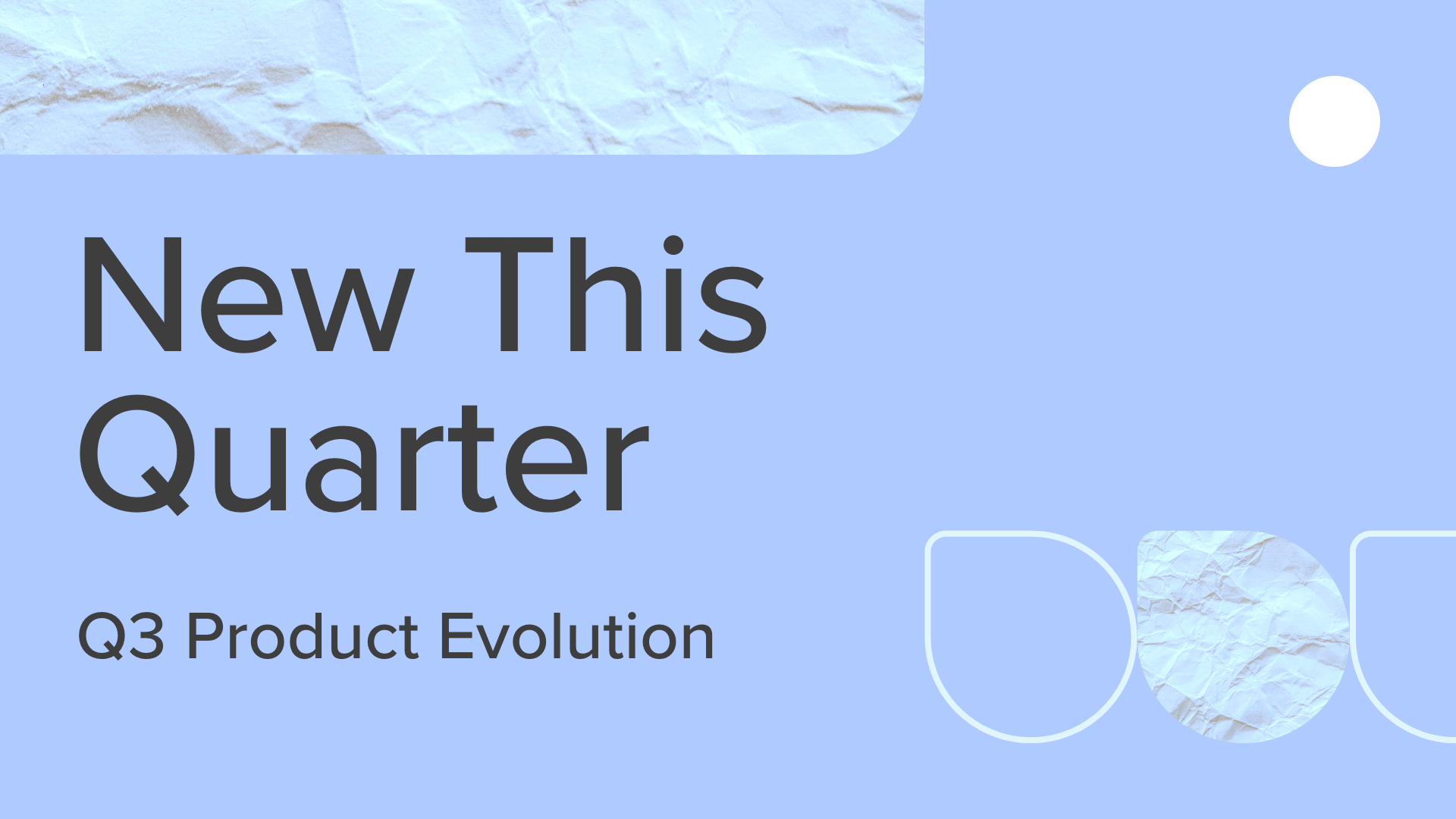
Explore Stormboard's Q3 highlights: Discover how user feedback shapes our evolution, and explore Q3 highlights with new features and enhanced UX for global organizations.
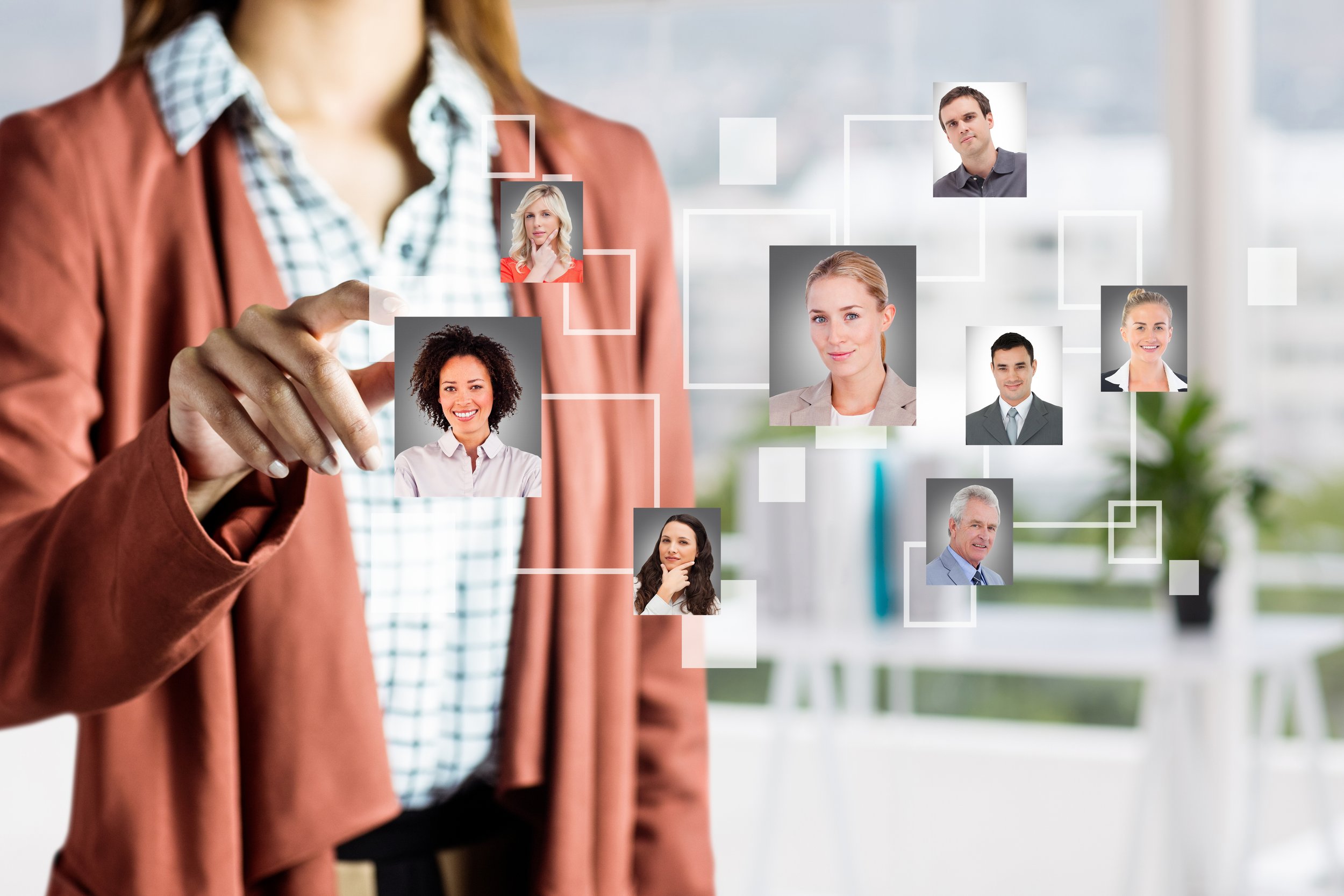
Discover how crafting buyer personas can elevate your marketing strategy, making your website more effective and enhancing customer interactions in the competitive business landscape.

Navigate the complexities of business process management (BPM) with a proactive approach to overcome common challenges in implementing automation. Discover how AI technology, no-code, and low-code solutions make BPM accessible, enabling you to streamline processes, cut costs, and save time effectively.
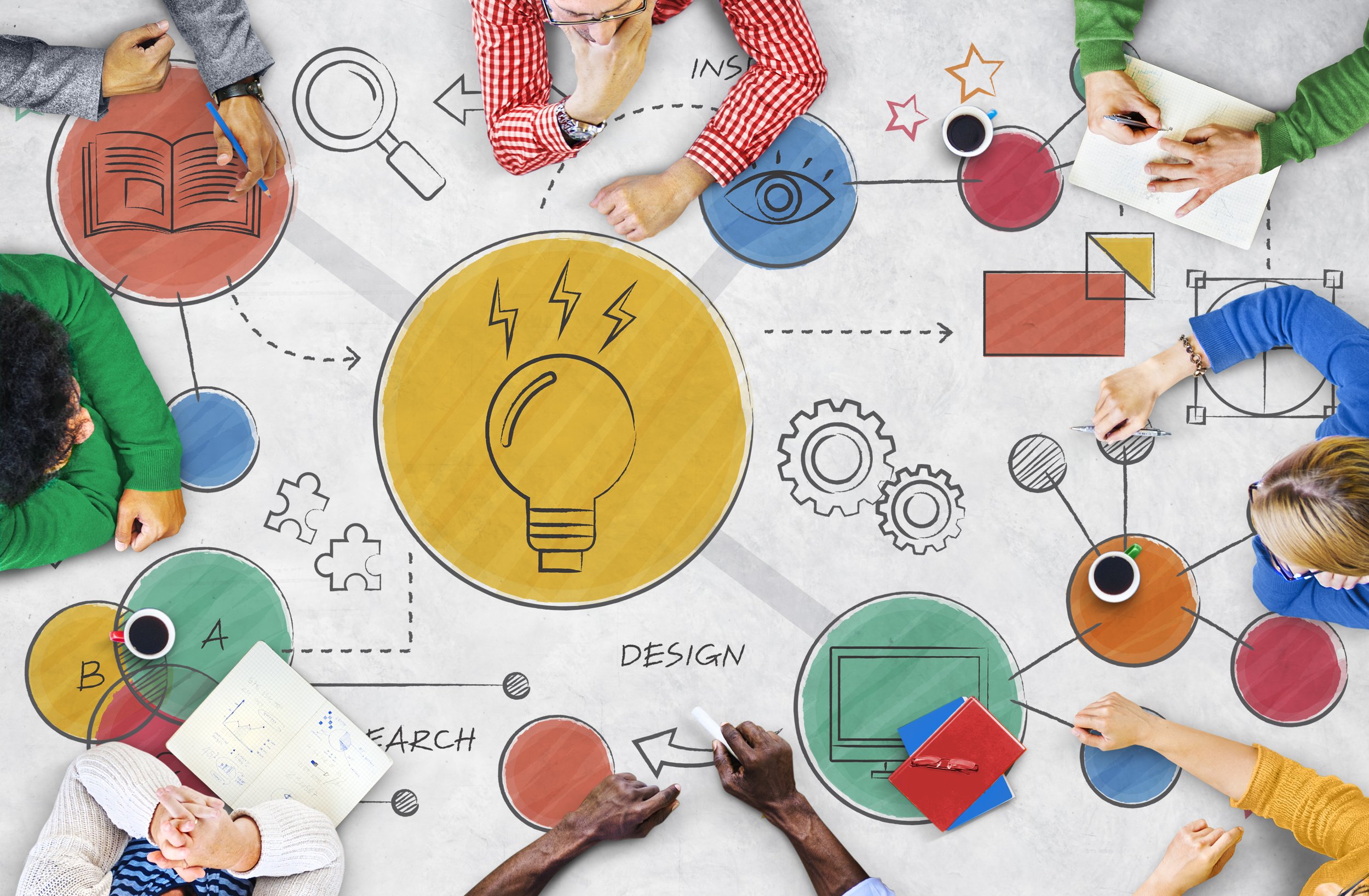
Optimize Collaborative Brainstorming: Learn the art of efficient idea generation with these five crucial steps. Enhance team collaboration, foster innovation, and bid farewell to unproductive meetings. Learn how to elevate your brainstorming sessions for impactful outcomes.
How Collaborative Leadership is Changing Business
Scared of the blank page add sample content to your template to get to work faster.
DOWNLOAD NOW: The LCS App Click here
- LCS Community
Toyota’s 8 Step Practical Problem Solving
Simon Elias, Former Director, Lean Competency System (until Oct 2023) | 08th July 2016
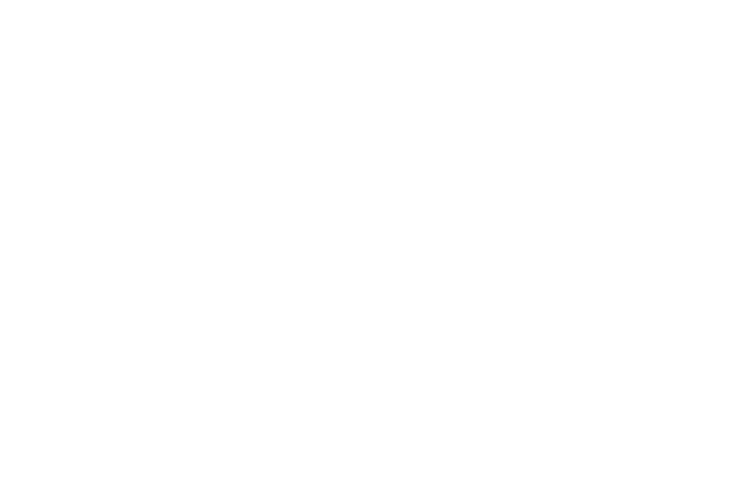
A video from the Gemba Academy Practical Problem Solving course that explains an eight step problem solving process. It also covers PDCA and use statistical tools such as control charts, Pareto charts and scatter plots.
Comments
Comment on this Article
Featured Article
Enhancing learning: the power of continuous improvement in greek language online tuition.
Iraklis Lampadariou | 12th September 2023
Data Analytics Tools Offer Small Business Owners These Important Benefits
Test | 23rd September 2022
How to Boost Collaboration in Your Small Business Team
Test | 26th July 2022
Five Tips for Developing an Effective CPD A3 Plan
John Homewood | 2nd August 2021
What’s Your Vision?
Simon Elias | 23rd June 2021
Want to Contribute an Article to the Community?
Community members are welcome to post an article on any lean related topic. Go the the Article Submission Page and add your article.
- Organisations
- Consultancies
- Individuals
- Qualifications
Quick Links
- Find members
- Resources for members
- Resources for Accredited Organisations Introduction
- The LCS Impact Awards
- Useful Downloads
Lean Competency System © 2024. The LCS is a licenced service of Cardiff University
Sign-Up To Our Newsletter
LIST OF TRIZ-BOOKS
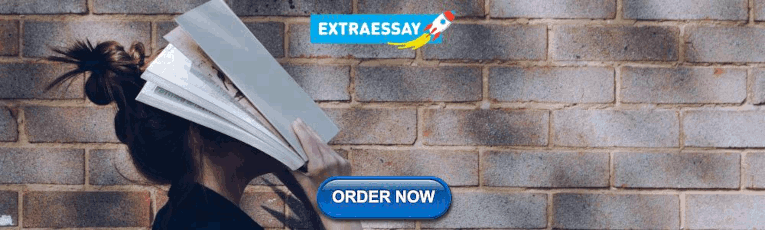
IMAGES
VIDEO
COMMENTS
The art of problem solving is constantly trying to evolve and be re-branded by folks in various industries. While the new way might very well be an effective method in certain applications. A tried and true way of identifying and solving problems is the eight steps to practical problem solving developed by Toyota, years ago.
https://gembaacademy.com | The Gemba Academy Practical Problem Solving course explains the exact 8 step problem solving process used by these lean exemplars ...
https://GembaAcademy.com | Learn the 8 steps Practical Problem Solving methodology, lean thinking exemplars such as Toyota use to attack problems. ️ For mor...
The 8-Step Practical Problem Solving Process: The eight steps: Clarifying the problem and describing the current situation. Breaking down a big problem into smaller, more specific problems and studying the process. Setting a challenging yet achievable target. Analyzing the root cause.
Toyota practical problem solving consists of the steps as listed below. Note that sometimes you have a step more if you decide to split a step into two. Clarify the Problem. Break Down the Problem. Set a Target. Root-Cause Analysis. Develop Countermeasures and Implement. Monitor Process and Results.
Solving" Process Some of the best problem solving methods are the simplest and one of those that continues to stand the test of time is Toyota's 8 step method. This method also goes by the name of "Practical Problem Solving" or "PPS" for short. In the diagram below not only can you see the steps for yourself but you can also see how ...
Toyota's 8 Step Practical Problem Solving, Revisited. By Jon Miller Updated on March 4th, 2021. The practical problem solving steps…. It is too early to talk about solutions. It is still too early to talk about solutions. It is still too early to talk about solutions. It is still too early to talk about solutions.
This is a fundamental building block of Toyota's success and is practised by all employees at all levels. Toyota's 8 Step Problem Solving. In a practice-based workshop, Mark Davies, Senior Manager at Toyota Lean Management Centre UK, took us through the 8 step problem solving process :-1 - Clarify the problem 2 - Breakdown the problem 3 ...
A3 8 Step Practical Problem Solving - Skill Level 1: Knowledge Optional - Additional Information & Reading How the A3 Came to Be Toyota's Go-To Management Process. by Isao Yoshino. August 2, 2016. The discussion below between John Shook and Isao Yoshino first appeared on The Lean Enterprise Institute website www.lean.org.
As listed in my previous post, the Toyota Practical Problem Solving approach consists of the steps listed below. Clarify the Problem. Break Down the Problem. Set a Target. Root-Cause Analysis. Develop Countermeasures and Implement. Monitor Process and Results. Standardize and Share. Before you start to clarify the problem, you may also need to ...
Toyota's 8 steps for problem-solving act as the lens that allows you to view different aspects of your operation from a new perspective. Consider these eight steps as you start on the path to continuous improvement. 1. Clarify the problem. The first step in solving a problem is realizing that one exists. You can define a problem by asking ...
A Quick Recap. As listed in my previous post, the Toyota Practical Problem Solving approach consists of the steps below. Clarify the Problem. Break Down the Problem. Set a Target. Root-Cause Analysis. Develop Countermeasures and Implement. Monitor Process and Results. Standardize and Share.
An overview of the Toyota 8 Step Practical Problem Solving Process also known as PPS and part of the Toyota TBS. Click the link below to read an explanation of the Toyota 8 Step Practical Problem Solving Process as a PDF: Toyota 8 Step Practical Problem Solving Process PPS TBS... People, Purpose, Performance - Future State Consulting.
8 Step Process for Problem Solving 26 A C D P Step1. Clarify the Problem Step 2. Break Down the Problem Step 8. Standardize Successful Processes Step 7. Monitor Both Results and Processes Step 6. See Countermeasures Through Step 5. Develop Countermeasures Step 4. Root Cause Analysis Step 3. Target Setting
Systematic problem-solving is a core element of a True Lean™ organization. This course teaches the 8-Step problem-solving method used within Toyota at all levels and functions to practice effective continuous learning and improvement. We use a learn-by-doing format as teams will work through real problems selected within their organization ...
#ProblemSolving #LeanVlogWhat is Problem Solving is explained in this video by Toyota's approach.Here the transcript of the video.Toyota's 8 Step Problem Sol...
The 8 Steps to Problem Solving Method was developed by Toyota Motor Corporation as a practical, structured, and simple way to handle any problem from the smallest issue to the most complex roadblock. What is the 8 Step Problem Solving Method?
Toyota's 8 Step Practical Problem Solving. Simon Elias, Former Director, Lean Competency System (until Oct 2023) | 08th July 2016. Load full article. A video from the Gemba Academy Practical Problem Solving course that explains an eight step problem solving process. It also covers PDCA and use statistical tools such as control charts, Pareto ...
Problem-solving creativity combines creative ideas, such as exploring knowledge, defining problems, and comparing ideas to identify the most creative ones (van Hooijdonk et al., 2020). Several ...
This was the first comprehensive book (128 pages) about a methodology of inventive problem solving. 50 000 copies of the book were printed and sold. The book summarizes the experience with studying 4000 patents, first seminars about methodology of inventive problem solving and the earliest results from using the TRIZ approach.
The problem of teaching the methodology in senior school, colleges, universities and post-graduate courses is considered in chapter 8. ... METHODOLOGY OF PRACTICAL ACTIVITY. 3.1. Characteristics of Practical Activity. 3.2. Means and Methods of Practical Activity ... Chapter 8. TEACHING THE BASES OF METHODOLOGY. CONCLUSION. SUBJECT-HEADING ...
Our world-class problem solving approach in neighborhood campuses. 12 US locations and growing! For students grades 1-12 Learn more ... The richly illustrated adventures of four little monsters help students build problem solving skills in math and science For students grades 1-5 Shop now Since 1993, AoPS math textbooks have offered ...
As a result, these methods may converge with constant step size, and their convergence rate is linear. Recently Gurbuzbalaban et al. have proposed the incremental Newton (IN) method [10]. Despite a similar name, the IN method is quite different to NIM. The IN method belongs to the first group of incremental methods with B kequal to a partial ...